Mark's Note: Today's post is by Erwin van der Koogh, who comes to us from Australia. The thoughts and opinions here are his, although I agree with enough of it to publish it here. I'll be participating in the discussion via comments and I hope you'll join in.
By Erwin van der Koogh
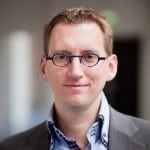
The one thing that Lean Six Sigma got wrong can be summarized in three words:
“Pretty Much Everything.“
In 2002, Michael George and Robert Lawrence Jr. published Lean Six Sigma: Combining Six Sigma with Lean Speed, a book that started a revolution that quickly took hold in boardrooms around the globe. Total Quality Control and Six Sigma had always appealed to senior managers, but now it came with the added bonus of increased speed and reduced cost. It was a very welcome addition in the post “dot-com bubble” era and was always too good to be true.
My beef with Lean Six Sigma, however, is that as far as I can tell there is almost nothing in there that resembles the Lean I know and love.
Now before we delve into the common misconceptions that surround Lean, I want to make it really clear what I mean when I mention Lean. With it, I mean the version of Lean as taught by or influenced by people like Taiichi Ohno, W. Edwards Deming, Russell L. Ackoff, Jeff Liker, Tom & Mary Poppendieck, Donald Reinertsen, and countless other Lean experts I listen to and have worked with. Lean is based on a long-term vision, exceeding customer expectations, holistic thinking, creating flow, and respect for people.
When I talk about the version of Lean that isn't all that Lean, as popularised by Lean Six Sigma, I'll just call it “Six Sigma.”
Lean is all about quality
One of the core assumptions by Mike George and Robert Lawerence was that Six Sigma was all about quality and Lean about speed. This couldn't be further from the truth.
Principle #5 of the Toyota Way management system says:
“Build a culture of stopping to fix problems, to get *quality* right the first time.”
It gets worse though. Six Sigma has a very limited concept of quality. It is mostly about the absence of defects, as they describe:
“The Six Sigma program is in place to eliminate any abnormalities, failures, or defects that occur within a given process”
Quality, however, is so much more than just the absence of defects, it is about meeting and exceeding customer expectations.
Lean is not about speed or even reducing waste, but reaching customer outcomes
Ask most any manager what Lean is about and they will tell you it is about removing waste. Now if removing waste was of such importance, don't you think it would have made at least one of the 14 principles of Toyota's management system as documented in The Toyota Way? Go check for yourself. There is nothing there about waste.
#Lean is not about speed or even reducing waste, but reaching customer outcomes Share on XAs I mentioned before, Lean is about meeting and exceeding customer outcomes. And for Toyota, the cost of the car happens to be a very important customer outcome. Which is why they invest such an insane amount of time in reducing waste. But for Toyota reducing waste is a tool, not the goal, which is cars that provide great value for money.
Removing waste or reducing defects might do very little for your specific circumstance and should never be the goal. Ask instead: what do you want to achieve for your customers?
Lean isn't about belts and ranks, but about every single employee
Six Sigma has a system with rank and belts. The more training you have received, the higher your rank or belt, which is just like Judo or Karate. You start with a white belt and work up your way to a black belt and beyond. In Six Sigma, a ‘Lean Deployment' is a process where, in a few weeks or months, a few experts in the process and Six Sigma redesign the process (or subprocess, the horror) to reduce waste and errors.
This is in complete contrast to the Lean principle of “respect for people.” Here are just a few snippets from the “Toyota Way” principles list:
- “… foundation for continuous improvement and employee empowerment”
- “Grow leaders …”
- “Develop exceptional people and teams …”
- “Respect your extended network …”
- “Make decisions slowly by consensus …”
To underscore just now important human beings are in any Lean organisation, Toyota has recently been replacing a portion of their robots with humans. They've done so because humans can learn and improve.
And this is in a very predictable industry, car manufacturing. The major variable is how many cars of what model to produce, with which options. It is very likely your organisation is surrounded by a lot more complexity than that. Human beings can deal exceptionally well with complexity (and other human beings) if you let them, robots cannot.
Redesigning a process without the input of everyone involved and giving the new standard to all your employees, maybe even putting up a process flow diagram on the wall, is not a good example of respect for people. And it certainly does not tap into the knowledge, wisdom, and experience of your workforce.
Lean is not a project, but a deep, company-wide, culture change
I would be very happy if I never have to hear about another ‘Lean Deployment' again. The idea that you can improve the whole by improving a process was proven to be wrong in 1965 by Robert Machol in his book System Engineering Handbook.
