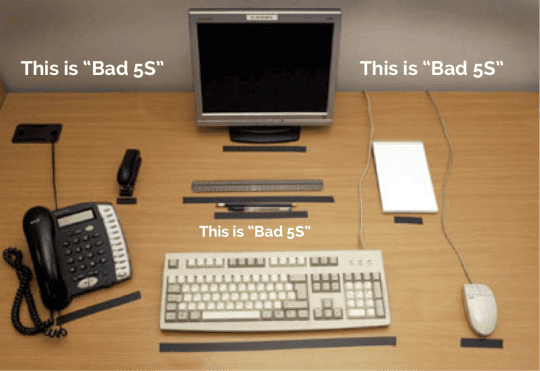
Update – My “Office 5S Gone Wrong” video has gotten more than 200,000 views on YouTube since I created it back in 2010…
You might remember my blog post from 2007 titled “Bad Lean/5S Hits the UK Media.”
It featured a link to a news story from the UK that included the picture at left. An accounting firm was implementing “Office 5S” in a very top-down and, arguably, misguided way, including marking where your keyboard, phone, and computer monitor go. You might also remember my criticism of Kyocera's Office 5S program from 2008.
This is an illustration of directly copying a tool without thinking through why that tool is helpful. Does it help to label where your phone or keyboard goes? Probably not. It's an example of directly copying tools from a factory in a way that might not be appropriate, it's also likely to tick people off in the organization.
You might also have seen the first video animation that I did last week about the waste of getting new recycling bins. I've created a new video that shows what a “bad office 5S” scene might look like… something that's “L.A.M.E.” not Lean.
Here is the new video, with the transcript below it for those without sound or those who can't play YouTube videos at work (but it's much funnier hearing the computer voices, I think). I hope you don't have anything like this going on in your organization. Add comments if you have any stories to share.
Thanks to Dan Markovitz for giving input on this script and its revisions.
Via YouTube:
Scroll down for some translated videos
The Script
Hello Anne, are you excited about our new Office 5S program?
I can hardly contain myself. This is going to be much better than our Office TQM initiative and the Office Six Sigma program, I am sure. Woo hoo, sign me up.
I'm glad you are excited.
Yes, I'm sure you can hear the excitement in my voice. Can I ask a question?
Normally no, but just this once, go ahead.
Who told you to do 5S in the office?
Our consultant did.
And what does the consultant specialize in?
He teaches people how to do 5S.
Maybe you have heard this expression — “When all you have is a hammer, then everything looks like a nail?”
The consultant says you must mark where your hammer goes in your workspace. It makes you more efficient. The best factories do this.
Hello? This is an office. I don't have a hammer at my desk.
See, you would know the hammer is missing if you had a tape outline showing where the hammer and your other tools go.
No no no. But I am a marketing specialist. I create marketing proposals. I do not have a hammer.
Then you can put tape around your computer, your monitor, your phone, your stapler, your coffee cup, your purse, your mouse, the tape, the staple remover, that book, and those paper clips.
Why would I have to put tape around my monitor?
So it does not get lost. We will always know where the monitor is. You will not waste time looking for it. Our office will be more efficient.
Has anyone in our office ever have a monitor go missing?
I don't know. You must do this. It is on my goals and objectives to implement 5S.
So I will open my desk drawer and put tape around each of my pens and pencils
Ah. The consultant says there will be a strict limit of two pens per desk. Any more than two pens is waste. We must not waste money. We must be lean.
Do I have to put tape around my family photos?
I'm glad you asked. You are no longer allowed to personalize your workspace. We must be lean.
How is this helping me do a better job?
The consultant says it will.
Why?
He was very adamant about it.
Why?
He yelled and screamed a lot in Japanese.
How do you know he is right?
I'm sure he is right, we paid him a lot of money.
Look — It takes us 6 weeks to get a new proposal out to a client. Maybe we should work on fixing that, you know, reducing the cycle time. Maybe we will get more clients. We can grow the business.
We must do 5S.
Do you even know What the five Ss are?
The five Ss are 5 words that start with S. They are: Straighten, Salami, Stopwatch, Sasquatch, and Salmonella.
That doesn't sound right.
The words are all Japanese. We must learn them. We are a learning organization. Don't you want to learn?
I still don't understand how this will help.
The consultant said this was very important, we will do the 5 esses or maybe even 6.
Will this make the organization more effective?
Effectiveness is not one of the 5Ss. That starts with the letter E. So it is not important right now.
