What do Boeing frontline mechanics and engineers think about this day? What did they expect going into it? How did the day turn out? I'd love to know.
“Quality is made in the boardroom.”
W. Edwards Deming
I rolled my eyes hard when I read this announcement from Boeing, as part of the aftermath of the January 5th door plug blowout incident on an Alaska Airlines flight:
Boeing to hold Quality Stand Downs
In recent years, there have been many complaints about the Boeing culture. Culture starts with the executive suite. They're responsible for the culture, and they're responsible for the results of bad decisions made in the boardroom or the remote C-suite. Or they should be responsible.
Common complaints include:
- Boeing's engineering and quality culture was damaged after the McDonnell Douglas merger, and former McD leaders taking over
- “Schedule is king” being the mantra instead of “quality first”
- Finance and accounting leaders focusing on “shareholder value” instead of safety and quality
Boeing's announcement smells like blaming the front-line workers, mechanics, and engineers for problems rooted in culture and executive leadership.
I lived through a different version of this type of dysfunction at General Motors almost 30 years ago. I don't have first-hand knowledge of life at Boeing, but it sounds familiar (as I blogged about here, for example).
“During the session, production, delivery and support teams will pause for a day so employees can take part in working sessions focused on quality.”
This seems to assume that the production, delivery, and support teams are the problem. I hope the executives, board members, and all company leaders are also participating in these sessions.
“The sessions allow all teammates who touch the airplane to ‘pause, evaluate what we're doing, how we're doing it and make recommendations for improvement,' said Stan Deal, BCA president and CEO.”
Again, these sessions shouldn't be limited to those who “touch the airplane.” If Deal and other leaders want “recommendations for improvement,” they'd better be ready to truly listen and to take action.
Hear Mark read this post — subscribe to Lean Blog Audio
And this begs the question, “Have Boeing leaders not been soliciting recommendations for quality improvement?” If not, what “working session” will Boeing leaders attend related to that?
If the front-line workers say, “You need to stop pressuring us to constantly speed up,” will they listen?
If they say, “Stop punishing people who speak up about quality concerns or inspections,” will they listen?
Will leaders be sent to working sessions about “psychological safety” and what they can do to help Boeing employees feel safe to speak up without being punished?
Can Boeing leaders live this Lean mantra?
“Safety, Quality, Delivery, and Cost — in that order, every day.”
I don't mean slogans and posters. I mean walking the walk.
Maybe I'm being overly cynical. But it's born from manufacturing experience. I could be cynical and wrong about the Boeing day. Or I could be cynical and correct that the stand-down day is performative and more about public relations than real quality improvement.
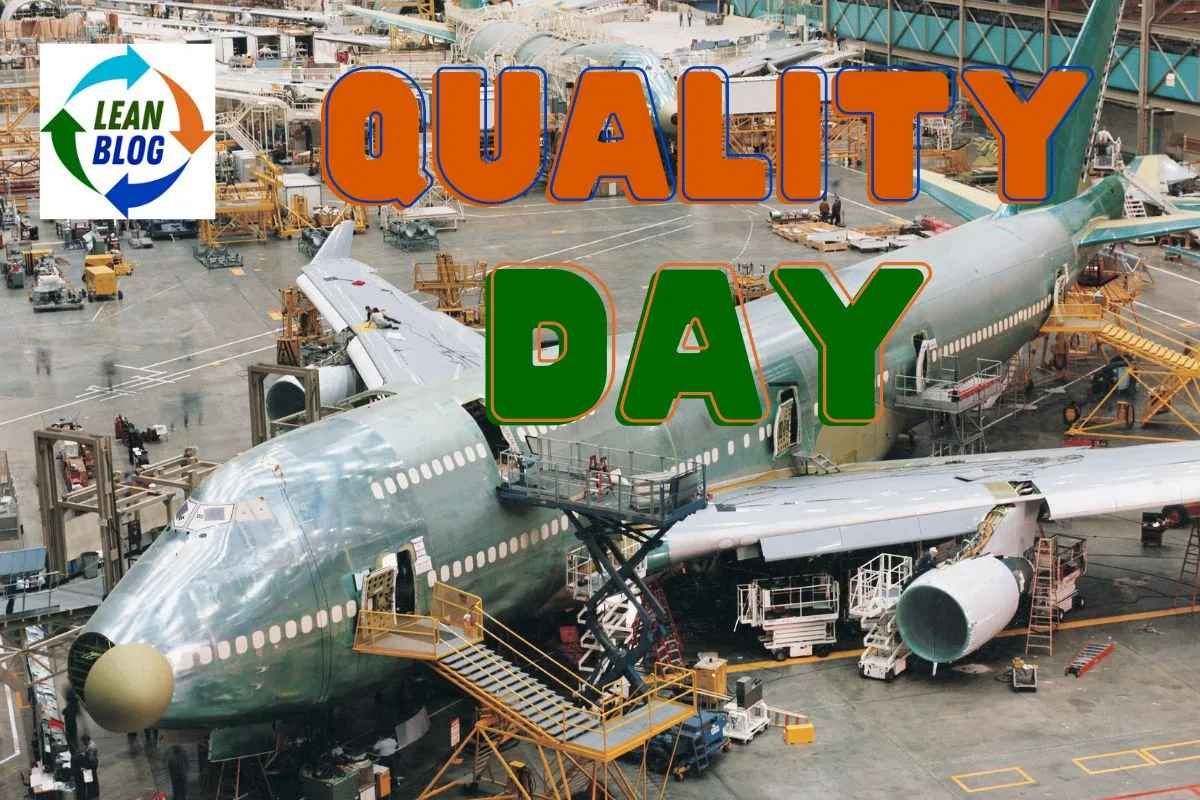
From the Seattle Times:
Boeing plans safety ‘stand down' as United reconsiders 737 MAX orders
Some other quotes:
“Employees will participate in “hands-on learning, reflection and collaboration,” Boeing wrote in a note sent to all commercial airplanes employees and posted on its website. The goal is to identify quality and compliance improvements and create actionable plans, according to the note.”
