Lean sometimes gets, I think, an unfair rap that it's only a method for incremental improvement. See this article, from the NEJM website, for example: “Limits of Lean — Transformative Care Redesign Must Go Beyond Typical Lean-Based Improvements.”
Listen to Mark read this post (subscribe to the podcast):
The author is being fair in distinguishing between what's “typically” done and what should be done.
The phrase “Lean transformation” gets thrown around a lot… and for good reason. That should be the goal. We shouldn't incrementally improve a fundamentally broken system or organization. Doing the wrong things slightly better isn't the path to success. I agree.
I've been fortunate to be involved in some transformative Lean efforts in healthcare organizations.
The dual pillars (the “equally important” pillars) of The Toyota Way management system are:
- Continuous Improvement
- Respect for People
I generally think of “continuous improvement” to mean the Kaizen model of everybody improving, everywhere, and every day (see this video with Masaaki Imai).
Much of the focus, rightfully so, is on front-line staff and leaders driving small improvements. Below is a Kaizen model, a version that was adapted from The Toyota Way Fieldbook by Franciscan St. Francis Health (and included in our book Healthcare Kaizen). This model emphasizes, as Imai does, that there different levels of Kaizen.
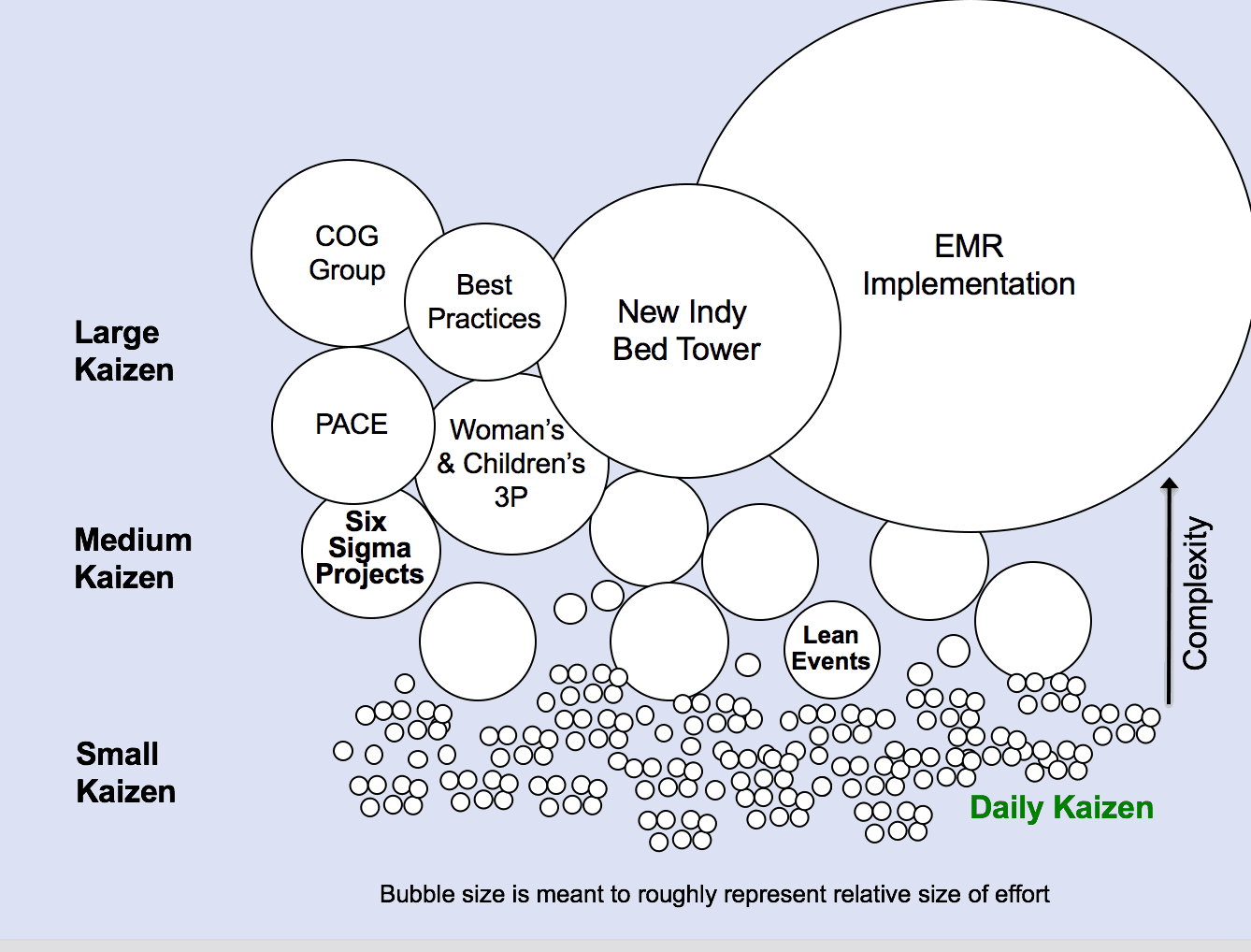
Management is more responsible for system-level Kaizen, or more radical improvements.
