Children's Hospital of Philadelphia (CHOP) is the oldest children's hospitals in the United States. I don't think I've ever been there, but I remember them having Lean improvement efforts going back to the mid 2000s when I first moved from manufacturing to healthcare.
Children's hospitals, in general, are even more amazing places (compared to a typical hospital) because they're full of people who are somehow (generally) more loving and more caring than people in general hospitals. I think there's a self-selecting element that draws certain people to children's healthcare… the most caring of the caring, perhaps.
It always pains me to hear accusations of people being treated unfairly in any workplace. That bothered me when I worked in manufacturing and it bothers me when nurses are overburdened (as just one example of bad working conditions in healthcare).
Earlier this year, I saw this news story, and my friend Paul Levy (a Lean-thinking former hospital CEO) predicted correctly that it would bother me when he tweeted this:
“In the basement of CHOP, warehouse workers say they're held to impossible quotas”
The article talks about workers (employed by a vendor that was hired by CHOP) who deliver supplies being held to what is described as an unfair productivity standard… as it says in the article:
“It's not clear to them what their rate is while they're picking or how it's calculated — the former supervisor, who spoke on condition of anonymity because he works in the same job at a different hospital, said it was “computer-generated.” What workers say they do know is that the rate is nearly impossible to meet if any little detail is off: If they're understaffed or overstaffed, if it's a holiday, if there's a person who's new and just getting up to speed.”
Conditions like that are troubling if it's an Amazon fulfillment center (as was in the news) and it's really sad when a hospital is doing that to people.
I use this quote a lot from Darril Wilburn, a former Toyota leader:
“It's the responsibility of leaders to create a system in which people can be successful.”
It sounds like that isn't the mindset in this department at CHOP or some parts of Amazon.
If the rate is nearly impossible to meet unless things go perfectly then that's not a well-designed performance measurement system — it's not a well-designed work system. There is always going to be variation in how long it takes to do something (unless the job is very simple and very repeatable).
People need to have slack… 100% utilization sounds good but causes so many problems (it can put safety or quality at risk, for example, not to mention the stress that's created).
How many good people, hard-working people, get fired for performance that's mostly driven by the system? Or they're getting fired for “low” performance that's within normal variation? Is this the Red Bead game in real life?
And what is the long-term cost of this hiring, ranking, and firing to the organization?
“The result [of their system], four current and former staffers said, is a workplace where workers live in fear of getting fired because of a number that doesn't account for the realities of the job, a number they barely even understand.
“It's exhausting if I'm killing myself trying to meet these invisible numbers,” said a picker who works the overnight shift and spoke on the condition of anonymity for fear of losing his job.”
That sounds bad. What are some of the stated values of CHOP, from the Quality and Patient Safety page?
Just picking three of them:
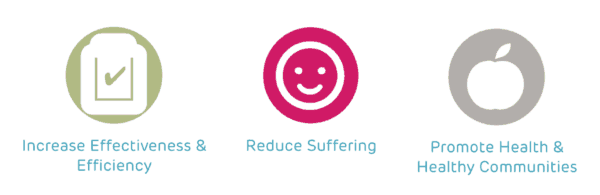
Yes, it's important to improve efficiency (and a truly Lean organization can be safer, with better quality, and better efficiency at the same time… as a result of better-designed work).
But how much does effectiveness suffer when contract workers are under such time pressure? How many incorrect deliveries get made? How many items get damaged?
Below is an example of an Amazon delivery that I received recently. I don't blame the Amazon-contracted gig-economy delivery worker if they were having to rush to keep up with a work standard that's unrealistic. What caused the torn box? Maybe they threw the box (which contained copies of my latest book) and/or it wasn't packaged well. It wasn't a matter of life and death, at the least.
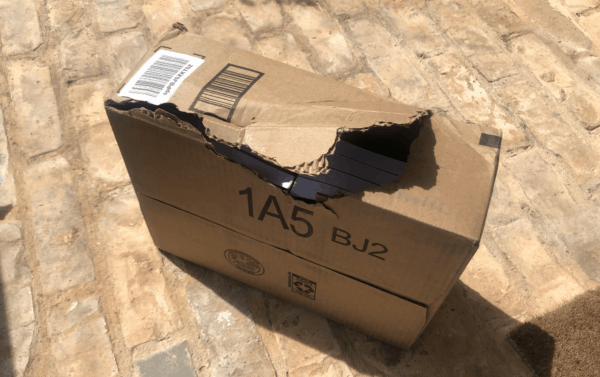
It's a good thing it wasn't raining. My books didn't get wet. Rain would have made it harder to hit their productivity targets for delivery, now that I think of it. Rain might have affected safety if they were rushing.