The only way you can improve your organisation is to get everyone to work on improving the whole. There are quite a few things that need to change for that to occur. Every employee will need line of sight to your customers and everyone needs to understand how the whole process is performing. And most importantly, we have to accept that for the whole to be optimized, we need to accept that some parts are not optimized. All of these require a thorough cultural change in your entire organisation. Do you have one person who is responsible for the entire process from a first lead to delivery? Is it the CEO?
The only way you can improve your organisation is to get everyone to work on improving the whole. Share on XLean is not about making numbers, but long term vision
A few years ago, I observed a meeting with Lean Six Sigma experts to figure out what to tackle next.
On the table were a few possible projects they wanted to tackle with one project having huge projected benefits. It was a major pain point for customers, regulators were very concerned about it, and it was very possible that bad decisions were being made all over the company because of the bad data that was being supplied.
Imagine my horror when the first order of business was to get rid of that project because they needed to realize at least $1M in savings this quarter. It was too hard to quantify the dollar value of the benefits even if they could deliver the project in time.
Lean principle #1: “Base your management decisions on a long-term philosophy, even at the expense of short-term financial goals.”
Period.
Lean is not about processes, but about creating a learning organisation
But by far the most important issue is that Lean is not even about processes. Processes are a great tool to become a learning organisation. That should be the goal for every organisation that is trying to stay relevant in the current economy. The increased pace of change, the disruption and complexity are all certainly going to continue, and they will very likely accelerate. The only real competitive advantage left in this century is adaptability. The one prerequisites for adapting? To be continually learning.
Six Sigma has its place to help improve certain processes, but to survive & thrive in the 21st century we need to look beyond ‘Lean' Six Sigma and start getting real about real Lean.
Please scroll down (or click) to post a comment. Connect with me on LinkedIn.
Let’s work together to build a culture of continuous improvement and psychological safety. If you're a leader looking to create lasting change—not just projects—I help organizations:
- Engage people at all levels in sustainable improvement
- Shift from fear of mistakes to learning from them
- Apply Lean thinking in practical, people-centered ways
Interested in coaching or a keynote talk? Let’s start a conversation.
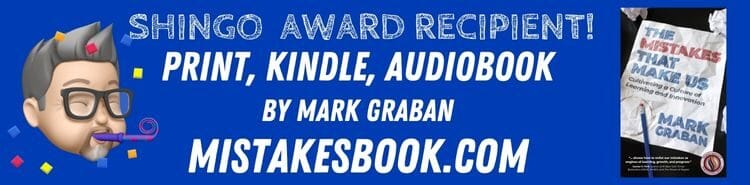
Like Mark, I agree with enough of what Erwin says to recommend reading it. Approaches like Lean or Six Sigma emerge out of specific contexts where they are successful, but then their boosters go global cosmic.
Six Sigma started out as a modernization of the tools used to achieve process capability in various segments of the electronics industry, with the goal of making statistical design of experiments a common practice, and the belt system was a way to propagate this body of knowledge. Success in this limited endeavor did not justify making it into a business panacea.
Lean started out as TPS, which is, to date, the best known way to make cars. TPS has a much broader scope than Six Sigma, encompassing management and technology. It includes human resource management as well as design concepts for welding lines. The “Lean” label for TPS was a way to allow other car companies to apply it without explicitly referencing Toyota, and to package it for use beyond the car industry. While it’s clearly applicable in many industries, including health care, it’s not a panacea either.
What happens when you try to expand an approach beyond its range of applicability is that you drain it of substance in order to make it generic, as has happened to both Lean and Six Sigma, not to mention Lean Six Sigma. All you are left with at that point is homilies.
I agree with most of it Michael. Although I am fairly convinced that the Lean principles are applicable to pretty much all enterprises. But just transferring practices from contexf to context is folly indeed.
Great Article – I have been in many hospital organizations where the OTHER consultant is only talking about Waste removal and not about the people and how to educate and develop a culture of lean.
Also As you stated “Lean Six Sigma” is really a watered down version and often does not even resemble Lean. I really thry to avoid using the term “Lean” because I think it is so often used incorrectly and I use the term “Process Improvement” and “PI Culture mentality”
Well done Erwin. When I’ve observed most “Lean Six Sigma” training programs, they are just Six Sigma programs with a single module on waste. Its like the didn’t even make an effort to integrate it, let alone get it right.
Here’s an example of where that “Lean” content in a Lean Sigma training curriculum seems superficial and incomplete. This is very typical of Lean Sigma… it’s basically Six Sigma in disguise.
I just now glanced at a chapter of a new Lean Sigma book… it describes “the Lean Sigma implementation process” as nothing but a series of projects. Ugh. That misses the mark, at least if you want to call it “Lean.”
