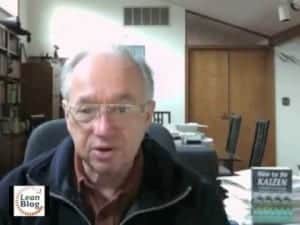
Here is my first LeanBlog Podcast, featuring author and consultant Norman Bodek, President of PCS Press.
I have to give credit for the idea to Norman, as he approached me about doing a series of audio interviews as a follow up to and continuation of our Q&A that I posted here on the blog earlier this year.
I'll take credit for turning it into a podcast, something that I plan on making a regular feature, every month or so. There will be additional conversations with Norman, and I also plan on interviewing other lean leaders and innovators.
Visit the main page for all episodes and information about how to subscribe.
LeanBlog Podcast #1 Show Notes and Timeline:
- Introduction to the Podcast (until 2:22)
- The difference between kaizen and kaizen events, early history of bringing the kaizen blitz (“kaikaku”) to America (starting at 3:18)
- Early development of employee suggestion systems (4:18)
- Difference between suggestion systems and “cost savings systems” (5:00)
- How Toyota started their suggestion system of “small, little ideas” (5:26)
- There is a point where the audio is poor, Norman says at 6:00, “…ideas per employee per year, one per month, one per month implemented idea per employee. So, that represented millions of ideas. In fact, I published a book once…”
- Norman mentions an early book, 40 Years, 20 Million Ideas: The Toyota Suggestion System, now out of print, but available used through amazon.com, albeit at a rare book price. Then, the audio improves again.
- How do you “manage 1800 ideas” per month? (6:40)
- Norman's experiences with Gulfstream and employee suggestions (8:30)
- How kaizen is not a bureaucratic system (10:40)
- What are the proper incentives for employee suggestions? (11:40)
- What are the two pillars of TPS? (13:05)
- How do you “keep score” with employee suggestions? (14:15)
- How do you balance between kaizen and standard work? (14:40)
- What is your role as a supervisor with employee suggestions? (15:40 and 22:30)
- How has Toyota changed their suggestion system over time? (16:50)
