You might have noticed that the cover image for this post shows a Neopolitan pizza and a traditional wood-burning pizza oven.
If you didn't see it, here it is (and it might make you hungry):

Why would I include this photo, other than because of my love for eating (and making) this style of pizza?
There's a reference to pizza in this article from General Electric about the practice of Lean in one of their factories — in Italy.
Smooth-Running Machine: Lean Techniques Help a GE Aerospace Plant in Italy Find Its Footing
Before we get to the Lean content, here is the pizza reference from the article:
“…the plant's canteen is legendary in GE Aerospace circles for its homemade pizzas, which emerge perfectly baked from the kitchen's oven.”
What a perk that would be! That level of pizza surely beats the typical mediocre hospital cafeteria pizza that I see in my travels. Even the best of that hospital pizza isn't very tempting when choosing what to eat for lunch. I don't know for a fact that GE has a traditional “wood-burning pizza oven,” but I will just picture it that way in my head unless proven otherwise. I'm assuming, but at least I'm stating my assumption and recognizing that I could be wrong.
But now to the meat of the story, related to Lean.
“…site leader Gioacchino Ficano is a believer in the idea of continuous improvement. That's the business philosophy incorporated into lean management that is at the core of GE's culture.”
If you haven't been following GE in recent year, there appears to be a cultural sea-change from the days of the late CEO Jack Welch. GE was famously a “Six Sigma” company during Jack's time and for a while after his retirement. I wasn't a fan of Jack's leadership style, to say the least.
For the past four years, their corporate CEO has been Larry Culp, formerly of Danaher — a great “Lean manufacturing” company (via their “Danaher Business System”). He's also the CEO of GE Aerospace, formerly GE Aviation.
I'm excited to hear Larry speak at the upcoming AME annual conference in Dallas next month. You can register and get 15% off using code “MARK15.” Learn how.
See two previous posts that I've written about Larry, who I do admire:
But now back to the GE article about their facility in Italy, where many great Lean principles and concepts are on display.
Better for Customers and for Employees
Their improved results are not only driven by “new procedures” as descried in the article. The improved results are also driven by “newly empowered staff,” and that empowerment is a recurring theme in the article.
Avio Aero, the GE Aerospace business that runs that plant, has improved their customer delivery performance while also making it better for employees.
The “before” situation:
“Our people on the shop floor were also unhappy, and becoming unwell as they chased delays,” Ficano adds.
At first, there was a mistake made in adopting a tool that was said to be blaming front-line workers for systemic issue and results. Generally speaking, I appreciate it when people can admit and learn from a mistake – ala the discussions on the “My Favorite Mistake” podcast).
Plant managers, thankfully, realized that workers appeared to be dejected was a symptom of problems, not the cause of the problems in and of itself.
“We didn't want to start by blaming people, as it was not the point indeed,” says Ficano.
I love to hear leaders and organizations get away from the blame game.
They found a long-time GE employee to help:
“Hobbs is a keen proponent of “putting the operators first,” a management technique that empowers and energizes shop-floor workers to root out the hidden causes of delays and inefficiencies, and thus drive transformation.
“They are the most knowledgeable people you have, so they should be treated as the main customers,” Ficano says.
That sounds like the Lean principles of “respect for people.”
For readers in healthcare, how can we always be “putting the caregivers first”? Doing so will also benefit the patients, just as “putting the operators first” leads to benefits for the GE Aerospace customers.
Kaizens or Kaizens?
The article describes “a kaizen” — when it would be more clear to call it “a kaizen event.”
To me, that distinction matters because the traditional “kaizen event” is just one form of “kaizen” (or continuous improvement). You can do small “kaizen” improvements that don't require a formal event — it's more like a “Just Do It” (or a “Just PDSA It” as I'd rather call it).
People in some Lean circles say “kaizens” when they mean “kaizen events.” Art Byrne, former CEO of Wiremold, does that in his “The Lean Post” articles, for example.
Hower, my Healthcare Kaizen co-author Joe Swartz and people at his health system say “kaizens” to mean “small staff-driven improvements.”
So “doing kaizens” can mean two different things, depending on the setting.
Like the US and the UK, are we “separated by a common language”?
Linguistic nitpicking aside, I really like the sound of that new GE culture.
Faster Problem Solving, Safer Problem Solving
One example shared in the article is that they mapped out the previously “convoluted” problem-solving processes that took a really long time to complete — so, thankfully, they looked to reduce that flow time.
Problem solving tends to be better (and faster) when it's done by those closest to the work (and this can sometimes be referred to as Real-Time Problem Solving).
Effective problem solving (and continuous improvement) starts with a foundation — it's a required precondition, if you will — of “psychological safety.“
The GE leaders recognize that. We can't just tell people that they should speak up and that they should feel safe — we have to make it actually safe. The level of psychological safety is the perception of each and every employee, based on what they're experiencing. The boss can't say they should feel safe.
“We learned that the inability to raise issues in the first place was our real problem,” says Ficano. “That helped us to build a system whereby everyone feels psychologically safe speaking up.”
The article describes the “after” — faster problem solving and happier employees. The article also refers to “healthier” employees… I'm guessing that's partly a result of the high-quality pizza being served!
Now, are they also applying Lean methods to how those pizzas are being made? I'm willing to not only “go and see” but to also “go and smell” and “go and taste” in order to get to the bottom of that question, ha ha.
Please scroll down (or click) to post a comment. Connect with me on LinkedIn.
Let’s work together to build a culture of continuous improvement and psychological safety. If you're a leader looking to create lasting change—not just projects—I help organizations:
- Engage people at all levels in sustainable improvement
- Shift from fear of mistakes to learning from them
- Apply Lean thinking in practical, people-centered ways
Interested in coaching or a keynote talk? Let’s start a conversation.
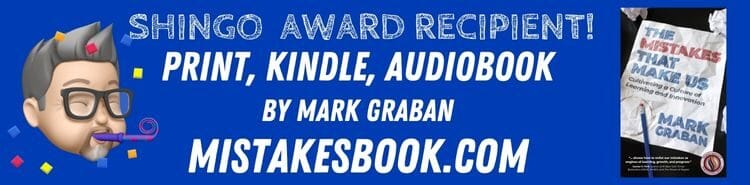