The Japanese word “Kaikaku” gets used to mean “radical Kaizen” or “radical improvement” (where “Kaizen” is translated to mean “good change” not just “continuous improvement”).
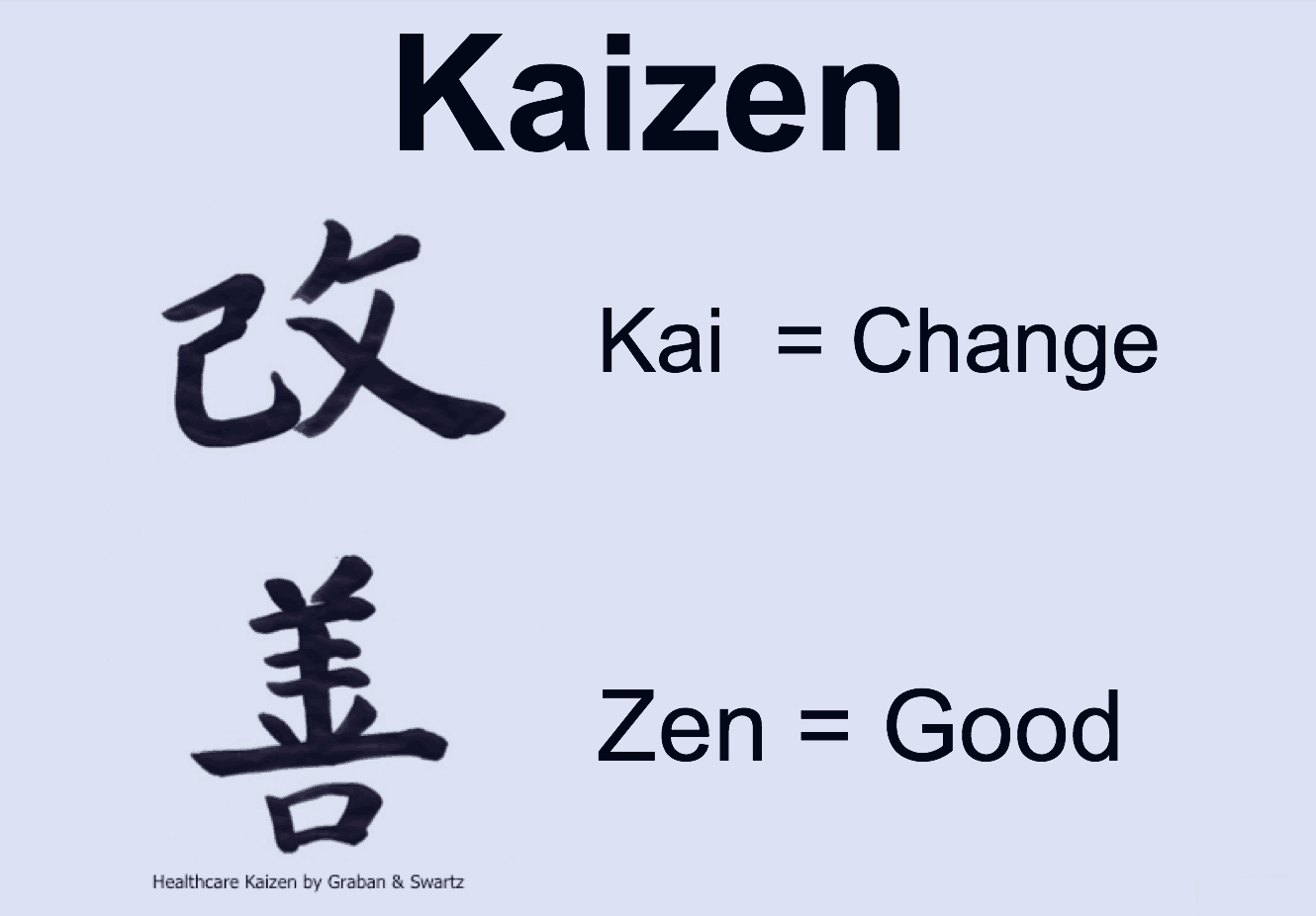
The NEJM article says:
“Citing the successes of a few organizations, some health care leaders treat Lean thinking and methods as optimally positioned to drive major leaps in quality, cost savings, engagement of patients and employees, and even population health. Regrettably, limited evidence supports these high expectations.”
