Today's Post in <50 Words: The key question is “Let's say your census is lower and you have a few hours left in the shift… do you send your people home or engage them in something useful that invests in your future?” Truly Lean hospitals will engage staff in improvement instead of sending them home early.
I get asked a lot, “How do you know if a hospital is truly ‘Lean?'”
Nobody is ever perfect or “fully Lean,” but you could ask, “How do you know if somebody is on a legitimate Lean transformation journey?”
If you could only ask one question that would give you a pretty solid sense about whether they're on the right path or not, what would you ask? I'll give you the question I'd ask later in the post.
What If You're On a “Fake Lean” Path?
It's almost easier to answer the opposite question, you could maybe identify some characteristics that demonstrate that an organization doesn't yet “get it.”
For example, an organization that only uses Lean tools and hasn't yet changed the way they manage — they're not really Lean… yet (or never will be).
Also, an organization that thinks Kaizen is only a series of weeklong RIEs, RPIWs, or projects instead of also practicing daily continuous improvement — they're not really Lean… yet (or never will be).
This starts sounding like the Jeff Foxworthy “you might be a Redneck” jokes that are so easily to lampoon.
I recently adapted that style of jokes and created memes that illustrate my concept of L.A.M.E. (Lean As Misguidedly Executed)… I used Bob Emiliani‘s “Fake Lean” term because it flows better, I think.
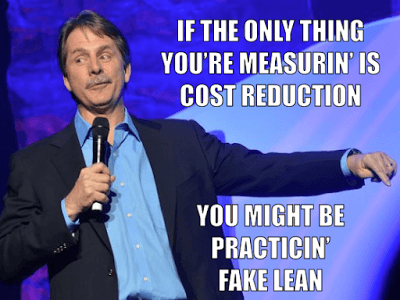
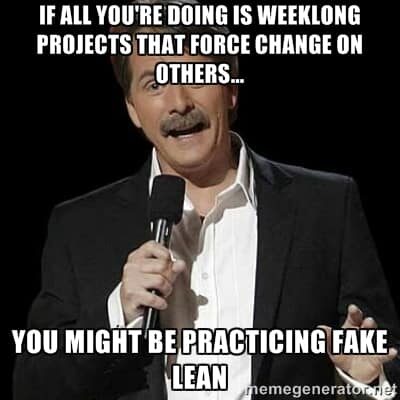
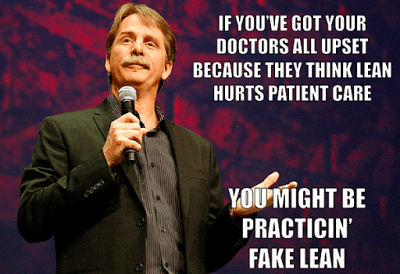
If you have another “… you might really be L.A.M.E.” or “you might be practicin' Fake Lean” meme to submit, leave a comment or submit it as a Lean Meme.
But What About Flexing?
I was at a hospital last month where their Lean efforts, after two years, they said they had very little energy or progress related to Lean. I'm not sure if me giving a talk would help, but that was the intent.
A nursing director complained about how their Lean consultants brought in the practice of “flexing” — or sending nurses and staff home early when the patient census is low. This really had people demoralized and managers were frustrated about being hounded for being 0.06% over their labor budget.
These consultants (no longer being used by the hospital) come from a background of being hospital executives and it's unclear where they had any real Lean training or experience… so they seem to do pretty well selling what they're doing as cost cutting (which isn't really Lean, either).
I'll say it bluntly: Flexing is NOT a Lean practice. It's a common healthcare practice… but it's traditional cost cutting. It's not “Lean.”
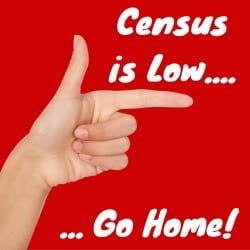
I've blogged about this before, back in 2009:
“The Emperor's Sacred Cow's New Clothes – “Flexing” Hospital Staff“
As I pointed out there, Toyota does NOT send employees home early to save money when production has stopped for some reason. They wouldn't do this if there was just two hours left in a shift. Heck, they don't lay off employees when a plant is down for WEEKS or MONTHS (see this blog post).
Hospitals think they are saving money and reducing costs by sending people home early. I bet the end result of “flexing” actually increases costs.
Does Toyota “waste money” by not sending people home? Of course not!
Flexing is NOT #Lean. Ask Toyota. They don't try to save money by sending folks home early. Share on XWhat does Toyota or a Lean organization do?
