Ken Congdon at Healthcare Technology Online recently interviewed me for this story that's now online: Kaizen: The Key To Lean Healthcare?.
Mark Graban, lean expert and co-author of an upcoming book titled  Healthcare Kaizen, often compares Kaizen to the suggestion box methodology.
“Traditionally, suggestion boxes have employees submit anonymous ideas,” says Graban. “Those ideas are then reviewed by a committee on a monthly or quarterly basis and are either implemented or dismissed. The individual who submitted the idea rarely gets any feedback on their idea.
Kaizen, on the other hand, is a local process that moves much faster than the suggestion box approach. Someone in a workgroup will talk to their supervisor about a change they feel should be implemented. These ideas are either collected on a bulletin board or entered into a web-tracking system.
Rather than running these ideas up to a committee, the employee who made the suggestion and their supervisor are empowered to implement these changes on their own. Â
The idea of Kaizen is that a lot of little ideas evaluated and implemented at a local level can have a huge impact on an organization and can generally be implemented much more quickly and easily than a single million-dollar idea handed down from corporate.”
Read the whole article here. Your thoughts? Leave a comment here on the blog post… and don't forget this week's charity auctions of Lean books and more.
Full Article:
Kaizen: The Key To Lean Healthcare?
By Ken Congdon, editor in chief, Health IT Outcomes
Now, more than ever, hospitals are being expected to do more with less. The pressure to operate more efficiently will only increase when (or if) healthcare reform goes into effect. Reimbursement changes and cuts will place a significant strain on hospital budgets and challenge the industry to streamline operations. This reality is forcing some hospitals to lay off staff and close clinics or other associated facilities. Others have focused on deploying health IT solutions as a means to maximize efficiencies. There's no question that several of today's health IT solutions can go a long way toward helping a hospital optimize workflow, increase productivity, and reduce costs. However, as the old adage states — even the best technology will do you little good if the underlying processes are broken. That's where lean methodologies come in.
Lean methodologies are geared toward continuous process improvement, and there are two predominant lean schools of thought — Six Sigma and Kaizen.
Mark's comment: Six Sigma is not a “Lean school of thought” – it's perhaps related, but a different methodology than Lean.
Both philosophies are focused on improving processes by eliminating waste and reducing defects. Both have also been credited for saving corporations billions of dollars over the years. However, each takes a slightly different approach to achieving this outcome. For example, Six Sigma incorporates more statistical analysis than Kaizen, focusing on eliminating defects so that a final product is as close to perfection as possible. Kaizen, on the other hand, looks to improve all aspects of a business by standardizing processes and eliminating waste. The Kaizen philosophy also strives to include every employee — from corporate executives to entry-level workers — into the process improvement initiative.
Applying Kaizen To Healthcare
Kaizen stresses that the real experts in any organization are the people that actually do the work each day, and these employees should be intimately involved in improving their own workflows. In healthcare, this could be a nurse in the emergency department, someone working in finance, a surgeon in the operating room, or an IT executive. Each of these folks face their own unique challenges and frustrations, and each have their own ideas for how their specific workflows could be more efficient. Kaizen aims to empower these workers to implement these changes, rather than waiting for a fix to be handed down from upper management.
Mark Graban, lean expert and co-author of an upcoming book titled Healthcare Kaizen, often compares Kaizen to the suggestion box methodology. “Traditionally, suggestion boxes have employees submit anonymous ideas,” says Graban. “Those ideas are then reviewed by a committee on a monthly or quarterly basis and are either implemented or dismissed. The individual who submitted the idea rarely gets any feedback on their idea. Kaizen, on the other hand, is a local process that moves much faster than the suggestion box approach. Someone in a work group will talk to their supervisor about a change they feel should be implemented. These ideas are either collected on a bulletin board or entered into a web-tracking system. Rather than running these ideas up to a committee, the employee that made the suggestion and their supervisor are empowered to implement these changes on their own. The idea of Kaizen is that a lot of little ideas evaluated and implemented at a local level can have a huge impact on an organization and can generally be implemented much more quickly and easily than a single million-dollar idea handed down from corporate.”
According to Graban, there are several ways Kaizen can be applied in healthcare settings. For example, an ER nurse may notice that one of the reasons for discharge delays is that physicians batch the orders they send to the lab. This often forces the first patient seen to wait around for another four or five patients to be evaluated before any of their paperwork is processed. In a Kaizen environment, this nurse could point out this problem and, together with their supervisor, suggest and implement an alternate workflow where physicians chart each individual patient immediately following their visit. The entire ER team would then evaluate whether or not the new workflow helped reduce discharge delays.
Making workflows more efficient through Kaizen can do more than just decrease patient wait times, it can also save lives. For example, inefficient workflows can often be the cause of hospital acquired infections (HAIs). A classic example is incorrectly inserting an IV or central line. There are a set of supplies that clinicians need to gather to correctly insert an IV. This process can often be time-consuming and burdensome for a clinician. As a result, a nurse may cut corners and insert an IV without all the prescribed draping or other supplies. These shortcuts can lead to infection. A simple, low-cost Kaizen idea would be to eliminate the wasted time associated with tracking down supplies by gathering everything that is needed to start an IV and place it all in the same shelf in every room. This eliminates the need for staff members to run from room to room to locate the supplies, and decreases the risk for HAIs.
