As we sit in seat 26A, mindlessly watching a movie, we take for granted that our cell phone (or the shirt off our back) won't be suddenly sucked out through a gaping hole in the side of a plane. That's because the odds of this happening are unimaginably low. Until now, that is. Are we entering a new era where shoddy manufacturing (or maintenance) exposes us to more risk, reversing a decades-old trend of greatly improved aviation safety?
On January 5th, an Alaska Airlines 737 MAX-9, designed and assembled by Boeing, safely executed an emergency landing after a “door plug” blew out of the plane's left side. Thankfully, the resulting hole and loss of pressure didn't suck out any passengers or crew.
Now, the window and middle seats next to the door plug were thankfully empty. That raises questions about what Alaska knew and what chances they were taking by continuing to fly the plane after previous complaints about “whistling sound” and alerts about cabin pressures on previous flights that plane took.
The crew performed valiantly in these circumstances, and we should celebrate them. This incident creates an opportunity for the aviation industry (including regulators) to learn how to ensure this sort of door plug failure never happens again.
Instead of blaming human error, people should ask why the company didn't have better systems to prevent or detect the mistake or mistakes that led to this incident. Some leaders throw up their hands and lament,
“It's human error… we'll never be perfect… so what can we do?”
Instead of leaving that as an unanswered rhetorical question, we need to work at it seriously. What can we do to prevent mistakes and protect ourselves from human error?
Hear Mark read this post — subscribe to Lean Blog Audio
Don't Blame and Insult Workers
In the aftermath of incidents like these, many people have an unfortunate habit of asking, “Who screwed up?” and “How much should we punish them?” instead of asking more constructive questions, such as “How could this have occurred?” and “How do we prevent it from happening again?”
I cringed when I read an opinion piece online that blamed the incident on:
“…some idiot [who] didn't screw in the bolts tightly enough.”
The author later added, unhelpfully and inaccurately,
“I am confident that I could do the job correctly, and I write for a living.”
