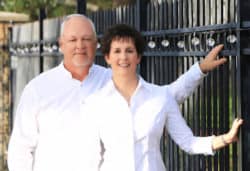
My guests for Episode #300 of the podcast are Tracey and Ernie Richardson, authors of the excellent book titled:
The book is full of solid insights and personal experiences from their time working for Toyota in Georgetown, Kentucky at the plant known as TMMK (Toyota Motor Manufacturing Kentucky).
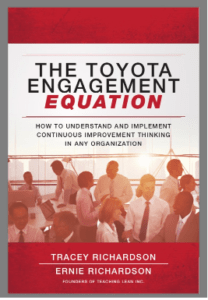
You can find their book's website. Tracey and Ernie are both faculty members for the Lean Enterprise Institute. Tracey's blog is called The Toyota Gal.
In our podcast, we talk about their experiences at Toyota, including lessons they've learned about problem solving, people development, and what they call “D and A” – discipline and accountability. We also talk about Ernie's experience within health clinics at Toyota and other healthcare organizations.
I hope you enjoy the discussion even if you work in healthcare or another realm outside of manufacturing.
Streaming Player (Run Time 49:26)
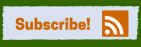
For a link to use for this episode, refer people to www.leanblog.org/300
For earlier episodes of my podcast, visit the main Podcast page, which includes information on how to subscribe via RSS, through Android apps, or via Apple Podcasts. You can also subscribe and listen via Stitcher.
Links, Topics, and Questions:
- Tracey started at the TMMK plant in Georgetown, Kentucky in 1988, working in production
- Ernie started working in powertrain production and then moved into HR
- He was able to help show that Lean works everywhere, even in non-production settings (including health clinics that were started at Toyota North America sites).
- Tools, philosophy, and culture of Lean / TPS apply in many settings
- The Ohio State MBOE program
- Tracey's faculty page on the LEI website | Ernie's page
- You can find them on LinkedIn: Tracey and Ernie
- Why write this book after there are already so many about Toyota? What was the spark and the motivation for writing?
- Is it harder to learn Lean / TPS lessons when you already have older habits in place?
- Toyota taught them to be open to change… learn from your old habits and processes… what can we take from that?
- “But we don't use the excuse of we don't have time for it.”
- Every single person there had a development plan, developed with the person
- “Who did you develop today?”
- David Meier was her first Group Leader there (hear my podcasts with him… and there is a new one coming soon)
- “Go see, ask why, show respect” – leaders go to see the problem the team member is seeing and facing
- What does “respect for people” mean to you?
- “Making people who make cars”
- Servant leadership… how can a leader make people's job easier and more effective?
- The Toyota “green book” – info
- “Toyota's not a perfect company… nobody's perfect. The Japanese trainers would get scared if there weren't problems.”
- What's the danger of a “tools only” approach when trying to emulate Toyota?
- DNA (D and A) — discipline and accountability… how do you define those words?
- Discipline around standards is the foundation for improvement (having discipline vs. being disciplined)
- “If you don't have a standard then it's impossible to truly measure continuous improvement.”
- You have to respect a person by telling them the reasons why to do something
- “I don't think that not following the standard was an option.”
- If there's a better way, there needs to be a way to improve the standard.
- “Asking why the person is not following the standard… Not penalizing the person if the process is bad”
- What would you do in healthcare when the systems or processes are bad, where there's not really a good solid standard?
- “Standards are put in place for processes where the output needs to be controlled. And we put enough standardization in place to be able to control the output but not so much that it constricts the process or keeps a person from being able to perform.”
- Ernie's experience in the clinics at Toyota and hospitals
- “Enough standardization” – a foundation, not a roadblock
- All processes can have a standard… do you need a standard?
- The biggest problem is people not being able to see the outcome of what standardization would do for them.
- Mark: We shouldn't standardize for the sake of standardizing
- Ernie: Once healthcare providers see the benefits, they become big advocates.
- Tracey: Shifting from the “5 whos” and “root blame.” Don't blame people for a broken process, especially if people aren't trained properly
- What does the customer (patient, caregiver) need the process to produce?
- Toyota aims to reduce “mental burden” of how many decisions are being made within a process or a window of time.
- E cubed (E^3) – everybody engaged every day…
- It's the “Thinking Production System.” Encouraging people to think and being engaged in looking for abnormality from standards.
- The essence is the “Thinking People System”
- If we sell, tell, and convince people… it's going to be very difficult to have sustainable standards
- If you engage, involve, and empower people to create a standard together, it works much better
- We knew the standard was probably going to change… we wanted it to.
Video and Webinars With The Richardsons:
Automated Transcripts (Not Guaranteed to be Defect Free)
Announcer (2s):
Welcome to the Lean Blog Podcast. Visit our website www.leanblog.org. Now, here's your host, Mark Graban.
Mark Graban (13s):
Hi, this is Mark Graban. Welcome to episode 300 of the podcast. It's February 15th, 2018. My guests today are Tracey and Ernie Richardson, authors of an excellent book titled The Toyota Engagement Equation, How to Understand and Implement Continuous Improvement Thinking in Any Organization. Now, I really enjoyed the book. It's full of solid insights and personal experiences from their time working for Toyota in Georgetown, Kentucky. In the podcast today, we talk about their experiences at Toyota, including lessons they've learned about problem solving, people development and what they call D and A, and a discipline and accountability.