I've seen many “major leaps in quality” for example, such as Dr. Richard Shannon and his colleagues dramatically reducing central line infections in a few different organizations, using basic Lean methods:
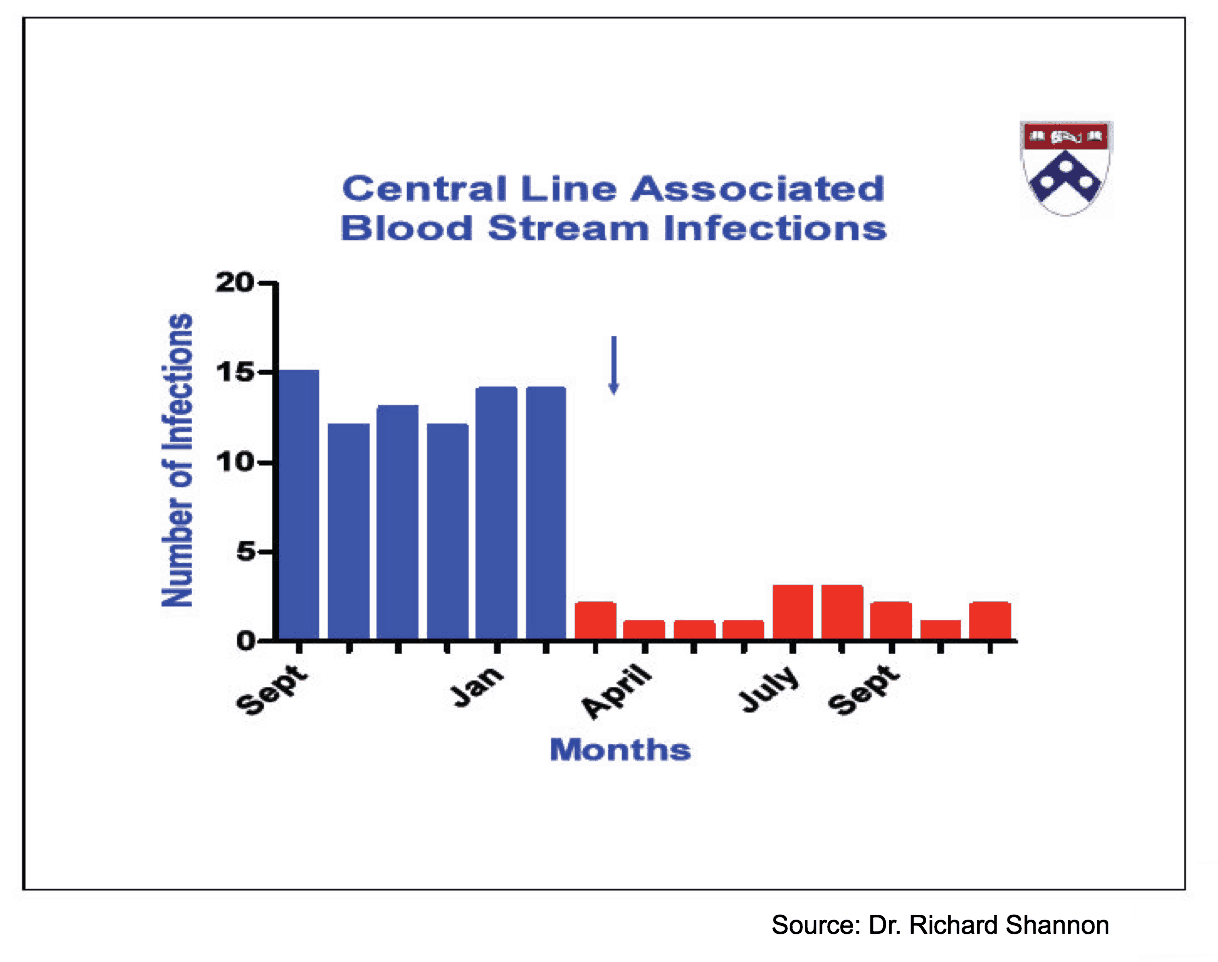
That wasn't just minor incremental improvement. I guess there isn't enough in the academic literature to convince people that Lean can drive transformative results.