But isn't the gaol of 5S to improve effectiveness?
Our lean consultant did not explain that to me. I only know that a successful five ess program is the first step. It is always the first step. Always.
Yikes. I need a cup of coffee.
You can find the coffee in the new 5S approved location. But I am afraid that you can no longer drink the coffee at your desk. That would be a 5S violation.
Really? A 5S violation? Why?
You ask why a lot. I will sign you up for the five whys lean training.
But this is absurd.
You must follow the lean rules. Now I must go and fill out my 5S audit sheet. Goodbye.
Concluding Thoughts:
When 5S becomes a checklist exercise–or worse, a mandate imposed without context or clarity–it stops being Lean and starts being L.A.M.E. What's missing is not more tape or stricter audits, but a better understanding of purpose and people.
The real opportunity with Lean tools like 5S is to make work easier, more effective, and more engaging–not to stifle people with arbitrary rules. Let's not forget: the “Respect for People” pillar in the Toyota Production System isn't optional.
If you're rolling out 5S in an office, start with listening. Ask: What problems are we trying to solve? How can we involve the people who do the work? And how can we ensure we're not just copying tools, but actually improving processes in a way that makes sense?
Otherwise, we risk turning Lean into a parody of itself–one that gets more laughs than results.
Let's aim for better.
Spanish Video:
French Video:
German Video:
Please scroll down (or click) to post a comment. Connect with me on LinkedIn.
Let’s build a culture of continuous improvement and psychological safety—together. If you're a leader aiming for lasting change (not just more projects), I help organizations:
- Engage people at all levels in sustainable improvement
- Shift from fear of mistakes to learning from them
- Apply Lean thinking in practical, people-centered ways
Interested in coaching or a keynote talk? Let’s talk.
Join me for a Lean Healthcare Accelerator Trip to Japan! Learn More
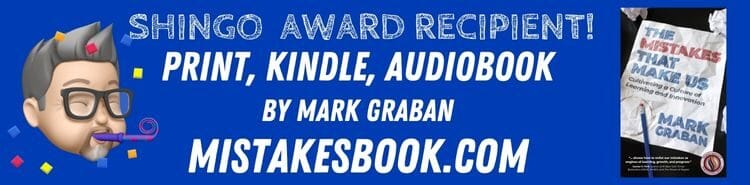
Don’t move your mouse, it won’t be in the right spot anymore!!!
I am always losing my monitor. Thank goodness for 5S gone awry to solve this problem for me.
What we need is 5S for kids – I keep misplacing mine.
My 5S tip is to drink bottled water in the office. That way, when you tip over the drink, the piles of paper don’t get soaked and you don’t have to waste time sorting them right away.
and with perfect aim, the expert marksman launched his arrow 5 feet wide of the target. Why? Because he was frightfully nearsighted.
All the technique in the world won’t help you if you can’t focus on what is most important.
Thanks for the post, it is a good lesson to learn. When first introduced to lean, I was told to tape off everything in my office, too. Like many, I was taught that beginning with 5S would indoctrinate everyone into Lean culture. Unfortunately, the 5S initiative flopped miserably and the same difficult, inefficient work continued on forever.
An unfortunate truth: Energy spent on pointless 5S is a waste all by itself.
It looks like these guys would disagree with you!
http://2leanprincipals.com/2010/08/10/practical-uses-of-fmds-in-the-office/
Excellent! Why wasn’t he hearing her? Why weren’t sensible questions embraced??
How do we make being sensible “sexy”? I have worked with several organizations and I am convinced that one of the major road-blocks to organizational leaders embracing lean, to improving processes through straight-forward, data-driven decision making, is poor PR. These front-line generated ideas are not ‘revolutionary’ enough, the basic tenets of continuous improvement are not ‘evolutionary’ enough, the branding is ‘stale’… making it difficult for good ideas to be heard amidst all of the noise.
Does anybody have any ideas for rebranding good sense?
Great questions, Shana. Too many organizations try to be “revolutionary” when they don’t first have the basics covered, the “blocking and tacking” if you will. There’s no foundation upon which to be evolutionary, yet alone revolutionary. I don’t know what you can do with some of the deeply engrained societal norms that your time is better spent on fun, exciting, revolutionary, sexy stuff.
He screamed alot Japanese….Sasquatch and Salmonella…fabulous…I am in tears!!
Shana:
I love it… “rebranding good sense”!
Talking over lean principles and applications with an executive level acquaintance, he has said more than once “…well, this is really just common sense and good business practice.” As if that’s a a reason to blow it off! The “been-there-done-that” reason for not improving.
