If you clicked on my intentionally attention grabbing headline (or what might be a parody of those)… no, Toyota isn't killing their famed and much-copied Andon process.
Toyota is just changing the mechanics of the Andon system – or perhaps improving it… in the spirit of Kaizen, or continuous improvement.
If you'd like more background on Andon cords and that process, see a blog post (and a video) I about my trip to Toyota and Japan (and click here for info on going to Japan with me in November).
In this Automotive News video, they report that Toyota is changing the physical setup of the Andon cord… going from hanging cord to waist-high yellow call buttons that will be within “easy reach of workers” in their stations.
Here's what the old cords look like, from their video (the worker is reaching up to pull a cord, which I've marked with the green arrows):

I'm guessing the intent and the response is the same with a button, compared to a cord. It sounds like they're just changing the physical mechanism for speaking up and flagging a problem.
I'm sure the new buttons will be designed to be easy to press or hit, since Toyota encourages people to call out problems.
When you're in a Toyota plant (including San Antonio, where I live), you see workers pulling the cords fairly frequently. And, when they do, a team leader is there within seconds.
You see this team leader response in the Automotive News video (the team leader is in the hat and the worker, at the car, pulled the cord just a few seconds earlier).
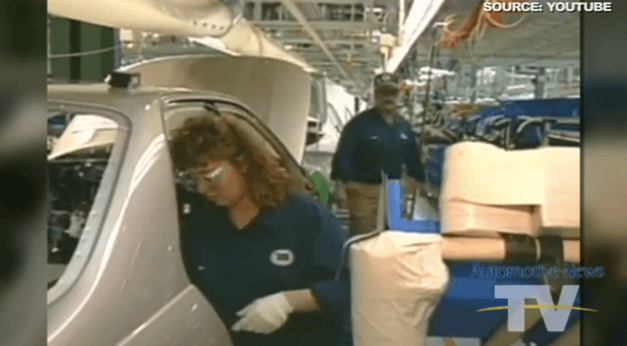
When I've taken healthcare students to the plant, they are impressed with the concept of the andon cord system, including:
- Workers are encouraged to speak up (by pulling the cord) when they even suspect a problem
- Somebody comes to help right away
- The team leader is helping, not yelling
- The line stops if the problem can't be resolved
The healthcare visitors (and I) ask about how wonderful that type of process would be in healthcare. It's not about the cord, it's about the process (ala the Patient Safety Alert systems at places like Virginia Mason Medical Center and in Saskatchewan). The hospitals don't have physical cords hanging over beds and operating tables. Andon is a process and a management system, not a cord.
Back to Toyota… it sounds like they did a small test of change by installing these buttons last year at flagship plant in Toyota City, reports Automotive News. The goals were to remove overhead clutter and to “create a more comfortable and safer work environment.”
Toyota plans on rolling out the new andon cord buttons to other plants in the future.
It's good to see Toyota continually improving and not being stuck in their ways. An Andon cord doesn't have to be a cord.
Here is the full video that Automotive News shows, with Steve St. Angelo and Gary Convis of Toyota (at the time) explaining how this works and, more importantly, the philosophy behind it (the video is no longer available). :-(
That philosophy should be the same with buttons.
Updated: Here is a longer print story from Automotive News with a few more details:
“Toyota cutting the fabled andon cord, symbol of Toyota Way“
Why do they want to avoid the overhead clutter?
Toyota's manufacturing gurus want to cut the clutter over the workspace, creating a sort-of blue sky, for a couple reasons. First, it creates a less oppressive, more comfortable, open-air work environment. Second, there are safety and efficiency benefits because there is less overhead to snag long, cumbersome components or tools.
That makes sense. Another added detail is that the buttons are WIRELESS:
Moreover, the wireless buttons can be added to existing plants, which can reconfigure old lines and design new ones without worrying about where and how to string the old cord.
The buttons are expected to be added to other plants, though the shift may be slow. They are already used at select overseas subsidiary plants in China, Thailand and Indonesia.
It goes to show — it's not the cord or a button that matters… it's the process and the management system that matters.
What do you think? Please scroll down (or click) to post a comment. Or please share the post with your thoughts on LinkedIn – and follow me or connect with me there.
Did you like this post? Make sure you don't miss a post or podcast — Subscribe to get notified about posts via email daily or weekly.
Check out my latest book, The Mistakes That Make Us: Cultivating a Culture of Learning and Innovation:
Toyota still trying to pave the way. Well, they do not have a problem with sharing knowledge.
As part of Saskatchewan’s commitment to eliminating harm to patients and staff, Saskatoon Health Region is developing the provincial model line for our new safety alert/Stop the Line system, based on the learnings from Toyota and Virginia Mason. Since March 2014, staff, physicians, patients, families and visitors at St. Paul’s Hospital can call 1600 day or night to report a safety concern, and based on the nature of the concern, there is a proscribed response by the manager, director or VP.