Mark Graban (57s):
So I hope you enjoyed the discussion, even if you work in healthcare or another realm outside of manufacturing. Ernie did some work within health clinics at Toyota and some other healthcare organizations. So we touched on that a bit. And there, there are definitely lessons learned here. It's really, it's about leadership, it's about people, and that really applies everywhere. So if you would like to find links to finding Tracey and Ernie on social media, their books, website, more information like that, you can go to lean blog.org300. Tracey and Ernie, thank you for joining us to talk about your book today.
Mark Graban (1m 38s):
I'm really excited to have you here.
Ernie Richardson (1m 41s):
Thanks for having us, Mark. We look forward to it.
Tracey Richardson (1m 43s):
Yeah, Mark, this is great. We enjoy doing the podcast and sharing our wisdom.
Mark Graban (1m 50s):
You have a lot of wisdom in the book and, and a lot of stories, and I encourage you we to check that out and, you know, we'll touch on, you know, couple topics today and hopefully peak everybody's interest. Tracey, if you can start off, you know, there are a lot of personal stories in the book, which I really enjoyed. It really, you know, connects the lessons to, you know, some really engaging stories. But can you give kind of the brief intro, you know, there's a lot of your career story in the book. Can you introduce some of your background and, and what you're doing now post Toyota?
Tracey Richardson (2m 23s):
Yeah, absolutely. So as most know was start at TMMK in 1988 when we were kind of rolling the, the startup phase, going there and being part of kind of the building things around us. It was before we were even making sellable vehicles. And so had the blessed opportunity to work with trainers. I started as a team member. So I was on the line in IP trim and realized very quickly that, you know, there was an internal training system, you know, with Toyota Institute and University of Toyota, and then our own training center that worked closely with TMC, Toyota Motor Corp.
Tracey Richardson (3m 3s):
So I just, you know, kind of put myself out there to say, this is, this is gonna be a neat path. And so I went through pre-promotion training, moved up from team leaders, spent a few years as team leader, line supervisor hourly, and went back to school for leadership classes for moving on to salary management. So I spent 10 years from our, our hourly position to salary in the plastics department, moving around in various areas from instrument panel to to bumper injection molding to headliner bumper cores, a lot of, lot of various parts there and plastics. And was there until 1998.
Tracey Richardson (3m 44s):
So I did 10 years in production and Ernie and I made a decision I wanted to go into hr, but that's not always easy when you're married to an HR manager. So we made a, a family decision and I actually left my position as a full time employee at, at Toyota Motor Manufacturing Kentucky. And I kind of went in the back door and came back as a contractor, consultant, vendor trainer, whatever word you wanna use. And I became a trainer for Toyota across North America in the different plants. So went kind of sharing my wisdom, giving back to the plant that they had invested in me. And then a few years into that I started to get a pool externally and joined LEI and worked for some colleges, work with Ohio State in their MBOE program.
Tracey Richardson (4m 34s):
And you know, we do a lot of conferences, lean frontiers and in different things. So the, the pool of external took over and, you know, today we do mostly a private client and go to the, go to their gemba and we do some conferences speaking and then other things like podcast and, and do a lot of things online obviously. But yeah, it's been 30 years from working on the line as a, a team member to a consultant out there sharing my wisdom of that collective 30 years. And it's been a really neat journey.
Tracey Richardson (5m 13s):
We've, we've really been blessed to, to be a part of that, that phase at Toyota.
Mark Graban (5m 19s):
And Ernie, you know, if you can kind weave in a little bit of your background, you know, your, your story and Tracey's stories intertwine here in different ways, but what you can tell us about your background and you stayed longer at Toyota, if you can
Ernie Richardson (5m 32s):
Tell us about that. Yeah, actually, you know, I spent my 25 year career at Toyota, worked at IBM before I went to Toyota. Interesting about the problem solving aspect of the two different companies. We talk a little bit about that in the book. Spent the first half of my career in powertrain as, as a startup as a team leader, which is hourly position. Worked my way up through the management and powertrain and then moved over to human resources about halfway through my career. And, and then was able to, you know, we always hear people talk about, well that lean thing works in building cars, but non-production does it work in.
Ernie Richardson (6m 14s):
And so I got to spend the last half of my career actually working in the different fields in hr. And it does work everywhere, whether you're building cars or, or building safety systems or building medical clinics or, or medical processes. And so the last few years of my career at Toyota, after, in the 25 year career, I actually was operations medical director for Toyota North American wide. So we were responsible for clinic operations all across the, the us, Canada, Mexico. And so I got to see firsthand how we can take the philosophies and, and the tools and the culture that we were taught in manufacturing years ago and actually start rolling that into healthcare insurance companies, clinic operations and those kinds of things.
Ernie Richardson (7m 9s):
So it was pretty, pretty good. And in that area also, we worked on, you know, I worked in safety at our plant in Kentucky, also disability management, how we, how we process that, which is as, as a lot of people knows that those processes need, need some help.