Lean IS the brand, or as close as we’re likely to come. Unfortunately its an unprotected brand so L.A.M.E. consultants and office managers like the ones in Mark’s video get to dilute and damage it. It’s up to us to keep selling it (and teaching it!)
I love the 5S dialogue. It is exactly how I felt when they did a 5S in my area which is an Orthopedic Call Center back by the doctors’ offices where we NEVER see a patient ever. it is a secure area and no one is allowed back her by staff. So when we were told only a certain number of personal items, nothing under our desks (we are not provided enough drawer space to put purses, etc., away) I couldn’t understand how this was going to increase our ‘patients’ expereiences’ here at PNC. The dialogue was respectful with just the right touch of humor, but it hit the nail on the head. Thank you.
That’s a real shame to hear about that.
Here is a very nice and related blog post from Patrick Anderson on this topic of personal items and motivation:
http://leaninalaska.wordpress.com/2010/09/10/motivation-in-the-workplace/
The number of personal items on someone’s desk is not anywhere near the top 1000 pressing important issues in a given health system, I’d argue and I think you’d agree, Moey.
This kind of approach would not work in the organization I currently work for. First, the majority of staff would be frozen in place at the thought of all the bureaucracy they would have to go throught to order a label maker.
More importantly, the scenario would never happen because it assumes a manager would actually stop by my desk.
PTW
Oh Mark, just what I needed on a Friday afternoon. Thanks for that. I only hope I never come across as that kind of consultant!
Jeff Hajek has a blog post including a misguided labeling of a stapler:
http://www.velaction.com/dont-go-crazy-with-your-5s/
Hi Mark
This video is great!!!
Can I translate it to Portuguese? I ´d love to show it back here in Brazil. If I can, can you post a transcription of it? Would be easier to translate captions …
Sure, you can translate it. There is a transcript below the video here on this page. Email me the translation and I’ll make a new version of the video for you to share (mark at leanblog.org)
Ha, here’s a differing opinion I found:
http://www.leanoffices.com/lo_page.asp?PageID=8774
“Using electrical tape (available in several colors) create an outline on your desk for your stapler, 3-hold punch, phone, laptop, and other desk accessories. Instantly, you’ll be able to see if something is missing or out of order.”
So your video isn’t that much of a parody, it’s reality for some, I guess.
[…] Added Note: Interesting enough, I wrote this last Thursday before Mark Graban published his post on 5S. This is great timing. Here is a link to his post and why office 5S can go so wrong. […]
[…] Both Lean implementations and other workplace culture changes suffer from the same dilemma: How to be more like highly successful companies, without simply trying to borrow all of their tools? […]
[…] some of my points, I think, about the overly strict and overly restrictive instances of “bad office 5S” (like this joke video I made). Here is the subtitle for the […]
[…] Situations where “Lean” is used to tell people to tell office workers to take memorabilia off of their desks (as was done at HRMC) are clearly L.A.M.E. This is the sort of thing I’ve criticized and even mocked in a video. […]
Oh god! I am living this hell right now. Apparently I am resistant to change, because I like to have the telephone beneath the list of telephone numbers on the pinboard, yet somebody decided to put tape around it elsewhere. The highlighter pen I use everyday keeps getting put into a drawer, yet an index card system that I have not used once in the last year gets pride of place with yellow tape around it.
It might work for the INTJ types, but it is driving me nuts.
MT-
My sympathies!
This isn’t about personality type (I hope, speaking as an INTJ) but about common sense. We have recently brought lean into the office (after years on the shop floor) and there was concern during initial training about “people 5S-ing my desk”. We had to reassure folks that they would be in charge of their work space. I shared this blog post so they could enjoy (and be armed with) the humor.
Counterpoint came when one woman, whose workstation must always be staffed, spoke up to say how important 5S at HER workstation was to her (she’d worked in the plant before coming to the office and had done this on her own). Because other people must fill in when she is on break or out for the day, having good visual standards for set up and disposition of materials makes things smoother for everyone – both the fill-in people and the regular when she returns.
So, if you’re on your own, why should I care where your stapler is? On the other hand, standardizing shared resources (and hand-off points, too, for that matter) can improve things.
That’s good sense, I think, especially when the people doing the work set it up. What do you think?
