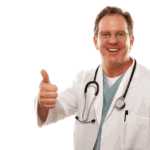
One of the two main pillars of the Toyota Way management system is “respect for people.” I've blogged about that often over the past ten years, including this post.
“Respect for people” is a critically important (and necessary) component of a Lean transformation effort. Toyota has referred to “respect for people” and “continuous improvement” as the “equally important pillars” of their management approach. As Bob Emiliani says, it's “Fake Lean” if you only focus on the “continuous improvement” pillar and ignore “RFP.”
In contrast, hospitals have been guilty of many practices that are not respectful to staff or to patients. This includes unfortunate situations like hospitals tolerating surgeons who yell and throw things in the operating room and hospitals not doing everything possible to truly make safety a top priority. There are also the mundane and harmful situations where staff are not listened to and their ideas are ignored.
Lean provides a philosophy and a management model that should be nothing but good for staff and patients. The idea of “respect for people” might sound nice in principle, but what does it mean in a practical sense.
Respect for people can be illustrated in these ten ways, and more:
1. Ensure people have what they need to do the work
If you get to tour a Toyota plant, you'll notice how they put a lot of effort into making sure production team members aren't having to run around to search for tools or supplies. A Lean hospital would ensure that healthcare professionals have what they need to do their patient care work. This includes having the right amount of equipment and supplies, making it quick and easy to find, making sure things are working properly, and more.
2. Don't put people in a broken process
We often hear the lament that hospitals have “great clinicians and great people working in a broken system.” It's frustrating to doctors when they are always behind schedule and it's frustrating to everybody who is working in an overwhelmed emergency department that has patients waiting in the hallways for days. We shouldn't stress people out by expecting superhuman performance to outweigh poorly designed systems. That's a recipe for errors and burnout.
3. Don't drive cost cutting through layoffs
The traditional healthcare approach is “cost cutting” and since 60-70% of a health system's cost is payroll, that's where executives usually look first. These cycles of layoffs might harm quality, even though the layoff announcements always claim “patient care will not be affected,” and it definitely hurts morale. The best Lean hospitals, including ThedaCare, have some form of a “no layoffs” philosophy or “no layoffs due to Lean” policy as they find other ways to reduce cost through process improvement. Some CEOs have realized that the old cycles of layoffs haven't really reduced costs and they're using Lean as an alternative.
4. Don't overburden people
Unfortunately, hospitals overburden staff in a number of ways. I've seen nurses with 80 minutes' worth of tasks to complete each hour. It's impossible. Many people talk about “muda” (the Japanese word for waste) but we also have to pay attention to “muri” (the word for overburden) in a Lean culture. Working an exhausting 12-hour shift (or multiple shifts in a row) is probably an unreasonable overburden. Overburden leads to errors and harm to patients. To reduce this overburden, we need to reduce waste and free up time or…
5. Have proper staffing levels
Lean teaches us to not “throw people at a problem,” but there are times when I've seen a department that's actually understaffed (therefore, the staff are overburdened and quality suffers). There are many times when Lean can be used to reduce staffing levels, which is best handled by redeploying people to other areas, growing and providing more care with the same staff, or not replacing people who leave through natural attrition. I've been involved with Lean projects where the data unmistakably showed that an area was understaffed and that got corrected. Facts trump opinion or feelings on this.
6. Give help and support when needed
When staff are struggling with overburden or other problems, managers need to be there as supportive servant leaders. We don't leave overburdened staff to fend for themselves or “be tough.” A Lean culture doesn't look down on people for speaking up when they need help. Again, when visiting Toyota, we see how employees are encouraged to “pull the andon cord” and they get help and support instead of getting scowls for stopping the line.
7. Not blaming people for systemic errors
In healthcare, most problems, errors, mistakes, and harm are caused by systemic factors, such as overburden, poor training, or other process problems. It's not just Lean that believes and teaches this, but also see “Just Culture” as a methodology. It's not fair to expect people to “be careful” in a bad system or when they are overburdened. Lean helps us move away from the traditional “name, blame, and shame” healthcare environment. This culture shift is not just the “nice” or “right” thing to do — stopping the blame game is the best way to protect patients and improve quality. Read more about this.
8. Let people do meaningful work
Lean leaders help connect people to the mission and the purpose of their work. A Lean culture doesn't just ask “why?” when problem solving or investigating a root cause, it also “starts with why” and explains why work should be done a certain way. We don't want people to just be busy (including searching for supplies, which is busy but not value adding or rewarding), but we want them to be able to care for patients and focus on the work that's most meaningful (see the “Loving Care” approach from Holland).