Mark Graban (7m 28s):
Yeah. Well, and and we'll come back to the end or the podcast and, and talk about healthcare. I know there's a lot of people listening who, or either working in healthcare, you know, because they came from manufacturing and they've always been there as as, as they always say, patients are not cars. And well yeah, of course not. But they, these methods work in, in, in different places. We can, we could maybe someday we can do a whole podcast about, we could probably talk an hour about your experience in the clinics, right?
Ernie Richardson (7m 58s):
Yes, absolutely.
Mark Graban (8m 2s):
I I won't, I won't, I'm not trying to put you on the hook for that wool.
Tracey Richardson (8m 6s):
Oh, well we, he, he would love to share that cuz there was a lot of, lot of good things internally with Toyota and some of the things they created that, that is a story of its own. And being part of the, the probably the first processes that that did that is, is kind of neat as well.
Mark Graban (8m 25s):
Yeah. So, you know, one question I always love to ask authors is, you know, what was the, the spark, the motivation behind the book? You know, there's already a lot of books out there, you know, about Toyota, the Toyota Production System and lean. So I'm curious, what, what was the genesis of, of you guys doing the book together?
Tracey Richardson (8m 46s):
Yeah, so the book actually, the idea actually started about 10 years ago, I think it was oh seven. So we're right on that 10 year mark when I started putting the chapters together. And it, the, the beginning of it was similar to what it is now, but if a little more about me and kind of the biography type and I kind of altered that to mesh in the beginning of Toyota. So I knew there was a story there to be written 10 years ago. I wasn't maybe ready to tell it or understood the context of it, but you know, from, we've been told a lot since the book's been out that hey, you know, there hasn't been from an inside perspective of somebody growing from, you know, this, this floor level up through management to, you know, training, consulting, et cetera.
Tracey Richardson (9m 43s):
You know, from what it was like, you know, the the, the day to day, the doing, the living, the breathing of that culture that we get so many questions about, you know, how how was it? And I really thought, and then, you know, as Ernie was finishing his time, you know, we were like, with his stories and my stories and even though there are some, some parallels there, there's also some differences. And to bring somebody, we wanted to take somebody on a journey with us and how we learned, you know, everybody's on, you know, today it's, it's kind of called lean and we can talk about that in, in a little bit. But how, how did we become who we are?
Tracey Richardson (10m 27s):
You know, what was that journey and what was it like to be at Toyota? And so we wanted the journey to allow somebody to walk with us and there's a lot of great books out there and, and we, we've read a lot and, and know a lot of the authors that have written them, but we wanted to come in from an angle of here's what it was like for us actually working there and the failures, the successes, the trials and tribulations, the sometimes I don't understand while we're doing this question, you know, really take you with us. And you know, from the feedback that we have been getting, it's, it's coming across as we hope that it, it's a journey with us and what it was like to be there.
Tracey Richardson (11m 15s):
And from many people's perspectives, you know, we didn't start off any different than most people do. We knew nothing. And you know, we had this blank canvas that, you know, they kind of took us and molded us in many ways. And so the book resides in, in the living and breathing of the culture and how we learn from a firsthand perspective.
Mark Graban (11m 37s):
Yeah. And it's a unique perspective. I don't know any other books out there that were co-authored by. So you, you added value directly to the vehicles you pulled the andon cord on on, I'm sure. I mean it's, that's a very, very real perspective, right?
Ernie Richardson (11m 55s):
Ab absolutely. And, and you know, I guess the uniqueness part for us, Mark, is that the, the really, when we were being developed on the culture side, you know, we didn't know anything different and, and, you know, the coin of lean came out at some point in time and we all were internally were wondering wonder what this lean thing they're talking about is. And the reality of it is, it was the culture that was continually built and got to experience it all the way from, you know, some of the stories in the book of where it's okay to stop the line and it's okay to have problems, It's okay to have problem solving, it's okay to take time to do those things, but we don't want to continue repeating them.
Ernie Richardson (12m 44s):
So we gotta develop standards and, and to be able to see that in place. And as you know, when we talk about standards, the accountability discipline, accountability to standards is, is really hard for companies to, to live up to. And at Toyota, that was just our norm.
Mark Graban (13m 5s):
And you, I know, I know from the book, you know, Tracey, you were going to college when you started working at Toyota and, and, and Ernie, you had that experience at ibm. And this is more of a general question, Is it, is it harder to embrace and, and understand, you know, some of these concepts when, when that you've got habits from a more traditional non Toyota like non-Lean organization as opposed to being, being more of a blank canvas at the start of a career?
Ernie Richardson (13m 37s):
Well, I think it is harder if you, if you already have, you know, habits in place. However, I think the, the main ingredient, and I think the thing that coulda kept teaching us was being open to change and constantly looking, let us learn from your habits or, or your processes in the, in previous to coming and what can we take from that? But here's what we're trying to build and here's here's the vision we're trying to go to. So I think it's absolutely hard, but I don't, I don't think it's impossible. I think honestly don't know it's any different when we started than a lot of companies, the difference was is I guess we don't really use the excuse of, well we don't have time to do it or we don't, we don't, we don't know exactly what to do is that we were learning as we were going.
