The book that I'm writing on learning from mistakes is not an academic research-driven project. My “field research” mainly consists of the 200 podcast interviews that I've done, asking a wide range of people, “What's your favorite mistake?”
Update: The book is available! The Mistakes That Make Us: Cultivating a Culture of Learning and Innovation.
There are stories and reflections from Toyota people and those in their close orbit, such as:
As Katie wrote in her book, Learning to Lead, Leading to Learn: Lessons from Toyota Leader Isao Yoshino on a Lifetime of Continuous Learning:
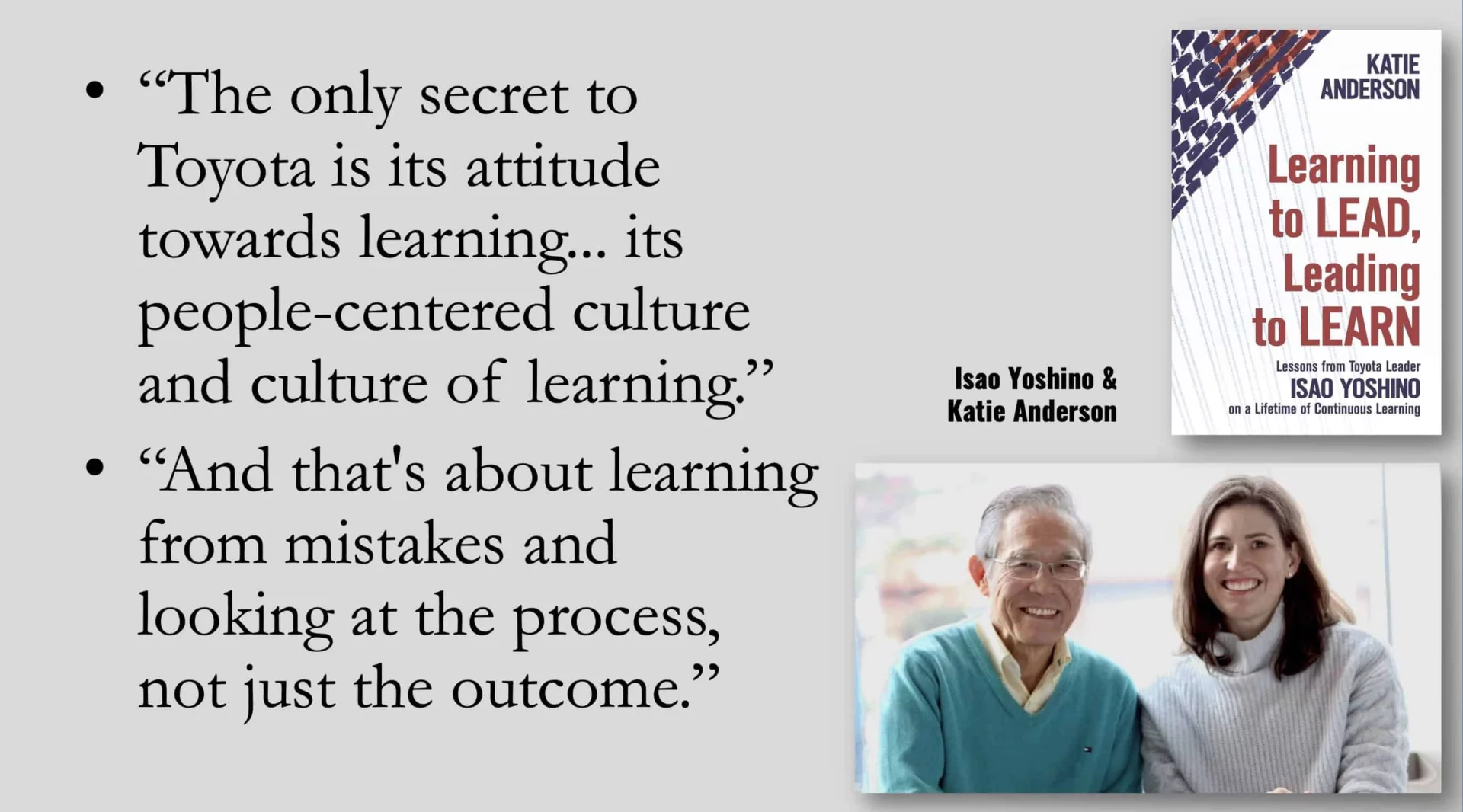
I think it was from the book, not the podcast. I could be wrong. I'll go check.
But the stories from former Toyota people are so clear and so consistent when it comes to learning from mistakes.
I did go check the book by Liker and Hoseus, Toyota Culture: The Heart and Soul of the Toyota Way.
There are many mentions of “learning from mistakes” in that book. Co-author Mike Hoseus had a story that he shared in the book that was very similar to the stories from Yoshino and Meier — he was applauded for pulling the andon cord and admitting a mistake. They quite literally applauded.
“He did not seem angry at me for making the scratch,” said Hoseus about his team leader.
It's about mutual trust and safety:
“Without trust in their employers, employees are reluctant to admit to the existence of problems and learn that it is safest to hide them…”
We shouldn't blame people for hiding problems when they feel like it's not safe to disclose them.
Toyota has worked hard to create that culture. They've stated their ideals. They aren't perfect — and I'm guessing there are moments each day somewhere around the world when they fall short — but the standard is clear.
