Tesla CEO Elon Musk has been quoted as saying he will:
…”school Toyota on Lean manufacturing.”
OK, let's take inspiration and lessons from the apparent Tesla Way management system. What would happen if hospitals and other organizations tried emulating Tesla instead of Toyota? What are the methods and mindsets? The behaviors and principles? What's the management approach and culture?
Let's explore just a few elements of the apparent Tesla Way:
Meeting Targets
At the end of the first quarter, Tesla was very far behind its stated production goals for the Model 3. The stated goal was 2500 cars per week. They managed to hit 2020 in the last week of the quarter.
This was after they missed their original goal of 5000 cars per week by the end of Q1.
Lesson: If you can't make your goals, lower them. You had a goal of getting your average Emergency Department waiting time down from 4 hours to 2? Don't have it down to 2… revise the goal to 3 hours. Promise that you'll get the average waiting time down to 2 hours next quarter.
Motivating Staff
What contributed to this Q1 “near make” for Tesla? One factor might have been what some might label a “motivational” email memo that was sent to Tesla employees by Doug Field, their head of engineering and production, before the final end-of-quarter push.
The Los Angeles Times framed it as:
“Tesla executive exhorts workers to ramp up Model 3 production and prove ‘haters' wrong“
Ah, exhortations. Elon Musk might not have the time of day for that old (dead, actually) fuddy-duddy W. Edwards Deming used to complain about exhorting workers all the time.
Point #10 of his famed “14 Points” said:
10. Eliminate slogans, exhortations, and targets for the work force asking for zero defects and new levels of productivity. Such exhortations only create adversarial relationships, as the bulk of the causes of low quality and low productivity belong to the system and thus lie beyond the power of the workforce.
- Eliminate work standards (quotas) on the factory floor. Substitute leadership.
- Eliminate management by objective. Eliminate management by numbers, numerical goals. Substitute leadership.
Well, Elon Musk and Tesla might say they are going to school Deming on quality and leadership.
Exhort away…
Field wrote (the memo was obtained by Bloomberg):
“The world is watching us very closely, to understand one thing: How many Model 3's can Tesla build in a week?” Field wrote. “This is a critical moment in Tesla's history, and there are a number of reasons it's so important. You should pick the one that hits you in the gut and makes you want to win.”
At the time, Tesla was reportedly building 200 Model 3s a day. Field was exhorting the employees to build 300 a day. That's a 50% jump.
Lesson: Send memos to hospital staff telling them THEY need to figure out how to improve patient flow. “How many patients can this hospital see in one week?” Imply that your staff aren't winners unless they hit this goal.
A memo exhorting the workers to care more and to try harder is Tesla's attempt at schooling GM in the preachy, blaming memo department (as I wrote about here and here with GM stories from over 20 years ago).
Does Field really think that the problem is the workers? They are probably doing the best they can given the decisions made by leaders about system design and automation (including a mistake that Musk admitted, as I blogged about here).
Finding External Enemies
Field, in his memo, was trying to create an “us against the world” mentality. I guess that's better than workers focusing on an “us against management” mindset.
Those of us who are doubting or criticizing Tesla are being labeled as “haters.” Well, that's constructive. Let's pick an external enemy instead of focusing on what you can control. Field wrote:
“I find that personally insulting, and you should too,” Field wrote in the March 23 email. “Let's make them regret ever betting against us. You will prove a bunch of haters wrong.”
Lesson: Blame an outside party, like the Leapfrog Group or the Joint Commission. Tell staff that Leapfrog patient safety grade of “C” is “personally insulting.” Call the Joint Commission “a bunch of haters.” That will certainly motivate your staff. Unless your staff are also a bunch of haters.
Not to be schooled on motivational memos by Field, Elon Musk sent his own missive to employees (after taking over production from Field), where he set a goal of 6000 per week.
“Any Tesla department or supplier that is unable to do this will need to have a very good explanation why not, along with a plan for fixing the problem and present that to me directly. If anyone needs help achieving this, please let me know as soon as possible. We are going to find a way or make a way to get there.”
What if the problem is an over-reliance on automation, which Musk earlier admitted was his fault?
Memos like this, and the ones sent by GM, follow the pattern of blaming the workers and those lower in the organization.
“We are going to find a way or make a way to get there,” writes Musk. If it's that easy, where was that attitude and focus in previous quarters?
Lesson: If your hospital executive team chose a bad Electronic Health Records (EHR) system or didn't provide enough training, and that's bogging down patient flow, tell the staff and the departments that THEY need to come up with plans.
Last year, Musk was praised for sending a memo where he said he'd meet with workers who got hurt and that he'd come do the job of anyone who got hurt. Even Tesla admits he hasn't followed through on that.