I agree with standardisation (see what I did there? – I followed a perfectly correct standard, but some would mark it wrong) I also think that the moron with the roll of tape could at least consult with the other desk users. The desk is no longer a shared space, it is a personalised (I did it again) space for the tape moron, that the rest of us are now permitted to share. I follow tape guy after 2 shifts he follows me after only one, so wouldn’t it be more efficient to tape the desk layout up the way I like it?
I’d love to post up a picture, our company has spent $300k on a lean manufacturing course for supervisors, that we have been forced to attend during our own time, with an additional 600 hours worth of unpaid assignment time (It is a post-grad diploma). We are near the end of the course, and this is the first tangible benefit I have seen implemented in our facility.
We are going to become a world class kindergarten, instead of a world class manufacturing operation. I guess this lean consulting is only a racket if you aren’t in it.
That sounds like a huge waste of money and an embarrassment for “lean.” It sounds more like “L.A.M.E.” than what lean is supposed to be.
Is your company working on anything (that you can see) that would make things better for customers or safer for the employees??
As part of the diploma we are each to do a continuous improvement/loss and waste project (600 hours). We have almost finished the coursework content, the senior management seem to do everything according to the 7 diseases (eg why are we all there in our own time? – Because the organisation is run on fear).
It is we who are meant to lead/implement these improvement initiatives, yet my colleague has chosen to tape up the desk (not, I hope as part of his project, although when I had re-arranged things to suit myself, he did mention photos & audits in order to “sustain” the new paradigm.
I really want to institute meaningful improvements, and not get bogged down in the L.A.M.E. There is a possibility that the tape meister has done this in order to deliberately upset the rest of the team, or as a joke, in which case I see it as even more wasteful than if he was earnest.
After we had attended 3 or so classes, we invited the group facility managers along to explain to us why we were there, and what they hoped to achieve from us completing the course. A direct quote from one of them to my colleague: “If you don’t like it, then why don’t you bugger off?”. That will remain in memory forever.
Unfortunately we are in a small rural township and the the facility pays significantly more than the national median. The coping mechanism of choice for the majority of employees is, unfortunately, disengagement.
We were told this course was taylored (no pun intended) to our sites, yet we are a continuous processor, and every case study we have looked at has been either service, or assembly related, so on a side note, can you suggest any good lean work/material that has been done in continuous process industries?
The good thing about the course facilitator/consultant is that he is at least honest enough to tell us all that he is a personal friend of our CEO.
On my next shift rotation, if the tape is still there, I intend to give it a kaizen blitz, all of course in the name of continuous improvement!
Thanks for your blog too Mark, I found it as part of a google search to see if there really were people stupid enough to tape desks up like this. Everything I have read here so far seems well aligned to my thoughts on how lean should be.
My dad was a self-employed builder of custom kitchen cabinetry and in his own way worked desperately hard to increase his productivity/efficency. He never ever advertised and got all business via word of mouth and repeat custom. Three years after retiring he still gets regular phone calls at home from customers offering a premium in order for him to build them a kitchen. Most things I have learned about lean, I can think of an example that dad had practiced, but he would be shocked if you gave it a name. He just called it working smarter, and keeping the customer satisfied.
Of course part of the reason customers still chase him is because nobody can believe he retired as early as he did, thanks to satisfied customers who were happy to pay for the value they received.
I remember one day a little old lady turned up to pay her final account for a new kitchen which ran into thousands, she rounded the amount up to the nearest hundred,hugged him, and gave him a bottle of single malt scotch with a card that said “Thank you for restoring my faith in tradesmen.” She was crying, he was starting to tear up, and he had made a healthy profit on the job already and later admitted to feeling a little guilty.
To me, that is what lean should be about, not tape on desks.
Sorry to ramble, thanks for ‘listening’.
Ok, soo the tape is gone. Not removed by me, but another colleague, with whom I had not discussed the issue.
The sad thing is that not only has the tape ended up in the trash, so has a large part of the drive for implementing lean practices, and the reputation of lean in general.
I can hear it now:
“Oh yes we tried lean manufacturing and management made the supervisors put tape on their desk. It only lasted a week, and if the supervisors won’t do it, I can’t see it taking hold on the operating floor.”
Several years ago the 5whys were abandoned because of poor implementation and are still subjected to general ridicule. I can imgaine the response when I tell the same people who ridicule 5why that I want to implement 5s
MP, is your company just trying one lean method at a time??? Or are they trying at all to have an integrated lean effort where they understand how the different parts fit together into a management system?
Bravo, both for the script and the humility required to make it. I was cracking up the whole time. A simple clip like this speaks volumes more than serious tomes about the impact of what you refer to as LAME (and what Bob Emiliani calls FAKE Lean).