As CEO, I and our board chair are immediately notified of Level 4 concerns and only the board chair can close the file on Level 4 incidents. Although we have lots of kinks to work out before replicating to other sites within the region and across the province, we are already seeing a more than doubling of reporting and a positive reaction from people reporting, which is helping us develop a safety culture. Like Toyota, we anticipate that our safety system will undergo continuous improvement.
Maura Davies, President and CEO, Saskatoon Health Region
Maura –
Thanks for sharing more details about your efforts to create an effective Patient Safety Alert system that protects patients and supports staff members.
Thanks for your leadership and sharing!
Mark
Mark,
This article really struck a chord with me.
In all seriousness, though, I wonder what is driving the change. It seems that a cord that can be pulled from multiple locations at the point of the problem would be quicker/easier than walking to a button, even if there is some overhead clutter associated with it. Now, if a wireless button was worn on the uniform shirt, that would be a different story.
Always interesting to read your stuff.
Jeff Hajek
Thanks for the comment and the pun, Jeff :-)
I’d like to learn more about what Toyota is doing. What problem does the overhead cord really cause? What does it interfere with, from a practical sense?
I hope it’s not just a matter of somebody “not liking how it looks.” Is this really going to be easier for the workers? Is it really going to be an improvement?
I like your idea of mobile technologies and an individual button… maybe one that’s worn on the worker’s safety helmet / hat… they have to make sure they aren’t wearing anything on their person that could scratch or nick a car that’s going by.
I think the brevity of the Automotive News mention raises more questions than answers. I can’t find anything else in the news about this.
Very nicely put. Yes Toyota try to improve all the time. I wonder if the idea of changing the cord to a button came from one of their staff?
Hi Mark:
I used to work at Ford and since 2009 the andon model copied from Toyota uses a button. Well actually 2 buttons. The first is an andon in white color. When an operator press it, the team leader would come to assist the operator and a red button, to stop the line if the team leader is unable to solve. Engineers used to have pagers! where every time the line stopped a message was automatically sent, meaning that the line had a problem that neither the operator nor the leader was able to solve and we should go quickly to the line to assist and restablish the flow.
Saludos from Mx.
Thanks, Rodrigo. It seems like having a separate red button to stop the line would discourage the line from actually stopping.
My understanding of the Toyota andon system (see the new video that I added at the bottom of the post) is that the line stops unless the team leader (or associate) pulls the cord to re-start it. The default is that the line stops if the problem is not fixed by the end of the job cycle… it doesn’t require a second button or second cord pull to stop.
How often did the line actually stop at the Cord plant? Was there pressure to keep the line running as the main priority?
Mark,
I’m surprised you don’t know about the various pull-boxes Toyota uses. Tsk tsk.
Currently there are 3x types. Fixed (the one you seem to be familiar with), Temp (shuts line down immediately and may or may not be equivalent to an e-stop) and Planned Stop (used to signify the line is down for beyond the line’s control).
Temp stops are used whenever a line must be shutdown preform the fixed stop position (for a number reasons including but not limited to equipment travel restrictions).
As for buttons vs. cords, this isn’t new. Lines were built with pullcords but buttons in older plants have been implemented where its necessary, on raku seats for example.
Eliminating cords altogether is a dumb idea. A cord can be pulled along the length of a team member’s process; a button is in a singular location. A button would increase walk time to push in same instances, though it does cut down on clutter.
Finally, production employees at Toyota are team members, not just workers.
Thanks, Jay. I’m not a Toyota insider, as this post shows.
I mean no disrespect by saying “workers.” Of course, they are whole people (including their brains) and they are team members.
To your comment about eliminating cords being dumb… I hope and presume that Toyota will keep cords where they are the best option?
Removing the cord was inevitable due to the prevalence of bluetooth
Today, I got to tour the Toyota plant in Japan that builds the Prius and Camry models.
They had yellow andon call buttons on the rolling tool cart that’s part of the assembly job zones.
Final assembly had the traditional cords.
It all worked the same way — signal and the lights and chimes go off and a team leader comes almost immediately to see what they need help with.
[…] Updated: Why Toyota is Eliminating the Andon Cord from its Factories (1846) […]
[…] are empowered to stop the line via an “andon” button and a Team Leader will respond in a very short period of […]
[…] I wrote about last year, Toyota is switching from the traditional “andon cord” to yellow push buttons. Here, at this plant, they had buttons that rolled along with the team members on their parts cart. […]
> If you clicked on my intentionally attention grabbing headline (or what might be a parody of those)… no, Toyota isn’t killing their famed and much-copied Andon process.
This is seriously unethical advertising and very uncool. If your intent with this blog is to gather reputation, then let me tell you this title is doing you more harm than good.
Did you also complain to Automotive News for their headline of “Toyota cutting the fabled andon cord, symbol of Toyota Way”?