A few weeks back, the British media was having a field day with reports of and complaints about what sounds like a horribly misguided “office lean” effort at a British government office. Read more about it.
The picture below is from one newspaper article (with my added labels). It shows a desk where every item's location is marked with black tape. Read more (in a later post) about why this image is labeled as “Bad 5S.”
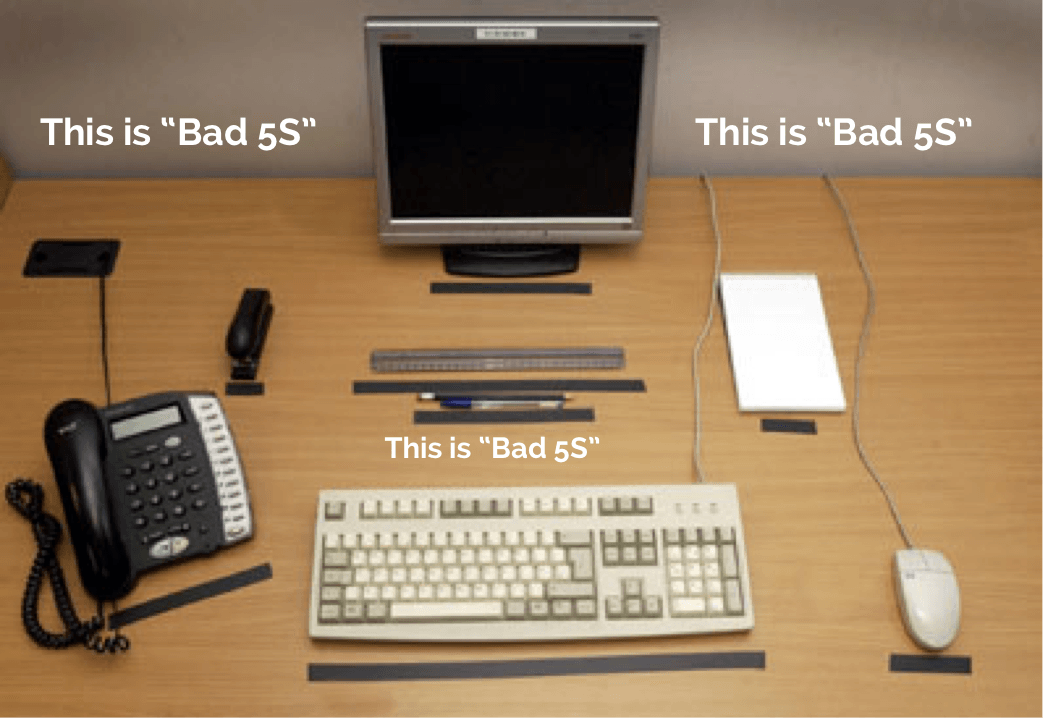
The article explains:
The exercise, which involves markers for items including computer keyboards, telephones and stationery, is designed to improve efficiency by making desks neater.
However, one worker last night described the system, being implemented by logistics company Unipart, as “demeaning”.
This is a classic example of bad 5S and bad lean efforts. Stuff like this is all too common and it really gives lean a bad name. As we've talked about in other posts, 5S is about reducing waste and making abnormal situations apparent.
What waste is prevented by marking where the phone goes? None, probably. Is there anything to be gained by seeing that the phone is two inches too far forward? No, not really. Seems like this 5S effort isn't doing much, but antagonizing folks.
This article calls it “madness” in the headline and adds:
According to the Daily Telegraph , the programme has been so far reaching that one member of staff was asked whether a banana was ‘active' or ‘inactive', in other words whether it was going to be eaten immediately, which was acceptable, or whether it was for later, which would mean the fruit would have to be cleared from the desk.
An HMRC spokeswoman said the programme, which was devised by consultants Unipart to improve performance, would help ensure that office space was efficiently used and would also support working relationships.
The consultants had good intentions. 5S *can* be a powerful method in a lean company. But, marking the location of items is just one aspect of 5S and 5S/lean have to be done the right way. The article also said:
“… employees were allowed to move items into zones that suited them best.”
If the consultants asked each accountant where they wanted their items, that might have been one positive sign — showing the slightest bit of respect for people in that sense, perhaps. So why did employees find it degrading? Probably because the consultants didn't explain “why,” as Toyota would tend to do.