Deal also said:
“We have taken important steps in recent years to strengthen our Quality Management System's foundation and its layers of protection. But the AS1282 accident and recent customer findings make clear that we are not where we need to be,” Deal wrote in a message to employees last week.
It remains to be seen if Boeing leaders are blaming employees, saying, “You have failed us (the executives)” or if they're taking responsibility and telling employees, “We have failed you (and our customers).”
I imagine conversations like this (with the management person sounding like the VP, Bill Lumburgh, from the movie “Office Space”):
Management: “We need to rigorously follow our Quality Management System every single day.”
Workers: “Um, we know. You haven't allowed us to do so.”
Management: “Yeah…. so make sure you pay attention during the quality sessions today. Yeah… that would be great… Oh, and we need you to come in on Saturday to make up for the lost day of production.”
If you have first-hand experience with this day at Boeing, you can leave anonymous comments on this post if you'd like to share your perspectives and thoughts. You can use a burner email account. I'll protect your identity.
Update January 26th:
Highlighting this comment:
“The stand down might be worse than you feared. I hear that it was organized by McKinsey. Nothing says “genuine, in-touch with the factory, and competent” like hiring an outside firm with zero quality experience to run your quality stand down.”
Here is a news story about the day:
Boeing pauses production at Renton for a day in safety ‘stand down'
Is the problem “processes” or “culture”? They seem to be focusing on… processes:
“Though the 10,000 participating employees were encouraged to speak up about any concerns they have and offer suggestions about ways to improve the facility's processes, it's still not clear just what those workers discussed during the daylong production pause.”
What if those concerns included things like, “Stop pressuring us to work faster than we can! Stop focusing on quantity over quality!”
Would people feel safe to say things like that if they felt that way? And what will management do with suggestions related to processes or culture?
“The employees gathered in small groups to visually inspect work areas and identify improvements. Each team is now creating an “improvement and action plan,” Boeing said in its news release.”
I'm somehow picturing a lot of 5S work… will that really move the needle on quality.
I'm all for respecting people and valuing their input. I'm not sure calling them “tools” is the best way to do so:
“The most powerful tool we have is our people,” Ed Clark, the vice president and general manager of the 737 MAX program, told employees Thursday, according to a 1:19 video shared by Boeing. “The most powerful tool you have today is you speaking up. Use your voice.”
Encouraging people to speak up is one thing. But what really matters is the way management responds to people speaking up and using their voices.
People won't speak up if they're afraid. They'll also choose to not speak up if they feel like doing so is futile.
I'm not convinced that Boeing is really working to create a “speak up culture” with high levels of psychological safety.
Leaders must LISTEN UP. And they must take action.
You can also join the LinkedIn discussion:
Update April 11:
Does this look like the way you improve quality?
Please scroll down (or click) to post a comment. Connect with me on LinkedIn.
Let’s work together to build a culture of continuous improvement and psychological safety. If you're a leader looking to create lasting change—not just projects—I help organizations:
- Engage people at all levels in sustainable improvement
- Shift from fear of mistakes to learning from them
- Apply Lean thinking in practical, people-centered ways
Interested in coaching or a keynote talk? Let’s start a conversation.