My point exactly Mark. Lean isn’t something you are done with. And certainly when they pick part of a process instead of the entire thing it gets to be very dangerous.
[…] Source: http://www.leanblog.org […]
While Erwin makes many great points, I feel he also makes a few mistakes in his description of Six Sigma.
Every Six Sigma program that I’ve seen base their discussion of quality and defects on the Voice of the Customer (VOC). They do not ignore or downplay the customer, but rather seek to specificlly understand what the customer wants because it is the failure to meet that need that creates a “defect”. In my experience, Six Sigma projects do tend to be more specific (eg translating what a customer wants into a specific measurable) than Lean projects, but to say that Six Sigma has a limited definition of quality misses the mark.
On a related note, I’ve been through numerous Lean and Six Sigma training courses and I’ve never seen the Kano model covered in a Lean session, but it has always been included in my Six Sigma sessions. Again, because Six Sigma is still based on meeting and/or exceeding the customer’s needs.
Also, reducing Six Sigma to being just about Belts and stratification of employees is an over-simplification. Yes, the division into Belts is kind of silly on the surface, but it is no more sillier than the insistence of some Lean practitioners to proclaim their status of being a Lean Sensei. The value of a Belt designation isn’t about who should be involved with improvement (it’s everyone’s opportunity) but it is about the amount of training and/or experience that someone has. Within the Six Sigma realm there are some really advanced tools that can seem intimidating to folks and forcing everyone to learn about say, Design of Experiements, is overkill. Everyone can however learn about the importance of clearly defining a problem they want to work on, figuring out why the problem is occuring, creating solutions, and ensuring that the solutions stick. And that’s a formulation that pretty much works for a “Lean”, a “Six Sigma”, or even a “Lean Six Sigma” project.
It might not be sillier, but is it fair to say that 95% of Six Sigma programs have the formal Belt designations and requirements, whereas only a few Lean folks here and there use that term “Sensei”?
One practice is a silly norm, one is a silly outlier.
About that 95% 6S with belts, I wonder what percentage of the 95% have actually produced tangible quantifiable improvements for their organisation?
Often the subset goal of developing a certain % of belts is the only goal attained, not what these belts were supposed to enable. Makes me wonder if someone actually tabulated the cost of developing and training these belts, versus the benefits these belts generated for the organisation. I suspect the Cost/Benefit analysis might demonstrate a poor ROI; and then doesn’t this fall in the category of ‘waste’?
;-)
There’s more to life (and to Lean) than ROI, but I see your point.
The last manufacturing company I worked for had trained and certified something like 300 green belts and they had done something like 302 green belt projects… there was very little improvement activity after the belt process was done. The environment wasn’t conducive to it… such a waste, I agree.
Good points Brian. Talking about “waste”, Right?
Interesting perspective but feel like it propagates the same parochial mindset often seen from those that are as single minded in their approach to six sigma.
Having been exposed to organizations that leveraged both methodologies to varying degrees, it seems clear that lean AND six sigma are focused on delivering on customer expectations. For the most part, corporate excellence programs are better served to have at their disposal a broad array of quality tools when considering what will work most effectively within their business operating systems and cultures.
Let’s not forget, any of these ideas are only worth what they can deliver in results on the front line of a business. Theoretical discussions in virtues of one methodology over another are of little interest to the executives who fund these programs. For them, it is, and will always be about the results (albeit too often focused on the short term, but that is a discussion for another time).
We need more articles, blog, and publications like this out there. Well done.
Love it.
Nick
Thanks Nick,
Toying with idea on a post about how KPIs & suboptimization almost lost us World War II. Going to be a blast to write as well.
Very well articulated, excellent pointers, well done Erwin
Every day the army and navy decide to argue about supremacy of national defense is an unproductive day. There are too many pressing problems in this world affecting too many customers that need action, today. Both lean and six sigma share the same vision for organizational sustainability, and tactics for workforce engagement in problem solving. We should recognize the differences in the approaches, and if we must decide which one is “best”, how about doing it the good old fashioned way: we’ll settle it annually with a lean vs six sigma football game. Do you have any head coaches in mind? :-)
I would be equally critical of any effort, done under the banner of Six Sigma, Lean Sigma, or Lean that did not
1) focus on quality
2) focus on customer needs
3) attempt to engage everybody in improvement
4) focus on changing the management system and culture
5) focus on the long term
6) work toward creating a learning organization
We can look at definitions of what any of these methodologies are supposed to be and what’s actually happening in practice. There are misguided Lean initiatives that fail the six tests above (they involve a handful of experts focused on cutting costs, telling people what to do, etc.). I call that L.A.M.E. (Lean As Misguidedly Executed) instead of Lean.
