I hope you're a regular listener to my Lean Blog Podcast series, where I've interviewed authors and Lean leaders since 2006.
I've been doing podcasts so long that they were trendy, then out of style, and now they've been fashionable again in recent years.
Some people give me feedback that they would just rather read than listen. I get that. I'm not really an audiobook person, myself, but I do listen to a few other podcasts (about Lean and otherwise).
I've published full or partial transcripts for some episodes for free on the blog and I've also compiled others into an eBook that you can buy through LeanPub or the Kindle Store (note to self, update the eBook with the more recent podcasts).
I've had some people, including recent guest Tom Ehrenfeld, suggest that I share highlights from podcasts – quotes and short audio snippets that are shareable. That way, people who don't want to listen to a 45-minute discussion can get something out of it.
My first experiment was to compile highlights from Podcast #262 with Steve Spear.
Some of these highlights can be read in this LinkedIn article (and the text is also found further down in this blog post, but the audio clips are only in the LinkedIn post)
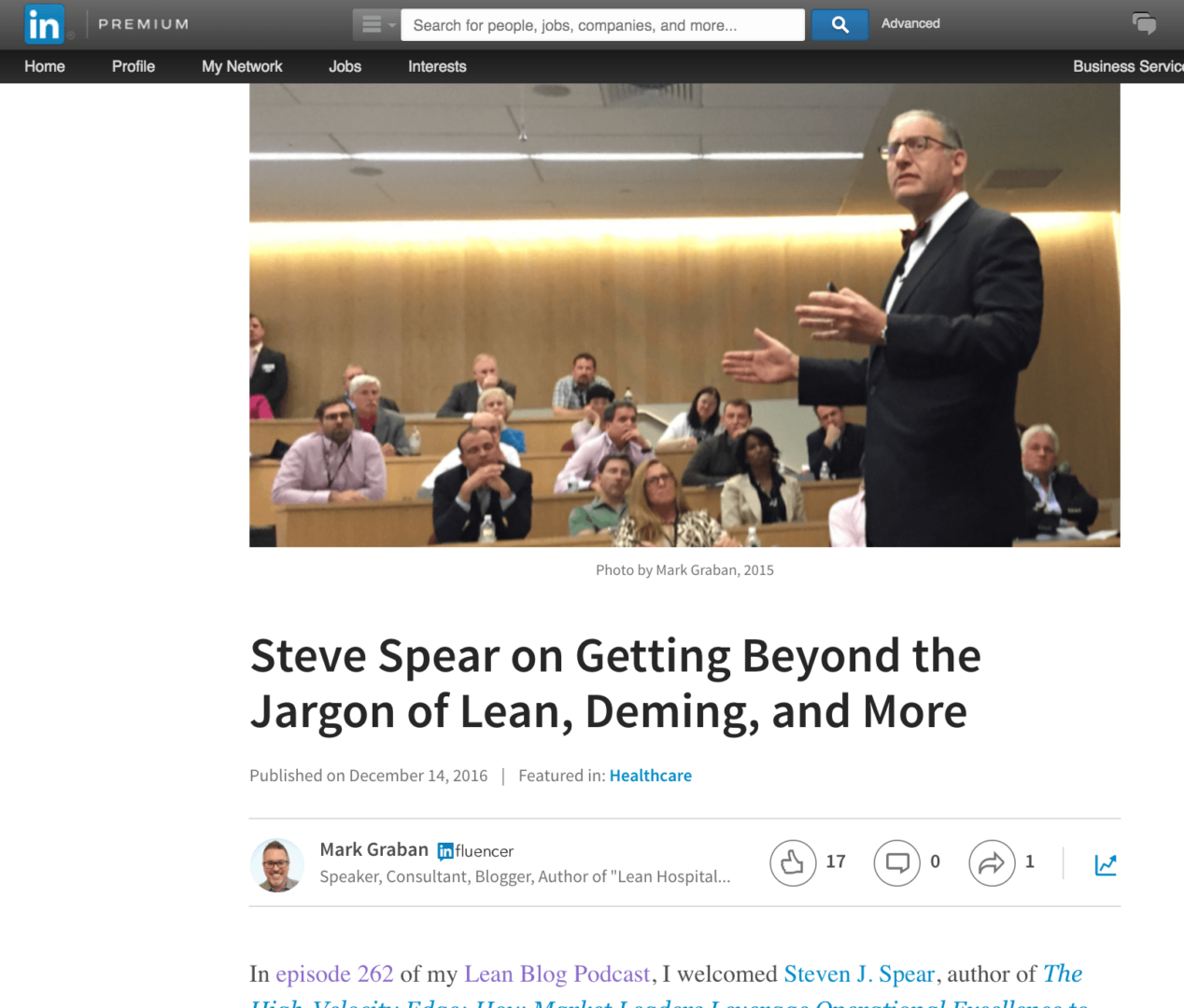
That page has some short audio snippets embedded, and you can also find them on a new Soundcloud channel that I've set up.
I hope that experiments like this make the great thoughts of my guests more accessible.
More highlights from this episode will follow in a future post.
If you have feedback or suggestions, please let me know. Are there old episodes you'd like to see get this treatment?
