First off, a huge thumbs up and thanks are due to Eric Ries and his thought-provoking “Startup Lessons Learned” conference on the “Lean Startup” methodology that was held Tuesday. I am thankful that Eric made live streaming video of the conference available for free to groups that met up around the world (including our group in Dallas). Please thank him by pre-ordering a copy of his book The Lean Startup via his website or via Amazon). I also made the notes I took available via Google Docs. (Some other good notes here).
This post is about one little thing that Eric said during his opening remarks, the notion that time and motion study, as a practice, has been “discredited.” I'll argue it's important to not throw away this crucial tool for manufacturing and healthcare improvement – but we need to understand what related mindset should be discredited.
Here is video of Eric's excellent talk (which is worth watching for many reasons, even if you're not involved in a startup)…
RATS. The video is not available anymore in November 2014.
Taylorist Time Studies
At one point, he correctly calls out Frederick W. Taylor, one of the fathers of industrial engineering, to criticize his outdated separation of thinking and doing, that improvement was only to come from the educated expert class. Taylorist mindsets are very embedded, even 100 years later, in MBA education and common business management mindsets.
Many industries are still attempting to recover from the Taylorist mindset by, among other things, adopting the Lean mindset that improvement is for everybody – that those doing the work need to be the ones improving their own work. Unfortunately, many organizations are still based on the Taylorist approach, without any attempts to correct course.
Many of Taylor's approaches contributed to the Toyota Production System and Lean. But, many of Taylor's management mindsets should be discredited – namely this separation between thinking and working. Taylor wrote that the man doing manual labor must be stupid (and “phlegmatic”!), otherwise he wouldn't be doing such work. Again, a pretty outdated concept and a polar opposite of the Lean “respect for people” view.
Here's a photo of a classic stopwatch wielding time study man, from an old Ford video…

Taylor and Frank Gilbreth, the other father of industrial engineering, used time and motion study. Their time and motion study seems to be all about the expert observing others and that expert dictated what changes should be made to the work. The people doing the work had change forced upon them. Many organizations still rely far too much on experts to tell workers what to do. Time and motion study was also, unfortunately, used to set production quotas. This created pressure for people to “hit the numbers or else,” and as Dr. Deming taught us, this hurts quality and demotivates people.
Lean Time Studies
I'd like to report that time and motion study is alive and well and it's being used to great benefit. I believe the difference that makes this “lean time and motion study” (if you will) is that experts are teaching the people doing the work to do time and motion study on their own work (as part of a broader Lean education approach). The people doing the work are then the ones to develop their own improvement ideas, often based on the insights they come up with after being taught Lean principles.
I've taught nurses, laboratory technologists, physicians, pharmacy technicians, and other healthcare professionals how to do time and motion studies on their own work and within their own teams and departments. This time and motion study helps people identify waste and unnecessary variation in their work and it also helps them see how different roles fit together (or don't fit together) in a system (or a non-system).
There's nothing wrong with time and motion study when you're applying it to your own work or when it's peer-to-peer. People can use videotape (as Gilbreth used film) to analyze work – except in the Lean mindset, we let people watch the videotape so they can see themselves working – and they can (and do) come up with ideas for improvement.
A Doctor Time Studies Himself – Patients Win
I've blogged about a Dallas cosmetic surgeon, Dr. John Tebbetts, before and I mentioned he use of Lean methods in my book, Lean Hospitals. Dr. Tebbetts applied Lean methods and used time and motion study to videotape his own work in the operating room. He used the videotape to identify wasted motion that just took up time or caused internal bleeding or trauma to the patient.
Shorter surgeries, by eliminating waste (not working faster), means less time under anesthesia and faster, less painful recoveries for patients (and fewer infections). It also means he is more productive as the surgeon. He has published this work and the results in peer-reviewed journals.
Dr. Tebbetts initiated his own time and motion study out of his own motivation to improve. His patients benefit, he benefits – it's win-win. Time and motion study is great, *if* it has the Lean mindset and not the Taylorist approach.
“Subject” or “Scientist”?
One other comparison was found in an article published in the journal for the Society for Hospital Medicine last year. In one article, the University of Michigan Health System used industrial engineering students (correction: “undergraduate business administration students”) to shadow hospitalists (physicians), performing time and motion studies. One thing that made me raise an eyebrow was that the students timed how long hospitalists were in the bathroom. It raised the issue of whether these students were being little Frederick Taylors.
I co-authored a companion piece that was published in the Journal with Amit Prachand, a former industrial engineering classmate of mine from Northwestern University, who now works in process improvement at Northwestern Memorial Hospital in Chicago.