We can find bad behavior and bad management under many banners.
That said, the “Lean Six Sigma” books consistently get one thing wrong about Lean… starting that Lean is only about waste or flow or efficiency and that “you need Six Sigma to improve quality.” I get more annoyed by Lean Sigma belts badly misstating or misrepresenting Lean (going back to Michael George’s book) and that has nothing to do with a “which methodology is best” argument or discussion.
I’d like to see more of your thoughts on this topic, Erwin. I think you get to the core of the problem very well. I want to comment specifically on the value of involving everyone in change and improvements.
Over the years I’ve worked as an engineer in 4 different companies where the “Lean Six Sigma” or “Total Quality” or some other variant of the same swept through the place. Ultimate results were mixed – two continued their death spiral, the others survived but didn’t thrive. The top thing that united all of them was the absence of any real involvement of “hands on” engineers or other front line people.
Once I was invited to a “roundtable lunch” with a VP and a dozen or so other employees. That was good as far as it went. Not long after, I heard a rumor that flex time was going to be ended for everyone due to a few people abusing it. I called that VP to ask if he was aware of this (and what a slap in the face it would imply for those of us who wanted to help with the changes) – he spoke to me, but wouldn’t listen. He said yes the general manager saw a few people clearly violating the policy and yes it was fair to revoke it for everyone.
Having seen first-hand how clueless our managers were, I didn’t hesitate when I had an opportunity to go to another company about 6 months later. What did surprise me is how common this kind of thing is — putting money into mere hand-wringing while making sure no real change happens.
– Nancy V. @vanschoo
Erwin’s post is well spoken and I wholeheartedly agree with most every position taken. If LEAN were truly and purely as he describes it, I would be its most ardent follower. However, in my experience LEAN is many things to many people, and as a methodology it has at a minimum diluted and at worst polluted. The name itself damns it to be less than the ideal Erwin describes. The name frankly suggests and in spite of the larger ideal it may have represented at one time, has been reduced to elimination or reduction of waste. Even its namesake Toyota appears to have lost sight of the ideal as evidenced by their recent slips and slides in customer satisfaction and retention, and consumer ratings on reliability and value. It would appear that even Toyota has adopted the this co-opted or perhaps corrupted version of LEAN.
I believe what we need is pretty much the version of LEAN that Erwin describes, but I don’t think there’s much of a chance of reigning in all the variant (yeah deviant) versions of it. The odds are better that Putin will give back Crimea to Ukraine. I recommend recouping Erwin’s original version of LEAN, bring it current (I’ll explain shortly) and give it a new name that can’t be confused with LEAN or SixSigma.
What I mean by bring it current is that both SixSigma and LEAN were borne of manufacturing and a product-dominant world. Ever wonder why neither methodologies translated well into the services world? Think about it! The product-dominant world is collapsing under the weight of global demand for services. Our world is slowly but surely migrating to services over products. As a point of fact, many product centered companies have been re-positioning their products as services (Rolls Royce and IBM are but two). This reality hits home when one realizes that products are of no actual value to the customer until they are put into service (i.e used).
I’m actually working on this very concept and you’re welcome to join me.
I agree that there are many versions of Lean that are deviant, harmful, and far from the ideal. These often exist in places that call it LEAN in all caps :-) It’s not an acronym, but that’s just a pet peeve.
https://www.leanblog.org/2012/03/is-lean-an-acronym/
OK, sorry for picking on you for that, Don.
I’m not sure if a “reboot” of Lean with a new name would help. The problem, I think, is not with Lean or Six Sigma… or TQM… but it’s a problem of these noble approaches running into “the way we currently manage.” That old traditional approach (which disrespects employees and focuses mainly on cost) is going to to win more often than not. The old guard corrupts the new approach to make it seem more palatable, thereby killing the effectiveness — I’d consider “Lean Sigma” to be one of those bastardizations.
I disagree, though, with your comment about Lean not translating well into services. It *has* done very well… but only when top management is willing to change its spots. “Traditional management” is commonplace and strong in healthcare… which is why we far too often see Lean turn into an exercise of cost cutting and layoffs, even though it’s clearly not supposed to be that.
Some active discussion of this post on LinkedIn:
LINK
Totally agree, very similar to my recent LinkedIn post https://www.linkedin.com/pulse/lean-six-sigma-oxymoron-troy-taylor?trk=mp-reader-card
Best regards
Troy
Right on. It seems every improvement process / system change quickly dissolves into a quick fix / flavor of the month, with focus on the techniques (and often just partial techniques) to get recognition for the practitioner / consultant (e.g., the “belts”), and not on the basic tools / continuous improvement goals and the overall long term commitment – starting with sr. managment – to achieve a change in the way of perceiving and doing business. Since such goals are usually measured in years, while rewards are based on quarters, sr. managment often moves on before their results, good or bad, and be measured, and a successor may sometimes get the praise or the condemnation based on programs initiated previously. Even Toyota faltered when global sales leadership become more important than the principles driving the “Toyota Production System” (enhanced Dr. Deming, et al).
