This article made me smile the other day — especially the comments about Lean, front-line staff, and systems:
Q & A with Art Gianelli, president of Mount Sinai St. Luke's
According to his LinkedIn profile, he is also in a role as the “Chief Transformation Officer for the Mount Sinai Health System.”
When asked what helps attract staff to the hospital, Art mentioned Lean:
“Staff are attracted to the opportunity to work for the Mount Sinai Health System. They are also attracted to working for a hospital whose services are growing and increasing in complexity.
Mount Sinai St. Luke's is a Lean hospital.
When I first came to Mount Sinai, I advised Dr. Ken Davis, the president of the Mount Sinai Health System, that my experience of running a hospital was through a Lean framework and that's what I wanted to do here at St. Luke's. He was absolutely encouraging.
From day one, that's what we've done here. We've used Lean to develop our daily management system, for process improvement and to galvanize and energize the culture.”
 That's great to hear. He elaborates:
“It's evident to anyone who comes here, that the experience of working at St. Luke's is different than at other hospitals.
Here, the wisdom of the frontline staff is valued and cultivated. We want our frontline workers to be emissaries of problem solving. I think people who are attracted to that and that level of agency with respect to their work, really want to come here.”
Respecting and engaging frontline staff in improvement is not unique to his hospital… but it's definitely fair to say that, today, a majority of hospitals do not have a true “culture of continuous improvement.” It's out there… and this is what Lean is supposed to entail, since “continuous improvement” is one of the two main pillars of “The Toyota Way” management philosophy — with the other being “respect for people.”
We'll see and hear about a culture of continuous improvement next month at Franciscan St. Francis Health. I'll be blogging and sharing from there (our event is just now sold out).
Read more from Toyota's Jamie Bonini on the philosophy of TPS (which Lean should emulate):
Back to Art… he also said:
“We also try to emphasize the tenets of a just culture. Errors, when they do occur, are typically associated with system and process failures. What we're not trying to do is create a culture of blame, we're creating a culture where we can examine our failures and do so honestly and transparently in a way that's not pointing fingers at our employees, but instead identifying processes that can be fixed and improved.”Â
That's also fantastic to hear. I've written about “just culture” before and that's very much in line with Lean/TPS mindsets.
Most problems are caused by system problems. It's not fair and just to blame individuals for systemic problems. The “just culture” approach helps us figure out when it's fair and just to “hold a person accountable.”
Too often, when an individual gets blamed, the response might include “re-training” or other approaches that seem unlikely to help prevent future problems that will result from the same, unfixed failure mode.
When asked about our broader healthcare cost challenges in the U.S., Art again mentioned Lean:
“The real debate should be about how we can organize the delivery system in a way that reduces waste significantly such that we can change the trajectory of health care costs. Some estimates have pegged the waste generated by our health care delivery system at $750 billion annually. One of the reasons we're committed to Lean at Mount Sinai St. Luke's is because its focus is the elimination of waste and the introduction of value to the patient through innovation.”
 As he says, it's not just about waste reduction (doing less of the wrong things), but it's also about doing MORE of the right things — providing value in terms of health outcomes and quality of life.
Here is a webinar that I did for Gemba Academy on waste in healthcare, citing similar numbers. Better quality doesn't have to cost more…
I also saw an article in the Wall Street Journal the other day about how better quality doesn't have to cost more in healthcare. That has certainly been proven out through Lean — in many industries. And there are other innovative approaches that can help.
Cutting Medical Costs Can Be a Bargain
I'll be interviewing Art and one of his colleagues who is also involved in leading their transformation efforts — check out my podcast series and be sure to subscribe so you don't miss the episode. We'll be able to delve into all of this in more detail.
Please scroll down (or click) to post a comment. Connect with me on LinkedIn.
Let’s work together to build a culture of continuous improvement and psychological safety. If you're a leader looking to create lasting change—not just projects—I help organizations:
- Engage people at all levels in sustainable improvement
- Shift from fear of mistakes to learning from them
- Apply Lean thinking in practical, people-centered ways
Interested in coaching or a keynote talk? Let’s start a conversation.
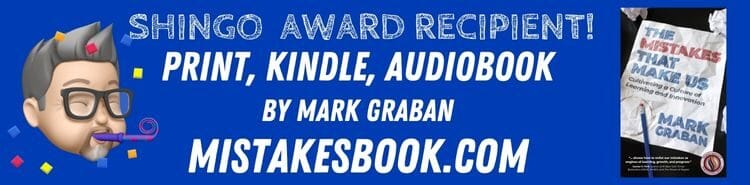
I think this article is very interesting in the sense that I had not previously thought about a hospital in this context. It is great to see the steps they are taking to empower their front line workers as this is where the majority of the problems may occur, and similar to manufacturing often times these workers have solutions that can help improve the process.