We asked this question:
Were the hospitalists playing the role of “subject” or “scientist” in the time and motion study?
We couldn't tell because we weren't there, but we wanted to raise the issue so that other hospitals would consider the Lean approach over the Taylorist approach.
The hospitalists would be “subjects” if they were merely observed by the outsiders. They would be “scientists” if they were engaged and involved in the improvement of their own work.
Which of those approaches better exemplifies Toyota's “respect for people” principle?
So, please, don't throw the tool out with the old mindset… time and motion study still has an important place – just use it the Lean way. Teach people to do their own and don't use the data to create quotas that must be hit – especially in relatively high-variety settings, including healthcare.
Please scroll down (or click) to post a comment. Connect with me on LinkedIn.
Let’s work together to build a culture of continuous improvement and psychological safety. If you're a leader looking to create lasting change—not just projects—I help organizations:
- Engage people at all levels in sustainable improvement
- Shift from fear of mistakes to learning from them
- Apply Lean thinking in practical, people-centered ways
Interested in coaching or a keynote talk? Let’s start a conversation.
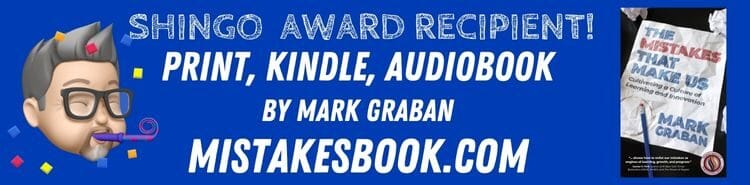
Hi Mark,
Don’t forget Allan Mogensen’s breakthrough work in integrating time & motion studies, suggestion systems and Gilbreath’s work into the Work Simplification programs. These resemble the Job Methods programs which were exported to Japan and likely influence Kaizen Teian system development through the fifties and sixties in that country.
Historical Footnote: Time Studies in the workplace were the target of a legislation, aiming to ban the management practice, sometime in the late 40s. The effort to strike down this legislation was led by my home state senator from Vermont, Senator Ralph Flanders! Yeah!
Mark, thanks for pointing out the importance of attitude. I think that attitude makes all the difference in many processes.
I’ve found that some software Quality Assurance folks think their job is to point out developers’ flaws. Other folks think their job is to help the team deliver the best quality product to the customer. Much of the work they perform is the same regardless of attitude, but the results are very different.
I can think of some situations where I’ll use the “‘Subject’ or ‘Scientist'” concept in the future.
Great point Mark:
Bill Kerber and I mention in our book, Lean Supply Chain Essentials – A Framework for Materials Managers, how time studies can be used to help in determining labor costs in the warehouse…probably the second highest cost, aside from inventory.
We fashioned this after what the two of us used to do as operations consultants – Short Interval Scheduling. This got supervision out on the shop floor and constantly monitoring production and production issues. We found that this could be adapted to the warehouse quite effectively, where there typically wasn’t much real lean going on.
Our most important process observations are done with our hands in our pockets – no stopwatch, no clipboard! Training a team to study their process, this is always part of the lesson. Start out just watching (and next, watching and asking questions). This way we can see the process and the waste and aren’t distracted by the digits flying by on the stopwatch or making records on the clipboard.
As you observed, video is great for the same thing. You don’t need to quantify waste to eliminate it, you just need to see it and understand it. The need in some organizations to report explicit improvement results in terms of time (and thus money) drives some of the need for (obsession with?) stopwatches. A rough quantification of value adding time vs. waste in a time-value map is good for a team predicting the outcome of planned changes, but this is more important as an exercise in the discipline of P-D-C-A than as a measurement of waste.
We do take a lot of times, however: timings are essential for planning – cycle time (in conjunction with takt time) drives cell or line design and staffing, and is essential to our understanding of capacity.
When it comes to refinements like line balancing in daily work, visual information is better than stopwatch digits. Who is waiting? Who is overburdened? All you have to do is look. And if we have done our job as leaders and teachers, the people on the line see and respond to this, moving up and down the line (or across the cell) as pace and problems demand. No stopwatch necessary.
Timing visits to the bathroom? For the sake of the I.E. students involved, I hope we are missing some context here! Our task is to lead improvement in systems that create value. Things like bathroom breaks, a place to hang your coat and leave your purse, time for a stretch and drink of water, are baseline requirements for people to do their jobs comfortably and without distraction. I suppose if we were looking at unit design and the bathrooms were inconveniently located there might be something to this. As I said, I hope some key context is missing!
