How many times do we hear people say things like “We don't have time for Lean” or “We don't have time for Kaizen“? It happens a lot, right?
As I've said before (and in this video) a “lack of time” is a problem to solve, not an excuse to hide behind. If improvement is important, you find ways to make it happen. If developing staff capabilities and learning how to “practice Lean” is important, you start some experiments and you figure it out.
The classic “Kaizen event” (aka Rapid Improvement Event or Rapid Process Improvement Workshop) is a full week. That poses a real challenge to many organizations. How do we dedicate staff time to that? How do we backfill staff to keep things running normally? These are solvable problems and many organizations figure this out, even if it's not easy or painless. Some organizations get creative and solve the problem by doing shorter, more focused events (or an innovative “6-3” schedule as discussed here).
If it's too difficult to pull staff away for a week or a few days, some organizations have used the daily continuous improvement model of Kaizen to identify and fix small problems. It's easier to find 20 minutes or an hour to work on a small problem (and small solution) here and there within a team. Yet, many organizations still struggle to make this happen.
Listen to Mark read this post (and subscribe to the podcast):
Not having time to improve is a Catch 22 perfectly illustrated by this graphic created by Hakan Forss:
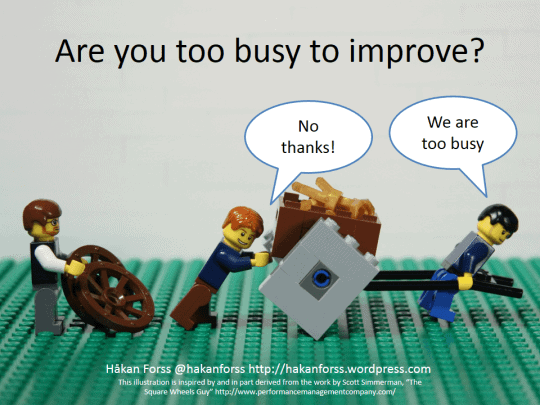
So How'd You Get 16 Weeks of Time?
When I started working in healthcare just over ten years ago, I was part of a consulting team at ValuMetrix Services, which was part of Ortho-Clinical Diagnostics, which was a part of J&J at the time.
Unlike many consultants, our model was not built around lots of training or a series of weeklong Kaizen events. We had what we referred to as Lean transformation model, which was basically a 12- to 16-week project that dramatically redesigned and overhauled a department or a value stream.
This model was taught to Ortho by consultants who had worked in J&J manufacturing and sometimes worked with our healthcare clients, including Mark Jamrog and Charlie Protzman, who has written some books on Lean healthcare now too (see here and here).
The basic model included 100% DEDICATING the time of four to six staff members to the project that entire time, 40 hours a week.
The early ValuMetrix projects were based in hospital clinical labs, which was natural since ValuMetrix was working with the customers of Ortho-Clinical diagnostic lab analyzers and equipment. A “core lab” project would usually include a few medical technologists from the main areas being affected (such as chemistry and hematology) and maybe a technologist from another area (like microbiology or histology). There was usually a lab assistant on the team. We'd often have an emergency department nurse or inpatient nurse to help represent the internal customer viewpoint.
Again, we'd have these folks FULL TIME for the entire 12- to 16-weeks. At an average fully loaded cost of $50 an hour, 40 hours a week times six people times 12 weeks is a staff cost and investment of $144,000 (plus the cost of our consulting services).
That's a huge investment. The cost would be higher if they used short-term agency / temp staff or overtime to help backfill the Lean project teams.
As a consultant, my role was to help teach and coach, so the Lean teams (and their leaders and colleagues) could learn by doing over that time. I would typically be there for two or three weeks before stepping back for a week to allow the Lean teams to continue working on their own. Sometimes, they'd do really well and sometimes they would struggle… but that was part of the development process.
Our goal wasn't just about ROI – we were also trying to build capabilities so that:
- Lean was more than just a project, becoming “the way we do things”
- Lean could lead to ongoing continuous improvement
- Lean could be spread to other parts of the hospital (with or without the consultant's continuing help)
The ValuMetrix case studies aren't online anymore, but you can read one of them that I've saved and posted on my website.
Here's part of the case study:
The importance of building a Lean team of hospital staff
Fundamental to the ValuMetrix Process Excellence approach is to build a Lean team of hospital staff so that Lean processes can be sustained after the consultants leave. At Riverside, the lab's Lean team consisted of two med techs, one pharmacy tech, one lab assistant supervisor, and an administrative assistant who worked half-time.