What if two employees who shared a desk (as happens in these British offices) disagreed with where items went? They wouldn't pick up and move the tape constantly would they?
Oh, they do… and it gets worse.
I could go on and on about how that effort gives “Lean” a bad name. If you're just antagonizing people by putting tape around stuff, please stop. Trying using Lean methods to solve real business problems (such as slow cycle time, defects, cost, or employee safety).
Lean, done right, won't feel “demeaning” to people.
Please scroll down (or click) to post a comment. Connect with me on LinkedIn.
Let’s work together to build a culture of continuous improvement and psychological safety. If you're a leader looking to create lasting change—not just projects—I help organizations:
- Engage people at all levels in sustainable improvement
- Shift from fear of mistakes to learning from them
- Apply Lean thinking in practical, people-centered ways
Interested in coaching or a keynote talk? Let’s start a conversation.
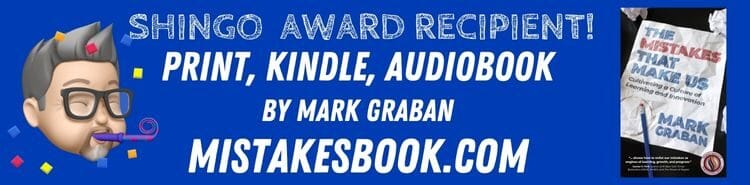
Yes these “LEAN” efforts seem quite a bit extreme and a certainly demeaning. Isn’t there a point where LEAN methods can make participants or recipents feel bashed and belittled. Perhaps they were trained in a very ineffecient process and strictly instructed to follow that way. They perform this task for a few years taking “ownership” of the faulty activities. Then someone comes along and tells them “it’s all wrong.” (Hopefully, they would be more tactful and gracious.) Certainly people will feel “demeaned” but they could be built up and brought to better work. Are there any good examples of this balancing act?
You’re right, CW, that’s the “soft side” of implementing lean and change management, in general.
You have to show respect for people in how you work with them. You have to be understanding that people won’t want to give up that sense of ownership for the old way of doing things.
One other point I’d make is that 5S is not about being “anal retentive” or a neat freak. 5S, as Jamie Flinchbaugh talks about a lot here, is done to eliminate waste and to make problems visible. That’s why I don’t put tape around the stapler on my desk at home. It’s only me and my wife and we are pretty good about putting the stapler back. There’s no “wasted time” spent looking for the stapler.
I really question when 5S is the first or only “lean” activity that’s done. Is that really the high-impact place to spend expensive consultant time? You really need to be addressing core issues of flow, cycle time, quality, and other customer issues.
I’d like to hear what “efficiency” benefits were really achieved with that UK project.
Straight bananas and bent cucumbers
There’s nothing the media likes better than “the world’s gone mad” stories. There’s also another journalistic truism about never letting the facts get in the way of a good story.
The taped up civil servants’ desks is a classic example of the genre. By reducing to absurdity, the media missed the point of lean working.
And just to set the record straight.Unipart has never advocated nor ever would putting tape on desks. Yes we use 5S as we introduce HMRC to many other lean tools from six sigma (yes it does work in office environments)to value stream mapping.
We’ve been on the lean journey for more than 20 years now. See our website at http://www.unipart.co.uk.
But don’t take our word for it, see what an independent academic thinks of us at the renowned Cranfield University in the UK.http://www.som.cranfield.ac.uk/som/research/centres/cbp/downloads/New%20Lean%20Thinking.pdf
One does always hope that bloggers writing about their specialism would actually go back to the source and check facts before repeating them.
The black tape story was widely disseminated but was always simply the same unchecked story endlessly recycled.
“Marktim” – please feel free to email me using the link in the left hand column if you’d like to have some discussion about setting the record straight.
The bloggers are supposed to have higher standards than all of your British newspapers??
A couple of clarifications on the Cranfield reference.
1) The references refers to Uniparts operational division, not its consultancy arm. It makes not comment on how the consultancy is delivered, how they engage nor whether any of the work they have done is sustainable.
2) To suggest that one could take the reference and apply it to their consultancy work would mean that all the people that carry out the consultancy work have been in Uniparts operations, otherwise how would they have such a great understanding of the Unipart way of working. This would mean Unipart do not recruit directly in to their consultancy. I dont think this is the case.
