It's inspiring to hear a CEO talk about Lean and continuous improvement concepts, as Larry Culp, Chairman and CEO of GE Aerospace, did recently on CNBC.
“We just need to get a little bit better every day.”
In Japanese (and in Lean management), we often refer to that as kaizen.

He also spoke about focusing on “safety first” and “problem-solving over finger-pointing” — things that I think are key to the Lean approach. GE Aerospace calls it “Flight Deck.”
Larry Culp's emphasis on “problem-solving over finger-pointing” is a powerful leadership approach that ties directly into the core of Lean thinking. When leaders create an environment where people feel safe to speak up about problems–and even mistakes–they're fostering what we call “psychological safety.” In my book The Mistakes That Make Us, I write about how if people fear punishment or blame, they'll stay silent to protect themselves, which is the enemy of both improvement and innovation.
Culp's focus on solving problems instead of blaming people is exactly what's needed to build a culture of continuous improvement. When we stop looking for who to blame and start asking, “What did we learn?” (as Toyota leaders tend to do), we unlock the real potential of our teams. That's when we create an environment where people are willing to take risks, share mistakes, and work together to find better solutions.
This mindset makes the workplace not just more humane but also more effective. In the long run, a culture that encourages speaking up and learning from mistakes will outperform one that relies on fear and punishment every time.
How can we develop a new generation of CEOs who care about operations and supply chains–and better yet, have them be Lean leaders??
Culp's leadership at GE Aerospace can potentially create a ripple effect far beyond his own company. When a CEO of his caliber embraces Lean principles–especially in an industry as complex as aerospace–it's a reminder of just how impactful Lean can be across any sector. Imagine if more aerospace companies followed suit, adopting Lean thinking not just as a set of tools but as a core philosophy focusing on safety, quality, delivery, and cost (SQDC).
This kind of leadership doesn't just improve operational efficiency; it can inspire industries like healthcare, where the stakes are even higher. I've long believed that if we applied Lean with the same rigor in healthcare as companies like GE Aerospace are doing in manufacturing and aerospace, the benefits could be monumental.
Leaders who prioritize Lean thinking in areas like patient safety and system-wide problem-solving could dramatically improve outcomes. Culp's approach serves as a great example of what's possible when leaders take the long-term view, focus on people, and commit to making things a little better every day.
Related Posts:
Please scroll down (or click) to post a comment. Connect with me on LinkedIn.
Let’s work together to build a culture of continuous improvement and psychological safety. If you're a leader looking to create lasting change—not just projects—I help organizations:
- Engage people at all levels in sustainable improvement
- Shift from fear of mistakes to learning from them
- Apply Lean thinking in practical, people-centered ways
Interested in coaching or a keynote talk? Let’s start a conversation.
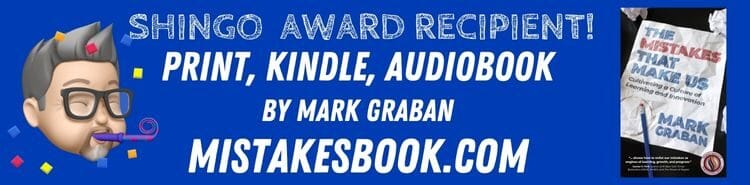
[…] GE Aerospace CEO Larry Culp on CNBC: A Little Higher Each Day – Mark Graban highlights some latest factors from Larry Culp’s present on CNBC about specializing in drawback fixing and psychological security tradition in wake of GE Aerospace issues. […]