Lesson: Write a memo promising to meet with any employee or patient who is hurt. Say that you'll go and do the same work (paging Dr. Musk) have the same medical procedures done to yourself to prove that things are safe.
Another View
I'm not the only “hater” regarding these memos. Read this insightful article:
“Tesla doesn't understand that its goals are different from its employees'“
“to a lot of people, shipping out 2,500 Model 3s per week probably sounds like a pretty arbitrary thing to strive for.”
There's that pesky Deming popping up, with his warnings against arbitrary targets (it's in that same point #10). As Brian Joiner wrote in his book Fourth Generation Management: The New Business Consciousness, there are three things that can happen when you have a quota or a target:
- Distort the system
- Distort the numbers
- Improve the system
The number of cars produced is pretty hard to distort, since those are easily counted (although somebody could report inaccurate numbers). It's more likely that people are pressured into distorting the system (including letting quality and/or safety suffer). Or, they could actually improve.
I hope it's the latter. And that improvement would probably mean Tesla leaders improving systems, rather than thinking the results came from workers working harder.
Fleshing out “The Tesla Way?”
So what is “The Tesla Way?”
Maybe Jeff Liker can write a book called The Tesla Way. Nah, Musk would call him a “hater.” Will an MIT research team go and study Tesla (Jim Womack has already volunteered, in a way). Maybe a whole industry of consultants will pop up to certify you as a “Tesla Belt.”
Are you inspired by the Tesla Production System? Want to adopt or adapt it for your organization?
“But we don't build electric cars…”
OK, never mind.
Update: Field left Tesla to re-join Apple.
Please scroll down (or click) to post a comment. Connect with me on LinkedIn.
Let’s work together to build a culture of continuous improvement and psychological safety. If you're a leader looking to create lasting change—not just projects—I help organizations:
- Engage people at all levels in sustainable improvement
- Shift from fear of mistakes to learning from them
- Apply Lean thinking in practical, people-centered ways
Interested in coaching or a keynote talk? Let’s start a conversation.
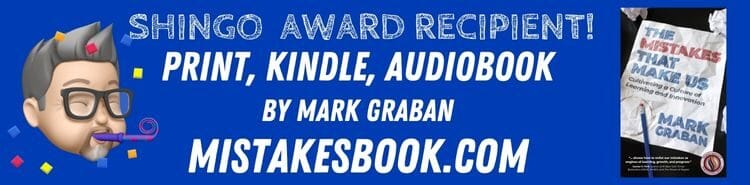
The discussion on LinkedIn:
No where does it mention the customer demand for the Tesla Model 3 per day or week or whatever. Is 2,020/week? 2,500/week? 5,000/week???? If the demand rate is lower than any of expected outputs it is over production and I can still hear Bruce Hamilton’s voice ringing in my ears from the Toast Kaizen video, producing more than what the customer demand is over production waste.
If the demand is greater than what they can produce you introduce Muri with it’s own potential negative consequences.
Good question. Tesla is unlike most other automakers in that they have the pre-orders and a backlog they are working from.
From what I’ve read, when waiting list were given the chance to order, 70% have said “no.” It could be they are saying “not now” and are waiting for the future $35,000 base model that Tesla isn’t making yet.
I found this analysis of the backlog:
Tesla May Be Burning Through Model 3 Orders Faster Than Expected
So the answer to the “takt time” question is “we don’t know for sure?”
Elon claims that they have 2 years of backlog at 5000/week production.
https://twitter.com/elonmusk/status/992374493132742656?s=21
At least they won’t have to change the TPS report name….
In today’s news:
Tesla stock drops as Elon Musk gives bizarre earnings call
From TechCrunch:
Tesla earnings show record revenues with record losses
Less than 10 years ago in our organization (a budding lean hospital) the hospital administrator exhorted every department leader to “press the pedal harder” and “tell your employees to be nicer” to improve patient satisfaction scores. Nobody blinked then but it is almost laughable now because we have proven exhortation does not result in improvement.
Speaking of arbitrary goals, another hospital system from about the same time and renowned for their lean progress had a stated annual goal of 10% productivity improvement. I am sure that came from their Toyota trained consultants. Fortunately for their patients, they missed that goal, got rid of their consultants, and decided to forge their own lean path.
Why do you say “fortunately for their patients?”
I agree arbitrary targets can drive a lot of dysfunction. Productivity improvement would be good. Of course, unless people pushed productivity at the expense of safety and quality. Then again, doing so wouldn’t be the least bit “Lean.”
I think many organizations set aggressive productivity improvement goals without consideration to the big picture. If some organization has achieved a 10 percent productivity improvement in one year and maintained or improved safety and patient experience I would like to know how they did it.