Andrew – I agree absolutely. I should have elaborated in the post, but as I describe in my book, this process observation is often qualitative – see the work, see the flow and identify waste. We use detailed time study for more specific questions, like determining the number of microbiologists we need reading plates each shift.
It’s not always “stopwatch and a clipboard,” the I.E. stereotype of yore (I am an I.E.). Once during this observation, an elderly female patient we met said to me, “Oh, you’re the time study man!!”. Quaint, old timey term, eh?
I agree with you. Most management concepts are applied poorly. Many of the concepts may also be bad. For example, performance appraisals are both done poorly and a bad idea. The solution is not to do them righter:-) http://management.curiouscatblog.net/category/performance-appraisal/
But many things that are done poorly and the actual application is criticized, with good reason, can be used successfully. I would put benchmarking and time and motion studies in that category. Most of the time it is done poorly and produces bad results. But it can be done right, and provide value, so long as you have the right management system surrounding it and execute well. In practice I think, one think that helps separate good managers from bad ones, is knowing how your organization will actually execute (not just dreaming about how nice things could be if only…) and not just trying things that they should know will produce bad results in their organization.
I dislike the blind application of time and motion studies or even simple line-balancing exercises (timing operting cycle time) that many Lean consultants preach in healthcare environments. For lab processes and many surgical processes, there is some merit. For medical diagnosis, assessments, consults, etc, I believe there is limited utility; yet the toolheads will often continue to apply and get frustrated when they can’t create “flow cells” in complex medical, emergent, or psychiatric environments. At what point do we acknowledge that the approach isn’t applicable to “every process” irrespective of industry? Agree/disagree?
Thanks for your comment and question. Nobody here is advocating blind application of any specific tool.
What’s applicable “anywhere” is teaching people how to observe their work and to identify waste and process improvements. If there’s a reason to quantify it and something good that can come from the data, then great.
The goal shouldn’t be to “create a flow cell,” the goal should be to improve safety, quality, access, cost, and staff morale.
Going in with solutions like “we’re going to create a flow cell” isn’t a good idea.
There are settings where a flow cell isn’t the right approach. That doesn’t discredit flow cells, in a general sense. Agree/disagree?
Mark/Anonymous,
I think far more of the creative/thoughtful work that people do can be standardized and turned into flow than most people realize. Take our blogging efforts. If you are anything like me, you have processes out the wazoo (techinical Lean term) that support your writing–where you store reference articles, how you set up your workspace, the schedule you keep, etc. You probably have posting shortcuts, technical improvements on your site’s software, and an editing process. You may have a checklist on how to keep from missing steps, or how to get the best search engine results with your articles. You probably work to create better flow by limiting interruptions and working on tasks to completion rather than bouncing around. And I am assuming you work to reduce setup time on getting changed over from consulting mode to blogger mode.
But “writer” isn’t a profession that pops to mind when one thinks of Lean, just as diagnostics isn’t. While I don’t advocate blind usage of tools, I caution people against blindly dismissing them as well. While approaches and tools are not applicable in every situation, I have yet to see a situation where basic principles of continuous improvement and waste reduction do not apply.
Nice article, by the way. Just downloaded Taylor’s book on my Kindle. I’ve been in a ‘back to the classics’ mode lately. Re-read some of Shingo’s and Deming’s work, and now diving back into Freddie’s book.
Couldn’t agree more. Learning to see waste is applicable everywhere. Creating a flow cell should never be the goal of an improvement, and there are settings in which flow cell isn’t the right approach. My experience is that some lean advisors are more interested in demonstrating some “holy grail” of lean in an environment instead of focusing on the real goals of improving patient care. Has anyone else experienced this?
No, I have not experienced this. It might be happening, but I can’t imagine that can be too widespread.
Mark,
Paraphrased from one of my old blogs: (apologies for being lazy)
I still see the ghost of Frederick Taylor at different organizations around the world in the form of Work Standards. Work Standards are an anachronistic method for measuring hourly employees’ performance. Typically, an Industrial Engineer, with stopwatch in hand, will determine how long it takes a nervous and distrusting individual to perform a task or process. After some manipulation of the data (an ambiguous process), a Standard is established. There are a few problems with the Work Standard and the way companies use it:
1. The standard is set by “someone else”. Most people don’t trust data developed by other people. If you want someone to believe something, they have to be a part of developing it.
2. The intent of the practice is to measure a person and not the process. Although this might make it easier to conduct performance reviews, it dehumanizes the work force and results in no improvement. If you believe, which I do, that most people come to work with a desire to succeed and do well for the company, how can you believe that “missing” the standard is the the fault of the individual?
