My whole career, I have worked with the Lean methodology (aka the Toyota Production System).
I've just really never done much with Six Sigma. I've read about Six Sigma. I took a Green Belt course when I worked at Dell in the late 90s. I've studied and used statistical methods (especially what I learned in my Industrial Engineering studies and at MIT), but I've never done anything I would call Six Sigma in my career.
I have respect for Six Sigma as a discipline, just as if I were a chef, I would have respect for pastry chefs. They can co-exist in the kitchen. You might both use whisks, but you have slightly different training to do different things. These roles aren't interchangeable, and neither are Lean and Six Sigma. That's one reason I get riled up about so-called “Lean Sigma” or “Lean Six Sigma.”
Most of the “L.A.M.E.” (Lean As Mistakenly Explained) examples that I see on the interwebs come from “Lean Sigma” discussions, especially on LinkedIn.
What are the fallacies that are thrown around? They include, but are not limited to:
- Lean is about the average, Six Sigma is about the variation
- Lean is about internal processes, Six Sigma is customer-focused
- Lean is for efficiency; you need Six Sigma for quality (this one is the fault of Mike George and his books, many say)
- Lean and Six Sigma are just toolboxes, and you use whichever is appropriate for the problem at hand
These are all incorrect, as somebody with good Lean training or Lean experience would realize.
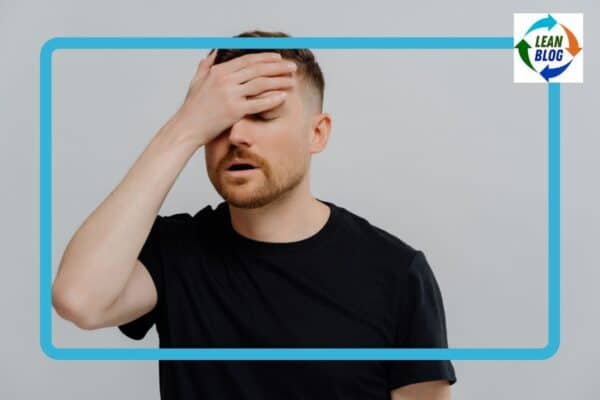
Truth: Lean focuses on the average AND variation
I've used Lean in settings like hospital laboratories where the focus was on both the average testing turnaround time and reducing the variation. This was done by improving flow, reducing batching, improving the standardized work and having a kaizen, or continuous improvement, process in place. I'm sorry, we didn't “need” Six Sigma to focus on variation.
A related fallacy is to say, “Lean doesn't use statistics.” Toyota doesn't practice Six Sigma in any formal way, but they use the “7 basic QC tools,” as do many Lean people (including histograms, etc.).
Truth: Lean is inherently customer-focused
In this hospital lab testing improvement work, we talked with doctors and nurses (“internal customers”) and patients and their families to figure out which lab tests were the highest priority for fast and accurate medical decision-making and what patients thought about being woken up at certain times of the morning to have their specimens collected. Lean hospitals often include a patient or two in “Rapid Improvement Events” (something that should be done more often, actually).
It's not hard to find stories in the Toyota literature (including Jeff Liker's books) about that company's deep respect for the customer and the deep understanding of the customer's needs from a product design and manufacturing standpoint (although, reportedly, the Toyota dealers in the U.S. still have a long way to go).
Truth: Lean is about flow AND quality
The two pillars of the Toyota Production System are “just in time” (improving flow) and “jidoka” (quality at the source) – see the diagram of the “TPS house” here. There is a “lean six sigma” healthcare book that says explicitly (and completely incorrectly) that Lean addresses every type of waste except for the “waste of defects” and that you need Six Sigma to address that.
Malarky!
Lean (going back to the roots with Toyota and Dr. Deming) is inherently a quality improvement system. Quality and flow go hand in hand. That's a lesson I learned well when I worked at GM under our plant manager who had been one of the first GM leaders to work at the famed NUMMI plant (Larry Spiegel, he was quoted in this radio story).
Truth: Lean is NOT just a “toolbox”
Lean is a quality improvement system, a management system, and an organizational culture. Or even mainly a philosophy.