The last place I worked for took 5s too far. I was on the manufacturing floor, but I saw tape around computer components and for pen cans ect… Even on the production floor they took it too far where it actually decreased efficiency. They started taking away our tables to inprove space efficancy and we now had to search around the building just to find a table to fill out our paperwork. It actually slowed down the manufacturing process.
Matt – Thanks for your comment. That’s sad to hear that somebody’s idea of “efficiency” made it more difficult for people to do their work. That often happens when experts or “the boss” decides what to do. That illustrated so clearly why we need to engage everybody in improving their own process and take everybody’s input equally, not just a top-down decision.
This is an amazing thread and I did enjoy the script that inspired it. I was involved in implementing 5S in my office (part of the Department for Work and Pensions). I had to overcome immense amounts of cynicism and was not helped by the fact that the Tax Office had already done ‘the tape thing’ and the active/inactive banana! Fortunately we’re more enlightened at the DWP and took the pragmatic approach of integrating 5S with other lean working techniques. During 5S training we used traditional examples like the hammer on the pegboard but we interspersed more relevant examples to show staff how 5S might work in the office. We also emphasised the benefits of visual management and decluttering the workspace and we empowered teams to define their own 5S standards rather than imposing them. Furthermore, I was able to debunk the myth that personal items were not allowed. One member of staff had a desk that was festooned with a myriad of ornaments, cosmetics and other twiddly bits. Despite this none of it interfered with the flow of work across the desk. It was also crystal clear where everything belonged. I photographed her desk featuring it in a captioned document showing how you could follow 5S principles without losing the humanity in your environment. We’re not perfect and sustaining 5S is an ongoing struggle but at least the staff know why we’re doing it and what the benefits are.
Jerry – thanks for sharing your story of how it can be done in a much better, more humanistic, and more productive manner!
Hi Mark,
Thanks for your video & thanks to ALL the who commented. I have move to Facilitation of TPS/Lean in my company (Retail Outlets, Service, Office & Logistics) since Feb 2010. Me & My Team mates became responsible in rolling out 5S in our company in UAE. Peoples reaction to the 5S practise is always Defensive (usually eveybody is comfortable in his working space & believe the standard they are following is serving the purpose for them!)
Similar to your video dialogue happens in our case too! Although unlike others cases we do not instigate the placement of pens & stappler rather we leave it to the people to choose the placing where it is most convinient for them.
Looking at 5S & the benefits we can see that it touchs people behaviour & drives them into thinking on how to streamline & improve their work by doing 5S in their desktops (Files), Stock Rooms … and so on.
We have 5S champions in every location as an middle man between the Facilitators & the staff.
TPS is very intersting!!
[…] get into it a bit deeper into this Mark Graban posted the video with a transcript available on his blog post. If you want to learn more about 5s his leanblog is worth a […]
Excellent video, and seeing my GPS lady land more roles was very encouraging too.
She also plays the role of Siri in our iPhones :-)
My partner phoned me whilst I was watching this video. I was crying. She thought something had gone terribly wrong. I could not speak.
What a fantastic video! Fantastic!
Thanks, Andie!
[…] artifacts, without critical thinking, leads to ridiculous situations like this video I made illustrates. Seeing an artifact might be a “spurious observation” based on a superficial walk […]
Hi
I can’t use youtube in the office (it is blocked) how can i view the video in another format. I saw it at home and it is a really excellent way to show people that 5s shouldn’t always be used to the letter within offices. In my line of work we minimise the 5s methodology to work for the customer. Usually concentrating on paper filing and electronic filing.
can you help?
Sarah – you can also try watching it here if the site Xtranormal.com isn’t also blocked:
LINK
Is Vimeo.com blocked by your organization? I could upload it there.
It’s really annoying to see how many companies and hospitals block video sites or social media sites. If people are wasting time, that’s a process problem for management to address… because if you block it on computers, they will just use their smart phone…
Thanks for commenting on the video, glad you liked it.
[…] You might also want to check out my “Office 5S Gone Wrong” post and video. […]
[…] A Video Showing Office 5S Gone Wrong (4,687) […]
[…] a reminder, it’s not “Lean” to just put tape around everything — it’s got to be preventing problems or reducing waste (or helping people do their jobs […]
[…] frustrating workplace, and if they’re being engaged in improvement. If Lean is about, ahem, putting tape around everything on their desk, then people won’t embrace […]