I'd bet he could not. Captain Dunning, meet your co-pilot Kruger.
There's no need to insult factory workers or whoever the author thinks the “idiot” might be. The act of a person tightening a bolt is not hard in isolation.
What's difficult is doing an assembly job while supervisors press people to work at breakneck speeds and look the other way when employees cut corners on quality, all in the name of keeping up with the production schedule at all costs. That's a leadership problem, not a worker problem.
Ford used to say, “Quality is Job 1“–but in many companies, the sad reality is that quantity is the top priority, a message reinforced by executives on down.
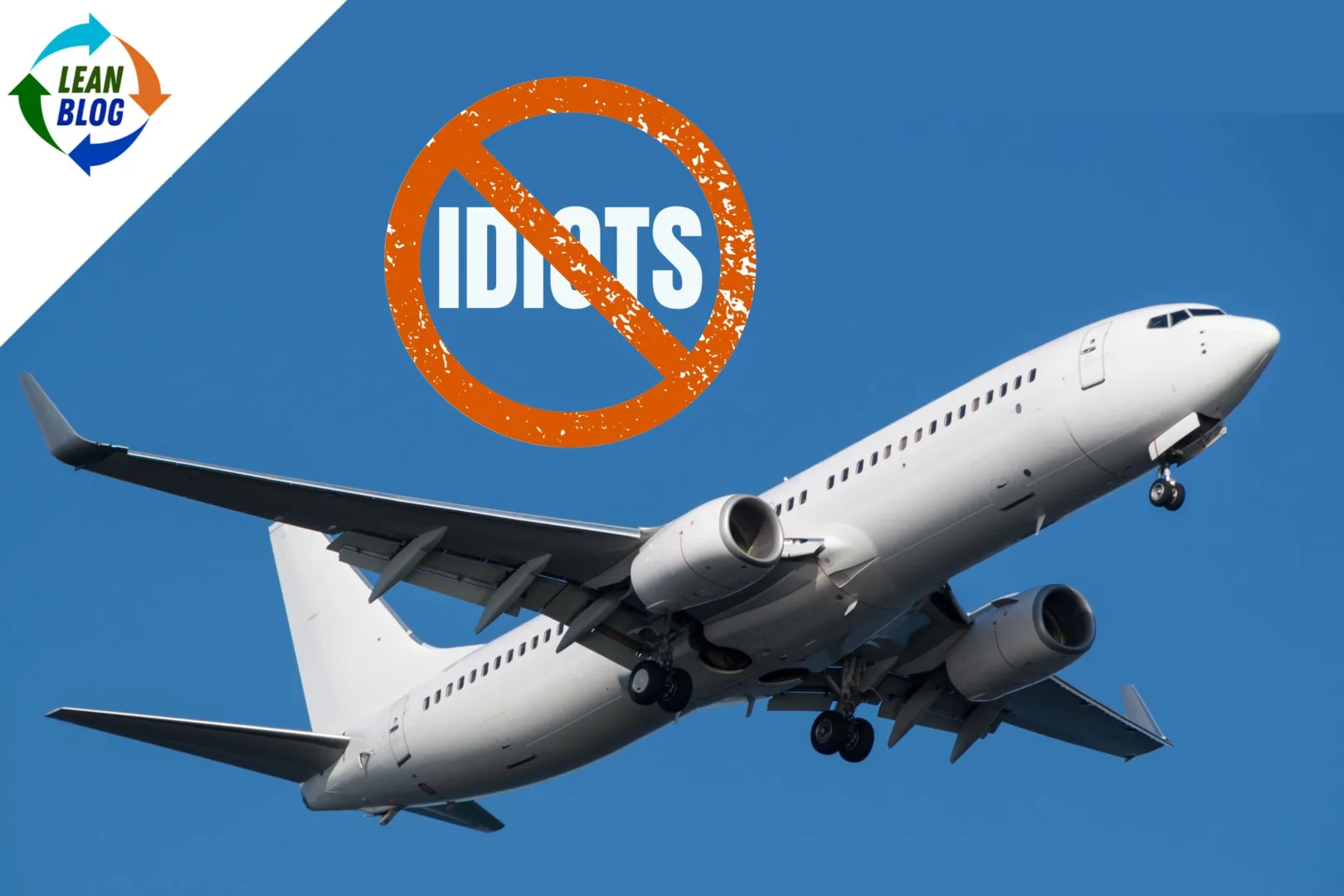
Stop Talking About “Idiots”
The way to prevent mistakes with bolts and other essential items on the plane is for everyone to stop talking about and blaming “idiots.” The root cause of the Boeing incident is not an idiot or multiple idiots. It's easy and even fun to blame people. Instead, we need to look at complex (and seemingly boring) things like processes, systems, management, and culture.
Why?
Because improvements in those factors have helped commercial aviation become the safest mode of transportation by far, as measured by fatalities per mile traveled. The last commercial aviation fatality in the U.S. was in 2009, more than 14 years ago. Previously, the longest stretch between fatalities was two and a half years.
In part, aviation is so much safer because of a mandatory incident reporting system that, by law, cannot punish individuals who use it to report incidents or near misses. Hospitals do not have such structures and cultures in place, so mistakes get repeated ad nauseam.
Manufacturing is a team effort, and results should be recognized as the output of a team, which includes production workers, engineers, other specialists, and every level of leadership. In Boeing's complex supply chain, this includes teams who initially attached the bolts holding the door plug to the fuselage (work done at Spirit Aerosystems, a supplier), the team at another supplier who allegedly re-installed the door plug after installing the wi-fi system (that company later said they didn't touch the door plug).
If you have the unlikely scenario of a team of “idiots,” one might ask, “Who are the idiots who are hiring… all those idiots?”