I read something the other day, again, about the “toolbox” thing. I've had many people tell me that their “lean sigma” training was almost entirely about Six Sigma and that they had a few hours of introduction to Lean tools, like 5S.
I don't blame the individuals who are spouting these fallacies about Lean being just a toolbox. They are only regurgitating what they have read or what they have been taught by some “certified Lean Six Sigma master black belt” (or CSLMBB). They sadly don't have exposure to Lean as a management philosophy, as I did back to my early days at GM (again, thanks to people like Larry Spiegel, not the average old-school GM managers).
People are certainly free to do whatever they want. I just wish when they are only using a “Lean toolbox” (or just one tool) that they don't call it Lean.
Call it “5S Six Sigma.”
Call it “Lean Toolbox Six Sigma.”
Better yet, keep the name “Lean” out of it, please.
Final thought – lest I get accused of being “anti-Six Sigma,” that's not the case. I'm opposed to misrepresentations of the Lean methodology. This kind of malarky hurts everybody who is trying to do things the right way. I'm opposed to “L.S.S.A.M.E.” This isn't a “fight between Lean and Six Sigma” — it's a fight between knowledge and ignorance.
Please scroll down (or click) to post a comment. Connect with me on LinkedIn.
Let’s work together to build a culture of continuous improvement and psychological safety. If you're a leader looking to create lasting change—not just projects—I help organizations:
- Engage people at all levels in sustainable improvement
- Shift from fear of mistakes to learning from them
- Apply Lean thinking in practical, people-centered ways
Interested in coaching or a keynote talk? Let’s start a conversation.
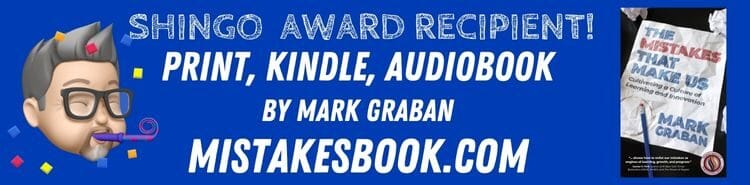
“…it’s a fight between knowledge and ignorance.”
This problem illustrates how difficult it is to be fact-based, in part because being fact-based requires work. University professors teach students how to do research (get the facts) and analysis (think critically) in order to improve one’s understanding (e.g. avoid fallacies) as a precursor to effective decision-making (i.e. avoidance of illogical thinking and decision-making traps). Research is a practical activity.
It is remarkable how, after graduation, few actually use the research skills they learned in school. They likely thought their research assignments were an academic (i.e. theoretical) exercise, but the problem cited in your post is entirely practical and could be corrected by doing some simple research.
Misrepresentations of progressive management are many and varied, and have existed for over 100 years. This nothing new. However, we should not fool ourselves into thinking our job would be easier if these misrepresentations did not exist.
“Lean is a quality improvement system, a management system, and an organizational culture.”
That covers it, Mark. Lean is all of those; its an overarching mindset. It seems people are in to buzzwords more than they are the mindset. They want a quick-fix toolbox rather than a discipline.
Whether I crack my egg in the middle or at the end, it’s still cracking an egg. Thank you Mark for exposing the truth.
I like to point out that Six Sigma is much more focused on specific projects – whereas Lean focuses on the culture. As I gain more and more experience I understand that culture is extremely significant. Projects – less so.
What I find is those that are more knowledgable in each area are more likely to be useful and to understand what you are saying. Many people that think they are doing lean are really just applying a couple lean (or quality) tools without really practices lean.
The people that really know there stuff about six sigma I find are very good. But the vast majority of people that say they are using six sigma are just applying a couple tools without really practicing six sigma.
It seems that often very watered down versions (of lean, six sigma or previously TQM, reengineering…) are sold to organizations. Those watered down versions are normally lame and often include lame strawman explanation of other methods.
http://management.curiouscatblog.net/2006/03/15/six-sigma-wont-fix-bad-management/
“Question: For a firm seeking to improve – what comes first? Six Sigma quality or lean implementation?