Six Sigma done right incorporates the impact of defects on the customer; Six Sigma done wrong focuses on measures and often drives behaviours that drive those measures without regard for impact on the overall product.
When I when through Lean Six Sigma training, it did reinforce what I suspected – focus on a small problem that could be measured rather than a holistic view of the process overall. While useful for small incremental improvements, it does not encourage thinking outside the box.
What happened in both cases, in my opinion, was the promise of a “silver bullet” that would solve the issues facing businesses. As noted by one commentator, short-term focus rather than long-term focus encourages this drive to find the one thing that can be used to address myriad issues.
Well-written and insightful.
My opinion is that the Six Sigma industry got off track when Six Sigma became more about cost cutting than quality improvement and when Six Sigma became focused on how many belts one could train.
The extension into “Lean Sigma” was arguably a reach into a new market… let’s train and certify “Lean Sigma” people now. Follow the money?
I’d also criticize Lean if and where it became all about cost reduction, too. Both Lean and Six Sigma can get really off track from what they are supposed to be.
There was a strange defense of Michael George’s book on Linkedin:
My response:
Sam, if that’s the analogy you’re going to make, let me propose one that might be more accurate: “Don’t blame the chef for his cookbook that has inaccuracies about food and some recipes that might be incomplete, because his cooking school and restaurant were actually awesome.” Having a book that’s a “teaser” for training might be a good business model, but that teaser should be accurate.
If Toyota’s approach of quality and cost to the customer really worked why are not their cars the least expensive and highest quality cars to purchase? I would suggest that their quality is mostly comparable to many other auto manufacturers as is the cost. So what gives?
Great questions.
For one, prices are set by the market. Toyota realizes that. Low cost doesn’t have to translate into low prices.
If their costs are lower and customers are willing to pay relatively high prices (due to things like the reliability data and high re-sale values), then that explains why they are so profitable.
As to quality… other automakers have indeed caught up in many ways… by using Lean/TPS methods. If Six Sigma were that powerful, wouldn’t an automaker use that to beat Toyota? I know that Ford has dabbled with Six Sigma, as has Tata (owner of Range Rover).
The author some really good insight into the state of many Lean efforts.
We can put work cells in the lab, huddles on the units, metrics on the wall, and standards on the equipment; but somehow we aren’t even close to Lean and it seems we might even be losing ground without the cultural change. What is more vexing is that many Lean Deployment efforts to change culture violate many of Toyota’s 14 principles described by Liker.
Roger Gerard talks about doing a behavioral based assessment of leadership in advance of Lean Deployments. I think he is right. And if you are afraid to ask the right questions of leadership that may be an immediate tell that you should do something else.
BS – What’s an example that you see of something that violates one of the 14 principles? I believe that it happens, but I’m curious if you can elaborate.
All of the principles below take time and in the rush to deploy Lean, cultural change, if addressed at all, has often been just another box to check off on the master plan. This may be why the author doesn’t like the term “deployment” which is just another term for project.
Principle #9 – “Grow leaders who thoroughly understand the work, live the philosophy, and teach it to others.”
Principle #10 – “Develop exceptional people and teams who follow your company’s philosophy.”
Principle #11 – “Respect your extended network of partners and suppliers by challenging them and helping them improve.”
Principle #13 – “Make decisions slowly by consensus, thoroughly considering all options; implement decisions rapidly.”
Principle #14 – “Become a learning organization through relentless reflection and continuous improvement.”
What is vexing is that I have done it myself. “Well, if we can just get some early wins and get some things up and running then leadership will start to ….”.
And early wins may be part of the problem. “Gee, Lean looks like it works so we really don’t need to change leadership behaviors and that culture thing will just take care of itself over time so just keep doing what you’re doing.”
Good discussion. Thank you.
Hey BS,
Seems weird calling you BS when the points you make so much sense.
Agreed!.. In none of the Lean Deployments I have seen has there been hardly any talk about leadership and/or culture. And without that it is impossible to get to long term continuous improvement.
The focus is usually very much on the short term. Quick wins and move on..
Most any noteworthy Lean transformation has involved a CEO who looked in the mirror and then started a very personal Lean transformation… if not at the very beginning of Lean, then pretty close to the beginning.