- Cross train people to learn new skills
- Work on Kaizen improvements
- Do other education
- Pay them to do volunteer work (during long shutdowns)
Why would Toyota pay people to build Habitat for Humanity homes? Are they really that caring? Do they have that much money to throw around? They're investing in their people, in addition to helping the community and building up goodwill. Volunteer work is a great way for team members to get to know each other, which can improve workplace performance, and to develop and practice leadership skills.
If you're at a hospital, when you temporarily have “too many employees,” where does your mind go?
- Let's send them home to save money and make today's productivity number look good
- Let's keep paying them and invest in our future quality, productivity, and staff satisfaction
Paying hospital staff to work on improvement should have many positive results. I guess that's probably only true if you have a formal Kaizen methodology (otherwise, you might just be paying people to stand around and talk).
Cost savings isn't the primary goal of Kaizen, but I'd be willing to bet that paying staff to work on improvement would have a POSITIVE return on investment… not every single day, but over time. Improving safety and quality will reduce costs. Staff feeling more valued might lead to fewer people quitting out of frustration, which reduces your turnover and hiring costs.
There is so much potential that gets thrown away when hospitals reflexively send people home early. Share on XSo here's another new Foxworthy meme:
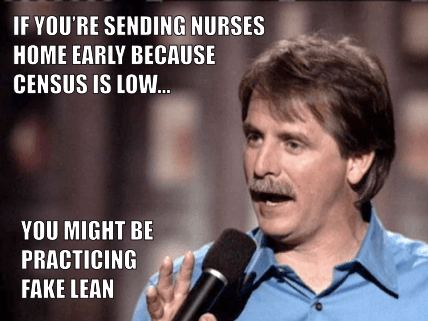
Flexing staff is a classic example of short-term thinking versus Toyota's long-term thinking. Focusing on the long term is point #1 in the Toyota Way for a reason. Sending people home today saves you money in the short term and that's easy to measure. The benefits that come from paying them to do improvement work… that's more long-term and harder to measure.
But, being able to focus on the long term, respect your people, and engage them in improvement… that's the sign of a mature Lean organization.
So, if I had just ONE question to ask to see if a hospital is really an advanced Lean thinking organization or not, if they were on a Lean journey that would make me optimistic about their future, I'd ask:
“Let's say your census is lower and you have a few hours left in the shift… do you send your people home or engage them in something useful that invests in your future?”
I'm not sure how many hospitals pass that test today. Hopefully, more will in the future. Does yours?
Please scroll down (or click) to post a comment. Connect with me on LinkedIn.
Let’s work together to build a culture of continuous improvement and psychological safety. If you're a leader looking to create lasting change—not just projects—I help organizations:
- Engage people at all levels in sustainable improvement
- Shift from fear of mistakes to learning from them
- Apply Lean thinking in practical, people-centered ways
Interested in coaching or a keynote talk? Let’s start a conversation.
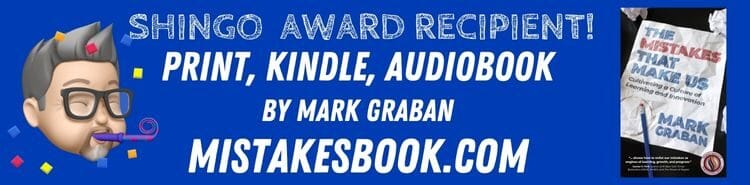
One question that I like to ask the folks at the top is:
“What are you personally doing differently on a daily basis as a result of Lean?”
Usually, the answer is nothing – or, a L.A.M.E. answer is given.
Flexing an old practice used in manufactories 100 years ago. Amazing that it is still used today, and in hospitals of all places. Sad.
Great question, Bob. Too many “L.A.M.E.” or “Fake Lean” initiatives involve executives delegating Lean instead of participating… and, like you said, changing their own ways. John Toussaint is a great example of an executive who had the humility to admit his own leadership style was harmful and he worked to change his ways.
Very sad, indeed, about “flexing,” especially since I’d guess the practice doesn’t really reduce costs over time.
When I previewed this post on Twitter, here are some other questions shared by people:
Other articles on “flexing” —
‘Go Home, Stay, Good Nurse’: Hospital Staffing Practices Suck the Life Out of Nurses
AJN Report: The Other Side of Mandatory Overtime
More:
Nurse Staffing Costs Must Be Weighed Against Cost of Errors
As Keith Leitner from the University of Tennesee said today at the Society for Health Systems conference:
“The best #Lean organizations in the world treat labor as a FIXED Cost. Treating labor as variable cost is dangerous.”
[…] be that leaders don’t understand Lean and they equate it with cost cutting. Or they’re sending nurses home early in the name of Lean (which is NOT Lean). Or the leaders are only driving top down change. Real Lean […]
[…] Is This The One Question That Determines If You’re Truly a Lean-Thinking Hospital? […]