James Womack: Agh! These are all the same thing. You need to start with the value stream for very product, draw a map of its current state…”
http://management.curiouscatblog.net/2005/11/27/management-improvement/
One interesting difference is how little good six sigma content is available online. There are easily 20 great blogs on lean and it has been extremely difficult to find much good content at all about six sigma since the web exploded in popularity.
I also do find a higher rate of lean implementations that go beyond the extremely surface use of a few tools than I do with six sigma efforts. Lean is more likely to result in actual changes in management thinking in my experience.
It is also funny (to me) that the vast majority of the tools in the toolbox for lean or six sigma were tools in the TQM toolbox before they became “lean” or “six sigma” tools.
I think one of the big problems is that Lean and Six Sigma are not comparable disciplines. As you mention, Lean is more about culture and should permeate every fiber of the organization. Six Sigma is a set of tools for improving the quality of a line.
I have no problem raiding the Six Sigma toolbox while rolling out Lean. I like to think of projects in terms of DMAIC or DMADV and I like the rigid, structured view of quality and customer requirements. This works well because Six Sigma tools are meant to be used on projects and processes.
Lean tools are different though. Primarily, Lean tools are used to teach Lean thinking much in the way that martial arts sequences are meant not to be used, but to teach muscle memory. While Lean tools can absolutely be applied, looking at them at project tools instead of teaching aides robs them of their true potential.
It is also funny how a typical SS guy would narrow down the scope of the problem (“in scope/ out of scope” and thinks he is doing a great job). A good lean practicioner would keep pushing the boundaries of his scope out to include as much as possible for he takes a more systemic view to processes and knows that lean approaches are about building a culture and managament practice of trying to get closer to the ideal state
When I hear Lean Six Sigma, my initial reaction was never positive…as I reflect on the two I notice that companies steeped in Six Sigma like to add the Lean. In my experience, Six Sigma is Problem Solving, just like PDCA. As I reflect on my GB/BB certification, what the Six Sigma methodology (i.e. DMAIC & DMADV) has provided is a structured approach to solving precision type problems. PDCA, in my experience, yields a much broader Problem Solving approach. Companies that do not have a set problem solving methodology tend to take from both Six Sigma & PDCA.
As a former (albeit short lived) consultant, which sounds catchier “Lean Six Sigma” or just “Lean” to a potential client who has not spent the time to determine the difference?
I agree that they should be separate. In fact, I was mistakenly sent an email from an organization trying to implement a six sigma program. I had invited a couple of their green belts to visit and see how a lean culture works. The email basically said that the sender didn’t want to hear any six sigma bashing. I don’t really believe that six sigma is sustainable from what I have seen. Lean thrived with my employees. Six sigma has not produced any sustained gains at the other organization. Without culture, it seems like regression happens almost immediately. This is also true of lean. Without Executive Champions, lean events eventually regress.
Just when I thought the days of “purist” thinking had passed, I get a link to this blog and suddenly I realize that improvement practitioners still focus on petty arguments with regard to philosophical underpinnings of methodology to the detriment of real advancement of the science of improvement and more importantly to the detriment of improvement efforts. Are we as an improvement practitioner community not beyond that? Is there any single improvement philosophy that has proven to be without limitation in and of itself? Certainly not Six Sigma; certainly not Lean (there is no such thing as Lean, it is a coined term for TPS); and certainly not Lean Six Sigma. A decade after the introduction of Lean Six Sigma (yes, by Michael George’s insightful books on the matter) we as a community still act like the science of improvement is static; it is either “this philosophy” or “that philosophy”. Is it no wonder that the demonstrated results of improvement efforts have been so spotty and in those cases where improvement efforts have been successful, so short lived?
I suggest that we, as a community, stop holding on to aging ideas and philosophies; not because they are inherently wrong, but because we should be focused on building on these ideas to find solutions that produces results for the organizations and entities which need improvement to remain competitive and effective. Oh and thanks for the new revelation that “culture” is an important part of improvement efforts. What a novel concept.
John – You are responding to a blog post that’s different than what I wrote.
I didn’t say Six Sigma doesn’t have value or that Lean and Six Sigma can’t work together. My complaint is with “Lean Sigma” people totally misrepresenting Lean.