3. It leads to distrust and more waste. If you measure people’s performance on a standard of time, and base their performance and compensation on that number, their goal becomes to ensure the number is attained. Unfortunately, it becomes common for people to manipulate the system in order to succeed. No one cares if the process has been addressed or not, because the focus is in the wrong place: the numbers.
4. Scientific Management does not support “respect for people”. Quite the opposite.
I have seen what this environment looks like and it isn’t healthy. At one company, we estimated that 5-10% of each employee’s day was spent “managing” the standards. That includes the time keeping, the reporting, the manipulation of the time codes, and more. The question I ask Management is, “Imagine what we can do with that 5-10% of their time that will actually benefit your company.”
Yes, that’s a perfect elaboration on my point: “Time and motion study was also, unfortunately, used to set production quotas. This created pressure for people to “hit the numbers or else,” and as Dr. Deming taught us, this hurts quality and demotivates people.”
What you describe is exactly the old style that should be discredited.
Teaching hospital people to do their own time and motion study is all about identifying waste and helping make sure they have enough staff to get the job done properly (at the best quality level), not about setting draconian standards. I think we’re on the same page there, but just wanted to make sure.
I have a stopwatch at work but only bought it as a toy/decoy and a threat to recalcitrant managers who claim that their staff’s timings are wrong. The stopwatch is there so I can time THEM doing the same job. A little bit of Lean humiliation of those who don’t trust their staff can go a long way.
We had a celebrated case where the guy tried the trick of saying ‘that [wasteful, time consuming practice] doesn’t take anywhere near as long as what [his staff] claimed’. He was intimidated out of his bizarre belief by his peers, managers of the same rank at other offices who were inclined to agree with the staff. But for effect, got the stopwatch.
It’s one thing to talk respect for staff – but I have limited respect for managers who themselves have no respect for staff.
Slightly off topic, but had the silliest experience yesterday I’ve had yet as Lean practitioner. Went to a meeting with some middle managers and pointed out how much waste we’d seen on the front line due to poorly directed phone calls. One tried to deny it, and asked what evidence we had. I said “Spoke to both the operators and the receptionists”
The middle manager was absolutely horrified that I’d spoken to the receptionist. I’d broken some code of honor or something – I don’t know. What could the receptionists possibly know about phone calls?
Mark, have you thought of doing a post on why some managers are completely un-humble and think they are the best thing since sliced bread? Is it the ‘self-esteem/self-affirmation’ movement? The Alpha-Males? To me this is the biggest threat to Lean, to efficiency and to a happy life in general.
I find myself too much in the company of managers who seem to think, like your ‘MBA’ above, that they know everything, there is nothing for them to learn, they must be better than everyone else because of the corner office and the car space and the pay grade.
I’ve found a natural transition from Lean into sites like the servant leadership stuff eg http://www.greenleaf.org
Surely it must be enough to have the corner office and the extra pay, without believing it must be because you are a superior grade of person, entitled to have the ground you walk worshiped.
If I can indulge my own schadenfreude, there are a few I’ve seen whose impulses seem little better than children’s: notice me, tell me I’m good, I’m nothing without your praise.
A barrier to working as a team to fix problems in processes.
Hi Richard,
Although I share your disdain for less-than-humble managers, let’s not forget that boorish people can be found at any status level.
I have found that when discussing observations with the experts in their workplace, i.e., the worker, less-than-humble behavior can be found there as well. Although this resistance is easier to work with over time than say with a fellow manager, it exists for some of the same reasons you describe above, sans preferred parking space, corner office, etc.
The problem that you describe, as I see it, is that these arrogant people do not have a leader.
Taylor and his disciples were interested in finding the fastest man or the one who could carry the heaviest weight, then setting their performance as the standard. This allowed the infamous speedups of automated lines – think Lucy and Ethel in the candy factory. That resulted in workers conniving at rate-busting, deliberately working slower when industrial engineers were around, or working fast to pile up production so they could knock off for an hour.
I’d suspect that in Taylor’s years, “stupidity” was a matter of speaking Polish or German rather than English, coming from the farm, perhaps with little education. Poor instructional methods added their effect.
Taylor also started the separation between engineer and operator. He said that the engineer needed to sit down to do his work so he needed a desk. He needed quiet so he needed an office. He needed to get away from the work rather than be close to the work.
This was part of the genesis of war between worker and management. I remember a friend who was beaten up in the parking lot after accepting a promotion to foreman from line worker.
