Lean can be very fragile. History shows that Lean can fall apart even in an organization that is years into a “Lean journey.” Lean can fall apart even if there had been a history of strong CEO involvement and leadership.
Hear Mark read this post (subscribe to Lean Blog Audio)
How is this possible? If often happens when a new CEO is brought in from the outside. In the case of the manufacturing company, Wiremold, it happened when they were acquired by a French company, Legrand.
As an aside, the team that coined the term “Lean” almost used the term “fragile,” as I blogged about here.
Back in 2007, Bob Emiliani joined me for Episode #30 of the podcast (I'm now approaching 300 episodes).
In the podcast, he told the “updated” Wiremold story (including the fall of Lean) in the 2nd edition of his book Better Thinking, Better Results. Wiremold was, for many years, considered to be one of the great Lean success stories.
You can listen to the podcast audio below and a transcript I just had made follows.
As you listen or read, think about how even the best “Lean healthcare” scenario could be undone by new leadership, as I blogged about here (and has happened many other times in recent years).
ThedaCare's Lean approach survived the first CEO transition from Dr. John Toussaint to Dr. Dean Gruner. Read about this in the comments, an excerpt from On the Mend.
Is it surviving the second CEO transition? Starting at 43:00 into this podcast (recorded after Gruner's retirement), he talks about the succession planning that he led. Read some of his comments here.
If you worked at a hospital that laid off their internal Lean team or otherwise killed their Lean program, I'd like to hear your story if you're willing to share. Contact me here if you'd like to share a story via email or if you'd like to schedule a phone call. I can keep your story anonymous if needed.
You can join or share the discussion we had last week about one quote from the podcast:
Podcast Transcript
Here is the transcript of Episode #30:
Mark Graban: Hi, this is Mark Graban from the LeanBlog. This is episode number 30 of the LeanBlog podcast for August 12, 2007.
Our guest today is Bob Emiliani of the Center for Lean Business Management, and also the author of the book Better Thinking, Better Results, which is now out in a second revised edition that includes a new epilog about Wiremold, the subject of the book, and how they've moved away from Lean after their acquisition by another company.
In this podcast, Bob and I will talk about why that happened, and what others can learn from the Wiremold story and efforts to prevent the dismantling of even the most successful of Lean transformations in other companies.
[music]
Mark: Joining us from Connecticut today is Bob Emiliani. Thank you for joining us on the LeanBlog podcast.
Bob Emiliani: It's my pleasure.
Mark: I wanted to talk about why you updated the Wiremold story, what was behind producing a second edition of the book Better Thinking, Better Results.
Bob: I did it because people wanted to know what happened to Wiremold's Lean effort since they were bought by Legrand in 2000. People also wanted to know what happened after our first edition. The other top managers started to retire in 2002, and ultimately, they wanted to know did Lean stick.
In the first edition of the book, I wrote that I was skeptical that Lean management would continue at Wiremold under new ownership, and with a new leadership team in which the Legrand personnel would eventually hold key positions.
I wrote that Legrand management did not buy Wiremold because it was Lean. They did not have any real interest in Wiremold's Lean capabilities or the management team's skills as Lean practitioners.
Legrand, like most manufacturers, has long operated their business according to batch-and-queue principles and practices. Therefore, it was just unrealistic to expect Legrand's senior management to recognize the value of Wiremold's Lean management system.
I also said in the first edition that it would be very interesting to see how Wiremold fares in the years to come under a parent company whose management practices are rooted in wasteful batch-and-queue. The question was will Wiremold managers be able to keep the Lean management system alive or will it succumb to the strong force of conventional management practices.
It turns out that Legrand's conventional batch-and-queue management practices prevailed. How and why this happened is something that all Lean practitioners should know about, because there's so much to learn from it.
Mark: That's unfortunate, and I agree it's something to learn from after reading the epilog to the book. What happened? What's the story behind it?
Bob: First of all, I'd like to say that I think it's extremely important to be consistent and apply a Lean mindset to these types of situations, where Lean has failed, just as we would do to any problem.
We start by seeing things as they actually are, even if it's ugly and even if it's not what we want to see. We confront the reality, and then we can identify ways to improve.
