Here's an article from Bloomberg BusinessWeek:
GE's Larry Culp Faces Ultimate CEO Test in Trying to Save a Once-Great Company
Very early on, the article mentions Culp's advocacy for “Toyota-style lean manufacturing.” Or is he pushing “Danaher-style lean manufacturing” and is that different? And does that matter?
Culp was “in his element” visiting a GE factory in Pensacola — can that be said about most CEOs?
Wearing jeans,
“He spent about two hours walking the floor and chatting with technicians, stopping only briefly for a call with the board of directors.”
Culp asked about what might be called production status boards:
“While overhead screens flashed measurements of the production pace in eight-hour increments, Culp wondered aloud if the metrics were visual enough and whether they could be broken down into 20-minute or even 10-minute slices, so workers would know sooner when they might be falling behind on their goals.
At the tour's end, he urged them to face up to production issues as early in the process as possible–or, as he put it, “Let's make it red, make it ugly, let's go fix them,” Wiesner recalls.”
The idea of making problems visible resonates with me. If there is a measurable “gap” between planned production and actual production numbers, a Lean organization wouldn't try to hide that reality. Understanding the real reality is key if you're actually going to work to improve.
Visual metrics (for understanding the real-time real reality) can be very helpful, but I'd add it's not just “workers” who need to know about this status. Supervisors (team leaders) and other managers need to know about this status so they can work together to solve problems. It's not about blaming workers — and I'm guessing it's the Bloomberg BusinessWeek writer who is putting this on the workers, not Culp. Sometimes Lean gets lost in translation through reporters.
At a company that used to train all leaders in Six Sigma, Culp is educating them in Lean:
“Culp ordered almost 50 GE business heads to take off June 10-14 for an on-the-factory-floor, “true-lean” manufacturing boot camp that he's helping to teach.”
If Culp is teaching “true Lean,” the article doesn't make clear who had been teaching “fake Lean” or what that entails.
Danaher and Lean
The article also gives some background about Culp and Danaher, his former company.
“Danaher was one of the first U.S. companies to adopt Toyota Motor Corp.'s kaizen process of increasing productivity with tiny, continuous improvements.
Its own version is called the Danaher Business System, or DBS, which in some ways resembles the Six Sigma quality-assurance regimen Welch embraced in the 1990s.
DBS relies heavily on measurable facts, including not only profits and sales but also nonfinancial metrics such as on-time delivery. These are measured on monthly, weekly, daily, and even hourly bases, depending on a project's urgency. From the moment Culp joined Danaher in 1990, he embraced it like a religion.”
I'm not sure if “like a religion” comparisons are appropriate… Lean and religion are different, where belief in Lean is not a matter of faith.
Again, this is probably on the writer of the article for choosing to focus on Toyota or kaizen as a matter of “productivity” — ignoring the equally important Toyota Production System pillar of “built-in quality” (learn more on the Toyota TPS web page). The other pillar of TPS is actually “flow” or “just in time” which is not the same as “productivity.”
This happens a lot in publications like the Wall Street Journal (and it happens too often in the realm of Lean Six Sigma, which too often portrays Lean as “all about” speed or efficiency, ignoring the contributions that TPS / Lean makes to quality).
Back to GE
If GE had been focused on Six Sigma projects, are they now embracing what we might call “small kaizen” and a true continuous improvement culture that engages everybody, everywhere, and every day?
Culp hints at this mindset:
“We're just trying to make progress a little bit every day.”
Culp talks about Lean a lot:
“On a conference call with analysts in January, he said, “When we talk about execution, we talk about daily management.” He used the phrase “daily management” six times and the word “lean” 11 times in a recent presentation at an industry conference.”
Understanding Variation
A surprising topic in the article was a mention of variation in metrics, as one GE aviation leader said:
“I can sit down with Larry and show him 30 metrics and tell him relative to plan, the variance was positive in every one.” But that's not enough.
“Did you do it because there was a one-time event that allowed you to get across the finish line? Did you have a lot of variation and just happened to be on an upswing at the end of the quarter? How do you control it to make sure this performance repeats itself?”
Variance from a target is not the same as variation in a metric. If all 30 metrics are “green” (better than the goal), it might only be green because of some possible “special cause” — are leaders gaming the system or taking temporary (and possibly dysfunctional) measures to make things look good at a moment in time? Or, do they have a consistent system that can produce predictably good results?
The discussion there reminds me a bit of what I cover in my book Measures of Success.
I hope Culp and GE do well, as it is an important company, as Culp said toward the end of the piece. Maybe they can go from “once great” to just “great.”
Please scroll down (or click) to post a comment. Connect with me on LinkedIn.
Let’s work together to build a culture of continuous improvement and psychological safety. If you're a leader looking to create lasting change—not just projects—I help organizations:
- Engage people at all levels in sustainable improvement
- Shift from fear of mistakes to learning from them
- Apply Lean thinking in practical, people-centered ways
Interested in coaching or a keynote talk? Let’s start a conversation.
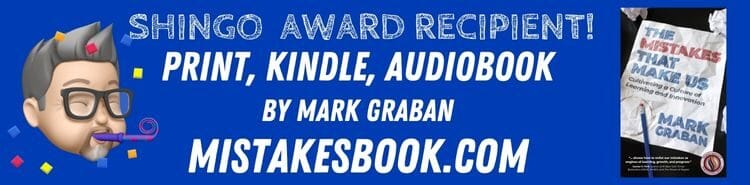
Hat tip to Paul Critchley for pointing me to this WSJ story:
Larry Culp’s GE Plan: a Fix, Not a Reinvention