Focus on Creating Good Systems Instead of Blaming Bad People
Toyota is arguably the world's best manufacturer and its famed production system has been emulated (to varying degrees of success) by other automakers, manufacturers, hospitals, local governments, and more. Toyota's success can't be attributed to hiring smarter or less mistake-prone employees. Their success results from preventing mistakes instead of firing people after each mistake.
Toyota has reduced quality problems over the decades by focusing on process details. They create and continually revisit detailed standardized work that shows how work is done and explains why they must do certain key elements a certain way. Toyota uses rigorous training methods to ensure people can do the right work the right way. They also have a notable culture of continuous improvement, where every team member can point out problems and implement suggestions without fear of punishment.
In other words, employees feel like they have a high level of “psychological safety.” Toyota has cultivated a culture where anybody is empowered to stop the line if they see (or even suspect) a quality problem. Quality truly is supposed to be Job 1 at Toyota, and companies like it.
Part of the intelligent system design at Toyota is incorporating “mistake-proofing” into machines, manual assembly, and other work processes. Effective mistake-proofing makes it easier to do the right thing and harder (if not impossible) to do the wrong thing. Mistake-proofing makes it easier to quickly detect (and resolve) mistakes that still occur. And Toyota has a strong culture of reacting to mistakes in ways that focus on learning and improvement instead of punishment.
The Japanese phrase used to describe mistake-proofing is “poka yoke.” It's OK, there won't be a quiz. Decades ago, Toyota leaders used a similar phrase, “baka yoke,” which quite literally means “idiot-proofing.” As lore has it, a production worker understandably got upset at this phrase, and Toyota shifted to focusing on the mistake and its root causes, not the person.
Edit: I found the story as told by Shigeo Shingo in one of his books and blogged about it here:
Firing “Idiots” Means Some New “Idiot” Will Make the Same Mistake
I recently heard about a food manufacturer where an employee used an industrial mixer to make a ground-meat kofta. When they pressed the button to start the machine, they discovered they had left a large mixing spoon inside, which destroyed the mixer.
The company fired the worker and apparently did nothing to prevent future mistakes. They likely thought they had fired an “idiot”–without reflecting on why they previously hired that person or, more importantly, what elements of the system caused that employee to make that mistake. It was a matter of time before a new worker made the same mistake, destroying another mixer.
Read the blog post about that story:
A more effective approach would be some form of mistake-proofing, such as wiring the mixer so it could not start until the worker places the spoon back onto its holder. Without that sort of process focus, how many people (and mixers) would that company cycle through before fixing the process instead of firing more people? Does anybody ask, “Who's the ‘idiot' who's running that place?” The owner is also likely not an idiot–they're probably a smart person who hasn't been taught better ways to manage.
Thankfully, I've been taught that “human error” should never be seen as the root cause of a problem. We're all susceptible to human error, regardless of how smart we are. We get fatigued, distracted, and forgetful, amongst other inherent faults in humans. When individuals make mistakes, leaders must delve into the system and situation that caused or allowed that mishap to occur, asking questions starting with “What?, “Why?” and “How?” instead of “Who?”
Toyota famously asks “Why?” five times to dig beneath the surface of a problem to a deeper root cause, a practice emulated by many tech companies as part of the “Lean Startup” methodology.
Read about “the many whys“:
Work to Prevent Mistakes and Human Error
Companies like Toyota work diligently to prevent errors and quality problems. For example, they eliminate the risk of a worker grabbing an incorrect part by using sensors to detect somebody's hand reaching into the wrong bin for a particular car. Companies can use wrenches that automatically tighten to the correct torque. Some bolts are designed to look different if they haven't been tightened at all. They don't just react to each mistake that occurs; they proactively seek out potential mistakes so they can be prevented before they first occur.
Human error in the cockpit caused many catastrophic aviation accidents of the past. But drilling down scientifically to the root causes reveals factors such as miscommunications or a co-pilot being afraid to speak up and challenge the captain about a potential problem. Aviation is so much safer today because the industry (and the pilot profession) focuses on learning from each mistake in a way that leads to more improvement and prevention than blaming an individual ever could.