I could nitpick that article or discuss the weaknesses in academic literature reviews, but that's a blog post for a different day.
Lean: Kaizen and Kaikaku and More Kaizen
When I worked in the hospital Lean consulting group at Johnson & Johnson, we did 12- to 16-week projects that were intended to transform a department or a value stream.
The goal was usually to improve key performance measures by redesigning and reinventing systems — usually aiming for 30 to 50% initial improvement.
In a typical lab project (read a PDF case study here), we'd teach a team of lab staff and managers how to analyze and understand their current state.
Spaghetti diagrams, like those below, weren't used to blame staff for being inefficient. We'd ask questions like “what takes you away from the real work?” and we'd brainstorm ways to reduce those problems – in the short term or the longer term.
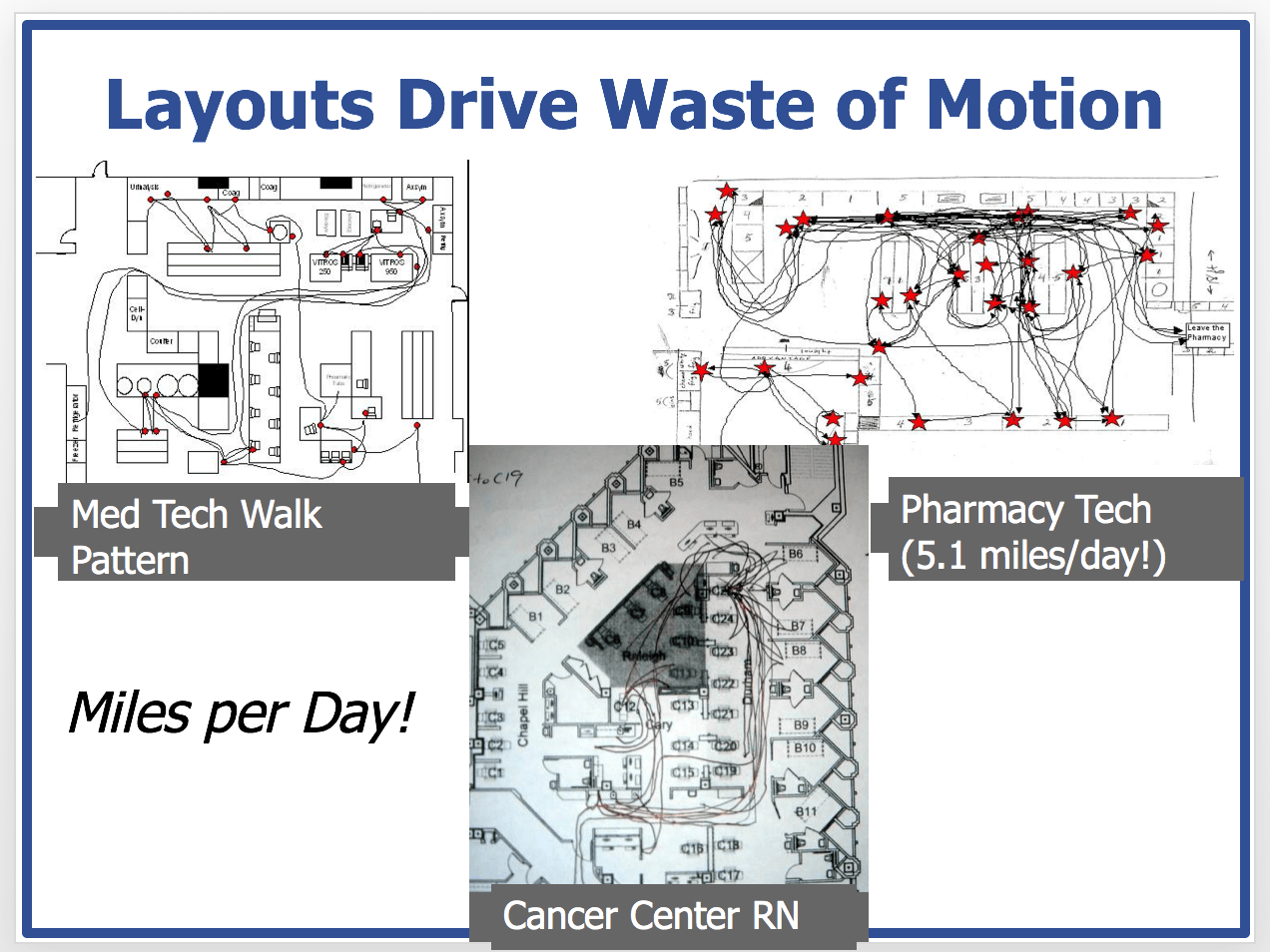
I've led similar efforts with hospital nurses and staff who were trying to understand their current state in the context of “Lean Design” activities that were trying to reinvent spaces and processes for new construction that was planned (read more about this).