You say we should keep things moving forward. I’m trying to help Lean Sigma move forward.
Lean Sigma seems to think that Lean is just about flow (that’s a 1980s view, see “Just In Time”).
Lean Sigma seems to think Lean is just a toolbox (that’s a 1990s view).
Those are the “aging” philosophies that Lean Sigma needs to move past.
Mark
Although not the point of this post, I think at the tools and project level Lean and Six Sigma can be highly complementary and in some respects are similar. The same could be said for the clinical trials model where scientists, who have never heard of PDSA or DMAIC, have reduced the mortality for some diseases by a factor of 10.
At the cultural and management system level, Lean and SS are very much different and highly incompatible. So, this is a point worth discussing at a different time.
I think Mark is right on with suggesting Lean Tools Six Sigma as the better descriptor for most LSS efforts considering the cultural and management aspects of the TPS are almost always ignored. I have seen some great project work from organizations that have adopted LSS as an improvement model. However, I am doubtful that they will achieve lasting organizational success by just working great projects. The same is true of the Lean project organizations. The right terminology might help enlighten leaders that there are aspects of Lean (more correctly, TPS) that can better move the organization to true North.
Michael George made a mint coining the term Lean Six Sigma. If I could write a book on “TPS Six Sigma” maybe……..
TPS already has built in problem solving structure..A3 Thinking (based upon Deming’s PDCA).
I think your onto something with the “Project” call-out that more than most companies employ.
Awesome blog. Thanks so very much for putting this discussion out there. As a Lean practioner since 2003, I have been trying to think through this Six Sigma madness. I even went through Green and Black belt training to help my mind understand the debate. (SixSigma.US). Every Six Sigma black belt problem being solved in my class was a Lean flow problem! LOL. Thanks again for this great content.
1) Lean.
A systematic approach to identify waste, focus activities on eliminating it, and maximize (or make available) resources to satisfy other requirements. Lean is a journey of continuous improvement rather than a destination. There is no -•end point-–… only a never ending journey of relentlessly eliminating waste.
2) Six Sigma.
A strategy that increases efficiency by statistical process control. A Six Sigma organization can be understood as having only 3.4 defects per million opportunities. Six Sigma relies on a repeatable 5 step approach to project management and problem solving.
I have always been taught if you have a problem…
step 1) Clarify and Validate the Problem
A3 Thinking
I still don’t understand why GE had to muck up Sick Sigmer with Lean anyway.
Six Sigma Stupidity destroyed them. Jack Welch said that Harry was like a madman and no one had any clue what he was talking about. Jack handed over $1B anyway. A scam was born!
Six Sigma is a destructive scam based on pure farce. It was created by psychologist, Mikel Harry. Harry claimed that all processes drift by +/-1.5 sigma, every 50 measurements, making them wildly out-of-control and unpredictable. It is hence impossible for a Six Sigma process to produce quality product, no matter where specification limits are set. Harry based his ludicrous claim on the height of a stack of discs! EVERY aspect is as worthless as its laughable foundations.
Dr Wheeler, the world’s leading process statistician, calls Six Sigma “GOOFY”. CBS calls it the most stupid fad of all time.
Of the 58 large companies that announced Six Sigma programs, 91 percent have trailed the S&P 500 since. Six Sigma has helped destroy its once best references GE and Motorola.
Why do people turn their backs on the great men of QUALITY: Professor Deming, Professor Lewis, Professor Ishikawa, Dr Shewhart and Dr Wheeler, for the lunacy of psychologist/salesman Mikel Harry.
Please read my papers exposing the Six Sigma scam:
https://www.linkedin.com/pulse/broken-dr-tony-burns/
https://www.linkedin.com/pulse/blame-mr-bill-smith-tony-burns/
https://www.linkedin.com/pulse/six-sigma-psychology-part-2-tony-burns/
I look at TPS as making problems visible and solving them at the lowest level possible, while they are small and have very little interation.
I look at Six Sigma as having let problems accumulate that they are so deeply ingrained in the system/process, you can’t tell where to look without using some complicated tools.
