Reminder: I'm doing a webinar today with Dr. Greg Jacobson, CEO of KaiNexus, titled “How To Spread Continuous Improvement” and I hope you'll join us. Register if you can attend live at 1 pm CDT or we'll send you a link to the recording.
Dr. W. Edwards Deming advised against relying on slogans and posters as a way of trying to improve quality.
Point 10 of his famed 14 points said:
Eliminate slogans, exhortations, and targets for the work force asking for zero defects and new levels of productivity. Such exhortations only create adversarial relationships, as the bulk of the causes of low quality and low productivity belong to the system and thus lie beyond the power of the work force.
See my friend John Hunter's post on this topic.
In a recent LinkedIn post, there was a comment that surprised me a bit since Dr. Deming wasn't the topic at hand. I think the topic was Lean and Six Sigma…
The comment, which I'm certain is from a true story said:
“Motorola used to buy floor mats. One read “Do the right thing.” One of my guys called me over, pointed at it and said “WTF do you think I try to do?” Rolled it up and we got some plain floor mats.”
The sign might have looked something like this:
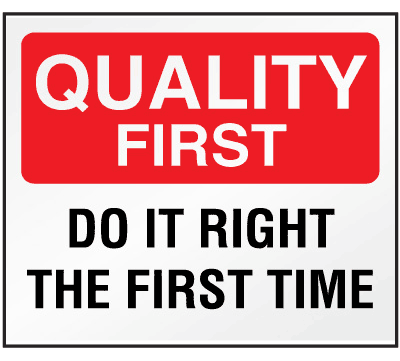
I totally understand why this might be offensive to people who are trying to do their best.
When I worked at GM 20 years ago, I learned that even the oft-maligned UAW production workers generally wanted to do quality work. They aimed to have pride and joy in their work, as Dr. Deming would have said.
I can think of a dozen ways in which management, at different levels, directly interfered with people doing quality work — namely by putting quantity (make your numbers!) before quality. That gets extremely demoralizing to say the least.
Management wasn't letting them do the right thing. For example, management wouldn't let the production workers stop the line momentarily to do their quality checks on machined parts – that was supposed to happen roughly every 30 or 45 minutes depending on the production rate. If inventory was low or management was concerned about looking bad for not making their numbers, employees were told to keep the line running.
Do the right thing? Ha!
Listen to Mark read this post (subscribe to the series):
When you have a demoralized or frustrated workforce, the last thing they want to see are posters lecturing them about quality or safety.
I would definitely NOT recommend that hospitals try to improve quality and patient safety through signs and posters. We need to, instead, fix processes and systems. As Dr. Deming said, “substitute leadership.”
Signs might look like in the operating room:
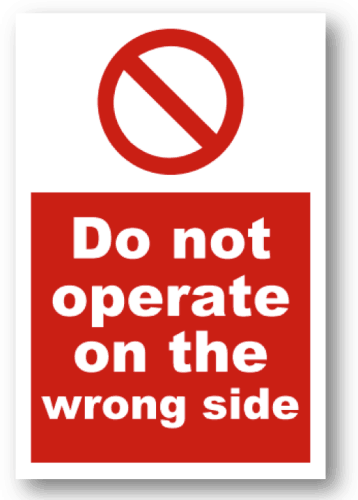
or in an inpatient unit:
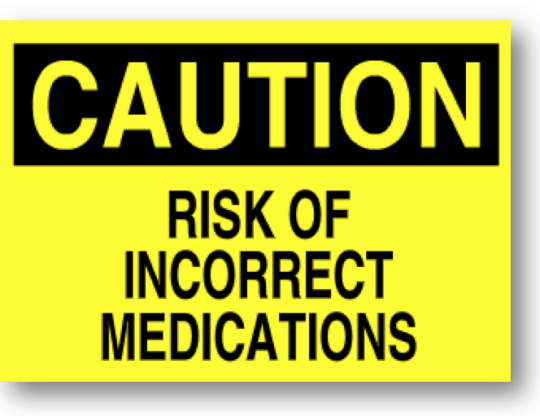
Nah, those wouldn't work. I hate to tempt anybody to even try… if it were this easy to improve healthcare quality, somebody would have tried it (and we'd have perfect quality without Lean or Six Sigma in manufacturing long ago).
We don't see signs like this in healthcare, even if the mindsets are present… the mindset of lecturing employees to be careful or blaming them when something bad happens.
Maybe healthcare management has more respect for their employees than manufacturing leaders. But, the hospitals are still searching for basic quality improvement methods that many factories mastered long ago.
Please scroll down (or click) to post a comment. Connect with me on LinkedIn.
Let’s work together to build a culture of continuous improvement and psychological safety. If you're a leader looking to create lasting change—not just projects—I help organizations:
- Engage people at all levels in sustainable improvement
- Shift from fear of mistakes to learning from them
- Apply Lean thinking in practical, people-centered ways
Interested in coaching or a keynote talk? Let’s start a conversation.
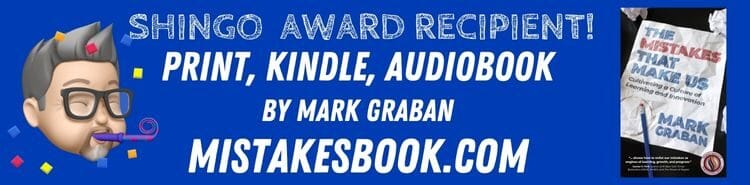