As you can tell from the examples outlined above, Kaizen isn't rocket science. To the contrary, it is rooted in common sense. However, many employees don't feel empowered to implement changes in their organizations, even if they are common sense solutions. Kaizen puts a structure in place that provides employees with this power. Kaizen changes are often small, but when instituted in masse they can make a huge difference. For example, Joseph E. Swartz, Director of Business Transformation at Franciscan St. Francis Health of Indianapolis and co-author of Healthcare Kaizen, estimates that his facility implemented nearly 4,000 Kaizen ideas last year that resulted in a multi-million dollar impact to the hospital's bottom line. If you aren't already leveraging Kaizen or other lean methodologies in your healthcare facility, perhaps it's time you gave them a try. Going lean could provide you with the added efficiencies and budget you need to make the best use of the IT solutions you choose to implement.
Please scroll down (or click) to post a comment. Connect with me on LinkedIn.
Let’s work together to build a culture of continuous improvement and psychological safety. If you're a leader looking to create lasting change—not just projects—I help organizations:
- Engage people at all levels in sustainable improvement
- Shift from fear of mistakes to learning from them
- Apply Lean thinking in practical, people-centered ways
Interested in coaching or a keynote talk? Let’s start a conversation.
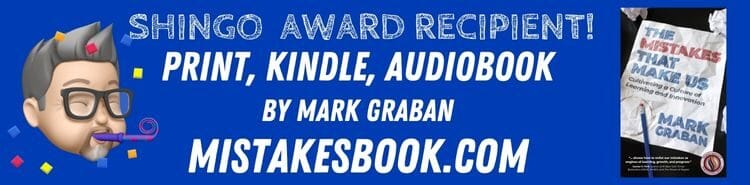
I really like the idea of kaizen and the speed with which it can allow improvements to be implemented and enable employee empowerment. What challenges are you seeing in healthcare to that approach? Kaizen is almost a disruptive methodology, and I think this is where the need for major culture change becomes apparent.
Hi KeAnne — we cover this on our book, some of the frequently stated barriers to Kaizen.
There are two major ones:
1) “We don’t have time” — a more accurate statement might be “we aren’t making time.”
2) Managers or leaders have been conditioned to think they are the only ones who can come up with improvement ideas, not the staff.
Kaizen isn’t complicated, but it sometimes requires an attitude adjustment… and the willingness to put in the effort to make it happen.
Mark,
As you may know we are working on daily kaizen in our PICU at East Tennessee Children’s Hospital. We are trying to get away from just a project based program where the “lean guy” or management is still solving all of the problems. We’ve had success with physicians, nurse practitioner, educators, nurse managers and other formal leaders conducting problem solving but have still not “cracked the nut” on frontline staff being involved with problem solving and daily improvements. We are however getting great ideas from frontline staff on ideas for problems to solve. All that said here are my questions that come from your statement, “the employee that made the suggestion and their supervisor are empowered to implement these changes on their own”.
1)Are you suggesting that frontline employees always work with their supervisor to solve these problems?
2)Is it too much to ask of frontline employees to do it completely on their own during the course of work?
3)How can a hospital from a management side create the environment and time for staff to problem solve? We have thought of setting an expectation and providing 4 hours (or any set period of time) a month for staff to spend on problem solving and call it the “4 Hour Challenge”. Instead of staff going home or floating to another department when census is low, they use that time for problem solving.
4)What role does upper management (CEO’s, VP’s & Directors) have in promoting daily kaizen or should if primarily be middle management (Unit/Department Managers and Assistant Mangers)?
Isaac – thanks for sharing what you and your organization are working on. Great questions.
1) Not “always.” If things can be addressed locally, then we want the employee and supervisor to work on the PDSA cycle (drawing in team members, as appropriate). Kaizen is never a solo activity. There are some problems that need to be escalated to higher levels in the organization or other departments. Leaders balance “empowerment” with “servant leadership” as required. Early in a “quick and easy kaizen” program, we want people to focus on things they can improve rather than only lobbing suggestions upward.
2) Again, we’re not asking them to do it “completely on their own.” Leaders need to help create time and support and coach people. This is a collaborative improvement process, we’re not just dumping work on people.
3) YES! Instead of sending people home, do Kaizen. When people say “we don’t have time,” we have to figure out how to make time.
4) This is chapter 9 of our book, and leadership is discussed throughout. All levels of leaders can encourage kaizen, practice it in their own work, coach it, and recognize it. The CEO can recognize people for doing kaizen in ways that are different than front-line leaders, of course.
Your questions might be good additions to the “FAQ” page on our website… so thanks.
http://www.hckaizen.com/about-the-book/faq/
Thanks Mark. Do I need to add them to hckaizen.com or will you? I’ve got several completed A3’s, Wall of Fame Pictures, Idea Board layouts if you would like copies of them.
I have modify the FAQ. Please test the “submit a kaizen” feature though, if you will, to help test that out.