Aviation reduces the risk of human errors due to fatigue by limiting how long pilots can fly or how many hours they can work in specific periods. Pilots use checklists to ensure they don't forget a critical step in a stressful situation. Aviation will learn from the factors that led to the fatal mistake of the Japanese Coast Guard plane being out on the Haneda runway when it shouldn't have. That analysis is still ongoing, and the learning will continue.
Toyota leaders are fond of saying,
“It's a leader's responsibility to create a system where people can be successful.”
That's a far better approach than saying, “We'll throw good people into a crappy process and blame them when something inevitably goes wrong.” Blaming others serves only to deflect responsibility from leaders; it doesn't fix anything.
Ask More Constructive Questions to Prevent Future Mistakes
Instead of blaming an “idiot” (or a collection of “idiots”), we should ask more constructive questions, including:
- How well had the worker(s) involved been trained?
- What checklists or other forms of mistake-proofing were in place to ensure the bolts were attached and tightened properly?
- How effective were inspection steps that would have caught an assembly mistake?
- Had they found a problem with door plug bolts on previous planes, and what, if anything, was done to improve the process other than just tightening that plane's bolts?
- Were workers pressured to keep quiet about problems to keep production running without delay?
The general public doesn't know enough about manufacturing companies to pontificate about supposed “idiots” in functions like training, quality assurance, or human resources–or in the executive suites. The flummoxing question is why companies full of smart people do apparently dumb things collectively.
In settings including manufacturing and healthcare, the system itself causes mistakes, defects, and harm–and invariably avoids being scrutinized. It's easier to blame an employee, even if that's ineffective, and companies seem to get away with scapegoating an individual in the court of public opinion. Experts point to the cause of this most recent Boeing incident being a manufacturing execution error rather than an inherent design flaw.
The initial NTSB report (released after I initially published this post) makes clear this seems to be the case, where the four bolts in question were left off completely after some repair work was done by Boeing (prompted by the need to rework some of Spirit Aerosystems' quality problems that were found).
With the MAX-9s grounded, investigators have found problems on additional planes. Even if the same so-called “idiot” worked on each plane, Boeing, as a company, failed to prevent the problem or to catch it before the plane shipped to the airline.
I can more easily brush off some commentator ignorantly throwing around the “idiot” word. It's far more damaging when plant managers, manufacturing executives, or even hospital CEOs think their quality or safety problems are caused by “idiots” instead of looking in the mirror to take responsibility for the broader processes, systems, and culture (or lack thereof) that are really the root cause of defects, problems, and deadly or even scary incidents.
Please scroll down (or click) to post a comment. Connect with me on LinkedIn.
Let’s work together to build a culture of continuous improvement and psychological safety. If you're a leader looking to create lasting change—not just projects—I help organizations:
- Engage people at all levels in sustainable improvement
- Shift from fear of mistakes to learning from them
- Apply Lean thinking in practical, people-centered ways
Interested in coaching or a keynote talk? Let’s start a conversation.
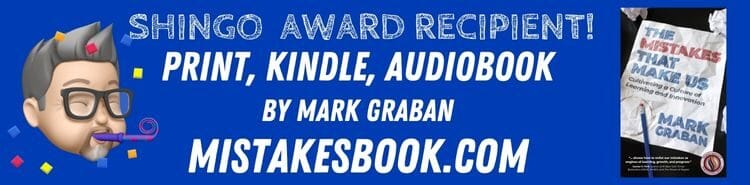
Here’s another data point about how pervasive the blame game is in the business world.
CNBC’s Jim Cramer (not a manufacturing expert) said in this video that #Boeing should fire the person or people responsible for those bolts allegedly being missing from the door plug… see about 3:15 into the video.
If it were only that simple.
It’s a matter of process, systems, incentives, and culture. Blaming and shaming (and firing) an individual or a few people does nothing to prevent future mistakes.