Something that's troubled me for a while is that too often a company's Lean efforts are characterized as problem-free. Basically, people just talk about the good stuff and tend to present a much better picture than what actually exists. It's just not reality.
There are a lot of problems, and we need each of these problems to surface in order to understand the root causes and identify and implement practical countermeasures.
Many people see what happened to Wiremold as a bad thing. In many respects it is, but it's also a very valuable story from which we can all learn from to help other people's Lean transformation efforts. I firmly believe that bringing this story to light is fully consistent with the Lean principles of continuous improvement and respect for people.
Wiremold backslid rather dramatically within three years after Art Byrne retired. Wiremold had a very strong management bench, two to three layers deep, to backfill Art and the other senior managers who retired or might leave.
But each member of Art's management team had great difficulty getting Legrand senior management to understand Lean. They all struggled, and so they eventually left. Of course, when what that happened, Legrand inserted their personnel into key leadership positions, and they knew little or nothing about the Lean management system.
They didn't support Lean in any significant way, and they did not participate in process improvement activities. In a lot of instances, they purposefully dismantled what Art and his team had done. It's not uncommon.
Changes in company ownership or top leadership are a huge discontinuity that is almost always fatal to Lean. History bears this out all the way back to the days of the scientific management system in the late 1800s.
When company owners or top leaders change, the management system quickly reverts back to the old ways of leading and managing the business. I thought the same thing might happen at Wiremold and it did.
I think it's important to understand what happened at Wiremold illustrates how wrong-headed the thinking is that if people practice Lean for several years, it will stick, that it will become part of the company's DNA. Guess what. It doesn't stick, and executives and others need to confront that reality.
Lean requires constant attention, maintenance, and improvement to keep it alive and healthy. It's people that keep Lean alive through the daily practice of Lean principles, processes, and tools. When the top leaders who have an interest in keeping Lean alive leave the company and are replaced by leaders who don't have the same interest, then Lean dies.
Lean requires constant attention, maintenance, and improvement to keep it alive and healthy. - Bob Emiliani Share on XAs you can imagine, it was personally very painful for Wiremold people to go backward. They fought very hard, but in the end what choice do you have? You either do what the boss wants, or you leave.
When the top leaders who have an interest in keeping Lean alive leave the company and are replaced by leaders who don't have the same interest, then Lean dies. - Emiliani Share on XMark: Why do you think it was that Legrand didn't value the Lean transformation that Art and his team and all the people at Wiremold had gone through those previous years?
Bob: Legrand senior managers, like most senior managers, didn't learn Lean in college or graduate school. They didn't get exposed to it on the job, so it really wasn't relevant, and those at the top apparently had little or no curiosity to learn about Lean management.
Art and his management team did not expect that to be the case, especially since Wiremold had done so well with Lean. Early on, there were good indications that Legrand senior management did want to learn about Lean.
After all, who wouldn't want to adopt a winning management system? But apparently, they didn't want to. Legrand senior management is not at all unique in this respect. They're just like most other top managers.
Mark: It sounds like, unfortunately, Legrand made some mistakes along the way, or at least we might view it that way as proponents of Lean. I was wondering if you could maybe talk about what you view some of those mistakes to be.
You already talked about dismantling some of the Lean practices. Maybe if you can share an example or two of how and why that was done.
Bob: From a Lean perspective, they clearly did make some mistakes, and in fact, they made some very big mistakes. Among other things, abandoning the Respect for People principle and blaming people for errors, going from 16 or 18 inventory turns back to 3 or 4 inventory turns cost a lot of money, which of course impacts shareholders, and then negatively impacts customers.
The collaborative relationship with suppliers gave way to arm's-length zero-sum power-based bargaining relationships and emphasized price. As you might imagine, there were plant closings and outsourcing to lower wage countries, basically the usual stuff.
It's very important for people to clearly understand that Legrand is not a bad company, and its leaders are not bad people. The actions that Legrand executives took after they bought Wiremold were sensible from their point of view.
They did what they were trained to do, and they did it very well. They did what they thought was best for Legrand and its shareholders. It's just that what they did happens to be the exact opposite of what Lean people would have done.