Ernie Richardson (14m 29s):
So I I do believe it's a, it's a problem, but it also can be the foundation for where you start.
Mark Graban (14m 39s):
So in, in that process, I mean what, what did they do at Toyota or, or what did you do as leaders, you know, to encourage people to be open to change and to, to embrace that sort of mindset?
Ernie Richardson (14m 51s):
Well the, the, and I didn't realize this when I first went in there for the first couple of years, but every single person there had a development plan and, and that development plan was tailored to what was viewed as the strengths and weaknesses of the person and developed with the person. And so every single person that worked that I had the opportunity to serve while I was there, you know, had different needs. And so we didn't, we didn't necessarily just make one size fits all. It was looking at every individual and and understanding what do I need to do to continue to develop them into being a, you know, we always talk about we're developing 'em, be the leaders someday we're developing to be the presidents, the general managers of vice presidents.
Ernie Richardson (15m 40s):
What do we need to do to be able to do that? And one of my trainers, my main trainer I talk about in the book actually, you know, he would ask me every single day when I, as when I got to be a leader, Who did you develop today? And, and you know, when I first started hearing that, I was thinking, man, he's kind of being hard on me, You know, but then he was, he was really reinforcing that culture and then before we would end, cuz he would make me do this every single day and before we would end, he would come back to me and say, Now what did you learn today? And so he's always trying to understand my development for how do I, how do I include the team, how do I develop people?
Ernie Richardson (16m 24s):
And by the same time then he's, you know, training and development me to do the other, do that with other folks that we,
Tracey Richardson (16m 32s):
And Mark, I think when you go back to our hiring process that, you know, Ernie and I both went through and, which was about a year and a half process because they were building the plan and we all didn't have anywhere to go early on. So it was kind of drawn out. But there was competencies that I learned later that they were looking for in people. And so when you were tested, you were, they were looking for listening, they were looking for personal, personal initiatives, leadership skills, problem solving skills, your ability to work with people. And so those competencies were underlying. So, you know, when I began, you know, David Meier was, was my first group leader.
Tracey Richardson (17m 16s):
He's the co-author of Toyota Fieldbook. Toyota Field Book and Toyota Talent with which is Liker. And so, you know, I was honestly an introverted person as a, if you look at Myers Briggs personality type testing, which we all had to go through as leaders in the early days at Toyota, you know, I was an introverted person, but I must have tested at a certain level for leadership. And so David worked with me on speaking in front of, you know, other people, our group and then expanded that. And there's a picture in the book and you know, when I look at it, I see the tear in my eyes because of my nerves that were happening at that moment.
Tracey Richardson (17m 59s):
But, you know, I did a presentation, a quality circle, it was an outcome from a quality circle that we did in, in the group. And, and so that particular day, Fujio Toyota, Mr. Toyota came by and we had to do a presentation. And so, you know, part of Toyota's development piece that Ernie's talking about, you know, the IDPs was, you know, David asked me, Do you wanna do part of the presentation? You know, and that made me nervous. But the next level was, you're gonna have to use a microphone, you know, and that just, oh my gosh, I'm gonna be projected all over plastic shop. It really terrified me. But, you know, he took a moment and said, you know, at any given time, if you feel so nervous that you don't think you can do it, just transition it to me and I will take over.
Tracey Richardson (18m 50s):
And that's all I needed. You know, I just needed, sometimes you just need like that fight or flight, you need an out. And it was those little things like that, that the trainers were developing, David in, David was developing me as well as our other leaders. And you know, that moment that was captured that's very priceless to me. And why it's in the book was such a developmental kind of just path that took me off as a confidence builder to do more and more. And I think Toyota really just invests in people that way. It's, we've always said that, you know, they, they happen to, you know, make cars, but developing people is the first and foremost, you know, cars are the outcome of a good people process.
Tracey Richardson (19m 37s):
And there's so many little stories like that that both of us were a part of that, you know, we just embraced that, you know, it really created who we were today, who we are today.
Mark Graban (19m 49s):
So, you know, along that line of, of developing people, having a plan, tailoring it to individuals, it does, does that seem to be an aspect of, you know, the, the Toyota expression, respect for people, respect for humanity? I mean, what, what, what else does that phrase respect for people mean to you from your experience there?
Ernie Richardson (20m 13s):
Well, I think it definitely starts with the individual development, but I also think it talks about the leadership styles within Toyota. The ability to, as Mr Mr Cho says several times, and, and you know, when you go to the gemba, you gotta show respect to the people. That means you've gotta try to understand what he's trying to say there is, you gotta try to understand the, the opportunities and problems they're going through and not just look for an outcome that you want. And so, and you know, go see, ask why show respect was his quote. And it was, you know, I've gotta understand what, what the issues are going through.
Ernie Richardson (20m 55s):
And, and that's not uncommon at Toyota. It is, it is fairly common that, you know, a supervisor may very well go down and, and just go on the line to understand what the problem is the team member's facing. You know, I've seen several presidents do that before actually, where they would see abnormality happening and say, Well train me on it. I want to be able to see it. And so I think it's always the ability to be able to make the connection with employee and understanding in true servant leadership, you know, they are the most important people that we have. And so how we as leaders gotta continue to be able to support to make their job easier and more effective and, and being able to connect that to, you know, their goals and objectives that we, that they're trying to get individually.