Toyota, and others no doubt, realized that industrial engineering principles are not that esoteric, and put them in the hands of workers. They allowed them to use tools like time and motion studies to find work methods that fit typical human capabilities and the pace of production required.
People learn. They can learn how to execute a slowdown, or how to improve a process. They can learn some of the legendary (perhaps mythical) tricks of the seventies, like leaving a soda can inside the door of a vehicle or finding a good spot for a nap, not to mention selling drugs or stashing a bottle of Jack Daniels somewhere handy. Or they can learn something with more intrinsic value, like being a part of an organization that produces a product to satisfy a paying customer and ensure a future livelihood — if they have the respect and attention of managers.
Fred Taylor was most interested in finding the ‘best’ tool for a task, or the most well suited person for a job.
During his time at Bethlehem Steel, Taylor came to loathe the ‘work gang’ concept under which bosses would gather men, with little or no regard for their physical abilities, and place them into impossible tasks. Most work gangs were independent contractors whose workday, and pay, depended upon being chosen at the morning ‘shapeup’ outside the mill gates.
Recall, also, that the vast majority of jobs in a steel mill in Taylor’s era were unskilled, brute labor jobs that preceded mechanical conveyors or mobile equipment of our modern experience.
The infamous ‘Schmidt’ study was meant to illustrate that fewer suitably strong workers carrying 90 pound iron pigs at a slower pace would be more productive than having a gang of men not well suited for the task trying to do the work at breakneck speed. Being contractors, most gangs were task-based and were free to leave the job once the day’s required work was completed.
Of course, winnowing the ‘work gang’ down in size did not sit well with the work bosses who survived, for the most part, in a world of tribute and kickbacks paid by the workers to be ‘tapped on the shoulder’ at the shapeup.
In today’s workplace, companies go to great lengths to find the most appropriate worker; the one best suited for that particular job, and we may owe thanks to Fred Taylor for that.
Hi Synfluent – you’re certainly right that we shouldn’t discredit all of Taylor’s ideas. Some of the mindsets certainly seem to be of a different era… all the more reason to update things to a modern perspective rather than throwing out everything he ever developed.
Hi Mark,
Great blog. Thank you for asking me to put in a comment. I’m in full agreement on not separating ‘working’ and ‘thinking’. And I’ve actually practised what’s being preached by capturing the activities of a team on video and getting them analysed through a work breakdown sheet. The discussions we had with the team from both the video and the analysis made it possible to create a breakthrough in mental barriers from both the professionals as from managements point of view. I’ve tried to describe this process in my blog post (also in English) http://leanliefenleuk.blogspot.com/2011/05/lean-in-health-care-changes-in-gemba.html
Looking forward to seeing you at HCVLN in a weeks time!
Thanks, Freek. Looking forward to seeing you at the Summit in Seattle!
[…] Based on my comment on: Time & Motion Studies Are Not “Discredited,” Just How They Are Used […]
Mark Graban
Honestly, I did not read all the comments here – there are 23 of them now. It would take hours to read and makeout what they say. But I will mostly agree with all of them. I have been developing some such theory on the same lines – by marrying Lean mfg to Work Study and getting into what I call as “Modern Work Study’ which focus on improvements, rather than the ‘Worker’. Well, I had put up my whole work into an useful software called WorkPro.
Again, honestly I am trying to market it (!) by saying Work Study with Lean is the best way and ofcourse use my software ‘WorkPro’ !.
Just go to this website http://www.workstudy.in and send me and give your feedback. You will meet the site in its greenish form, well it needs lots of improvements !
Thanks & Regards
Renga Iyengar
[…] Retired General Stanley McChrystal writes about the change in military strategy that was necessitated by the battle against Al Qaeda and insurgents in Iraq. It’s a business book that paints a compelling picture of the need to be more agile instead of being big, powerful, and plodding. Sharing information and letting others make quick decisions is the key to success in today’s world. McChrystal also writes quite a bit about the harm caused by the “experts only” approach to improvement driven 100 years ago by Frederick Taylor (read a blog post of mine from 2011). […]
[…] As I’ve written about before, some hospitals or engineers working within them have taking old-style Taylorism to an unfortunate extreme, including timing how long doctors are in the bathroom. […]
[…] Time & Motion Studies Are Not “Discredited,” Just How They Are Used […]
[…] non-value-added time that surrounds the work. Timing people is fine if you have THEM participating (see my post) and if the goal is to figure out how to make work easier and results better… the goal […]
[…] because they’re wearing a suit and an expensive watch. That approach, though still common, is somewhat discredited and is not what we’re talking about […]