There’s a common script.. Executives “sponsor” Lean but don’t really put much into learning about it… they continue with their traditional approach to management. After a few years of Lean not having a huge impact (wonder why?) they give up and say “Lean didn’t work here.” It’s more like they didn’t really try.
In my book, “Lean Hospitals,” going back to 2008 and its original publication, I tried to emphasize that Lean is not just tools, but also a management system and a philosophy. I wish I had data on how many C-level executives have read the book vs. internal consultants, etc.
Completely agree Mark.. There is still way too often an executive sponsor that brings in outside consultants to change ‘them’, the front-line workers.
I agree Mark and Erwin – to bring about the culture transformation requires Lean leadership from the senior leadership team and lots of it. There’s little to achieve and to sustain if consultants have to ‘change’ the frontline without leaders at all levels being focused on, and active in, the gemba.
Therefore Lean has to be a holistic approach in creating value for the customer, practised by everybody, every day, everywhere in the organisation. Specialists creating process improvements in a functional setup (outdated management thinking) is just not enough to satisfy customer requirements in the long run.
Erwin – thank you very much for this thoughtful and insightful article – it has cleared up many points of confusion I had. As an industrial engineer who ‘grew up’ in the automotive industry – I have been so immersed in Lean that it is part of who I am as much as what I do. I also was practicing variation reduction before I had ever been introduced to Six Sigma, and even after training struggled to understand how it could be used to improve processes in the way that I had been trained.
I really appreciate how you think, and would love to be able to sit down over a good meal and a bottle of wine to further explore these issues (too bad we are on opposite sides of the planet). I would, however, be interested in reading anything else you author or any articles you feel are valuable.
Many of the organizations I am now looking at are looking for Lean Six Sigma – however I feel more confident than ever now saying Lean & Six Sigma knowing that this will provide the results they are looking for.
One comment I would like to dispute that you received earlier was that Lean and Six Sigma are not as applicable to the service industry – I have found a service organization that has made incredible changes under the banner of Lean and Six Sigma – true changes including how the organization is structured in order to change or define new processes that are actually focussed on customer needs and wants. They are really following the Toyota way even if they are not aware of it – truly a banner organization.
I feel like I understand now better than ever, but I do have one question – six sigma in its design is a tool for reducing variation – true the customer focus helps to ensure that you are reducing variation that is important to the customer. It does not, however, address if it is the best, or even the right process, it just makes it more stable – or am I missing something.
I think there would be a world of difference between
1) a true combination of Lean (a full non-superficial approach) and good Six Sigma
2) “Lean Sigma” with watered down Lean tools
#1 would beat #2 every time.
Paul,
Thanks for the comment, it is greatly appreciated.
I will more than gladly take you up on that offer for a meal and wine if you are ever on this side of the planet :)
As for my comment about the service industry I mean that Six Sigma has little place in a service organisation. Lean is absolutely great for it.
As you mentioned Six Sigma is about reducing variability. And variability isn’t nearly as bad in service industries as manufacturing.
What do I care if you got your loan in 2 days and I had to wait 3 days?
Does it really matter than normally I get my coffee served in 1 minute, but it is really busy and now it takes 3 minutes to get my coffee?
In fact, customer service is all about people and their requests. And the better you can match your service to their request (and needs) the better you are. Assuming that none of your customers are identical there is already variability present. Stamping out that variability is going to destroy your customer service.
Of course there are parts of those organisations that could benefit from reducing variability. When I am on an operating table I would prefer a surgeon not to improvise too much. But in service organisations we should really ask ourselves is what variability we should embrace, which ones to ignore and which ones to reduce.
A great example I often use is Zappos and their call centre. Every call centre on the planet has average handling time as one of their most important KPIs. And most are trying very hard to reduce variability, so they can plan and forecast better.
Zappos only really has customer satisfaction scores as KPIs.. which means their record call is 9 hours and 37 minutes (http://www.businessinsider.com.au/zappos-longest-customer-service-call-2012-12)
That is why Zappos is considered one of the best customer services organisations. They embrace variability.
This might seem like a surprising comment from me, but is the goal of Six Sigma really “reducing variation” any more than Lean is about just “reducing waste”? I mean, lots of people define Lean and Sigma that way, but neither methodology should be seen as a substitute for thinking and judgment. What’s the right thing to do for our customers, our employees, and our company?
I can think of many situations where variation is not necessarily a bad thing, as you stated. There are times when a surgeon has to make judgment calls with a patient for their particular situation. We don’t want anybody to be shackled unnecessarily by “standardized work” or process.
Both Lean and Six Sigma should probably be viewed as ways of improving the organization for the long term.