For 14 weeks from July 2006 through early October, the team devoted 100 percent of its time to the Lean implementation process. ValuMetrix consultants were onsite for ten of those 14 weeks, providing extensive training and leading a current state analysis in the lab, which found that the existing lab layout and processes drove wasted motion and delayed turnaround times.
The ValuMetrix approach worked so well, according to Dr. John Jurica, Riverside's vice president of medical affairs, “because you have a team that is committed to it full time for a period of weeks. They did present-state knowledge and took the time for a thorough analysis. Often, people assume they know their own problems, so you don't take a critical look at mapping out the problems.”
Dozens of hospitals took the plunge and tried this ValuMetrix approach, with the dedicated staff time.
The ROI was often very compelling, although (as it says in the case study), the financial return on investment wasn't the only thing that mattered.
The ROI from these projects usually included:
- Reduced overtime costs
- Reduced temporary staff costs
- Reduced staffing costs (always done through attrition or reassignment, NEVER layoffs)
- Shorter patient length of stay driven by faster lab turnaround times
- Increased revenue resulting from increased capacity (doing more testing volume with less staff)
The ROI was usually very positive, even when considering the cost of physical lab renovations that helped improve flow.
I was reminiscing recently with one of my former colleagues. We both smiled and shook our heads a bit when we asked, rhetorically, “How in the heck did we ever get hospitals to agree to dedicating time and making such a big investment?”
Answering our own question, here were some factors:
- Lean was totally brand new to our clients, in most cases, so they wanted input and advice about HOW to proceed
- Our clients believed that the 12- to 16-week project approach gave more time for everybody to learn by doing, including the lab managers, directors, and (sometimes) the hospital senior executives
- The benefits, including ROI, had been clearly demonstrated from other projects and we had great word of mouth and referrals about our approach and results
I wrote about this approach in the different editions of Lean Hospitals (including the upcoming 3rd edition, which you can pre-order today).
In my book, I've called these initial projects “model lines” (or they're what John Toussaint and others call a “model cell,” also see his book Management on the Mend). Toyota and their TSSC group recommend this “model line” approach, as well.
In the 3rd edition, I shared some endorsements of this model from two different lab managers and directors:
Clay York, formerly the laboratory manager at Children's Health (Dallas, TX) reflects on their Lean success, as highlighted in Chapter 1, saying, “We saved $419,000 annually in labor cost, without layoffs, as a result of our initial Lean implementation project. These savings would not have been possible without the continual flow and implementation of ideas and suggestions from the people who do the real work. Freeing up their time to actually write up and follow through with their plans is absolutely necessary to achieve these types of results.“
Stephanie Mitchell, laboratory services director at Riverside Medical Center (Kankakee, IL) adds, “For Lean to be successful, you need dedicated staff and dedicated time to accomplish the goals of a project or improvement. They can't give the attention needed while still doing their regular job. So, we had four staff members dedicated to Lean for about 12 weeks as we redesigned our lab and we still occasionally schedule days for staff to process improvement and redesign. It takes time to work on improvement, but in the end the return on the investment was well worth it.”
What do you think about this sort of model line approach as an alternative or a complement to:
- Doing lots of training and belt certifications
- Doing lots of RIEs and events scattered throughout a hospital or system
- Using a limited set of Lean methods, like 5S, across an organization?
These projects are intense… I haven't done one since 2009, when I left to join the Lean Enterprise Institute. But, let me know if you'd like to talk about that approach and ways I might be able to help you in 2016.
Please scroll down (or click) to post a comment. Connect with me on LinkedIn.
Let’s work together to build a culture of continuous improvement and psychological safety. If you're a leader looking to create lasting change—not just projects—I help organizations:
- Engage people at all levels in sustainable improvement
- Shift from fear of mistakes to learning from them
- Apply Lean thinking in practical, people-centered ways
Interested in coaching or a keynote talk? Let’s start a conversation.
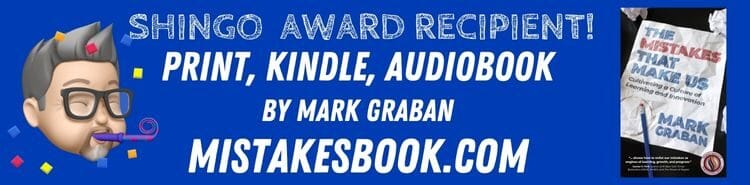
[…] participated in my Lean initiatives (and have documented others in my book and here on the blog) and the success came from ENGAGING […]