I read with interest your article on the recent incident involving Boeing. I found your reflection on the need not to criticize individual workers, but rather to explore processes and systems, very interesting.
As a supply chain management student, I see parallels with your analysis, particularly when it comes to the importance of well-established processes. The reference to Toyota’s approach is particularly relevant, highlighting the efficiency of their processes and their culture of continuous improvement.
The idea of “poka yoke” is intriguing, especially with the real-life example you provided. This shows how creating intelligent systems can help avoid mistakes.
With the constant development of new technologies, I wonder how emerging technologies such as artificial intelligence and automation could be used to improve the quality and safety of manufacturing processes.
Louis Jamard
I completely agree with everything that you have to say about this topic. Your first point about blaming and insulting workers should 100% be talked about more. It is extremely ineffective to place blame on specific people, because doing so frequently ignores the larger context of the procedures, and management.
I also really appreciate you using the “poke yoke” phrase, as that is something we are currently reminding ourselves to remember as a supply chain student. This phrase should speak to the boing corporation, and how they should develop a focus of constant development and a dedication to building processes that reduce the possibility of errors happening in the first place.
I appreciate your take on this subject, and am looking forward to reading more of your work.
Amia Kharitonova
I found this post very interesting, especially since my class is currently delving into topics like poke-yoke. Toyota’s reputation as a model for efficient manufacturing is often highlighted and I was fascinated by some of the measures they have taken to mistake-proof their processes, such as wrenches that have the ability to tighten bolts to the required torque and bolts that visually indicate if they’re improperly fastened.
In this specific instance, the door plug came loose due to missing bolts which were installed by another supplier. My question is, does Toyota outsource certain areas of production, and if so, how do they ensure other vendors meet the same quality standards that they strive for?
Thanks for your comment and question, Everett.
Yes, Toyota sources many parts and subassemblies from outside suppliers. It’s reported that they have 200 to 300 “tier 1” suppliers that they purchase from, and other parts come from upstream “tier 2” suppliers to the “tier 1” suppliers, etc.
A lot has been written about Toyota’s supplier management approach, which tends to be more collaborative than other automakers typically were — working together to improve quality instead of just demanding lower prices from the suppliers.
According to the initial NTSB report, it was Boeing that failed to put the bolts back on after removing the door plug so that Spirit Aerosystems could fix some other defects they had caused.
https://www.reuters.com/business/aerospace-defense/us-safety-regulator-release-initial-report-boeing-737-max-cabin-blowout-agency-2024-02-06/
I started working for Boeing within the past year, and the minute I walked in here, I recalled your Lean vs Lame comparisons. Because let me tell you, it feels worse watching it firsthand than it does to read about it.
I find one of the most cringe-worthy aspects of the Boeing story to be the CFO’s comments in March 2024 about how they will seek to reduce “traveled work”. https://finance.yahoo.com/news/boeing-targets-a-culprit-of-737-max-production-woes-traveled-work-190811343.html Traveled work is a term of art describing work incurred by having to fix defects in supplied parts. In this case the parts were fuselages and assemblies. Workers noted the defects yet the parts were accepted, used, and “fixed” later. The NTSB’s initial finding was the infamous door plug was part of that process.
We are taught in Six Sigma/Lean to reject defective parts. The Lean JIT manufacturing process depends on virtually no defects in the parts used. If Boeing followed modern quality manufacturing techniques, they would be rejecting defective fuselages from suppliers. Root cause in this case is allowing known defects to enter the product in the first place. Boeing has made a joke of the process. A sham.
When I was an engineering student at the Univ of Washington in Seattle in the early 1990’s, Boeing was held up as an example of engineering excellence. Company representatives would give tours and “dress for success” talks to the graduate students. What has happened is an utter degradation of a leading symbol of US technical prowess and engineering culture. The rot needs to be fixed from the top down.
Thanks for your comment. I agree that it seems like the problem starts from the top down. And I hope a CEO will help right the ship.