I was prompted today to think about an excerpt from my book Lean Hospitals: Improving Quality, Patient Safety, and Employee Engagement:
“In many hospital settings, staffing levels are set by benchmarking data, rules of thumb, habit, or financial constraints. Ideally, staffing levels should be based on actual workloads, driven by patient demand, and the standardized work that suggests the pace at which people can work without jeopardizing quality or safety. It would also be ideal to ensure that employees are not always 100% busy, as some slack time is helpful to account for variations in workload and to allow time for continuous improvement.”
By “many,” I could have maybe gone with “most”? Let's leave it at “many.”
I probably should have written more directly, saying “Don't try to ensure that employees are always 100% busy…” as some slack time is REQUIRED to… it's necessary, not a nice to have, if you want safety, quality, and flow.
Question for the readers:
Who is getting closest in healthcare to “staffing to demand” on a daily and hourly basis, making sure that there are ENOUGH staff members (and the right staff members) in place to be able to do the right work the right way — safe, high quality, caring care that minimizes delays — without overburdening staff??
Does that exist anywhere? I'd love to hear about it. Please leave a comment on this post. Or join the discussion about this topic on LinkedIn.
Another point… staffing to demand doesn't mean “flexing” — or sending staff home early when volumes are low. I'd argue that sending people home isn't a Lean practice at all. That's not what Toyota does. Here's another blog post on that.
We need to focus on the needs of patients and the needs of staff — that will then drive better results for the organization, especially if we are focused on long-term decision making, as Point #1 of The Toyota Way states:
“Base your management decisions on a long-term philosophy, even at the expense of short-term financial goals.”
How many healthcare organizations are doing that? How many are still driven by annual financial targets, quarterly targets, and daily productivity targets?
The long-term philosophy would drive us to use slack time in the day to work on continuous improvement instead of sending staff home early in the name of cost cutting. Continuous improvement (and using “non-productive” time for improvement) would be our daily practice if the statement “patient safety is always our top priority” were to be true.
A Longer Book Excerpt
Here is the rest of that section from my book on staffing levels being driven by patient needs:
“Takt is a German word that should be familiar to readers who are musicians as it signifies a pace or tempo, as in a piece of music. Takt is a Lean term for expressing the pace of customer demand for a value stream or a process. An auto assembly factory might have a takt of 50 seconds, meaning a customer buys a car every 50 seconds during the hours the factory is running. Takt is calculated as the number of available working hours (or minutes or seconds) divided by the customer demand.
In healthcare settings, applications of takt can be difficult to find or can be more complex than in manufacturing. While a car factory can have a level-loaded production rate for a month, based on average takt, a hospital must do work in response to patient demand that varies each hour and each day, as hospitals cannot level their work and build a parking lot full of cars to sell later. That said, there are some cases for which takt is useful in understanding our workload to drive staffing decisions.
For example, a hospital laboratory might need to draw 360 patient specimens in a four-hour window each morning. Takt is then 14,400 seconds divided by 360 specimens, or 40 seconds per specimen. As we develop standardized work (having eliminated some waste from the process as we do so), we might learn that it takes a phlebotomist (at longest) eight minutes to properly draw a specimen and then walk to the next patient. One person drawing a specimen every 480 seconds cannot meet the patient demand of a specimen every 40 seconds.
Simple math tells us we would need a minimum of 480/40 or 12 phlebotomists to meet takt. Practically speaking, we would want 13 or 14 to account for variation in the time it takes to draw specimens. In this case, and in other settings, we would likely have different takt time and different staffing requirements throughout the day and throughout the week.
We should do our best to use data to match staffing to demand, out of respect for our patients and for our employees.”
Please scroll down (or click) to post a comment. Connect with me on LinkedIn.
Let’s work together to build a culture of continuous improvement and psychological safety. If you're a leader looking to create lasting change—not just projects—I help organizations:
- Engage people at all levels in sustainable improvement
- Shift from fear of mistakes to learning from them
- Apply Lean thinking in practical, people-centered ways
Interested in coaching or a keynote talk? Let’s start a conversation.
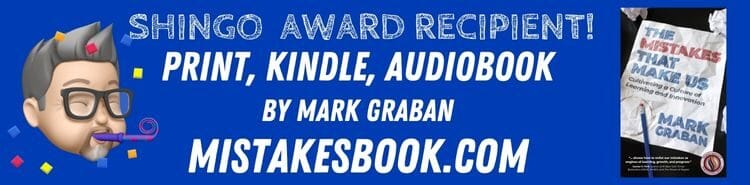