In episode 262 of my Lean Blog Podcast, I welcomed Steven J. Spear, author of The High-Velocity Edge: How Market Leaders Leverage Operational Excellence to Beat the Competition. This is the third time I've interviewed Steve, who was also a guest in episodes 58 and 87. Here are some highlights from the full discussion:
How can we help people in healthcare see the parallels and relevance of the ideas behind gemba, kaizen, Lean, and statistical process control, beyond the jargon of the terms themselves?
I began by asking Steve about the crux of his journal article Beyond the Jargon, and the idea that there is value that providers and health care systems could reap from examining other industries, such as electronics and automotive, to improve functionality, quality, availability, and affordability, however, the lessons can seem impractical and contrary when not translated into the culture and language of medicine.
“What we're really concerned about is a basic phenomenon, and it's the ability of certain organizations to deliver far more value into the marketplace, quicker and easier than their counterparts,” Steve began. “To deliver means trying to harmonize the efforts of many people toward some common purpose.”
Underneath that phenomenon, there must be some basic science about how to manage complex, dynamic systems to achieve great results. Issues begin when different communities look at the same challenge and start assigning labels to that science. Steve explained:
“The problem with labels is that they start acquiring meaning to a subset community, which is not transferable to other communities,” he said. “The lexicon originally was meant to be clarifying for those using the lexicon. What ends up happening, is it becomes confusing.”
Steve gave the example of “gemba” and all the rich meaning behind those five English letters for people within the industrial world, which is lost when mentioning gemba to a doctor or a nurse who has never heard the word before, much less being aware of its meaning. When explaining the term to someone who has never heard it before, it usually gets translated through a very shorthand and abbreviated explanation like “go to the shop floor.”
“To them it's like, ‘well I don't even have a shop floor, I have a bedside.'” Steve said. “If we want to communicate well with those communities, it becomes wickedly important to respect the lexicon, the meaning, and the values behind it, and communicate through their lexicon; and not insist that they learn ours, in a sense as a second language.”
Toyota, W. Edwards Deming, and Admiral Hyman G. Rickover; can you successfully synthesize these systems?
When the conversation turned into a discussion about the barriers some Lean lexicon can have, even within the manufacturing community, I took the opportunity to ask Steve's opinion on the merging of terms like Lean, Six Sigma, and TQM into terminology like “Lean Six Sigma”.
“It's not obvious to me that Deming had much influence on Toyota's thinking, it's not obvious that Toyota had much influence on Deming's thinking,” Steve said, also introducing another organization he's written about, the Naval Nuclear Propulsion Program. “It's pretty clear that Toyota and Deming did not influence the founder of that program, Hyman Rickover.”
“The folks at Toyota, Edward Deming, and the Navy reactor program were dealing with exactly the same common challenge of this harmonization of human effort toward a common purpose. And not surprisingly they came up with some real common ideas, and fundamentals.”
Steve continued to explain that leaders in building each of these systems developed a lexicon as well as tools to express or achieve the underlying fundamental common principles. The problem in the industrial and organizational fields in general, Steve suggested, is that there is this very fundamental, parsimonious, basic science about managing these complex systems, which are subject to constant disruption, but students new to these movements don't learn, internalize, and socialize on the fundamentals first, they're just handed the tools.
“It's like if you went to engineering school and they didn't tell you about Newton but they gave you MATLAB.” Steve explained. “The reason we have this fragmentation and then these sort of funny attempts to synthesize is because as practitioners we don't come back to the basic science, we just look at the tools, and identify by the tools and not the core principles.”
Continuing the conversation about synthesis of management systems, I brought up the complaint I sometimes hear, which is that while synthesis is a good goal, this blending can be problematic at times. For example, someone who is interested in Lean may find a “Lean Six Sigma” course and think this is their opportunity to learn both systems, only to have that course be 90 percent Six Sigma deep statistical methods (see my blog post on this subject).
Steve agreed this is a problem, considering that each system was created to gain some dynamic control over a complex system, but these systems vary and one method, like statistical analysis, may be good for one situation or environment, whereas another might require something different.
Steve went on to say that to have some sort of blind, ritualistic adherence to one system and not the other both shows a lack of fidelity to the geniuses behind these systems, and is not productive.
Steve's work has talked about the competitive advantage of a learning organization in the past, and when asked about this he spoke about how learning is essential today.
In a world that is changing faster and faster, your current capability and your current knowledge level becomes less and less relevant, faster and faster, Steve told me:
“The only way to keep pace is to learn better, faster, more consistently about what you should be doing and how you should be doing it, because what you were doing and how you were doing it may have mattered a day, a week, a month a year ago, but for sure it matters less right now. And in a day, a week, a month from now it will matter even less.”
Please scroll down (or click) to post a comment. Connect with me on LinkedIn.
Let’s work together to build a culture of continuous improvement and psychological safety. If you're a leader looking to create lasting change—not just projects—I help organizations:
- Engage people at all levels in sustainable improvement
- Shift from fear of mistakes to learning from them
- Apply Lean thinking in practical, people-centered ways
Interested in coaching or a keynote talk? Let’s start a conversation.
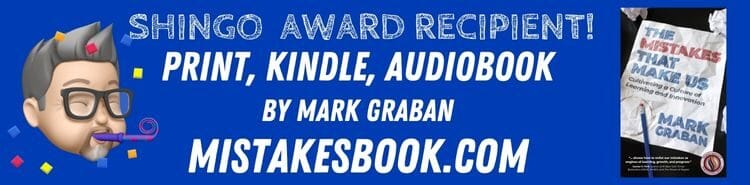