I've been overdue in writing more posts about our Japan tour that took place two months ago now. See previous posts in this series. I'm going to try to do one post a week on this topic.
It's always fascinating to visit a Toyota plant and it's even more so to visit with healthcare professionals. I've done this a number of times here in San Antonio (as I wrote about here). Often, this is the first factory visit a healthcare person has ever made. It's great to see through their eyes (and I still learn every time too).
Listen to Mark read this post (learn more and subscribe via iTunes):
Factory Roofs & VSM Icons
One thing I noticed, as our bus approached the Toyota Tsutsumi factory is the shape of the roofs in the area. I don't know exactly what building is pictured below, but it looks just like the typical factory / supplier / customer icon that's used in value stream maps.
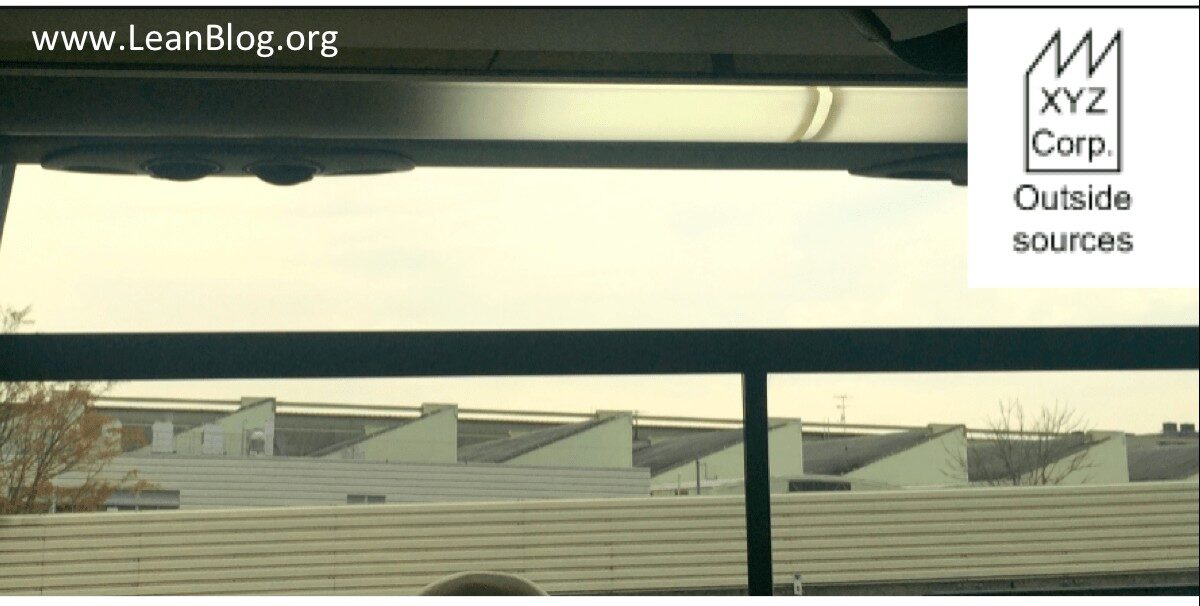
I've been told the roofs are shaped like that to help let in natural light. It's called a “saw-tooth roof,” actually, and it's not just a Japanese design. The buildings pictured there date from the mid 20th century.
What is TPS?
Our group of healthcare leaders and physicians from around the world learned about the Toyota Production System straight from the source. After spending time in the visitors center, we were guided through the factory. Our guide explained their philosophy is “customer first,” which would be “patient first” in healthcare, of course.
