Here is a photo that I took a few years ago at a Krispy Kreme store. For health reasons, I don't go there very often, but it's fun to watch the donut production automation and the donuts are amazing when they're hot and fresh.
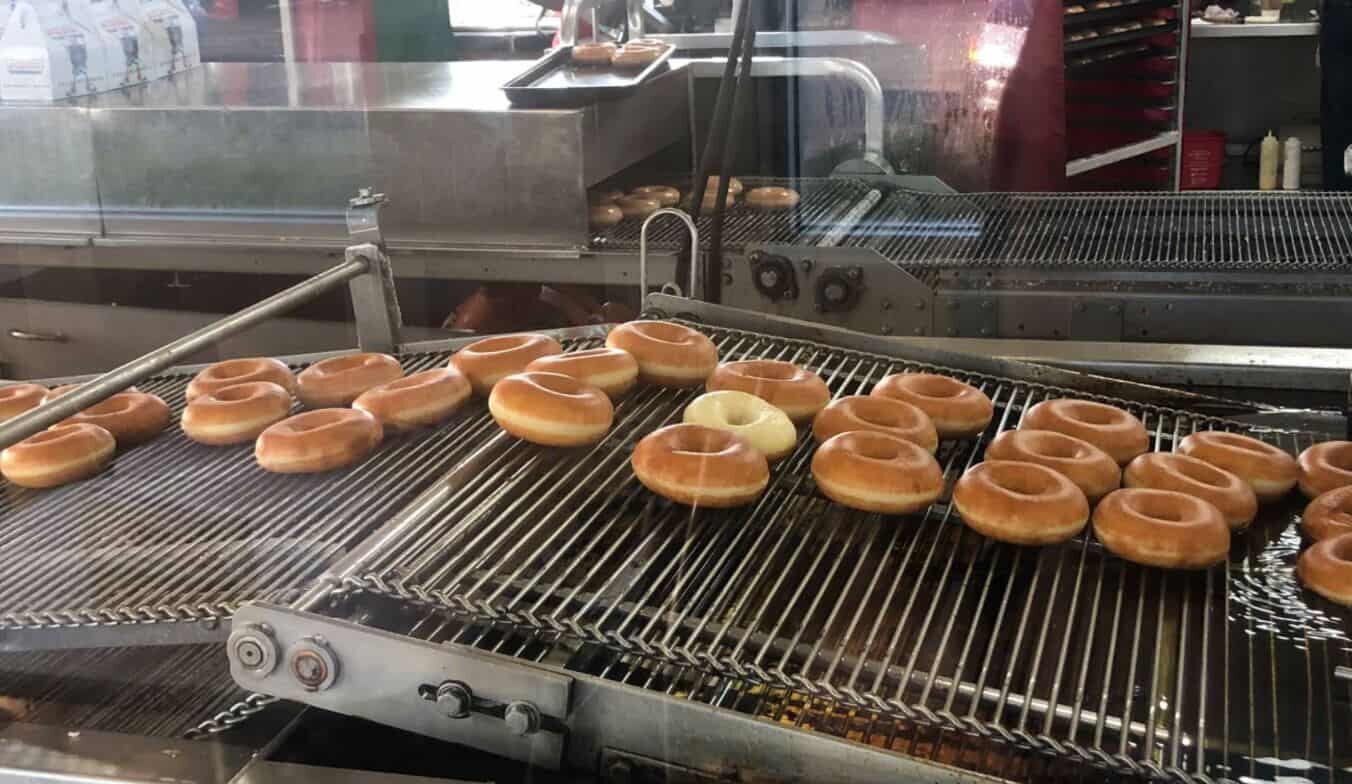
What jumps out at you?
There's a single donut that somehow didn't get flipped by the part of the automation (not seen in the photo, but it's off to the right and the donuts are flowing from right to left toward the customer and the point of sale).
Thanks to Ryan McCormack for this image:
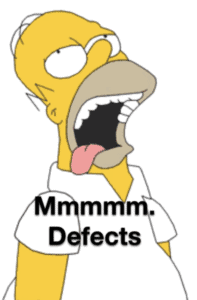
The donut machinery appears to have fried the one side of the donut in oil.
It's impressive that this is all done as a continuous flow. Then, there's a “flipper” that turns the flowing donuts over to fry the other side.
Any process should be designed in a way that make defects visible (if your process cannot perfectly prevent defects).
At least Krispy Kreme can see the defects. Inspecting and sorting out defects (or reworking them) is not the way to provide the best quality at the lowest cost — but it's better than letting defects flow to the csutomer.