I guess the question comes down to, “Where does the organization want to invest their time and resources?”
I agree “we” as practitioners need to move beyond this argument. I wouldn’t call it petty though. Observing the digital landscape (i.e. gemba/genba) as well as other key indicators (e.g. job descriptions), a person cannot ignore the many different flavors, approaches, etc., that in reality confuse the management teams as to which way may or may not be right for their company.
To illustrate the superficial understanding, I recently came across a discussion between two people on Twitter that was about Lean Sigma Six…
Having been a GE MBB as well as in a company that was well down their Lean road for some 15 years already, let me reflect upon both.
Six Sigma can be found in a full “version” or “lite” (only DMAIC with only some tools used), but its key characteristic in companies that use it, is that it almost always is a project-oriented, expert-driven, top-down initiative, with difficulties to sustain when the so called project pipelines starts drying up. At GE, I did experience Six Sigma as a culture by the way. This, because it was a language and a mindset that was present in almost all conversations and management team meetings. I have yet to come across another company that measured delivery reliability as span instead of a percentage. But despite its every-day presence, the improvement projects were still mostly add-on projects. And most other companies don’t even get into their day-to-day culture.
To embark on Six Sigma is relatively easy for leaders as it can be easier delegated to specialist teams. However, it therefore also is easiest to drop when leaders change.
Can Lean be approached like above as well? Sure it can, and many companies also see it as a top-down, expert-driven initiative with projects (or events). And they delegate it to Lean experts, coaches, yes even senseis. So there can be poor Lean just as much as there can be poor Six Sigma.
But Lean in its “full version” (if there is such a thing) encompasses a lot more than the “full version” of Six Sigma. There is a reason why the companies that are truly on a Lean journey, almost never speak of Lean. They speak of their production system, their way. Beacuse that’s what it is: a way of doing and running a business in all of its elements and aspects.
By the way, I still use (and see) a lot of good elements from Six Sigma (or Quality/TQM before it) in my mostly Lean work. It has made me much more aware of variation, it helps me with measurement quality, I still use a lot of SPC in my thinking and doing, and use pFMEA and PCPs in developing standards with the teams. Are these elements Six Sigma, TQM or Lean elements? Does it matter? As long as the nderlying principles and thinking is sound, and organizations put it to use consistently and coherently to develop and evolve their own production systems and ways, they can strengthen each other.
The key differentiator for me isn’t the tools, or even the project orientation (Lean also needs projects), but Leans broader scope as a system ecompassing a mindset, a way-of-seeing and accompanying principles resulting in an ever-evolving total business system.
Rob – thanks for sharing your experiences and insights.
To reiterate my position from my post – this wasn’t at all about “which is better,” Lean or Six Sigma. My beef is with Six Sigma folks (“Lean Sigma” people) who are espousing Lean Lite or Lean = Toolbox.
It doesn’t matter if SPC, FMEA, etc are labeled as Lean, Six Sigma, TQM — they are good, sound, proven practices based in science, not superstition.
[…] Just Call it “5S Six Sigma” Instead of “Lean Sigma,” Please […]
[…] full story on leanblog.org var featureBoxVar = "";See all posts on LSS topics of common interest Click here to know how Lean […]
[…] As I’ve written about before, this discussion about the merits of “Lean Sigma” has nothing to do with the merits of Six Sigma. The rigorous statistical methods of Six Sigma are certainly valid and can be quite useful… keeping in mind that Toyota, if you care about them as an example, doesn’t do formal Six Sigma. They use the “7 basic QI tools” that form some of the foundations of Six Sigma, but they don’t formally train or designate “belts.” I think this is a very practical approach that serves many organizations well, including in healthcare. […]
we can all agree that the main purpose of lean is to reduce waste while it is reducing variation for six sigma.Don’t you agree? with that being said, I feel like reducing variation is a reduction in waste. However, in you opinion what is a case where it is better to use either lean or six sigma, but definitely not together?, besides to avoid extra cost.
You mean 5S Six Sigma Stupidity.
EVERY aspect is as worthless as its laughable foundations based on the height of a stack of discs. Lean was tacked on merely to prolong the scam.