We were never trying to jump to solutions. As a consultant, I wasn't bringing in pre-packaged solutions.
We studied the current state and took that learning (and a better understanding of customer goals and needs) to go through cycles of Kaizen and Kaikaku and then more Kaizen.
Studying the current state often meant looking at the big picture, using methods like Value Stream Mapping to get customer input and break down silos.
It's a classic Lean lesson that you shouldn't just automate a bad process. You also shouldn't just tweak a bad process.
In these projects, we'd go through these cycles of:
Kaizen: Identify things that could be improved today… tweaking the current state in a way that was helpful. An example would be 5s-ing the current workspace or setting up a basic Kanban system that helped save time and improve efficiency and quality.
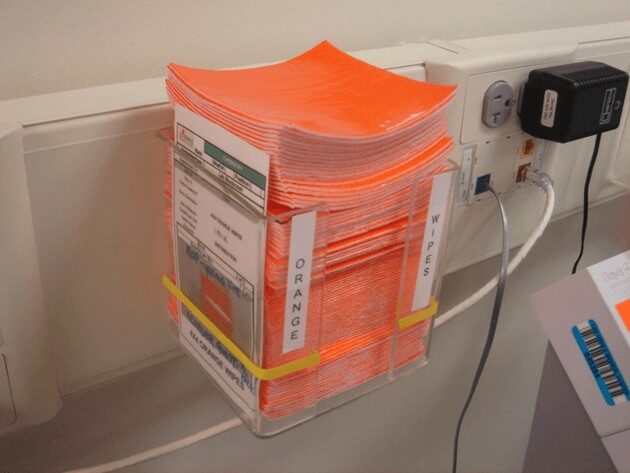
Kaikaku: While we were making short-term improvements (demonstrating that Lean was helpful), we'd be working on the longer-term reinvention and redesign of the system. In hospital labs, this would include changing the physical layout and flow of the lab. It wasn't about working faster in the old system – we were inventing a better one.
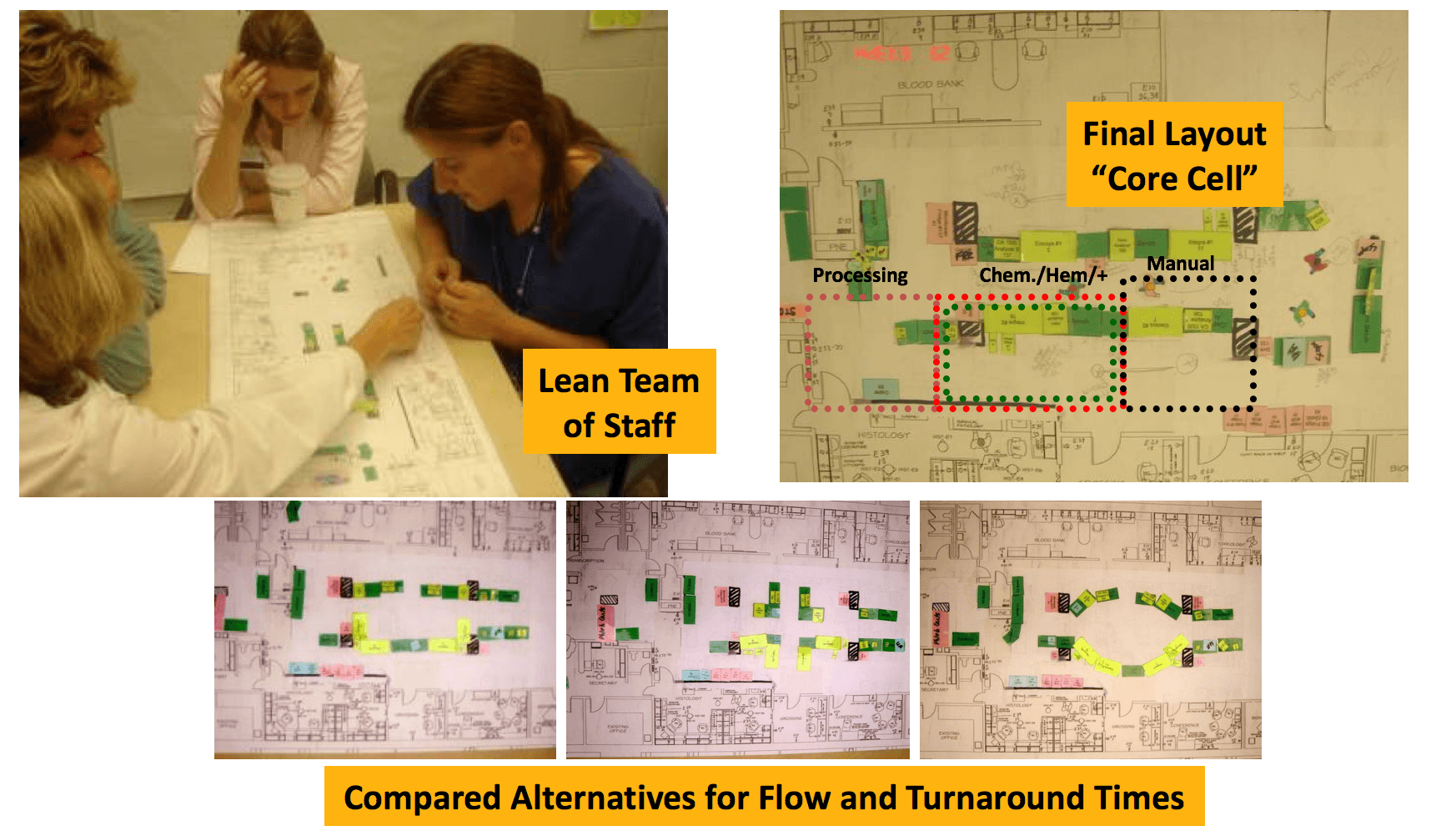
Kaizen: The key to sustaining results that come from redesign or radical improvement is to keep improving. That's why, through these projects, I'd focus on teaching department managers and hospital leaders how to engage people in ongoing continuous improvement. No redesign effort, no matter how much we planned and tested and iterated, ever led to a “perfect” design. We'd have to tweak and adjust. That's the Lean spirit.
This process would include team huddles, Kaizen boards, performance measures, and more.