9. Work to your level of licensure
In line with doing meaningful work, Lean focuses on:
- Letting nurses be nurses
- Letting doctors be doctors
- Letting medical technologists be med techs
- Letting pharmacists be pharmacists
- Letting anesthesiologists be anesthesiologists
It's not difficult to see people doing work in a hospital that should be done by an assistant or somebody with a lower level of clinical training. Hospitals often have a shortage of support staff — which might seem like it's saving money, but that's probably not the case if, for example, the lower level of laboratory assistants means that you're paying a more expensive med tech to do that work. It increases costs and demoralizes staff if they're not allowed to do the right work.
10. Listen and engage people in improvement
And, of course, Lean respects people by making it safe to speak up, by listening to them, and by engaging them in the Kaizen improvement process. This is such an important concept that Joe Swartz and I wrote a book about it (you can get chapter 1 here or an executive summary document).
What do you think of this list? What would you add? How does your hospital score on these ten dimensions of Lean and respect for people?
You can also share this image via social media or use it in your Lean education materials:
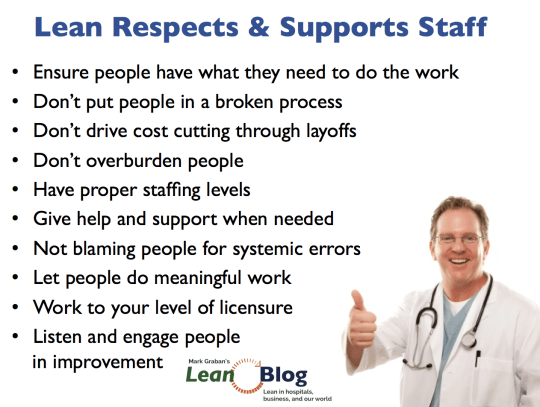
Thanks for reading.
Please scroll down (or click) to post a comment. Connect with me on LinkedIn.
Let’s work together to build a culture of continuous improvement and psychological safety. If you're a leader looking to create lasting change—not just projects—I help organizations:
- Engage people at all levels in sustainable improvement
- Shift from fear of mistakes to learning from them
- Apply Lean thinking in practical, people-centered ways
Interested in coaching or a keynote talk? Let’s start a conversation.
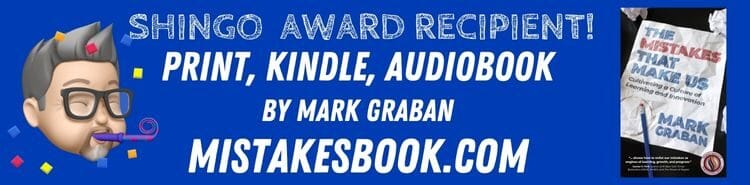
Would you expand on Point 9: work at your level of licensure. I’m not as familiar with the specifics of a healthcare environment, but this suggestion seems that it may introduce some batch/inventory/waiting waste to the process. For example, one complaint in a union-shop manufacturing environment is that one always waits for the “trained” individual to do specific tasks. In business, we often see functional silos that create batch/queue/inventory/waiting environments. How do you see the balance of small batch, JIT, cross functional work . . . and level-loading capacity of each healthcare worker? I’m not trying to apply lean “tools” indiscriminately, just would like to hear more details about how adding support staff reduces process waste and creates value for the customer.
Hi Brad – thanks for your comment.
Sometimes, in healthcare, there are licensing/regulatory requirements about who can do certain work. Often, this is in the best interests of quality or safety for the patients.
I don’t think of it so much as a matter of silos, but the right people doing the right work.
In a factory, if I had an electrician making 2x the hourly wage of an assembly associate, I wouldn’t want A) to pay an electrician to do assembly work (unless there was an opportunity to make use of an electrician’s idle time) and B) I wouldn’t let an unskilled associate try to do electrician work.
In healthcare, the higher skilled nurse, for example, isn’t as likely to be idle. If the nurse has NOTHING to do, it’s great for a nurse to do work that would normally be done by a tech or medical assistant. I’d call that teamwork, it would probably not hurt quality, and it would probably help patient flow.
But, if a nurse is ALWAYS doing work that could be done by a tech, adding another tech might increase costs in that budget bucket, but freeing up nurse time probably leads to better quality, shorter length of stay, and higher patient satisfaction, which has a huge financial impact for the hospital.
There are arguments for “let nurses be nurses” that go beyond their professional pride. I’m not advocating for an environment where people huff and say “that’s not my job.” But, sometimes it’s worth having people doing the right work for their skills and paycheck.
Hopefully that’s a helpful expansion on that point.
From LinkedIn:
Peter Dun van
Quote: Respect for people” is critically important”!
Megan De Graaf
Excellent article. Having been a nurse for many years, I have worked in a few hospitals that obviously didn’t seem to understand those basic principles. Many times cost cutting measures put non-nursing tasks onto nurses already full plate,
Tonye Barango
A very helpful and important reminder regarding the “total” improvement process!
[…] Respecting people (see more) […]