tl;dr: The blog post discusses how a sushi company's policy letter offers invaluable lessons for hospitals aiming for operational excellence. It advocates for adopting similar transparent communication and employee engagement strategies to improve patient safety and overall healthcare quality.
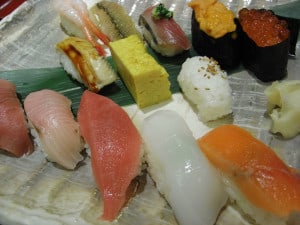
I love the Texas-based grocery store chain “Central Market.” It's like a local version of Whole Foods, basically.
One of their features is a sushi area run by a third-party company, Yummi Sushi.
Posted prominently is a letter that outlines their stated approach to quality and safety. Click the photo for a larger view.
Below, I'm going to basically transcribe the letter, but as if it were the policy of a hospital or health system.
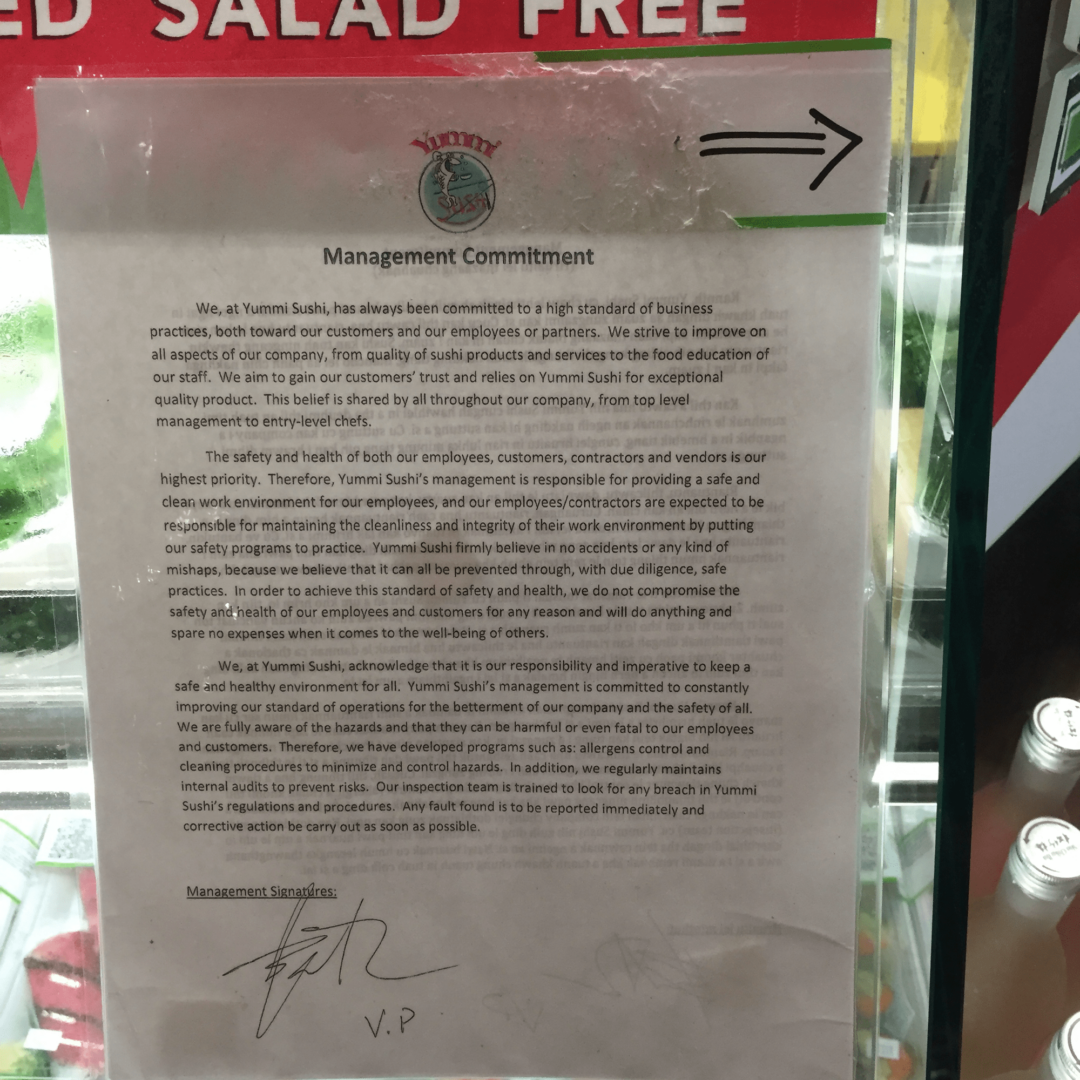
I can't find any news articles about safety or quality problems related to the company, unlike the customer illnesses and deaths caused by problems with Texas-based Blue Bell ice cream. Maybe Yummi Sushi is just very serious about quality and safety rather than just reacting or putting a good face on something bad that happened.