This outcome highlights a significant problem inherent to Lean management and its antecedents dating back to the late 1800s and early 1900 scientific management area, which very few people seem to appreciate. I'd like to bring more attention to this.
Mark: Yeah, sure.
Bob: That is, managers who do not understand what waste is and the benefits of process improvements miss great opportunities and may even inadvertently end up hurting the business. It's a common problem. It has a name, it's the mergers and acquisitions culture clash. It's nothing new, people are repeating the same errors.
Mark: It certainly sounds like they were going off of the mass production playbook.
Bob: Yeah.
Mark: Identifying what happened, and the situation — as you said — whether it was ugly or not, what do you think the rest of us can learn or should learn from what happened at Wiremold?
Bob: One of the lessons learned is that we should prepare for high probability events such as changes in company ownership or changes in top leadership. We know for certain that this will happen at some time in the future, so Lean leaders need to plan for that.
Art and his team did plan for these changes. In fact, they put a whole lot of effort into that, but in hindsight, it still wasn't enough. Lean leadership is about countermeasures to prevent outcomes they wish to avoid.
I talk about this in a chapter in my new book called Real Lean, Volume Two. It's called “Lean Estate Planning.” It's similar to how we might personally plan for our own estates when our day comes. It's a new idea that I think people need to pay some attention to prevent this kind of things from happening.
Another lesson learned is that Lean doesn't stick by itself even after 10 or 20 years of effort, if new executives one day come into the company with other interests. Look at Toyota. Their executives have long been worried about complacency even after seven decades of practicing their management system.
Another lesson learned is that Lean doesn't stick by itself even after 10 or 20 years of effort, if new executives one day come into the company with other interests. - Emiliani Share on XThey know that they can slip away quickly. They have to remain forever vigilant and ensure that the top leaders understand that people are promoted to the top, that they understand and practice the management system, and further that they continue to learn the management system no matter how long they work at Toyota.
I'll say it again, Lean requires constant attention, maintenance, and improvement to keep it alive and healthy. It's people that keep Lean alive to the daily practice of Lean principles, processes, and tools.
When the top leaders who have the interest in keeping Lean alive leave and are replaced by leaders who don't have the same interest, then Lean dies very quickly. The long view of history shows this happening over and over again, and in order for it not to happen, we need to be aware of what has happened in the past.
People will be utterly amazed the extent to which the Lean movement today is faithfully reliving the past and runs a very high risk of realizing the same marginal or unfavorable outcomes of what people have achieved in the past. The good news is there's a lot of practical countermeasures that can be applied, but basically only if we want to see that reality, confront it head-on, and take action.
Mark: I appreciate your sharing that story not only in the new edition of the book, which I've had a chance to see. I was familiar with the story from reading the original edition a couple of years back.
I was wondering if you could share some thoughts, maybe what kind of reactions you've gotten from the updated story, the new second edition and what's been happening in Wiremold.
Bob: The reaction has been favorable in the sense that people are getting some insight into what can happen, how Lean can backslide, how things can unravel despite tremendous long-term effort. That helps them plan for the future better. It makes them more aware of pitfalls and problems.
One thing people absolutely dislike is for their good efforts to just fall by the wayside. In going through the history of this earlier management system called scientific management, you read the leaders of that movements were very dismayed that their hard efforts eventually didn't amount to much. Nobody likes to see that happen to their effort.
Mark: No, of course.
Bob: This is starting to give an insight into the ways in which things can unravel and that we need to be aware of that. Bring it more to the front and center, and directly address it.
There's a lot of new stories about companies doing Lean, and that's great and so forth, but we don't spend enough time looking at the failures and understanding what's going on there. There's a tremendous amount to be learned from that. If we really expect this to move forward, then we have to get into understanding the failures or where the outcomes were much less than expected.
Mark: I think that's a healthy thing. One of the books on my shelf is this book, How to Prevent Lean Implementation Failures, by a different author. It highlights, “Here are some of the things that can go wrong…” and I think it's helpful to…
The same way you might use failure mode effects analysis to look at a physical process, maybe to anticipate what are the things that could go wrong with our management system, what's the risk, what would the impact be.