Tracey Richardson (21m 43s):
Yeah, when you look at the, the Green book, I think people call it, but the Green Toyota Way book, that's 2001, you know, it has the five values, but it comes from two pillars and one pillar's continuous improvement and one is the respect for people. And like you said, I think the, the respect for people side is truly people are first, the, the product is the outcome of that. And you know, the, the five values that, that stem from that you know, is in the Japanese word, they use genbutsu, which is the, the get your boots on. But the go see was one of the, the values in the, the green book, the, the teamwork part.
Tracey Richardson (22m 26s):
So these, these stem off the continuous improvement and respect for people. And then challenge, which goes to the, the idp, the individual aspect and, and then respect for people comes up as one of the five and then, you know, continuous improvement. So to me, and the, in the, in the Toyota way 2001, it's trying to bring tangible actions for leadership to say, you know, you can go see, you can challenge yourself. We had to respect people through Mr. Cho's thinking and vision of the, the, the go sees wide show respect, and then challenge ourselves, challenge the company, challenge others, and then all that creates this, this learning environment of, of ci.
Tracey Richardson (23m 14s):
So the values were more than just writing on a, on a wall or in a book. They were live, they were practiced. And, and that's what created the cultural, the climate, the feeling, the atmosphere, that it's very hard to describe the people sometimes what it was like, because none of us really internally in the early days, there was no reason to call it anything, honestly, because it was the only acronym we knew, and I make a joke about it, but it was really reality for us is j b you know, this is our job, this is what we do, this is who we are, this is what we represent, it's a way to do business.
Tracey Richardson (23m 57s):
And we didn't need the acronym. And I think that just came later as others tried to describe something that, you know, was, was being written down by then in, in a lot of books and, and other things. You know, it's, it's very dynamic to be inside that, that breathing culture that starts with that Toyota way I believe.
Mark Graban (24m 19s):
Yeah. And so was j b used as, as an acronym?
Tracey Richardson (24m 23s):
No, not really. That's my way of saying it was that simple because we, it was our job, It was an expectation, it wasn't a choice. And the expectation goes to, you know, part of our, our formula that we to talk about is, is dna, you know, there, there's a macro level DNA with, you know, every human. If you look up dna, you know, you get this, you know, definition that might be something of what's the, the fundamentals and characteristics that make up, you know, humans, but there's that DNA level in a company. So it's cultural dna, but then you have this micro level dna, which Ernie and I dubbed as this, you know, kind of discipline and accountability.
Tracey Richardson (25m 14s):
And if there's anything that kind of, Toyota's not a perfect company. I always tell folks there nothing's perfect. There is no perfect, you know, setting where there isn't problems. You know, the Japanese trainers would get scared if there wasn't problems every day. You know, we wanna understand how to, to get to an ideal state at all times. But this, the discipline and accountability, I believe is the difference in how they are we're successful in our successful today, is that that seed in there that is, is strong, you know, within all members, all leadership horizontally and vertically across the organization, I believe.
Mark Graban (25m 57s):
Yeah. So when you talk about the d and a as as you, you write about in the book discipline and accountability, how do you, I mean, those are words everybody knows, but how, how do you define those words? Or how, how are those words generally understood at Toyota?
Ernie Richardson (26m 15s):
So I'll, I'll start and then Tracey can add in some points, but let's go back to standards. So, you know, the, the, the discipline would be that, that we would not operate our processes without standards. And the accountability is, is that we have to follow through on the standard. That that's the reason we have the standard until the next best idea. So the, the, the concept is the discipline is making sure that we have a, a a way to work. And, and then the expectation of that is the way we work. And, and, you know, people think that's, or, or when we talk about that, people think that's very, very rigid.
Ernie Richardson (26m 59s):
The reality of it is within Toyota is it's just the way we do business. It's their way of life, it's their expectation, and it gives us the foundation to be able to make kaza improvement. And so when we go to other companies, that's the biggest challenge we have most of the time is, you know, when we start out with problem solving and we'll talk about, well, what's your standard? And they go, Well, we don't have one. And then you get into, well, you know, we have standards, but we don't pay attention to 'em. And so that's the discipline apart from a company perspective. And, and I think Mark, the, the concept of, you know, when we get, companies are asking us all the time of, well, what do we need to do first?
Ernie Richardson (27m 46s):
And, and so what we always talk about, we'll have the discipline to use standards and then the accountability to make the standard work. And therefore you can give you the foundational part of being able to now make improvements and, and improve as an organization.
Tracey Richardson (28m 3s):
Yeah. Think to, to add to that is, you know, the, the discipline to set the work standards, one thing, the accountability, you know, when, when Ernie and I define a standard or a work standard work procedure, SOPs, there's so many different variations. People don't have to use the word standard Sometimes that, as Ernie said, it's a, a rigid, oh gosh, you know, that's a terrible word, but it's just an expectation of, hey, it's the best known method at this moment that we have consensus to follow until we improve. So to me, that lessons the blow to say, hey, we've all had the opportunity to agree and have consensus, so we're on board.