In the couple of decades I’ve been involved with lean and six sigma, I’ve seen several situations where six sigma folks did a great job of improving a process, just to see some lean folks come along and find a way to not need the process in the first place. At the same time I’ve seen some necessary processes that could be further improved with some statistical rigor.
My biggest problem with “lean six sigma” and especially “lean sigma” is that I have yet to see a LSS or LS program that truly includes the “respect for people” pillar of lean, which, in my opinion, is by far the most important and most powerful component of lean. In fact, I’d say the whole concept of an exalted priesthood of colored belts flies in the face of respect for people, which is why I’m disturbed that “belts” are making their way into lean itself. Besides the fact that, unlike with six sigma, there is truly no defined body of lean knowledge to certify against – as much as some consultants would like you to believe otherwise.
Lean six sigma takes a subset of lean and a subset of six sigma, leaving out what is arguably the most import component of lean, and therefore does a disservice to both lean and six sigma – and to the people and organizations that embrace the bastardization of both concepts. Both concepts are great and can create tremendous value. They can and should exist together. Just don’t hobble by combining subsets – and forgetting about the power of people.
I agree about not combining a limited subset of both methodologies.
I’ve complained before that many “Lean Sigma” initiatives should just be called “5S Sigma.”
https://www.leanblog.org/2012/10/just-call-it-5s-six-sigma-instead-of-lean-sigma-please/
I criticize Lean Sigma a lot, and then hear people defend Six Sigma. I have nothing against Six Sigma. I’m criticized Lean Sigma and the way it waters down or misrepresents Lean. Then people say, “Well, what matters is what works.” OK, good luck with the Lean Sigma thing. But, I’d predict “Real Lean” (hat tip, Bob Emiliani) will do more good than watered down Lean…
I have been toying with the idea of tongue-in-cheek rebranding real Lean as LeanNTP (Lean for Non Trivial Problems)
Maybe I should just get on with that and make that page :)
Hi Erwin and others.
Interesting discussion. Erwin I like your commitment and passion. I wonder if anyone here is aware of the Theory of Constraints, Dr Eli Goldratt and TLS?
You will find some independent research from APICS May 2015 : http://www.scribd.com/doc/243282107/APICS-May-2006-TOC-LEAN-SIX-SIGMA-pdf#scribd
There is also much more on the internet.
Dr Eli Goldratt developed TOC standing on the shoulders of giants like Ford, Shewart, Deming, Ohno and others. Much in common with TLS and the later phenomena called TPS now morphed into Lean. TOC is science and systems theory applied to human systems (e.g. for profit and not for profit organisations – in production, projects, supply chain logistics, sales and marketing, throughput accounting and measurement and importantly thinking and decision making) and much much more.
I mention this as there was no mention of TOC in the above discussion which might mean that we can all sometimes be so engrossed in our own world we don’t see what is standing in front of us.
Cheers
Andrew
Sydney, Australia
Andrew,
I am very familiar with ToC (and a bunch of other great change initiatives such as Agile/Lean Startup/Beyond Budgeting and many more). The reason they are not included is that they weren’t relevant enough for the article.
But they are relevant in any real 21st century company.
You will be glad to know I am currently working with a team to find a bottleneck :)
Based in Sydney? I am in Melbourne myself. Always up for grabbing a drink with people who like these sorts of things. I’ll be up in Sydney over next month or two. Hit me up on info at http://21stcenturymba.com .
For what it’s worth, I was exposed to TOC early in my career, first being assigned to read “The Goal” in college. At GM, in 1995, we had formal TOC training and there were internal champions. It was a useful methodology for trying to help management not want to have buffers EVERYWHERE, as was their habit.
I’ve TOC to be helpful, but I don’t share the enthusiasm professed by some of it being a management system or a way of thinking… but that could be my ignorance.
Interesting and passionate discussion.
in despite of consultants’ opinions, enterprises want to solve their problems, involve and develop people, know how to use data , “keep it simple” , make real transformations, survive & be profitable…
Doesn’t matter the name of methodology, acronym or origin of method. Use it and get results…!
just my opinion
Manoel
Great post. We differ where you don’t believe lean is about reducing or eliminating waste. I couldn’t disagree more….especially for companies just beginning to find their bearings. Waste, as it pertains to an impact on quality, cycle time and speed impact customer expectations. Most importantly, however, is the reality that the customer pays for waste. Price is at least half the customer experience.
As you know, Toyota didn’t coin the phrase Lean. The Toyota Way, however, was adapted into what we know as Lean in the U.S. Plenty of fat here to make it part of the improvement and progress process! Again, great piece. I’m not sure why ‘Lean Six Sigma’ is even a phrase that’s used. Both useful and potentially together but different animals.
http://www.ThreeBellCurves.com hosts a white paper about culture that I think anyone interested in org culture might really enjoy. (yes, its a shameless plug).