I think the bigger issue here however is not whether they use the tape or not. The issue is that consultancies such as Unipart, PWC, McKinsey go in to organisations promising the world without understanding the business (I guarantee they have no real understanding of how health care operates) or a willingness to take the time to. As a result when pressed to do something they find they are unable and they revert to type and say “lets do 5S”.
Nowhere has this been articulated better than in John Seddons article for the HSJ “watch out for toolheads”. He points out the absurdity of some of the practices with tools like 5S and peoples reliance on them.
A lot of the stuff described in those articles sounds like “rearranging deck chairs on the Titanic.”
Are you kidding me that marking where someone’s pens go is the key to making happy customers and improving office performance? What a load of crap. The media might have jumped all over that, but it sounds like it was deserved mockery.
These “companies” have come in to public sector businesses and made enormous sums of money and delivered, by and large, nothing of tangible or sustainable value.
As someone that has been in to 30-40 plus organisations over the last 2 years in the wake of these companies, the organisations are now completely gun shy, dont believe there is any value in lean or any other methodology because all that happens is the consultants come in, realise its not the same as getting a sparkplug from london to manchester and that its far to complicated to get their heads round in a short space of time so they rearrange the post its.
Mad stuff like this has not helped at all those of us that are interested in introducing lean ideas and principles in HMRC. Although the teams themselves we speak to are receptive to the ideas a lot of bad press has been generated by Unipart and McKinsey’s approach and it can be an uphill struggle.
I think we will get there in the end though.
I disagree, I have worked across the DOH, MOD, NHS and with other public sector organisations and the to be honest I have had exposure to both McKinsey and Unipart and I am more impressed with one than the other.
I’ve spent a lot of time in the two trusts where McKinsey have been the longest delivering work and the teams are good and things are changing.
I’ve also been in a lot of trust where they have not been where results are equally if not more impressive.
The problem with consultancies in general is that by and large they do not deliver, they are willing to take the cash but when it fails they say that its because the organisation never did what they said and when it works they say the organisation could never have done it without them, they accept no responsibity for their actions nor do they have any sort of commitment to the organisations that they work with other than to extend the relationship for as long as possible and to take as much money as they can.
I love marktim’s comment. What he has tried to do is call the veracity of the story into question without saying whether it’s correct or not, despite the fact that he was clearly in a position to confirm this.
“One does always hope that bloggers writing about their specialism would actually go back to the source and check facts before repeating them.
The black tape story was widely disseminated but was always simply the same unchecked story endlessly recycled.”
Indeed, possibly. The blogger probably didn’t go into the office. He probably didn’t see the desk with his own eyes. He probably didn’t ask people in the office if it was true. The story may be unchecked, and it’s certainly been recycled and widely disseminated.
But what the story also is, tragically, is very very true.
So why is marktim trying to discredit a story when he either knows it to be true, or is in a position to find out that it is?
Well…looking at the picture, I think we can work out.
Wouldn’t it be nice if consultants kept their head screwed on and didn’t run around causing idiotic chaos that their colleagues have to try and attempt to distance themselves from using spurious means and intentional half truths?
For the record, even though I invited “marktim” to contact me via email, I never heard from him. If he’d like to “clarify” the record, I’d be willing to talk.
“You have to show respect for people in how you work with them. You have to be understanding that people won’t want to give up that sense of ownership for the old way of doing things.”
Sadly the HMRC project didn’t. As a … whatever you call a victi.. I mean, ehm, ?subject? of it I can say it felt like it was setting about doing exactly the opposite, and in a very abrasive way. One thing it particularly didn’t identify was the parts of the old way that worked as opposed to the parts of the old way that didn’t work. And after the baby was thrown out with the bath water they started to try and beat it into ‘buy in’ submission.
“One other point I’d make is that 5S is not about being “anal retentive” or a neat freak. 5S, as Jamie Flinchbaugh talks about a lot here, is done to eliminate waste and to make problems visible.”
Problems are certainly visible after the HMRC project. I believe the following are a few examples of what you would call problems.
– industrial action, one of which was at a trial office and purely the result of the trial http://news.bbc.co.uk/1/hi/scotland/4904958.stm
– The organisation being ridiculed and brought into disrepute http://news.bbc.co.uk/1/hi/england/tyne/6230629.stm and read about the active banana, or click the link for a “The Office” style mock report.
