In discussing Lean and working with people in different organizations, I so very often hear things like “we don't build cars” or “we're different.” I know I'm not the only one who hears that. The implication is “Lean won't work here, because we're different” in some way. Different country, different industry, different hospital department, different patient or payer mix, etc.
I wrote about being different back in 2009, if you want to check out that post.
Lean is, of course, not about a better way to build cars. It's a transferrable philosophy, management system, and methodology that is being applied in many different settings and industries, including healthcare.
I'm often told (sometimes by a person who is being sort of huffy):
“Patients are not cars.”
I know.
“A hospital is not a factory.”
Yup, agreed. Those are pretty solid facts. One of those things is not like the other. I appreciate people bringing up those points as a concern (as in “don't screw up our hospital”) but I'm less patient if people are hiding behind those phrases as an excuse to not change.
Instead of focusing on excuses for why Lean won't work, the key thing is to figure out how to apply Lean to your setting. What problems do you need to solve? Focus on that instead of “implementing Lean.”
What needs to be different because of your environment? If certain Lean dogma says “overproduction is the worst form of waste,” maybe the worst form of waste in healthcare is actually defects and harm to patients.
Hear Mark read this post (subscribe to the podcast):
Lean is Not About Building Cars
Some don't realize that Toyota wasn't originally in the car business. Their original product was weaving looms, machines that turn thread into fabric.
Here's one of those weaving looms I saw at the Toyota Technology Museum in Nagoya:
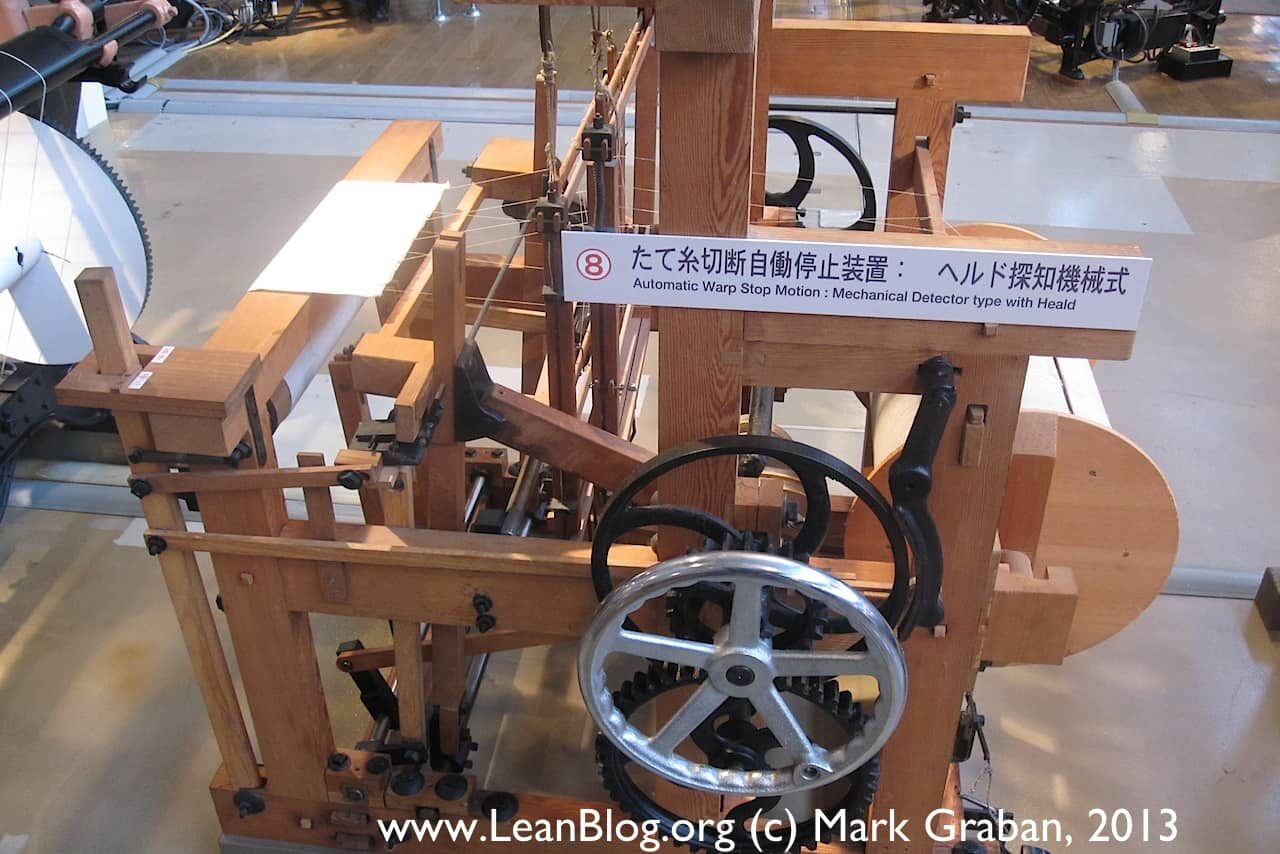
The sign says “automatic warp stop motion” because its “mechanical detector” automatically detected when a thread broke. This was a huge innovation in 1924.