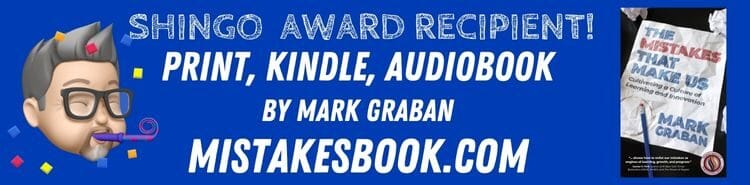
Here are some comments from this Reddit thread:
“It is management’s responsibility to set a high quality standard and ensure that it is met or exceeded, with no exceptions. To blame line employees is a huge red flag and prima fascia evidence that management is failing and is the root cause of poor quality.”
“No you’re right. Company culture comes from the top. If the culture is safety, it’s got to be management that makes that the case.”
“I work in manufacturing and shit like safety and quality are hard to “mandate” the same ways as “make more shit” it’s easy to yell at people and notice output is down.”
“At this point, Boeing needs to be broken up. A lack of competition has bred this sick, complacent, and ultimately incompetent company.”
“Boeing is what happens when you take an engineering company and replace all the engineers with MBAs, the employees turning the screwdrivers are not the problem.”
” In my opinion, the culture at Boeing isn’t one that encourages employees to raise their hands to build a better mousetrap or improve the product. Without a ‘see something say something’ culture, without fear of retribution, bad things can happen. And without oversight by outside, FAA government inspectors the risks are too high. People can be killed or injured.”
A quality output does not come from a poster, a slogan, or a pizza party, it comes directly from an organization’s culture. Culture, good or bad, is a by-product of everything the senior executives of an organization say, do, and promote (walking the talk). Whether they like it or not, these same executives also own the systems and processes by which products are made, or customers are serviced. When there is systemic failure, there is only one place to look for the cause, and this is also the first place where change needs to happen: at the top.
Well said, Andre!
From somebody who works in a different Boeing site, a credible source:
“The stand down might be worse than you feared. I hear that it was organized by McKinsey. Nothing says “genuine, in-touch with the factory, and competent” like hiring an outside firm with zero quality experience to run your quality stand down.”
A new article with other whistleblower comments from a former Boeing quality manager:
Former Boeing employees warn production defects ignored by company and US aviation regulator put passengers at risk
It really sounds like a culture problem and a management problem, not a “worker problem.”
If one quality stand down day was effective (was it?), Boeing thinks it’s a good idea to have… MORE.
https://www.boeing.com/737-9-updates#accordion-78d5956490-item-ac9b94e615
“In a message to employees, Boeing Commercial Airplanes President and CEO Stan Deal said the 737 program will spend several days in the Renton factory to focus on quality, including inspecting some undelivered airplanes for a potential nonconformance prior to delivery.”
As I blogged about here, their attempts to improve quality have to go beyond just doing more inspections.
“We will take advantage of the days in the factory so that our teams can catch up on unfinished jobs across all 737 factory positions. This is what we mean when we say that we will go slow to get it right.”
Catching up on “travelled” work is one thing. Is Boeing going to change the culture to one where workers can stop the line, Toyota style, to truly get it right the first time?
“In our drive to strengthen quality across Commercial Airplanes, your voice is critical. We asked you and everyone across our production system to speak up. Thanks to all those who have raised concerns and offered ideas.”
What will Boeing do now with the ideas that employees shared? Speaking up (and feeling safe to do so) is not enough — it must lead to action. Thanking employees for speaking up is a good start… but isn’t sufficient for improving quailty.
And why wasn’t Boeing already listening to their employees about improvement ideas? That should be a daily activity, not a special event.
On employee ideas being “evaluated”:
“There are more ideas that need to be refined before they can be put into action. Our teams will use the several days this week to workshop the ideas and try them out on the factory floor.”
Testing out ideas, hopefully in a Plan-Do-Study-Adjust manner, is better than just doing more inspections and more rework.
I find it very interesting that the executives, floor managers, and all those overseeing hands-on workers immediately found a way to place blame on the line workers requesting “recommendations for improvement.” There is clearly a lack of leadership, knowledge and accountability at Boeing. Where are the engineers in charge of quality? Are they being silenced by profit data driven executives?
Value Stream Mapping is a massive first step that the organization could use to identify quality issues and production delays. Yes, shutting down the factory and taking a few steps back would have effects way beyond the scope of the Boeing manufacturing plant, but hey, there should be competitor companies anyway and maybe this is what needs to happen in order for a door to open.
From the viewpoint of a Boeing executive, this strategy may be detrimental in the short term. However, following a successful revamp of production volume and quality will overcome the losses during the shut down and lead to more success in the future.
737 Max program head Ed Clark has been reported fired by Boeing. “He is leaving the company,” it should say, I guess.
https://www.nbcnews.com/news/us-news/boeing-ousts-head-737-max-program-management-shake-rcna139831