The Wall Street Journal has an epic track record when it comes to always getting it wrong when they write about Lean or the Toyota Production System. They always focus on just the “just in time” pillar, ignoring “jidoka” (built in quality) as the other pillar (per Toyota). They ignore many other aspects of TPS, like the culture and the management style.
See some of that track record, including recent pandemic supply chain articles.
You're normally better off reading about Lean from the source.
But, they did better in this recent article about General Electric and CEO Larry Culp (who knows Lean very well from his time as CEO of Danaher):
Larry Culp Rewired GE. Then He Unwound It.
Hopefully the link there is a “free link” that allows you to read it if you're not a subscriber.
To most, the big news is the “unwinding” of GE — splitting up into separate companies, as was announced recently.
But, I'm more interested in the “rewiring” of GE. The history of GE is that they really got into Six Sigma… then embraced Lean in more recent years. Larry Culp is, it seems, a die hard Lean / TPS guy (and I don't mean for this to turn into a “Lean vs. Six Sigma” debate).
“Before Larry Culp decided to break up GE, he had to break it down.”
And, as the article details, Culp wasn't focused on financial engineering — he was visiting factories and inspiring (if not leading) improvement at an operational level.
Hear Mark read this post — subscribe to Lean Blog Audio
The first example, from a factory in South Carolina:
“Using light green yarn, the group traced the journey of a steel blade through the miniature plant. They discovered the blade–which had been piling up at some stations–traveled nearly 3 miles on its 85-day journey through the plant.
The solution was clear: rip out the old machinery and rearrange the production line to shorten the green string. In the process, GE upgraded the machines to help stop the logjams. When finished in early 2020, the blade traveled just 165 feet and production time was cut by 42%.”
The meaningful detail here is, of course, not using light green yarn. Let's not all rush out to buy light green yarn. The key point is that they traced out the flow… and realized that rearranging machines can reduce travel distances, which also reduces lead times and inventory levels.
“In the process, [Culp] laid bare an organization that belied its reputation for operational and managerial excellence.”
GE generally has an amazing reputation when it comes to “operational and managerial excellence.” I had to look up the word “belie” to make sure it meant what I thought it did:
- “to give a false impression of”
- “to present an appearance not in agreement with”
- “to show (something) to be false or wrong”
Ouch. There's reputation and then there's the reality at the shopfloor level… that doesn't always line up with reputation or perception.
“Mr. Culp arrived at GE with a reputation as a high priest in the world of lean manufacturing, a management philosophy that seeks to cut waste and create a culture of continuous improvement.”
Thank you, WSJ for mentioning the idea of a “culture of continuous improvement.” Lean is usually portrayed as the risky elimination of inventory in that publication.
“One of [Culp's] first exposures to lean management was in the early 1990s when he worked in an air conditioner factory in Japan for a week as part of a training exercise. “There's nothing like being screamed at in a language you don't understand. It's a tough love environment,” he said.”
The key point is not to scream at people. That's a decidedly “old school” Shingijutsu approach to Lean that's not practiced by Toyota people today when they go work with suppliers or non-profits, through their TSSC group.
But, it's great that Culp is “addicted” to Lean improvement, as the article says.
“The concept of lean manufacturing was unofficially invented in the middle of the last century out of the work of a Toyota engineer named Taiichi Ohno who was tasked with making production more efficient in the post-World War II years in Japan. The system centers on an approach called kaizen, which focuses on seeking continuous improvement through in-depth sessions to assess employees' progress. It eventually became the Toyota Production System.”
Again, I'm very glad that the WSJ is mentioning the Kaizen approach to continuous improvement.
I'm also happy that the WSJ is passing along Culp's expertise.
“In an interview, Mr. Culp described it this way: “There are three core ideas at work:
- Focus on the customer.
- Elimination of waste.
- Ruthless prioritization of work.”
That third phrase isn't something I've heard from Toyota folks before, so I'm not exactly sure what he means.
That said, in a typical “strategy deployment” approach, companies (or healthcare organizations) shift away from everything being a “top priority” to being more selective. Better to get a few key things done and move on to more, rather than trying to do 200 or 300 projects all at once (this is something that Dr. John Toussaint has described in his writing and teaching for healthcare).
I'm also happy that the WSJ pointed out that Lean isn't just about factory operations, using a term I love, “carpet land.”
“Danaher eventually used the lean philosophy to run more than its factories. Its usefulness stretched into “carpetland”, as office-based activities were called, where even a task such as processing an invoice or preparing a regulatory document can become more efficient in time expended and resources used.”
