Thanks as always to Ryan McCormack for this… there's always so much good reading, listening, and viewing shared here by him! Subscribe to get these directly from Ryan via email.
Insights about improvement, innovation, and leadership…
Operational Excellence, Improvement, and Innovation
Transform the right way, for your organization
There's no one way to approach organizational transformation. It's long been fashionable to approach transformation by doing some “cost savings” projects to fund the transformation to demonstrate that it's worth it to continue. The challenge with this approach is that it usually ends at the “quick win” stage of thinking and never ends up funding the “hard stuff” – people and systems.
Hillel Lehman, VP of Transformation at Netsle Health Sciences explains why they chose to transform everything all at once and use employee metrics as its key success measures. Transforming everything all at once will require significant change management support, but it may be the only way to get the “hard stuff” on the table.
Woodward Inc., an aerospace supplier, chose an approach that focuses on supplier relationships to launch its digital transformation.
There's no one right way.
Virtual Process Engineers
Are process engineers going to be replaced by robots? Fret not (yet anyways). How AI Is Helping Companies Redesign Processes (hbr.org) explains how the cost of automation is enabling rapid adoption of AI to reduce not only low-value work but an increasingly variable set of work and decisions.
Was that Ryan or Bryan? How about Ryan 007?
Medical errors still occur as a result of carrying out orders and healthcare for the wrong person. I've always wondered why identification processes don't use a name AND a number. Apparently, I'm not alone. Valuing a patient's name by using a number instead.
American Experience: Henry Ford
Henry Ford pioneered many foundational elements of mass manufacturing excellence including the moving assembly line and standardized work. His 1926 classic book  Today and Tomorrow is a must-read for industrial engineers and lean manufacturing students. This weekend I tuned in toÂ
 American Experience: Henry Ford on Prime Video. This documentary provides great insight into Ford's rise from farm-boy mechanic to titan of the automobile industry. It's a warts-and-all account of the famous industrialist, shedding light not only on his enduring innovations but also his virulent anti-Semitism and questionable managerial tactics at the River Rouge complex. I highly recommend for students of industrial engineering and American history.Â
Creating a Culture of Improvement
Your supervisors eat culture for breakfast
Defining organizational culture only “at the top “and publishing posters is doomed to fail to make lasting changes to sticky workplace cultures. Why? Pretty simply, front-line teams and their leaders are responsible for carrying out the work day-to-day – and culture is highly influenced by frequent habits and behaviours. Supervisors and team leads have an outsized influence on organizational culture, so any attempts to understand or improve culture ultimately need to engage the team leads. Michael Balle reminds us that culture change requires a continuous conversation about culture with team leaders.Â
“You can't punish your way to perfection”
It's difficult to have high-performing teams without accountability. But often accountability is simply blame and punishment masquerading as leadership. Transparency and openness are necessary, but not sufficient to build a culture of safety. Mark Graban reminds us that you can't punish your way to perfection.Â
What's the best structure?
Finding the “best” organizational structure has been a centuries-long journey for industries and has yielded few breakthroughs and many disappointments. If Max Weber‘s ideas dominated 19th-century thinking and Alfred Sloan‘s shaped the 20th century's view of the “corporation”, what will shape the predominant thinking in the 21st century? Most contemporary searches for org-design nirvana have pitted command-and-control hierarchies/bureacuracies against democratized “flat” designs. But this is overly simplistic in an era of increasing complexity and transformation.
So what IS the best structure? In his new book, Henry Mintzberg says plainly that “believing there is one best way to structure organizations is the worst way to manage them”. I recently read and reviewed Henry Mintzberg's latest book Understanding Organizations…Finally and it may provide the most comprehensive and practical study of organizational design to date.
Some Wisdom from Seth Godin:

Coaching – Developing Self & Others
Don't dominate. Facilitate.
Suzi McAlpine shares some wisdom on how to facilitate rather than dominate your meetings. Â
Push vs. Pull
Managers are often taught to lead by ‘pushing', driving teams hard for outcomes, which routinely results in ‘pushback'. Less often, managers employ ‘pull', inspiring and motivating others to action, which can create more buy-in. Which should you use? Both according to the World Economic Forum's “Why ‘push' and ‘pull' management are key to successful organizational change”.
What's your life task?
Lack of motivation. Listlessness. We all suffer from deep bouts of indecision about life. The key to busting the slump, according to Jung, is to get to work. Find the “life task” when you are stuck in a rut.
Follow Ryan & Subscribe:
LinkedIn:Â https://www.linkedin.com/in/rjmccormack/
Subscribe to receive these via email
Please scroll down (or click) to post a comment. Connect with me on LinkedIn.
Let’s work together to build a culture of continuous improvement and psychological safety. If you're a leader looking to create lasting change—not just projects—I help organizations:
- Engage people at all levels in sustainable improvement
- Shift from fear of mistakes to learning from them
- Apply Lean thinking in practical, people-centered ways
Interested in coaching or a keynote talk? Let’s start a conversation.
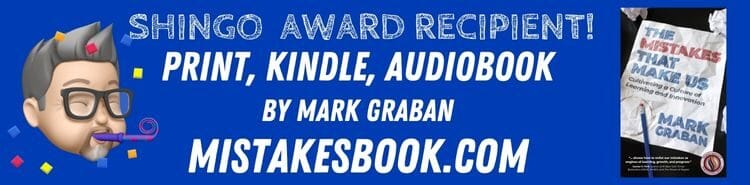