Tracey Richardson (28m 47s):
So that's part of respect for people to get their ideas for the, the work standard. And then, okay, we're gonna follow this because it allows us to quickly see abnormality. It allows us to have the benchmark for improvement is, Ernie said, there's so many companies that don't totally understand continuous improvement as as what it is or what do you need to do it. And so if you don't have a standard, it goes back to tachi, you know, his simple words would be no standard, no kaza, which in, in, in our regular words, but say if you don't have a standard, it's impossible to truly measure continuous improvement.
Tracey Richardson (29m 31s):
So I think when you go back to the DNA question one, the discipline said it, two, the accountability to say I'm going to follow it and to respect the person enough to give them the reason and the purpose why it's important. You know, if we sell, tell, and convince people to do things on a daily basis, it's gonna be a very, you know, difficult process to get people to understand if I engage involved and empower them in creating this standard together, it's a much more, you got a higher percentage of this teamwork and this respect for people thinking this, this cultural thing we're trying to create.
Tracey Richardson (30m 13s):
And, and you know, it's, it's their idea. It's not mine, it's not me telling it. And I think that was the powerful piece with our culture, that we knew the standard was probably gonna change through people having ideas to make it better. And that was part of that j o b expectation. We wanted it to, we wanted to encourage that, but we also had to train to it, make sure we understand, stabilize it, sustain it, then get it ready for improvement. So I think culturally that was a big difference for us in why we kind of created that, that DNA at a micro level of this. Because a lot of companies, you know, it's, it's kinda like saying, Hey, we have the speed limit sign out there on the roadways and we know it because it's actually a law.
Tracey Richardson (31m 2s):
It's probably beyond a standard, but we choose to follow it or not, you know? But if a cop's sitting there, you know, policing the road, what do we do by natural response? We hit the gas. So it's like we know and understand now what's the DNA inside our culture? You know, like neighborhoods, we all tend to drive slower because, you know, there's a reason children, people walking, you know, there's, there's a reason why seat belts are the same way, you know, so how do we get the buy-in and the why and the, the purpose behind it when that's absorbed and understood, people will work for you all day if you take the time and invest in that.
Tracey Richardson (31m 46s):
I truly believe that cuz they did with us. I lived and breathed that and we did, you know, for other people we see that happen as well.
Mark Graban (31m 56s):
And so, you know, you talk about the, the sort of intertwining concepts of of, of standards standardized work, kaizen, continuous improvement, you know, those, those words, you know, discipline. Discipline means having discipline, not, not not being disciplined.
Tracey Richardson (32m 15s):
Right, exactly. It's like anything, go to the gym, you know, I I'm gonna be disciplined to go three times a week. Yes, exactly.
Mark Graban (32m 25s):
So, you know, so when you talk about the gym, you know that, that that's very self-driven discipline. I mean, what, what was the, you know, the process in the workplace? Did, did the word accountability come into play if somebody, somebody was, was not being disciplined in the way they went about doing something? Or how, how did that enter into it?
Ernie Richardson (32m 48s):
Well, I don't think, not following the standard was an option. Any aspect of, you know, that because we want to have repeatable processes to be able to see gaps. And so it, it wasn't an option for someone to say, Well, I'm, I wanna do it my way. You know, obviously if it's a better way, we want 'em to be able to change the standard and, and constantly changing the standard is what we really reinforce. But the discipline part would come in place through HR policies and procedures to be able to ensure that the person's performing it in that correct way. And, and you know, we always looked at it as how why is the person not following the standard first and making sure the process is stable and, and not penalizing the person if the process processes bad.
Ernie Richardson (33m 39s):
And so we would look at the process and then, you know, work with a person to come up with the best solution, but not following standards, not an option.
Mark Graban (33m 50s):
So I I I think, you know, I ask a follow up, you know, come from the perspective of people working in healthcare, you know, this idea that, you know, this all this all goes hand in hand. People in healthcare might say, Well, our, our people have, or feel like they have a lot of freedom to not follow the standard. And then sometimes people will say, Well, wait a minute, there really isn't a well defined standard Yeah. Either, you know, so how, how do you hold somebody accountable to a standard that's either not defined or, you know, a system that's not well designed to, to allow people to be successful. I I I heard one of your former Toyota colleagues, Darrell Wilburn talk about this at a, a conferencing, you know, that it was the obligation of leaders to create a system in which people could be successful.
Mark Graban (34m 42s):
And, and, and that's, I think not the, the kind of servant leadership mindset that, that we see in healthcare as, as the, as the default. So what, what are your some thoughts, you know, to to, to people who, who, who may be experiencing a very different type of environment?
Ernie Richardson (34m 59s):
Yeah, so, so I think, I think the, to start with the, the definition of standardization is very, very confusing for some folks. So I'll start with saying, you know, standards are put in place for processes that we need to have control, the outputs need to be controlled, and we put enough standardization in place to be able to control the output, but not so much standardization in place that it constricts the process or keeps the person from being able to perform. Now the, my experience in healthcare is, you know, when they, when my, and of course I'm, I'm limited on the, you know, I worked in the clinics at Toyota and, and with some local hospitals, but the first thing I would say is they're looking, the ones that I were involved with was looking at standardization as a roadblock.