See Michel Baudin’s comments on this post via his site:
http://michelbaudin.com/2015/04/03/the-one-thing-lean-six-sigma-got-wrong-about-lean-erwin-van-der-koogh-guest-on-lean-blog/
Read the rest here
[…] 1.The one thing Lean Six Sigma got wrong about Lean […]
Yeah! Lean is a kind of process which is related to clear out the waste from hospitals and other manufacturing companies. Lean manufacturing focuses on the quality with customer’s maximum satisfaction. This process engages almost everybody to generate quality improvement with long term guarantees.
This guy is spot on. Not only with his understanding of Lean, but the reality that Lean/Six Sigma is not a real thing. There’s Lean and there’s Six Sigma. Doesn’t mean the two cannot complement one another, but they can’t be smashed together to make a new entity.
Erwin Van Der Koogh: Very descriptive article. Just described what so many others have expressed in other forums
Nevertheless track record doesn’t help them since most of both initiatives have been wrongly deployed and unsustainable because of lack of Organization Readiness and lack of Change Governance
Thank you for sharing
I’m not anti-LSS, but I do believe that it has been applied too broadly. Rather than the all-encompassing, go-to tool for improvement as it is/was billed and promoted, I look at it as merely a serviceable approach to improving one of the seven deadly wastes (i.e. defects). I possess many years experience with the Toyota Production System at a Japanese transplant company in the U.S. where we employed the PDCA cycle for structured problem solving. I didn’t learn about Six Sigma or DMAIC until after I left that organization, but I think the “DMA” portion of that methodology fits rather nicely within the “P” of Deming’s cycle, presuming that defects are the specific waste that an organization wishes to countermeasure and improve. I think it has limited utility beyond that.
The article prompts me to ask, what defines a philosophy? In terms of google search this seems reasonable ‘Philosophy is a way of thinking about the world, the universe, and society. It works by asking very basic questions about the nature of human thought, the nature of the universe, and the connections between them. The ideas in philosophy are often general and abstract.’ So does the article meet that criteria or is it seeking substantiation based on the delta between what was intended bs what is now? And how does a philosophy become corrupted to the extent suggested? Imho, philosophy is based on first principles substantiated by visible and scrutinizable cause and effect logic..
I have quit every organization that uses the term lean six sigma except for my employer who generally leave me alone.
Excellent, well-written exposition of LSS. Now get ready for the next so-called silver-bullet: Agile-Sigma! Woohoo!
When will corporations learn?
Beautiful article. I completely agree.
In my former job as a Lean manager at a 1 tier automotive company I made it very clear to the quality department that Six Sigma is only a method within Lean.
Thanks, Erwin, for the great reminder of the things that really matter!
I agree with your approach, Lean is a system that is supported by people there is a misunderstanding because of the American culture and Japanese culture I mean Six Sigma is about brought the money as fast as possible this methodology was developed by Americans and because of this somebody wants brought the same result with Lean combining them
Name a Six Sigma project where the final results was not a Lean Tool.
Six Sigma projects takes 3-6 months for a specific improvement in a specific area…that’s like saving a leaf in a burning forest. But Six Sigma is a sexy term to throw around in mgmt conference rooms, but working people only know of one word, “frustrations”.
This is because in any process, I have always found at least 95% waste, from building a turbine blade to a financial transaction. One company in New York, did not believe in “5S”, while another company in Utah had a fully integrated “Water Spiders”. What was common between the two different companies? They both expressed their “frustrations” within their journey of Lean maturity levels. Both General Manager to the team workers were using the same nouns and verbs…
The bigger question is not Lean or Six Sigma, it’s how does the Company manages itself.
Lean Management Operating System, build the operational / culture framework for success.
People +Performance+Process = Product
In the Lean world we believe in Pull vs Push. With the correct framework, teams will PULL the tools as you build your army of problem solvers, holistically.
80% Culture & 20% Tools. Toyota Way Principle #1
Quick review re. Waste in the Toyota Way.
First – All Toyota Principle titles are ‘affirmative’, (unlike half of Deming’s 14 points). This precludes name a principle to stop doing something wrong.
But, Principle #2, ‘create a continuous flow to eliminate waste (muda) through the process of continuous improvement-Kaizen.
The seven types of Muda are:
1. Overproduction
2. Waiting
3. Unnecessary Transport
And so on.
Principle 2 is actually ONLY about waste.
[…] 2. Mark Graban – author of Lean Blog […]