– staff turnover (people like me that finally had enough and jumped ship, and I was far from the only one.)
I daresay that probably isn’t what’s meant by making problems more visible though.
“That’s why I don’t put tape around the stapler on my desk at home. It’s only me and my wife and we are pretty good about putting the stapler back. There’s no “wasted time” spent looking for the stapler.”
And how much wasted time could there be if you put the in the wrong place on top of your almost empty desk anyway?
But there could be wasted time if you ended up taking the things you use to do your job well in and out the drawer all the time because you aren’t allowed to have them on your desk. Different things work well for different people. Some people are comfortable swapping between PC applications to access electronic references stored in Excel. And some people find it easier to glance down towards this year’s version of the rates and allowances card that they’ve used for the last twenty years and then back up again. Neither is a ‘bad’ way of working. Everyone is different and I think most people with basic grasps of sense realise this and allow for it.
“I really question when 5S is the first or only “lean” activity that’s done. Is that really the high-impact place to spend expensive consultant time? You really need to be addressing core issues of flow, cycle time, quality, and other customer issues.”
The problem with the HMRC project was that it targeted the wrong part of the process. It was correctly identified that there was a system that was inefficient. It also correctly identified that they needed to be seen to be doing something about it.
However for whatever reason, perhaps because they felt weren’t in a position to admit the problems with their fundamentally flawed computer system, or because they were less in a position to do anything about them, they targeted the staff instead. (Or should I say, the multitude of fundamentally flawed computer systemS? Yes, I should).
Yes, staff might have been a bit inefficient. I’d like to say we weren’t and that we worked just as hard and efficiently as the best out there, but maybe we didn’t. However that’s got to be less than a tenth of the problem if you butchered a system to make every work process impossibly inefficient.
Take the example of a simple task like changing an address and sending a computer generated tax code notice. In the bad old days this could be done in about… oh… 30 seconds if you were a fast on the old keyboard. Process: Change the address and send out the notice.
Introduce a new system to hold personal that is part of the Tax Credits fiasco, as a result of which you have to change the address on different computer system (one that can’t be controlled with the keyboard only and where you have to swap between keyboard and mouse several times to change the address). Have that system update the old one that still issued the coding notices overnight when it feels like it, so that you have to put the case aside, check it again the next day, and issue the notice IF the address was changed (or else put it aside and check it another day.)
Then wonder why less work gets done than before and what to do about it. The answer’s pretty obvious isn’t it? They don’t need to lean their computers. It’s clearly actually because they have bananas and personal photos on their desk, and because they don’t have tape to tell them where their keyboard should be.
“I’d like to hear what “efficiency” benefits were really achieved with that UK project.”
I had the benefit of being able to be told that the trial had been a massive success before it actually had started, and I think that set the tone for this exercise; nobody could admit failure.
HMRC need to be seen to be trying to do something about a horrible mess failures of successive new computer systems to operate effectively had got them into. The consultants need to be able to justify their fee, and in turn HMRC needed to be able to justify paying them it. Whether or not it transpired a claimed success would bring happiness all round, except perhaps for the staff and customers left with the mess.
In fact the actual result was that the project could never solve the problem, because it wasn’t trying to address that issue that was the problem. NICO may now be ‘lean’, but it’s computer system still doesn’t work. Therefore things like http://news.bbc.co.uk/1/hi/programmes/moneybox/6184433.stm are still happening and will happen again in the future too.
In terms of improving the aspect of the system it attempted to address, the project has also failed. It was either an abjectly flawed attempt to introduce the principles in question that became derailed in absurdity, or simply not an example of the application of the principles that it claimed it was. I know nothing about management theory so I don’t know which, but I suspect it was the latter.
I do however thankfully know about tax, which set me in good stead for when I left the shipwreck the project left behind. I’m as happy in my new world as I was in the old world of the HMRC before they started doing things that were and are just plain silly. And I get my work done even though I have three pictures round my desk and nothing to tell me where the keyboard goes.
Some interesting comments here. I too can comment from within HMRC as a (relatively) senior manager. And yes the whole way this has been rolled out from the start has been flawed. Of course there are some positive points around Lean. And yes of course staff could be more efficient. Howver we started with the basic principle that Lean WOULD increase productivity by 30 -35%. We then proceeded to pay consultants around £7.5 million to rove it would.
