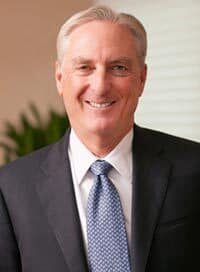
Dr. Gary Kaplan is the CEO of Seattle's Virginia Mason Medical Center, considered one of the world leaders in the adoption of Lean healthcare principles. He wrote the foreword for my book The Executive Guide to Healthcare Kaizen.
He co-authored a recent editorial in the BMJ Quality & Safety journal:
“Lean and the perfect patient experience”
It serves as a bit of a counter, saying “Lean does work,” to the recent NEJM article where two doctors claimed that Lean is inappropriate for healthcare.
Both editorials are unfortunately free of data. We know that Dr. Kaplan has direct experience leading VMMC's Lean transformation and that VMMC does have results to report. It's unclear if the NEJM authors had any direct experience with Lean or L.A.M.E.
Dr. Kaplan wrote:
“Lean can be effective in healthcare as well as in manufacturing, with a growing literature supporting improved patient experience, quality, safety and efficiency. The existing research is far from complete but there are at least abundant examples as proof of concept that, under many circumstances, Lean can be effective.2-4“
Note that he says it can work in healthcare. I would say the same thing. It does work… it can work… but that doesn't make Lean easy or something that's guaranteed to succeed. A lack of leadership and other factors (such as not really understanding Lean) can lead to a lot of problems or failures.
Dr. Kaplan writes about some of the pitfalls to avoid, including:
“The first of these [pifalls] is the misinterpretation of Lean merely as a set of tools targeted at short-term gains. The tools of Lean are well known and include value stream maps, 5S and rapid quality improvement workshops. These tools are effective in the short term, but true transformation and sustainability require, in addition, aligned leadership, a supportive institutional culture and integrating the Lean tools as part of a comprehensive management system.1 Absent these latter elements, expectations for Lean improvement should be limited to small-scale targeted gains.”
As I've written about here, Lean is not just a set of tools. It's also a philosophy and a management system.
Dr. Kaplan is also right that Lean has to be focused on longer-term success and goals, not just short-term gains. Hospitals often go for short-term gains by laying off staff… Lean is an alternative to that. Principle #1 of the “Toyota Way” philosophy says to make decisions for the long-term, even at the expense of the short term.
Listen to Mark read the post (subscribe to the podcast series):
One example of short-term thinking would be sending nurses home early to “save money” when census is low… when a Lean organization would choose to continue paying them that day so they can work on Kaizen improvements… arguably saving more money over time than sending them home would have realized. Read more about “flexing” and how that's not Lean.
Dr. Kaplan's editorial was in response to another piece in that issue that questioned if Lean provided benefits to patients:
“However, in this issue, Poksinska et al report that implementation of Lean management in 23 primary care centres in Sweden was not associated with improvements in the patient experience.5“
The authors of that piece are, rightfully, saying that healthcare organizations need to focus more on the patient (customer focus being a primary Lean philosophy and mindset). They are NOT saying Lean cannot impact the patient experience:
“Lean healthcare implementations seem to have a limited impact on improving patient satisfaction. Care providers need to pay more attention to integrating the patient's perspective in the application of Lean healthcare. Value needs to be defined and value streams need to be improved based on both the knowledge and clinical expertise of care providers, and the preferences and needs of patients.”
If organizations are only focused on cost cutting, that's not really Lean (see my recent post). If you're not focused on the patient as a customer, that's not really Lean.
Dr. Kaplan makes this point (and credit goes to BMJ for, unlike NEJM, printing two sides of a discussion in the same edition):
“…lack of improvement in patient satisfaction should not be seen as a failure of the Lean management system, but rather as the expected outcome when patient values and experience are not prioritised.
Nonetheless, the results of the study are provocative. No doubt all healthcare institutions identify patients as the first priority. However, do the needs of the patient truly come first? The results presented should provoke us all to re-evaluate our own priorities and, if we are applying Lean, to understand from which perspective waste is defined. In a sense, we would view the Lean implementation described in the Poksinska paper as a lost opportunity. The time and resources devoted to applying Lean to address the needs of the health system could be better used to improve value for the patients primarily, as well as all providers and staff. Cost-saving may then be expected to accrue from improved patient outcomes, and from better workforce engagement, productivity and efficiency.”
Cost savings is the end result of focusing on the patient, improving flow, improving quality, and creating a better workplace. Many organizations SAY that the patient (or patient safety) is the top priority, but that's too often just lip service.
My Healthcare Kaizen co-author's organization Franciscan St. Francis Health does focus on improving the patient experience. Their NICU has increased patient/family satisfaction (it's parents filling out the surveys) from about the 45th percentile to the 99th percentile. Their director credits the practice of Kaizen for this improvement – everybody identifying problems and working to fix them on a continuous basis.
Since journal articles matter, I'm working with Joe Swartz and the director of that unit to write an article that formally documents how they have used Lean and Kaizen to improve patient satisfaction. Again, that proves what's possible… but doesn't prove that it's easy or that every leader is able to make that happen.
We're close to selling out, but you can come visit Franciscan in April to visit the NICU (and other departments) and see what a culture of continuous improvement looks, sounds, and feels like.
Please scroll down (or click) to post a comment. Connect with me on LinkedIn.
Let’s work together to build a culture of continuous improvement and psychological safety. If you're a leader looking to create lasting change—not just projects—I help organizations:
- Engage people at all levels in sustainable improvement
- Shift from fear of mistakes to learning from them
- Apply Lean thinking in practical, people-centered ways
Interested in coaching or a keynote talk? Let’s start a conversation.