Listen to Mark read this post (learn more & subscribe):
Here's the modified letter:
We, at Excellence Health System, have always been committed to a high standard of business practices, both toward our patients and our employees or partners. We strive to improve on all aspects of our hospitals and clinics, from quality of our services to the education of our staff. We aim to gain our patients' and community's trust, those who rely on Excellence Health System for exceptional quality care. This belief is shared by all throughout our health system, from top level management to entry-level staff.
The safety and health of both our employees, patients, contractors, and vendors is our highest priority. Therefore, Excellence Health System's management is responsible for providing a safe and clean work environment for our employees, and our employees/contractors are expected to be responsible for maintaining the cleanliness and integrity of their work environment by putting our safety program to practice. Excellence Health System firmly believes in no accidents or any kind of mishaps, because we believe that it can all be prevented through, with due diligence, safe practices. In order to achieve this standard of safety, and health, we do not compromise the safety and health of our employees and patients for any reason and will do anything and spare no expenses when it comes to the well-being of others.
We, at Excellence Health System, acknowledge that it is our responsibility and imperative to keep a safe and healthy environment for all. Excellence Health System's management is committed to constantly improving our standard of operations for the betterment of our organization and the safety of all. We are fully aware of the hazards and that they can be harmful or even fatal to our employees and patients. Therefore, we have developed programs such as infection control and cleaning procedures to minimize and control hazards. In addition, we regularly maintain internal audits to prevent risks. Our inspection team is trained to look for any breach in Excellence Health System's regulations and procedures. Any fault found is to be reported immediately and correction action carried out as soon as possible.
Management Signatures:
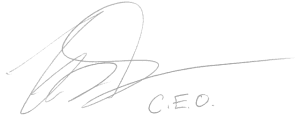
I didn't have to change much in the letter. I'd hope the letter would be signed by the CEO, not a VP. “Quality starts in the boardroom,” as Dr. Deming used to say.
Now, for a sushi restaurant or a hospital, a letter or policy like this is only as good as your willingness and ability to live up to it. That means living up to it EVERY DAY, not just when it's convenient.
Can a hospital really “spare no expense” when it comes to safety for patients and staff? Yes, when you realize that better safety doesn't have to cost more if you're achieving safety through processes, training, systems, and culture.
You can establish safe practices, calling that “standardized work,” if you will, but you have to create an environment where it's easy for people to do the right thing. You can't have an environment where people are frazzled, fatigued, or overly stressed. You need to give them the right equipment to do their jobs. Sushi chefs need very sharp knives. It's said in cooking classes that dull knives are the most dangerous. Is your hospital giving people sharp knives that are kept sharp through good support processes? Or are they told to “be careful” and get by with crappy knives?
Does your hospital scramble to get ready for the accreditation visits that happen every few years or are you CONSTANTLY overseeing processes and looking for problems? Are you “always ready” for the Joint Commission?
When you find problems, do you focus on constructive corrective actions or do you “name, blame, and shame?”
The board and the CEO are responsible for keeping people safe in a hospital. Frankly, the job of hospital CEO would keep me up at night or give me an ulcer, given all the things that can go wrong.
We need leaders who can handle that pressure and create an environment that delivers better safety, quality, and lower costs… instead of more blame and stress.
I think that the sushi company, on the surface, sets a good example. I should ask to talk to somebody in their management about the letter and how they live those policies… maybe for a follow-up blog post.
What do you think? Please scroll down (or click) to post a comment. Or please share the post with your thoughts on LinkedIn – and follow me or connect with me there.
Did you like this post? Make sure you don't miss a post or podcast — Subscribe to get notified about posts via email daily or weekly.
Check out my latest book, The Mistakes That Make Us: Cultivating a Culture of Learning and Innovation:
A relevant quality policy for health establishments…it provides a clear commitment to patient and staff safety.