Before this invention, you'd need a worker standing over each loom, visually inspecting for thread breakage. They'd have to stop the machine manually to stop it from producing bad fabric or defects.
That couldn't have been very interesting or rewarding work, to just watch a machine.
A loom that stopped automatically led to the principle of “jidoka.”
From Toyota's web page on jiodoka:
“The Toyota term “jido” is applied to a machine with a built-in device for making judgments, whereas the regular Japanese term “jido” (automation) is simply applied to a machine that moves on its own. Jidoka refers to “automation with a human touch,” as opposed to a machine that simply moves under the monitoring and supervision of an operator.
Since the loom stopped when a problem arose, no defective products were produced. This meant that a single operator could be put in charge of numerous looms, resulting in a tremendous improvement in productivity.”
It means automation with a human touch, but jidoka also leads us to the principle of building in quality at the source.
The Toyoda family made a lot of money selling the patent for the auto-stop loom and Kiichiro Toyoda decided he wanted to get into the car business.
Here is a photo, via Wikipedia, of the very first Toyota car, the 1936 Model AA:
“Toyota Model AA” by Chris 73 / Wikimedia Commons. Licensed under CC BY-SA 3.0 via Commons.
As the Toyota car business was launching, I'm sure there were engineers or managers who came over from the weaving loom business.
The ideas of jidoka, man/machine separation, poka yoke (error proofing), and quality at the source were carried over and Toyota eventually built upon that to create the Toyota Production System.
We're Different!
Anyway, I amuse myself trying to picture the first time a Toyota weaving loom person mentioned these concepts to a Toyota car person.
I bet somebody, at some point, said:
“Jidoka doesn't apply to us! We don't make weaving looms! We're different! We build cars.”
I bet they added “Weaving looms are not cars” for good measure.
But, thankfully that possibly-made-up person in the imaginary conversation didn't win that fight.
Thankfully, we have the Toyota Production System and Lean today.
Thankfully, people in healthcare and other industries are getting beyond their we're-different-ness to improve using these principles and methods.
You're different. That's OK. You can figure out Lean anyway… :-)
Please scroll down (or click) to post a comment. Connect with me on LinkedIn.
Let’s work together to build a culture of continuous improvement and psychological safety. If you're a leader looking to create lasting change—not just projects—I help organizations:
- Engage people at all levels in sustainable improvement
- Shift from fear of mistakes to learning from them
- Apply Lean thinking in practical, people-centered ways
Interested in coaching or a keynote talk? Let’s start a conversation.
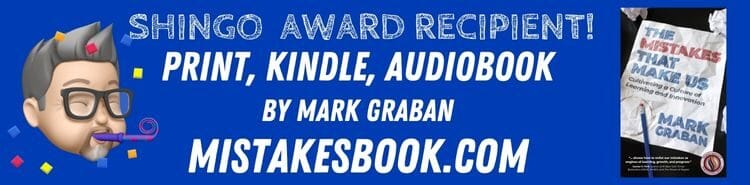
I guess I’m not off base:
Mark – I found the reference of the Kyushu plant video. I wrote about it in the Lean Post article “Lean in Japan: The Benefit of an Outsider’s View”:
http://www.lean.org/LeanPost/Posting.cfm?LeanPostId=477
“It’s human nature to resist change, or at least to feel uncomfortable with it. I was reminded of this at the Kyushu Toyota plant tour where I saw a video explaining the history of the Toyota Production System. When Taiichi Ohno first tried to implement new management principles of Just-in -Time and Jidoka to the Toyota employees, it wasn’t easy because “people were reluctant to give up their old processes.” This quote really resonated with me. Change is hard! Ohno had to be out on the floor and support this people to overcome their resistance to the new management approach.”
I think I mentioned this in our podcast discussion too. Thanks for inviting me to be part of the Lean Blog. It’s always great talking with you and I appreciate your thoughtful (and thought provoking) posts such as this one.
-Katie
Thanks, Katie. I wonder how much of it was just general “resistance to change” vs. “we’re different, we don’t build weaving looms!”?
Either way, I think the key lesson is that Ohno was “out on the floor” and he supported his people. Managers can’t just blame people or label them as being “resistant.”
Resistance is pretty often due to a lack of leadership or a lack of understanding (which could be due to a lack of leadership).