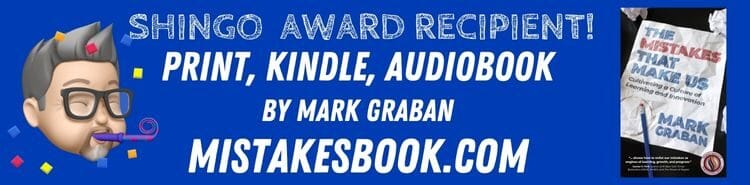
I agree with Kaplan about what Lean “can do” compared with “will do” or “does”.
It is naive to believe that managerial expertise in a Lean approach can be developed in a couple of years when it took Toyota decades and it is important to recognize that this comes from Kaplan who has been doing Lean with “success” in hospitals longer than anyone else has.
Customer satisfaction remains elusive for Hospitals and even for Toyota. While Toyota has a reputation for delivering reliable, well made cars and trucks their products rarely top the most desired lists or generate excitement as evidenced by Toyota killing off their Scion brand just as GM did with Saturn.
I will say that a well run hospital that demonstrates the ideals of Lean is in a much better position to provide great patient satisfaction (whatever that means) than one that doesn’t.
I think Saturn and Scion are two different stories. GM killed Saturn – the brand and the cars altogether, for a number of reasons.
Toyota says the Scion brand was a specific countermeasure to the Toyota brand not being cool for young people. Toyota says that problem doesn’t exist anymore, so the Scion vehicles will now be sold as Toyota. Or, that could be spin in their part. But, the cars aren’t going away.
Different reasons yes and no. Saturn had the better concept but made crappy cars. Scion had better cars but a crappy concept. Both dead in the end for failing to meet customer needs.
Too often our improvement efforts become disconnected from the symbiotic relationships between caregivers and patients. When asked about lean, Taichi Ohno once said, “All we are doing is looking at the time line, from the moment the customer gives us an order to the point when we collect the cash. And we are reducing the time line by reducing the non-value adding wastes.” In healthcare, when we do this patients are able to receive the services they need and want sooner, and caregivers are able to fulfill the reason they engaged in healthcare, to take care of patients.
Where lean efforts struggle is it because others can’t see the improvements or that we haven’t made the improvements clear? I believe we have a responsibility to make the improvements compelling and undeniable.
Or, when Lean efforts struggle, there could be an underlying lack of trust between employees and management or a number of other causes and root causes.
Excellent post! I often have to explain this to people that my company tries to engage with Lean. I wonder, how would you recommend handling a potential client that does not agree with this philosophy? Do you continue to give them educational materials and work with them in hopes that they will understand the long-term benefits far outweigh the short-term costs? With hopes that they will see some initial results from smaller projects and perhaps “come around” later. Or do you recommend implementing Lean with clients that are willing to take on this newer philosophy? Where is the balance, and at what point would it hurt the reputation of the company trying to help others implement Lean with companies that do not “fully” commit?
Thanks for reading and commenting, Molly.
Adopting a new Lean philosophy isn’t like flipping a light switch. There’s a difference between:
1) Understands there’s a new philosophy and is willing to work at it
2) Disagrees that there is a need for a new philosophy or disagrees that Lean/TPS is the right way
In case #1, you can and should continue working with them. For example, let’s say the executive and organization says they want to stop blaming employees, but it’s a hard habit to break. They will slip up, but they’re moving in the right direction.
There are some cases, though, that are just hopeless. If they reject the TPS philosophy, it’s probably less frustrating to, as a consultant, just move on. You’re right, having “bad clients” (those who are unwilling to learn) would eventually hurt your reputation.
Every consultant hopes to be at a point where you get to choose your clients… not just accept anybody who is willing to pay you for a while.
Thank you for your thorough feedback! It is very helpful to hear your thoughts.
We should start with making healthcare free for every citizen of the entire world. No matter wich country, every person on the planet has the right to free healthcare. That is the important thing to talk about. No more expensive medicines, have big money pay for this. Make it free so we can all focus on the important things in life. It will also greatly increase productivity.
Specific to leveraging Lean to drive patient experience, this is where nuance matters. The frustrating part is that many lean leaders and practitioners will listen to this and want to replicate VM’s path without understanding wht is the same and what is different.
Not that it’s easy for Virginia Mason to focus their Lean efforts on patient experience, but they certainly have a different patient profile than many of their local competitors. They have less than half the Medicaid population as Swedish. That may not seem spectaularly relevant, but it certainly impacts organizational strategy and drives prioritization (more complex patients, more co-morbidities/chronic conditions, more psycho-social variables, lower payer margins, etc).
Allocating resources specifically to drive patient experience is a luxury a lot of hospitals can’t afford. Being able to staff doctors, band-aid together IT systems, and minimize no-shows because their patients don’t have access to transportation is a very pressing reality for many health systems.
Many of the storied hospitals where traditional Lean has “worked” aren’t necessarily reflective of the average health system. They’ve either been in less-than-competitive geographic markets, had a solid payor base and low Medicaid population, or had huge endowments and broad resources that give them financial leverage no other hospitals have (I love the Cleveland Clinic and I’ve been a patient there, but they can solve access issues by hiring a half dozen pediatric intensivists – that’s not a realistic option for most other hospitals).
Lean isn’t enough. Denver Health figured that out even after winning Shingo. Lean leaders need to understand that and begin to expand their scope of knowledge beyond traditional Lean theory and applications. Many hospitals can more effectively improve access and patient satisfaction by hiring a Revenue Cycle expert than they would by hiring a Lean expert. Same principle applies for BI expertise or digital strategy capabilities. I grew up in Lean-heavy environments and I fundamentally believe in its value. But I also recognize that it’s rarely ever enough on its own. And lean leaders who don’t accept that usually end up making things worse for patients/clinicians rather than better (even when they perceive otherwise).