Our guide (read about her Kaizen in this previous blog post), also explained that TPS is:
- Just In Time: make what's needed, when it's needed, in the right amount
- Jidoka: build in quality, never send defects on
Jidoka was later described as “the harmonization of man and machine.” A picture from the visitor center:
A picture from the San Antonio visitor's center:
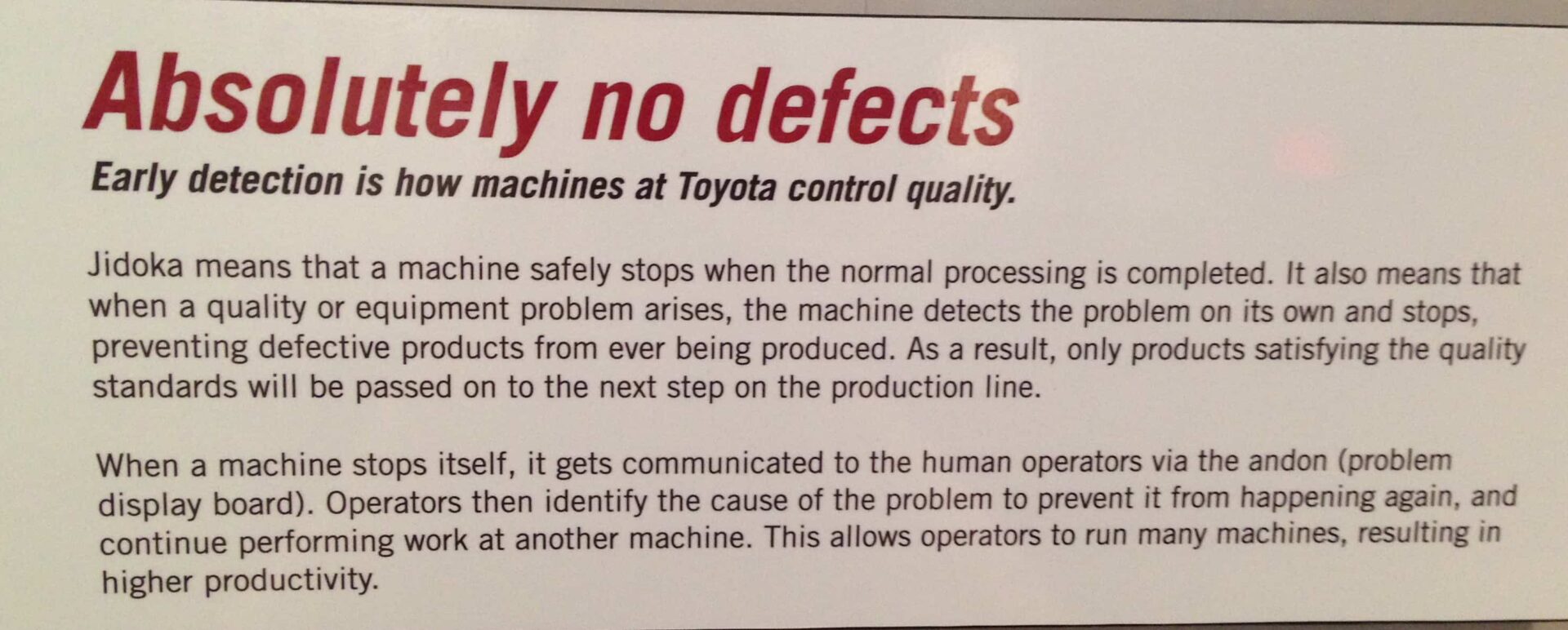
These are two core concepts, JIT and Jidoka, that should be the aim of Lean healthcare. In this case, it's the right care (with the right quality) at the right time. We sometimes use automation and machinery (and software) in healthcare, but there's a large human element in healthcare (as there is at Toyota). As at Toyota, we need technology AND processes and systems to help ensure quality when things aren't completely automated.
Patient flow and quality support each other just as JIT and Jidoka support each other in a factory.
Speaking of flow, during our introductory lecture the morning of this tour, Masaaki Imai (who traveled with Taiichi Ohno, one of the creators of TPS), commented that:
“Shortening the flow is the best way to reduce cost.”
This means working on reducing interruptions and delays in care and reducing waiting times for patients. That's different than a traditional “cost cutting” focus that healthcare organizations tend to have.
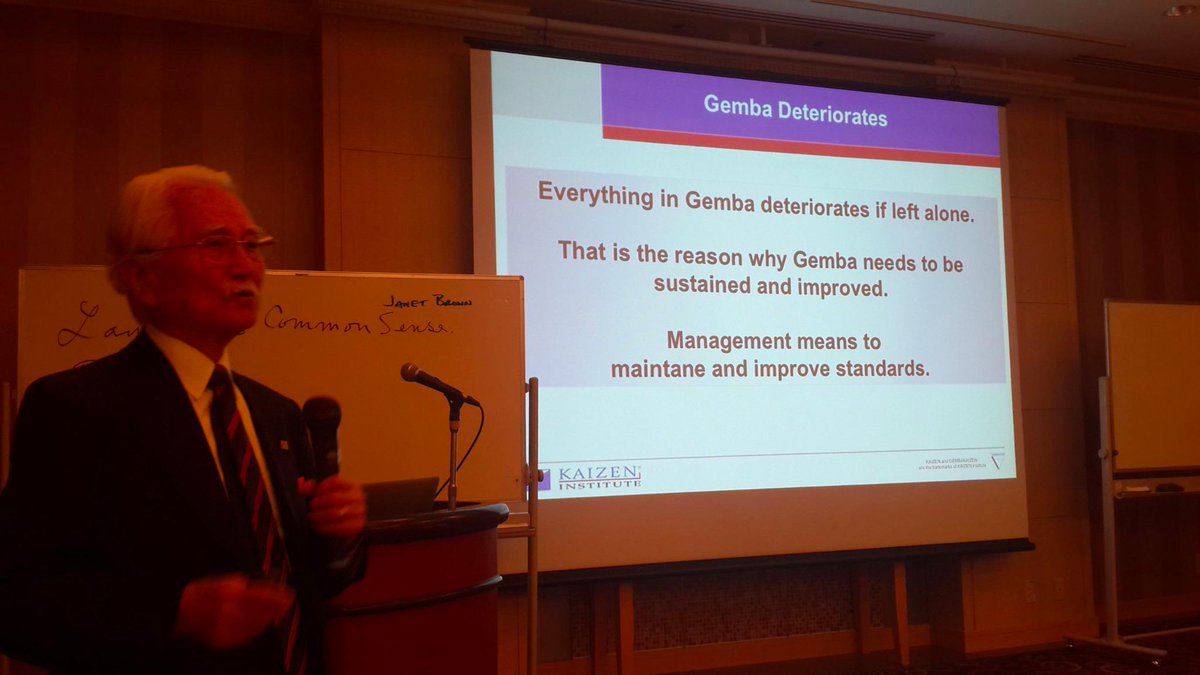
An Eco-Plant and Green Kaizen
It's appropriate for the plant to have a strong environmental theme, since the plant builds the hybrid Prius, along with Camry and Premio (Avalon) models. The plant, by the way, produces 370,000 cars a year, or 1,300 a day on two shifts.