Bob: That's right. To go through a formal failure analysis is not something that is normally found in the business world. For example, in business schools, they rely extensively on the case study method, and the vast majority of case studies report something positive.
It's not so familiar to look at something negative, and it's very unfamiliar in a business school setting to apply formal root cause analysis to the errors that occurred. We need to start doing that.
Mark: If we're talking through maybe looking at least root cause or root causes of what happened with Wiremold, you strongly hinted at one of those root causes maybe being the educational system, business school in particular. Are there efforts under way?
What thoughts do you have about how can we try to make sure Lean ideas are starting to get taught in business schools, or if Lean practices are good business, which I assume a lot of us listening, through self-selection that were Lean people listening to a Lean podcast would believe Lean is good for business.
What can we do to influence it so it seems less like a foreign program or an alternative approach to business and try to get it taught as maybe a more…How can we turn into a more conventional way of doing business?
Bob: That's a good question. The Lean Enterprise Institute has sponsored something called teachinglean.org that is trying to establish a group of people that are interested in bringing Lean into the classroom.
Then, MIT's Lean Aerospace Initiative has an effort as well. There was a joint meeting of these two groups last October to discuss ways to bring Lean into the classroom.
What ends up happening is it's on an individual professor-by-professor basis. It's really not engaging the deans or the provosts of business or engineering schools to establish Lean management as a major pedagogical approach to management and leadership and so forth, in those settings.
Mark: It sounds like the same company trap if the leadership leaves, or in this case if the professor moves on, someone else comes in, and suddenly you're not teaching Lean anymore.
Bob: That's basically the same thing. You're absolutely right.
Mark: Hopefully, we'll make progress in that area over the coming years and decades. Did you have any final thoughts that you'd want to leave with the podcast listeners here?
Bob: I just want to reemphasize the point that I think is very important. Looking back in the history of people trying to advocate a different system of management than the conventional batch-and-queue approach, it shows these kinds of failures and so forth happening over and over again.
I'm really trying to bring an awareness of what happened in the past so that people can gain an appreciation for how faithfully we're reliving that past.
Things are different today to be sure in a lot of ways, but there still is in my view a significant risk of having marginal or unfavorable outcomes occur. Just by awareness of this, that will help us or engage us into some root cause analysis and identifying countermeasures.
That should be a very different activity and effort than what has happened in the past. In the old days, people didn't do formal root cause analysis. They attributed the problems to various things, to reasoning, and maybe they did it five whys in their head, but they didn't really lay it out on paper and…
Mark: Or the five whos. [laughs]
Bob: Yeah, that's right. There was a bit of blame and particularly towards senior management. If we can engage in that process and get a better understanding of what's going on, then that serves everyone very well, all of the stakeholders, customers, suppliers, investors, employees, communities, etc.
Mark: Bob, thanks again for being here on the podcast. Really enjoyed it.
[background music]
Bob: Thank you. I hope it's been helpful to listeners.
[music]
Please scroll down (or click) to post a comment. Connect with me on LinkedIn.
Let’s work together to build a culture of continuous improvement and psychological safety. If you're a leader looking to create lasting change—not just projects—I help organizations:
- Engage people at all levels in sustainable improvement
- Shift from fear of mistakes to learning from them
- Apply Lean thinking in practical, people-centered ways
Interested in coaching or a keynote talk? Let’s start a conversation.
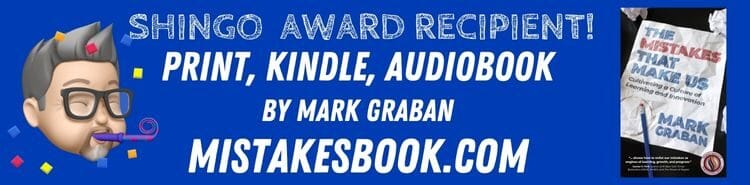
Mark – First, I hope people appreciate your work overall, and especially the 300 podcasts in particular. It’s an amazing level of dedication, constancy of purpose, and a valuable contribution.
Second, not many people were interested in this problem back in 2007. It’s odd that given the effort needed to establish Lean, that senior management teams would not take great care to assure its future continuation.