Mistakes are OK…
Here is one quote from the book that I shared on LinkedIn:
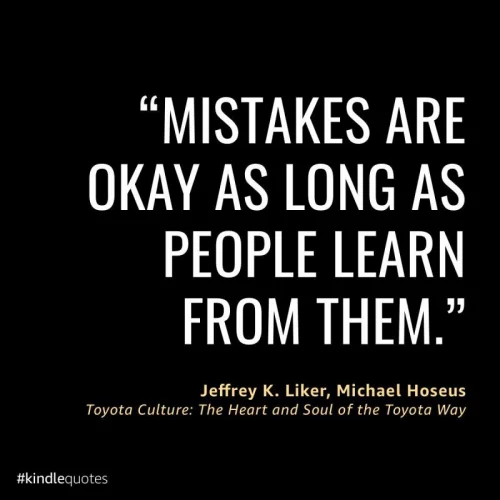
The famed Toyota Way 2001 document said this:
“We view errors as opportunities for learning.
Rather than blaming individuals, the organization takes corrective actions and distributes knowledge about each experience broadly.
Learning is a continuous company-wide process as superiors motivate and train subordinates; as predecessors do the same for successors; and as team members at all levels share knowledge with one another.”
Psychological Safety is Required
Some other quotes from Toyota Culture make very clear the need for psychological safety:
“Safety [at Toyota] includes more than just physical safety; it also means feeling safe psychologically. This starts with a respectful environment where team members do not fear psychological abuse.”
Not just physical safety, but also psychological safety.
That's why I've come to believe and say that psychological safety (a level that's “high enough”) is a pre-condition for Lean.
“…the holistic way in which Toyota looks at the safety of all stakeholders.
It involves providing for the physical and psychological safety of each member and their families.
It is an intentional value that drives subsequent action.
It is part of the Toyota culture that involves the ideas and input of all the members to create positive results in which all can take pride.”
This “holistic way” (“The Toyota Way”) is notoriously difficult to copy — if copying should indeed be the goal anyway. If people are trying to copy Lean tools without also understanding the need for psychological safety (and other elements of the Toyota culture), are they doomed to struggle or fail? I'd say “probably.”
Being able to learn from mistakes requires a high-enough level of psychological safety. We have to feel safe to raise concerns and also trust that our concerns will be taken seriously, if we're going to even bother to point out mistakes or to suggest a better way:
“[Toyota believes] people must be treated fairly, they must feel psychologically and physically safe and secure in their jobs, they must believe that any concerns they have will be taken very seriously and given due process.”
And one final snippet about the need to avoid blame…
“The strong belief in objective problem solving that focuses on improving systems instead of blaming individuals underlies a good deal of the daily kaizen.”
This builds trust and psychological safety. How can we build that in your organization? I'd love to help.
Contact me if you'd like to discuss any of this and my certification from LeaderFactor where I can help you assess the current state (through an anonymous survey), educate leaders, and coach them through the behaviors that are proven to build more psychological safety.
The connections have become really clear to me:
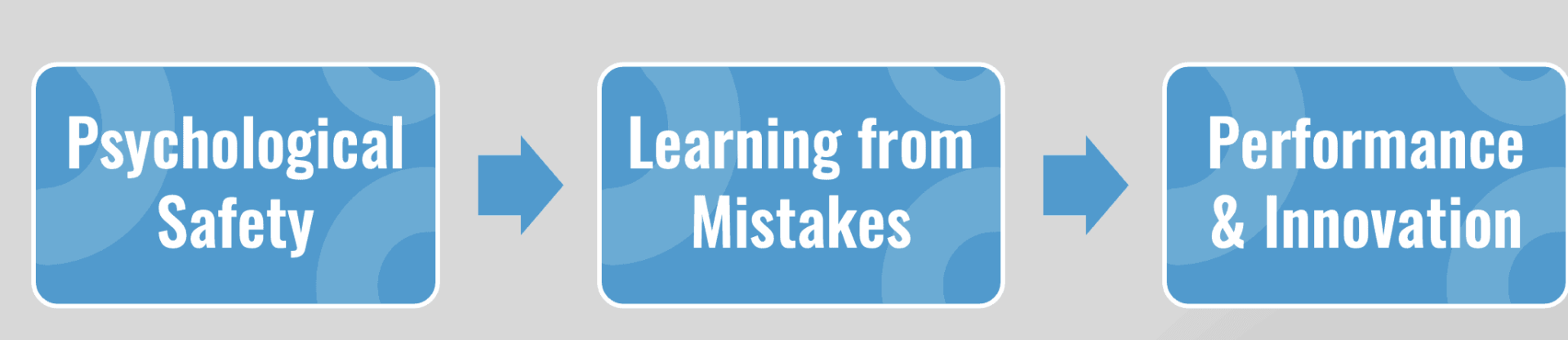
You can leave a comment on this post or feel free to join the discussion over on LinkedIn:
Please scroll down (or click) to post a comment. Connect with me on LinkedIn.
Let’s work together to build a culture of continuous improvement and psychological safety. If you're a leader looking to create lasting change—not just projects—I help organizations:
- Engage people at all levels in sustainable improvement
- Shift from fear of mistakes to learning from them
- Apply Lean thinking in practical, people-centered ways
Interested in coaching or a keynote talk? Let’s start a conversation.
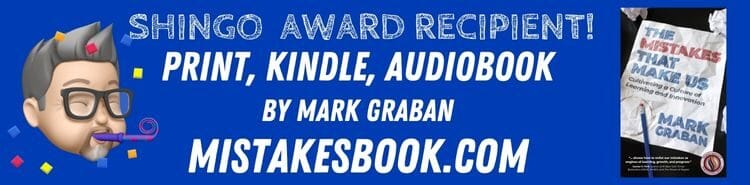
[…] At Toyota: Mistakes are OK, as Long as We Learn; Culture and Psychological Safety– Mark Graban talks about Toyota’s culture of trust and safety when it comes from learning from our mistakes. […]