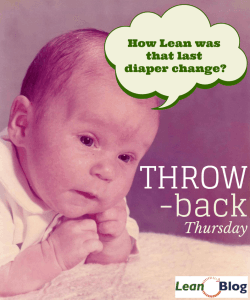
Continuing the “Throwback Thursday” theme for the 10th anniversary of my blog, today's post looks back at and builds upon one of my favorites from 2007. The post is a “GM War Story” from 1995 when I was just starting my career:
“GM Got Gamed (Or, How to Fudge Your Production Numbers)“
There was a bit spike in blog traffic last Friday and Saturday… an “out of control” data point, if you will. The special cause was a Canadian blog linking to that piece for some reason. But, I think the story is still relevant today, especially in healthcare (see the VA scandal about fudging the numbers last year).
In my 2007 post, I wrote about this 4 o'clock meeting where Scott, the production supervisor, would report his fudged numbers. I can elaborate on that daily meeting.
The daily standup was a meeting where the supervisors and support staff from different departments would gather: final assembly and the machining departments that made components, including blocks, rods, crankshafts, and heads. Maintenance and other support leaders and engineers, like myself, were there.
Each department brought a flipchart from their department that showed, by hour, the production goal and actual. There was a space to explain any gap, such as machine downtime, etc.
Listen to Mark read this article (learn more and subscribe via iTunes):
The daily meeting was a practice brought to the plant by one of the internal Lean consultants who had been hired by GM Powertrain headquarters. They came from companies like Nissan and from Toyota suppliers and they had great experience. But, plant management didn't really want the help and they didn't want to learn about Toyota stuff. But, the consultants (who were great mentors and teachers to me) had some mandate to do some “Lean” things (even though we couldn't say the words “Lean” or “Toyota” really, due to politics).
The daily review meeting (which might have been 3 or 3:30 now that I think about it… it was between the day shift and afternoon shift) was meant to break down silos, looking systemically for plant bottlenecks that would affect assembly. It was meant to help prioritize maintenance and other resources. The “reasons why” for not meeting production goals were supposed to prompt discussion and problem solving, not yelling and screaming.
This was one of the first examples I had seen where a Lean method (the flipcharts and the daily stand up meeting) was copied without having the right culture and environment around it. The Lean consultants would sort of shake their heads and tell me that the yelling and screaming wasn't part of their old cultures. But, they didn't really have permission from people like Bob to coach and mentor them. The consultants probably could have tried to talk to Bob privately (and maybe they did) but it probably would have just gotten them ostracized even more than they already were.
Another example of the right tool in the wrong culture is from a 2007 post of mine talking about how a Lean tool, the “andon cord” had been copied by a Ford plant… except for the culture not being there.
In contrast [to Toyota, with 2000 andon pulls a week], workers at Ford's brand-new truck plant in Dearborn, Michigan, pull the cord only twice a week – the legacy of generations of mistrust between shop-floor workers and managers.
We see the same thing happening in healthcare. Copy a tool from aviation (checklists and Crew Resource Management), but don't change the culture to allow these methods to really be useful.
So, in 2015, when we see a Lean tool copied in a hospital that doesn't have a Lean culture, we might see similar dysfunctions. Instead of saying “that Lean tool doesn't work here” and blaming the tool, maybe we should look at our culture. Can we change the culture to, for example, make it OK for people to speak up?
What do you think? Please scroll down (or click) to post a comment. Or please share the post with your thoughts on LinkedIn – and follow me or connect with me there.
Did you like this post? Make sure you don't miss a post or podcast — Subscribe to get notified about posts via email daily or weekly.
Check out my latest book, The Mistakes That Make Us: Cultivating a Culture of Learning and Innovation:
Hi Mark. Thanks for this nice article. We figured out that standup meetings are great but needed improvement (they took a lot of time and de-focussed our colleagues). Because of this we developed a SaaS tool to ʺautomateʺ the daily standup meetings – with just a single email. If you like to take a look: http://www.30secondsmail.com. Best, Revino