I’d like to know how Virginia Mason is preparing for Gary Kaplan’s eventual retirement. Pages 283-290 of the book offer some ideas for how to survive the transition to a new CEO or new owner (or new board or directors).
And third, to my understanding, Lean has been an off-and-on-again thing at Wiremold since the second edition was published in 2007. Perhaps someone has more up-to-date information (just the facts, please; no spin).
Thanks, Bob. I appreciate it. Thanks for your work on this subject.
I also wonder about succession planning at Virginia Mason.
John Toussaint had a very specific internal candidate development plan that led to Dean Gruner getting promoted to the job about 10 years ago. It’s chapter 9 in On the Mend.
This time, when Gruner retired, ThedaCare’s board selected an outsider. This outsider praised ThedaCare’s “Lean Six Sigma” approach, which means he misspoke or didn’t know much about ThedaCare’s approach, because Six Sigma was never part of the ThedaCare methodology.
I asked Dean about succession planning in this podcast, after his retirement.
The executive hiring process is uniformly poor in that it favors those who interview well (and operates under the flawed assumption that if you’re an exec, you can do the job). It usually results in the hiring of someone who cannot do the job. I’d rather hire someone who did not interview well – say, someone who challenged me as an interviewer, for example – but who can do the job.
Gruner said, at 43:00 into this podcast:
He says he had a very formal process. Gruner was NOT on the search committee, “which was a little strange,” Gruner said. But he said it was a great search committee with a former board chairman that knew the organizational well.
Even though they had some “very strong internal candidates,” the outside candidate was deemed better.
“I can see why they chose him.” He came from a larger market with great experience, Gruner said. Why would he come to a smaller market? He had been “following” ThedaCare for 8 to 10 years and it was “one of the few jobs he would leave for.” And it was a chance to be a system CEO instead of a regional CEO, Gruner said. He is “very familiar with Lean…. in Ohio, I learned they call it ‘Lean Six Sigma…” his oldest son’s a black belt. He’s seen Lean, when done well, accelerate organizations…”
“He’s a huge supporter of improvement and working with people. I think he will do well.”
The search process… Who doesn’t claim theirs is a “great committee?” Anyway, based on those tidbits, it can sound like a candidate more interested in self-aggrandizement than building upon the work of their predecessors. Bigger is better, right?
This worries me:
“He is “very familiar with Lean…. in Ohio, I learned they call it ‘Lean Six Sigma…” his oldest son’s a black belt. He’s seen Lean, when done well, accelerate organizations…”
Does being a CEO of an organization that understands and practices lean management make you well suited to identifying the wolf in sheep’s clothing that is “fake lean”?
Credit to Bob for the term :-)
It’s also worth noting that since most executives have never seen Lean as more than an initiative or as a collection cost reduction tools, it is inevitable that as times change their needs change, and Lean fades away and is replaced by something else that meets the needs of the times. Recognizing Lean as a management system should have helped overcome executive’s narrow perceptions of Lean, but that view came along in 2007 and may be have been too late. I fee that the current effort to position Lean as a corporate strategy reflects some amount of desperation (given the case presented for Lean as a corporate strategy is very weak), though it may produce some positive results among the nearly (or already) converted.
What do you mean by 2007? I was taught that lean was a management system long before that.
Me too; I understood Lean to be a management system way before that. I was referring to the year when LEI officially moved from “lean production” to “lean management.” It was at the 10th anniversary party of LEIs founding, which I attended. It was the result of focus group break-out sessions where one group recommended the change in focus to Lean management, and another group recommended that LEI start a new focus on Lean leadership, given its importance in Lean transformation. I understood the need to focus on Lean leadership long before 2007 as well. Anyway, LEI adopted those recommendations, so 2007 is the date when Lean management and Lean leadership started to become a more widespread subject of interest in the Lean community. So, “Lean production” was the term widely understood from ca. 1988 to 2007. And “Lean leadership” was not an item of significant interest until LEI said it should be (the result of their global reach and influence). In my view, the time delays in correctly representing Lean and comprehending the importance of leadership caused (significant?) harm the Lean movement.