Unfortunatelt Unipart amongst others failed to understand the technical nature of the work involved. They have constantly dumbed down what is involved relate much of the work to “processing”. This implies it is simply data capture. It is not. It involves volumes of complicated legislation and years of training. They fail to understand we acnnot “flip” (change) teams from one process to another and achieve similar productivity overnight. We are not talking about collecting motor parts for delivery here.
Unipart’s failure has been backed up by HMRC’s senior managements dogma and failure to take the good parts from Lean and make it fit in HMRC. Instaed we are hellbent on fitting HMRC into a rigid Lean structure whatever the costs.
Unfortunately panic is now starting to set in. We are not achieving anything like a 35% hike in performance. In fact in my office work on hand is the worst I have known in many years.
There has been an enormous investment which is not paying off and inevitably there is now strong downward pressure on managers and staff to increase productivity (and maintain quality) by whatever means.
A success? I think not Unipart. Before you tell others how to restructure their business, try to undertand it yourselves!
Well, it’s more than a year since the last comment and in HMRC we are still flogging the LEAN horse.
Not to say some of it doesn’t work, but the HMRC hierarchy still appears to have missed the point.
Now why am I posting at this time?
Well I’m heading to a meeting in the near future and one of the top brass is seeking assurances that all is quiet on the front – I expect – I’m looking for things to see if our LEAN is on the right track…..I mean do I really have to fill in 2 tick sheets to confirm my white board has tight nuts and I’ve used the right colour pens???
That seems a bit obsessive, checking the whiteboard for tight nuts.
Now, missing pens (a particular color or not having any) could delay a meeting or conversation. I could see having a visual display system so you can see if they’re missing (and clear responsibility in the support staff for who is supposed to replace missing markers).
But is the core value added process of the business being impacted with the LEAN efforts?? That’s really what matters, right?
Oh and one other thought to the last anonymous… that sounds like a bad sign if leadership wants “all quiet” rather than open honest discussion about how LEAN is working or not working.
Please keep us posted about how your meeting goes.
[…] a way, it could also look like “Bad 5S” (as in this case from a UK accountancy) if the tape square had been labeled “Commander in […]
[…] me, this is another way to view 5S for knowledge workers. It’s not about putting a tape outline around your stapler and mouse — probably you can find the damn things without the tape, and if you can’t, you […]
[…] things have happened in manufacturing companies, accounting firms, and sometimes hospitals. It’s unfortunate when these things happen and it reflects badly on […]
[…] would be efforts to speed up work (rather than reducing waste) so that quality suffers. Forcing workers to put tape around their keyboard in a misguided 5S effort is L.A.M.E., not […]
[…] 10, 2010 · 34 comments You might remember my blog post from 2007 titled “Bad Lean/5S Hits the UK Media.”It featured a link to a news story from the UK that included the picture at left. An […]
[…] by Mark Graban on August 28, 2008 · 3 comments leanblog.org | Lean Blog: Bad Lean/5S Hits the UK Media […]
[…] of “bad 5S” practices that you might see in an office somewhere. You might remember the blog post and picture from a few years back when an accounting firm int he UK was forcing employees to put tape around […]
[…] back to the example of the UK Office 5S effort (corrected link 6:39 PM), was there benefit to standardizing the location of a stapler? I’d […]
[…] that’s the message the book was trying to get across. I’m sure the author might think this example would be waste, so do I. If neatness and order means we mark where our keyboard goes, yes, that’s probably a […]
I’m not sure how credible the message is, but I received this via Twitter, in regards to this episode:
“i talked to one of the team behind this PR disaster.Didn’t involve the unions upfront-big mistake. They got there in the end.”
[…] example, the “5S” program in the UK that was described as “demeaning.” From the news reports, this didn’t sound very […]
[…] who try to teach “real 5S” not “LAME 5S” (or Lean As Misguidedly Executed). Remember this from the UK? This article brings us more 5S […]
[…] spirited on my blog, although I’ve made comments about these issues and people before (worse, worser, and […]
[…] “Bad Lean/5S Hits the UK Media“ […]
[…] in the world of purely creative pursuits-nor should they be. There is certainly room for flexibility in an office setting, but there should also be a “right way” of performing a process. Maybe you’ve heard one of […]