Visitors could, by the way, see the heijunka, or level loading, principle at work. The cars rolled down the line as a flow something like: Prius, Prius, Camry, Prius, Prius, Camry. There were probably some Avalons mixed in and I don't know the exact mix of production. But, the healthcare visitors were impressed that the assembly line can handle variety and doesn't produce big batches of Priuses before switching over to Camrys.
The plant has a slogan:
“Eco-cars are the product of eco-plants and eco-people.”
The plant:
- supports the planting of 50,000 trees a year
- uses 12,000 solar panels to generate half of the electricity used by final assembly
- paints the walls with “photo catalytic paint” that helps clean the air
- uses an innovative lighting system to funnel sunlight through reflective tubes to the shop floor, supplemented with light bulbs
- has a roof-top garden
- recycles extensively
There are technological innovations, but they also emphasize what they call “Eco-Kaizen,” or the continuous improvement of environmental factors through employee ideas.
Toyota implemented 430,000 ideas driven by employees in Japan over the past year, we were told. With 68,000 total employees in Japan, that's about six Kaizens per employee. The video in the visitor center described Kaizen and how the “plant is always evolving.”
Part 2 of this post will be published next week. Please check back!
Please scroll down (or click) to post a comment. Connect with me on LinkedIn.
Let’s work together to build a culture of continuous improvement and psychological safety. If you're a leader looking to create lasting change—not just projects—I help organizations:
- Engage people at all levels in sustainable improvement
- Shift from fear of mistakes to learning from them
- Apply Lean thinking in practical, people-centered ways
Interested in coaching or a keynote talk? Let’s start a conversation.
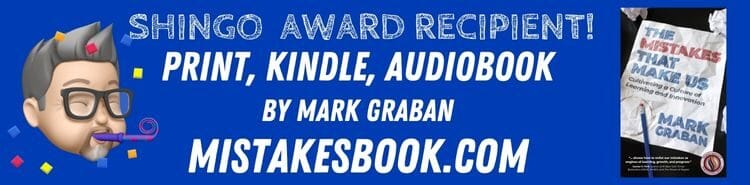
The saw-tooth roof was probably most popularized in the US by Ford’s architect, Albert Kahn. Once freed from belt-driven machine tools, factories could be laid out across one floor, which meant flat, square buildings instead of four-story, skinny rectangular ones. Long skinny buildings had lots of windows on the sides. The saw-tooth allowed modern factories to get back some of the light lost when they went square.
Of course, on one floor a factory is flexible and efficient for material handling and process improvement.
My favorite observation of this “in the wild” was in Lewiston, Maine where a series of abandoned textile mills line the river. The last mill to close in Lewiston was not the newest mill–a multi-story mill from the 1920s–it was Bates Mill Plant No 5, designed by Albert Kahn in 1914, a one-story highly efficient, saw-tooth factory that operated through the 1980s. Kahn, influenced by the auto industry in Detroit, brought the innovation back east too little too late. Others continued to build old style mills after Kahn.
In the 1960s when cheap TVA power and southern labor were combined with new factories in the Carolinas, most New England mills were abandoned.
Thanks, Andy!
[…] Looking back at the Toyota Tsutsumi plant tour, part 1 […]
[…] week, I wrote a post (part 1) looking back at our visit to the Toyota Tsutsumi factory that was part of our Japan tour that […]