Making defects visible is the first step in resolving the problem. Short term, throw out that donut — or, as somebody on LinkedIn pointed out in my initial post there, you can rework the donut by putting it back onto the machine to cook that other side. You'd probably have to catch the defect before it goes through the “glazing” machine”:
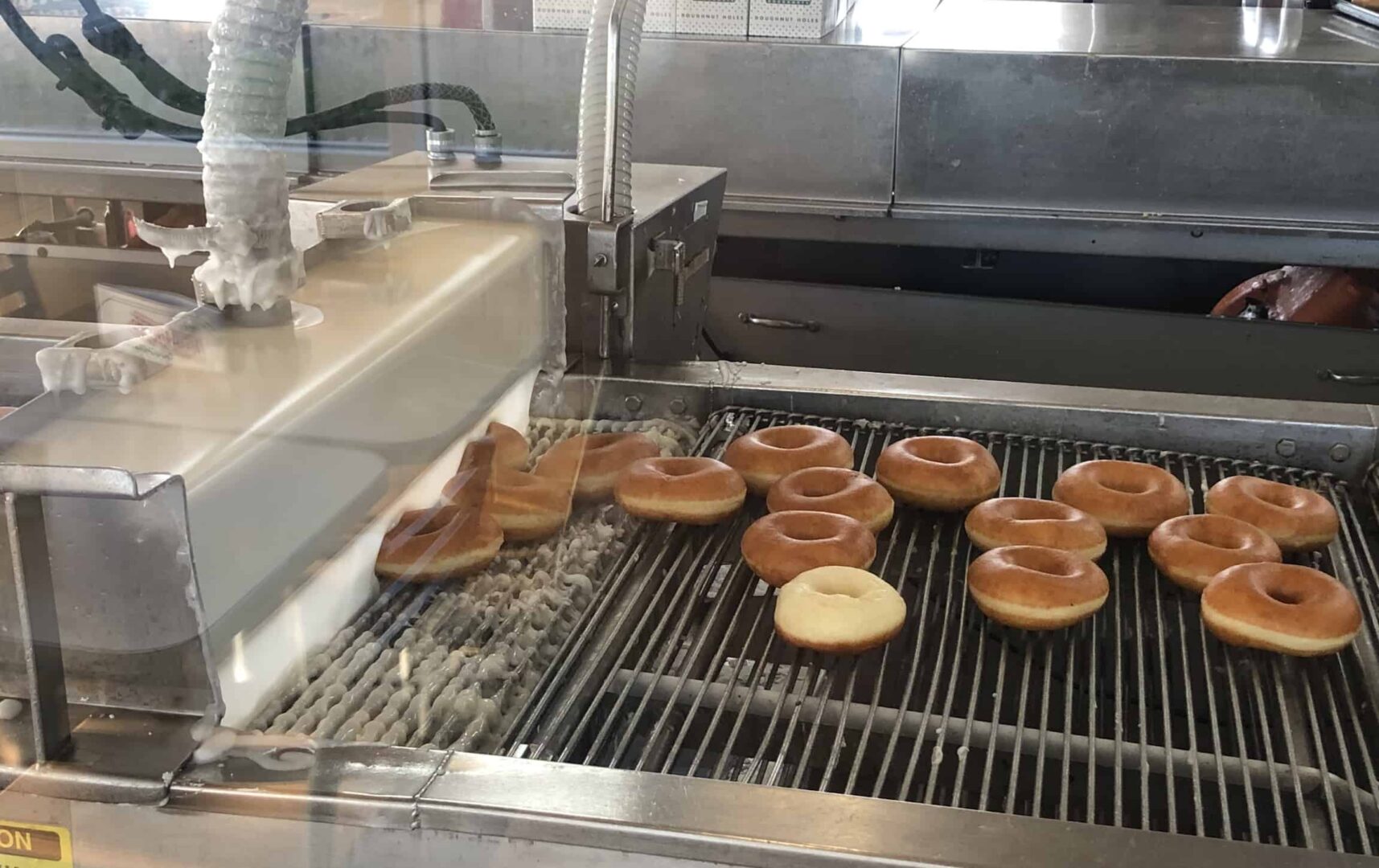
The “cost of poor quality” means throwing a donut away occasionally (I'd love to know the defect rate) or it means positioning an employee there to look for defects.
It's better to put preventive countermeasures in place — how can you make the automation more reliable? You'd want to reduce the waste of throwing a donut out and/or reduce the labor time spent on rework.
In healthcare (and many other types of work), the defects are invisible, which creates quite the challenge. Sometimes the mistakes are intentionally unreported, hidden, or covered up.
How do you deal with that?
As the late Paul O'Neill would have said, it requires leadership.
Leaders also have to create a culture of psychological safety, making it safe to point out mistakes or defects without the fear of punishment, humiliation, or retribution. This is especially true when most problems are caused by poor systems and faulty processes.
It's a mix of better management, solid systems engineering, and continuous improvement.
Thankfully, at a Krispy Kreme, everybody can see that that one donut is half baked (I mean half fried). That donut would probably never reach a customer.
In healthcare, defects and mistakes impact patients far too often, as I wrote about in this recent post for Value Capture about “Patient Safety Awareness Week 2022.”
Here is my initial LinkedIn post about this topic, which I've elaborated on here in this post.
You can post a comment here or you can still join in the original LinkedIn discussion.
Please scroll down (or click) to post a comment. Connect with me on LinkedIn.
Let’s work together to build a culture of continuous improvement and psychological safety. If you're a leader looking to create lasting change—not just projects—I help organizations:
- Engage people at all levels in sustainable improvement
- Shift from fear of mistakes to learning from them
- Apply Lean thinking in practical, people-centered ways
Interested in coaching or a keynote talk? Let’s start a conversation.
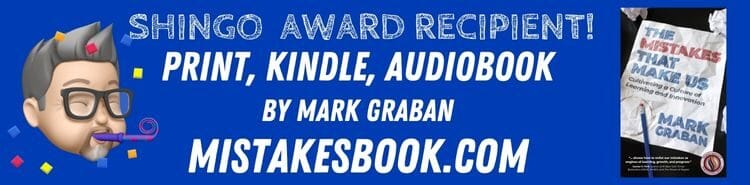