You can even apply the Kaizen process to improving the way huddles are done as you run your operations after the redesign, the improvement never ends.
Kaizen, Redesign, and Kaizen of LeanBlog.org
Every few years, there are reasons to do a redesign of my blog (technical reasons and design/usability trends). A few years ago, I updated the WordPress theme to one that was “responsive” so that readers who visit the site on mobile devices (which is now 30% of my blog's traffic) got a consistent look and feel as you would on a computer.
I try to continually improve the blog over time – to make it more interesting, load faster, etc.
I'm going through this process now where, within a few weeks, you'll see a LeanBlog.org site that looks different – and hopefully it's a change for the better.
In working with a blog consultant, their current state analysis uncovered some things that I could Kaizen immediately… so those have been implemented. For example, the site already loads a bit faster on mobile devices as the result of removing some unneeded code.
Now, I wait on the redesign, the Kaikaku.
Then, the cycles of continuous improvement will never end! And I hope you enjoy the improvements. I enjoy the process.
Please scroll down (or click) to post a comment. Connect with me on LinkedIn.
Let’s work together to build a culture of continuous improvement and psychological safety. If you're a leader looking to create lasting change—not just projects—I help organizations:
- Engage people at all levels in sustainable improvement
- Shift from fear of mistakes to learning from them
- Apply Lean thinking in practical, people-centered ways
Interested in coaching or a keynote talk? Let’s start a conversation.
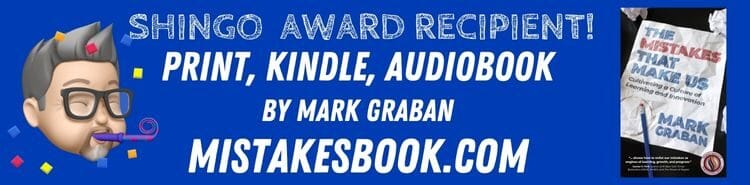