“Kaizen” is a Japanese word that means “change for the better” in the context of ongoing “continuous improvement.” The so-called “kaizen event,” a weeklong focused improvement effort is one type of kaizen, but it's not the only type. A powerful form of kaizen is the practice of small improvements that don't require a formal team or an entire week.
One recent example I can think of comes from the PACU, or Post-Anesthesia Care Unit (aka recovery room), where patients are cared for after a surgical procedure. A daily problem existed – it was not really seen as a problem, but it turned out to be easily fixable, once somebody was aware of the waste in the process.
The operating room and the PACU are both part of the surgical “value stream” or the patient pathway through different departments. Hospitals are often such silo-ed organizations, where people in different departments don't communicate regularly or work on improvements together. While patients are handed off from department to department, it's not unusual that no single person really understands the overall flow. This is one reason why the process of creating a value stream map is so valuable – it's not about creating the map, it's about understanding the whole system.
So, in this hospital, the O.R. nurse would put the patient's chart at the foot of the bed as the patient is wheeled to the PACU. The PACU nurse has to be at the head of the patient's bed, as they are paying attention to the patient's breathing and vitals. But, the PACU nurse is also supposed to be looking at the chart to review orders and other information… but it's at the foot of the bed.
In this case, which occurred daily, it was the type of situation that you just dealt with or tolerated. It wasn't “ideal care,” but most people couldn't image it being different or they just didn't notice that problem anymore.
But, when a single nurse became cross trained and moved from the OR to the PACU, they saw and experienced the impact of that chart being at the foot of the bed. The recognition of this problem led to the question:
“Why does the chart have to be placed at the foot of the bed?”
A few quick discussions later, between the PACU and the OR (across the value stream), they all realized that the OR could place the chart under the mattress up at the head of the bed.
It's hard for a kaizen change to be much smaller than that. But, it's a small change that has a huge impact.
That's what “continuous daily improvement” (as it's called at ThedaCare, for example) is all about. Noticing a problem and taking the initiative to do something about it, working in your department or working with the upstream or downstream department.
Often, staff members make an improvement and they don't think it's noteworthy because it's so small. Kaizen, as continuous improvement (not events), is about lots of small improvements adding up to make a big difference. As they say at my Healthcare Kaizen co-author Joe Swartz's hospital – “that's a kaizen!” Their leaders keep their eyes and ears open to help identify improvements that have been made so they can be documented and shared. This sharing can take place through paper “quick and easy kaizen reports” that are often entered into a web database (as they do at Joe's hospital). Or, hospitals can manage, share, and archive that improvement through the KaiNexus software from the startup I'm working for.
I also find it interesting to think about why an opportunity for improvement like that wasn't identified earlier. How is it that people see past that waste? Is it because they are really busy? Because they too readily work around a process problem like the chart being in an inconvenient or inaccessible place? Why don't departments work together more closely? And I ask these questions not to blame or beat up on people, but to think about the culture and the systemic barriers that prevent us from seeing waste or from making improvements.
It's changes like these that we are featuring in our upcoming book, “Healthcare Kaizen.” Weeklong events are fine, but that's not the only mode of  improvement that we need. We don't need a weeklong event to solve really small problems. A small change or a large kaizen event is always about the PDCA/PDSA cycle. These approaches are complementary, not competing.
Please scroll down (or click) to post a comment. Connect with me on LinkedIn.
Let’s work together to build a culture of continuous improvement and psychological safety. If you're a leader looking to create lasting change—not just projects—I help organizations:
- Engage people at all levels in sustainable improvement
- Shift from fear of mistakes to learning from them
- Apply Lean thinking in practical, people-centered ways
Interested in coaching or a keynote talk? Let’s start a conversation.
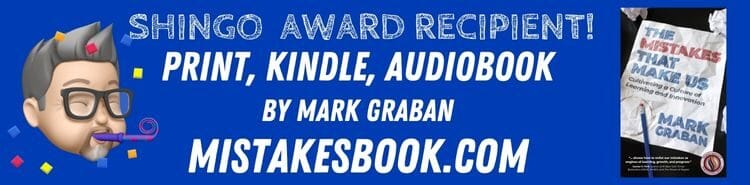