Ernie Richardson (35m 57s):
And what we had to kind of help them see is standardization is the foundation. So even, even in processes where people have to make split second decisions and split second different directions in what they may perform, we still wanna have standardized work or standardization on how they try to make those decisions and what helps them make those decisions. So the misconception that, you know, that I saw in, in these areas, and it's not into healthcare, it's a, it's a lot of areas that are, I I will say a lot of areas non-manufacturing is, you know, the ability to have creativity from the person and flexibility and certainly standard standards make that more possible, that makes it more definable and, and the ability to be able to, to develop some, a gradual standardization and you want to standardize as much as we can, but not constrict the people from being able to perform their processes.
Ernie Richardson (37m 2s):
So I would say that, and Mark, you probably have better feel than I do on this, but I would say that that all processes can have a standard that's the ability to, you know, at healthcare, do we need a standard for everything? Is, is the first question. And just from my limited experience in, in insurance and, and healthcare, I would say that the biggest the bigger issue for me is people not being able to see what the outcome of standardization would do for 'em. Yeah. They see it as a roadblock and not seeing it as how, how it can be a springboard for improvement.
Mark Graban (37m 42s):
Yeah. I, I, I agree. And, and you know, you know, as an outsider, my, my study of of Toyota and the Toyota books makes it really clear that, you know, we, we, we shouldn't standardize for the sake of standardizing. It's about the, the purpose and the results and that, that, that we're going for. And then there's that level, that degree of standardization where, you know, people in healthcare, you know, I try to be empathetic, you know, people are, when they're pushing back against what they think lean is, they're, they're kind of, they're pushing back based on history, you know, doctors, nurses, others for many decades had, you know, people telling them how to do their work and, and you know, these phrases, you know, cookbook medicine and, you know, come up and, and, and you're right, they, I think they're rightfully afraid of having standards that are too rigid, but I think they've also been victim of, of others pushing standards that are inappropriately rigid.
Ernie Richardson (38m 43s):
I, I totally agree with that actually. And, and also my limited experience would say is once, once the healthcare providers see the purpose and understand the value, then they're actually huge advocates for it and, and become a very big springboard for, because they honestly healthcare, the, the vision for healthcares want to be the most effective and efficient process possible for the health of, of our, their patients. And so they can do that using, we call it standardization, to be able to control the chaos somewhat. And so, but I think my experience would say that most healthcare providers, once they get a understanding that, and it's not going to be so much standardization, it completely makes 'em feel like a robot, right?
Ernie Richardson (39m 35s):
That, that now all of a sudden it becomes kind of the way they do business.
Tracey Richardson (39m 39s):
Yeah. There, there's, you know, a couple of things that come to mind as we're talking and, and you've, you've probably heard it, people say it all the time, the the five who's and the root blame, you know, the people fear sometimes that, you know, they're gonna be blamed for something. It's so rigid, I'm not gonna be able to remember all that. Or maybe they haven't had, you know, the j I t or the t i, you know, it's kinda like, here, follow this. We, we kind of give them a maybe a potentially broken process that we blame them for. They're the face of the process. And our trainers always grounded us around, you know, always look at the process before you look at the person and are we giving them badly designed processes that are actually, you know, failing, they actually will fail.
Tracey Richardson (40m 28s):
And then the face of that is the person, you know, doing the work. So yeah, that, that's another facet. I think that it's a paradigm shift in this, this whole thing around standardization and, and you know, if we look purely at what is the customer internally, externally need this process to produce, whether it's a patient, whether it's a, a person buying a vehicle or any type of output material and information flow, whatever I'm producing, I wanna try to do that in the most value added way. And, and there was an aspect within Toyota, we called it mental burden.
Tracey Richardson (41m 11s):
We actually factored in mental burden of how many decisions do they make within this transaction or within this process or within this, you know, window of time. You know, for us, we worked in minutes, but e externally it could be a half hour, an hour, it could be any, any particular thing a person's doing. And if there were x amount of decisions being made, let's say it's over 10 decisions in a certain amount of time, then quality or this, this process could have the ability to, you know, have a, a defect or a abnormality or discrepancy. And so when we involve people in asking the questions, and this should be, you know, at the process at the begin, but where are the work happening?
Tracey Richardson (41m 58s):
No matter what work it is, we should ask, you know, what decisions are we making? What, what's, you know, the material and information flow of the process. How are we, you know, how are we doing this and, and x or whatever that might be. I don't want it to make it be about cars, but when we get in there and ask the questions, we realize, you know, wow, this, there's a lot to this. And it does it need a standard, as Ernie said, standards are meant to control and to see abnormality and understand, you know, what's all involved. And sometimes we go in and we find things that don't need to be in there. So when you, when you can have that conversation at the gemba, I believe and involve the people that, hey, it doesn't have to be this way, it's not this rigid thing and let's create it together.
Tracey Richardson (42m 47s):
I think you have that, you get more buy-in and that starts slowly to create the culture of I'm here to help, not here to hinder. Yeah.