CHOP wants to reduce their patients' suffering. That's a great goal, the right goal. And making sure the right supplies are in the right place at the right time (in the right condition) is an important element in delivering timely, ideal care.
But what about the alleged suffering of their vendor's employees? What is the impact of that fear and perhaps unfair job loss on the health of the community? People probably take that fear home with them, which probably causes problems at home… and it does affect people's physical and mental health.
“There's always going be pressure to reduce costs and be as efficient as possible in any department that's not providing direct patient care,” said Andy Murphy, a Chicago-based health-care consultant with FTI Consulting.
There's always pressure… but the best path to higher efficiency and lower cost is working smarter, not harder. Design better processes, engage people in improving the work instead of pressuring them to move faster.
The pressure is not an excuse for employees to be under such pressure. Where is the loving and the caring? Does loving and caring patients mean it's accept to be uncaring toward contracted employees?
I emphasize that they're contracted… not to let CHOP off the hook. CHOP chose the vendor. CHOP is responsible for how people are treated under their roof.
This kind of standard-setting and monitoring is common in subcontractor relationships, labor expert David Weil wrote in his 2014 book, The Fissured Workplace, because a company otherwise risks tainting the reputation it's built when a contractor does not deliver. Performance metrics, in other words, are a way for companies to control their contractors, just as the contractor uses them to control its workers.
One story about a worker (who comes across as motivated in the article) said:
“Each type of item, regardless of how many are ordered, constitutes one “line.”
As an industrial engineer, that's doesn't seem like the greatest way to set a standard. Picking 30 of an item will take longer than choose one — and they are both “a line” for productivity measurement's sake? Now, someone could say “it all works out on average” — but does it?
That's like counting calories by counting the number of courses that you eat or the number of items that you eat. I ate 12 pieces of pizza, so that line item is the same number of calories as eating one side salad?
“He got two 15-minute breaks during his overnight shift, but he said he realized he couldn't afford to take them.”
That sounds just like nursing in many hospitals, unfortunately… and sadly.
“He knew he could move faster unpacking boxes of supplies and setting them up on the carousel's shelves, to which he'd later return as orders came through, but that would mean sacrificing accuracy for speed — and he didn't want to be sloppy.”
See, he sounds motivated… and concerned about quality. Why would an organization treat somebody like that badly?
“He continued to get reprimanded, which involved supervisors pulling him off the line to discuss the write-up. And every time he was brought in, he lost more time toward making rate. “Do they even think about that?” he wondered.”
Do they even think about that? Apparently not. That worker was soon fired for “unexcused absences.” Hmmm… why wouldn't somebody want to come in to that sort of environment?
I agree with the supply chain expert who is quoted in the story:
“Fred Landgraf, a Florida-based supply chain expert with health-care-focused Intalere, said hospitals have been slow to modernize their supply chains…
There are constraints that workers don't control — for example, if there's more demand at certain times on certain days. In those cases, managers should recognize the patterns and adjust staffing to meet demand.
But, he said, “you have to do that humanely, for lack of a better term.”
I think “humanely” is a great word. A hospital is supposed to be a humane place, children's hospitals even more so. Toyota preaches “respect for people” (a.k.a. “respect for humanity”) and they just “crank out widgets” as healthcare people sometimes say.
Healthcare should hold themselves to the higher standard to which they aspire.
Is This Lean?
There are two elements to this question. First, I'm glad that the word “Lean” was never used in the article. There are no accusations that the subcontractor is claiming any Lean methodology.
Secondly, what the article describes does not sound like a Lean (or Toyota-based) culture at all. Not at all.
So, I'm happy Lean wasn't dragged into the discussion… but the rest of it makes me sad.
I hope the Lean practitioners at CHOP can be part of the solution here.
What do you think?
Please scroll down (or click) to post a comment. Connect with me on LinkedIn.
Let’s work together to build a culture of continuous improvement and psychological safety. If you're a leader looking to create lasting change—not just projects—I help organizations:
- Engage people at all levels in sustainable improvement
- Shift from fear of mistakes to learning from them
- Apply Lean thinking in practical, people-centered ways
Interested in coaching or a keynote talk? Let’s start a conversation.
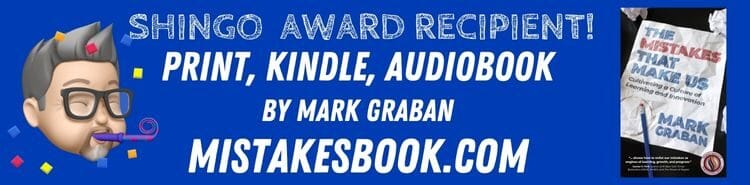