And, I'd add, that it's not just a matter of efficiency — quality matters (and improves) also through Lean.
There's another Culp / Lean success story:
“In early October, Mr. Culp spent five days at the GE aviation plant in Lynn, Mass., where his kaizen assignment put him with a small team studying a military engine part that was hurting on-time deliveries. The problem turned out to be an issue with welding on the part, leading to changes that went from yielding a usable part 59% of the time to 100% of the time. Nine different teams in Lynn that week made changes that cut costs by $2 million and reduced production time by 62 days, according to a memo Mr. Culp sent to employees.”
It's great that Culp gets Lean and leads the culture change. It's fantastic that he's willing to participate in Kaizen Events (as Toussaint did as a healthcare CEO).
You just hope that the culture change and the Lean methods scale beyond the CEO being involved.
The article also shares Culp's view on standard work:
“A basic concept of lean management is to create standard work processes in order to continuously improve. If the same job is done differently every time or varies by worker, there is no basis for finding improvement. The same job must be done the same way every time. No detail is too small. “Standard work is simply identifying the work steps required and the sequence of those steps, the time required for each, that go into making a process repeatable,” Mr. Culp said in 2020.”
I'm also happy to hear Culp talk about the application of Lean to Diversity, Equity, and Inclusion efforts (as people like my friends Christopher Chapman, Deondra Wardelle, and Joy Mason are doing.
“Mr. Culp has said that lean processes are helping GE find ways to improve the diversity of its workforce…”
I'd love to learn more about that.
Does Culp practice Lean at home? Nope:
“If you came and looked at my garage or my closet, you wouldn't see anywhere near the orderliness that you might see in a factory that I've been associated with,” Mr. Culp said. “I usually end my training sessions with, ‘but don't try this at home.'”
That's funny. I mean, you can apply Lean mindsets and practices at home if that suits you and makes life better or easier for you. But, Culp has had his hands full with Danaher and now GE. I won't fault him for leaving Lean thinking at the office (or the factory).
Please scroll down (or click) to post a comment. Connect with me on LinkedIn.
Let’s work together to build a culture of continuous improvement and psychological safety. If you're a leader looking to create lasting change—not just projects—I help organizations:
- Engage people at all levels in sustainable improvement
- Shift from fear of mistakes to learning from them
- Apply Lean thinking in practical, people-centered ways
Interested in coaching or a keynote talk? Let’s start a conversation.
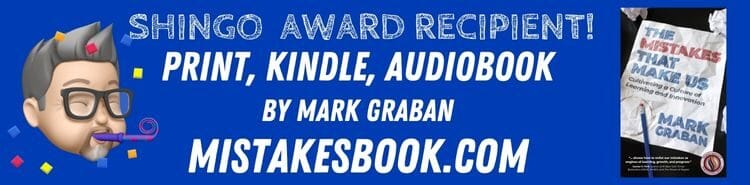
My years at GE were in the Aircraft Engine division, which oddly enough will be the surviving entity of Edison’s once proud laboratory.
While Six Sigma is what GE was famous for, the first week that I spent on the shop floor at GE was a Shingi-Jitsu workshop. The fixtures on the machine tools at that time were mostly SMED-influenced designs and work was rarely done in batches, outside of a few cells where the nature of the work prevented single-piece flow. (Try setting up a 144-inch broach machine with .0002″ tolerances in less than a shift).
While GE shops were not consistently lean, and they had many problems that would make any person who understands lean blanch, lean wasn’t new to GE in 2003, nor is it new to GE today.
But it is good to see the WSJ getting it right and GE emphasizing it again.
Thanks for that, Andrew. It seems clear that Jack Welch, as CEO, wasn’t a “Lean thinker” and probably didn’t show much interest in learning that (at least he didn’t promote it externally like he did Six Sigma).
I’m not surprised that there were Lean practices at an operational level. Some of that was probably inevitable.
But, when I got a job as a Lean specialist at Honeywell in 2004, I was told that the job opening I filled was there as a result of this sequence that was alleged:
1) GE was trying to purchase Honeywell
2) During due-diligence, Honeywell people were told “GE is Six Sigma only”
3) The Lean focused people got the message and left
4) The acquisition fell through (pushback from EU regulators)
5) Honeywell continued its approach of what I call “Lean and Six Sigma”
6) They had to hire new Lean people to fill those roles
I believe I read that Larry Culp plans to retire again after the GE spinouts are done… and the head of GE Aviation seems to come from a plane leasing and private equity background… so will the commitment to Lean remain as strong at GE / GE Aviation? Time will tell.