Mark Graban (42m 57s):
Well, and kind of, you know, stepping back to the book and you know, as we, we wrap up here, again, I'll encourage everyone to go check out the Toyota Engagement Equation, that, that equation, you know, which I'll, I'll leave for people to get out of the book, but you talked about dna, the D and a, what you're talking about there, Tracey reminds me of the, the part of the equation, the, the e cubed everybody every day engaged. That from my perspective seems to be sadly missing from a lot of what healthcare organizations would call lean. They're not having conversations with people about their work. They're trying to tell them how to do their work. I I, I personally, I I get frustrated when I see that sort of thing labeled lean.
Tracey Richardson (43m 42s):
Yes. And you know, it kinda, obviously it started, I think Lean came from obviously the Toyota Production System and you know, what, how do we articulate that externally? And then I think from the, the EQ perspective, I think a trainer a few years later said, You know, it's not really about Toyota, it's the thinking production system, you know, kind of gin two tps that, you know, we're encouraging people to think, you know, we, we want it to be about how every day everybody is engaged in looking for abnormality from a standard to be able to have this continuous improvement.
Tracey Richardson (44m 28s):
And Gen three tps, which is in the, the latter part of the book, and we talk about it within the, the EQ is instead of the thinking production system, taking it away from production, it's really the essence of the thinking people system. And, and so, you know, the, the everybody every day engaged, that was I think, an important factor of our culture and an expectation that no matter what level, no matter what silo or functional area that you're in, we're all here from an order to customer perspective. And if there's waste, all it takes all of us in all of our functional areas, we're, we're not a, we in a, we're an US and if we're the thinking people system, which I call the three gen three tps, then it takes us all to think and understand and have that line of sight from my individual work, how it, you know, contributes maybe to my department, how it contributes to the organization and in some cases global perspective for some companies.
Tracey Richardson (45m 36s):
And I think that was something that we really embraced internally and were taught from a very early, you know, stage that it, it takes everybody. And, and, you know, me putting my initials on the inside of an instrument panel was my eq. You know, I, I had to look at that from the perspective, but knowing that on a million cars out there from the late eighties to the, the late nineties, my name is on it. And I deemed that good, you know, because there was processes in place that I was following and understood the purpose of, and felt like I was really part of something that I helped create this, this beautiful, you know, product or it could be of service for people.
Tracey Richardson (46m 19s):
So I think looking at it from the perspective of, of thinking people system, it, it really, you know, can change the way people think about this, this lean thing or however it's being coined today from just a, a bad thing to just, let's think differently and let's all engage in that for the greater good of not we and they but us as an organization. Yeah.
Mark Graban (46m 47s):
Well that's, I think, we'll, that's a great point to, to wrap things up on. So Ernie and Tracey, where can people learn more about the book? If you wanna give a website address for that places they can find you on, on social media perhaps, or if, if you wanna give your email address if people have questions.
Tracey Richardson (47m 8s):
Absolutely. Both of us are on LinkedIn, so you can ask to be a connection there. Both of us are, are on there. I'm the, the Twitter person, so it's Tracey under underscore son, Tracey son on Twitter. Try to be on there as much as possible. We started a website for the book just recently. It's thetoyotaee.com. So the, the Toyota Engagement Equation and TheToyotaee.com and you can sign up for a mail is served there on that.
Tracey Richardson (47m 49s):
And we try to share things, you know, on occasion we've got chapter 11 on there. If people wanna see a chapter before they've purchased the book, you know it, it's there to share. And you know, Amazon, there's been some great feedback on, on Amazon as well with the book so people can see what other people are reading. And then our emails are on the website, the Toyota ee so you can find us out there socially, we're, we're out and about when we're, when we're not on the road, we're, we're kind of chatting on the internet with you and others out there in the lean world. Yeah.
Mark Graban (48m 25s):
Well, thank you for, for doing all that and, and thank you for a book that I think is a very welcome and enjoyable addition to the lean literature. I really appreciate it and want to thank both of you. Our guests again today have been Tracey and Ernie Richardson. Thank you so much for spending some time with, with us today. Thanks,
Tracey Richardson (48m 49s):
Mark. Thank you, Mark. We appreciate it.
Announcer (48m 52s):
Thanks for listening. This has been the Lean Blog podcast. For lean news and commentary updated daily, visit www.leanblog.org. If you have any questions or comments about this podcast, email Mark at leanpodcast@gmail.com.
Please scroll down (or click) to post a comment. Connect with me on LinkedIn.
Let’s work together to build a culture of continuous improvement and psychological safety. If you're a leader looking to create lasting change—not just projects—I help organizations:
- Engage people at all levels in sustainable improvement
- Shift from fear of mistakes to learning from them
- Apply Lean thinking in practical, people-centered ways
Interested in coaching or a keynote talk? Let’s start a conversation.
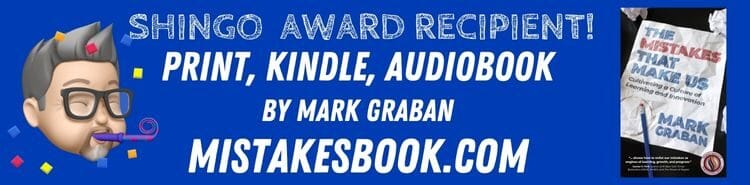