- Why giving $20 an idea was a problem (18:15)
- Proof that Toyota sometimes makes mistakes – but improves! (18:50)
- Focusing on “implementations” as opposed to “suggestions” (21:05)
- What happens when you criticize a suggestion? (23:00)
Quotes:

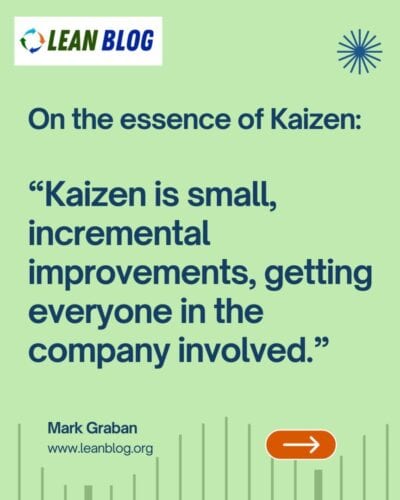
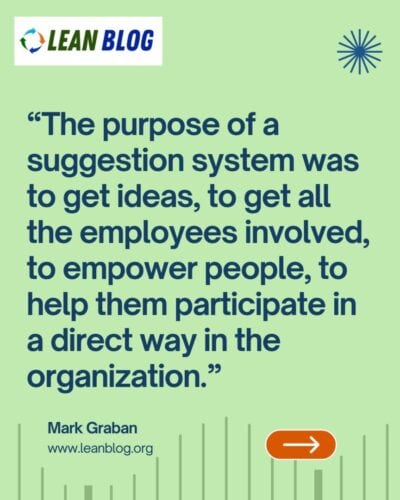
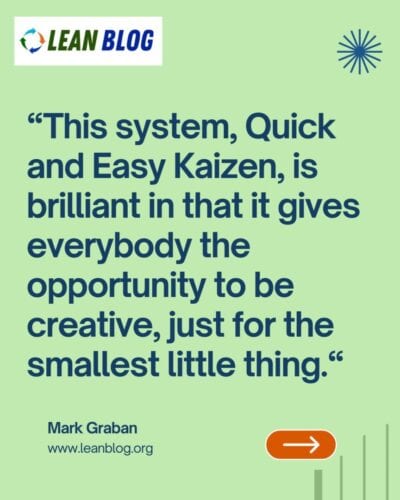
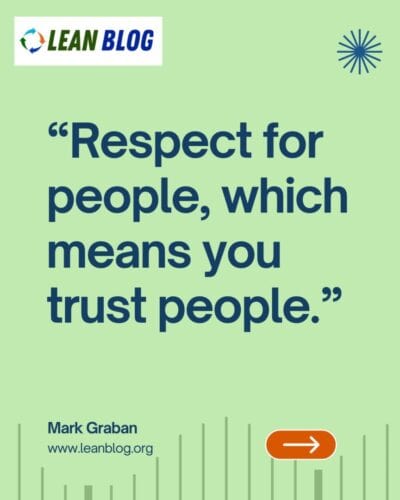
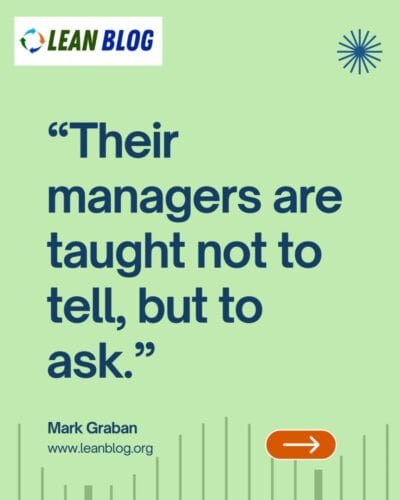
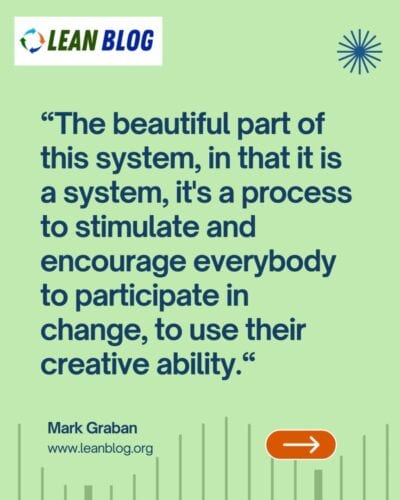
Here is a blog entry that Norman wrote about the podcast, with additional thoughts:
“Mark Graban interviewed me this past week for his first Podcast. We talk about my discovery of Quick and Easy Kaizen, how it was the heart of the Toyota system, getting all employees involved in continuous improvement. The puzzle to me is why every company doesn't add this most valuable process to their management lexicon. We say that “People are our most valuable asset,” but we do very little to develop that asset to its fullest.
China does represent short-term labor savings, but in the long term, we are giving away our companies to them. This week I was watching parts of the Tour de France bicycle race on television and saw one of the leaders on a Giant bike.
At one time, over fifteen years ago, Schwinn was probably America's leading bicycle company. They went to Taiwan to manufacture their bikes to take advantage of the low labor cost. The company in Taiwan was Giant. Initially, Schwinn wanted to reduce their assembly costs, but Giant convinced them to also save money on engineering and every other phase of manufacturing and design. After ten years or so when the initial contract was over, Giant told Schwinn, “We don't need you anymore. We know how to make great bikes, you taught us how.” All we have to do is learn how to market the bikes. Shortly thereafter, Schwinn went bankrupt and sold their “name” to another American company.
Unfortunately, we are great at short-term thinking. Toyota recognizes the threat from China but they are building more and more automobiles in America. If they can do it, why can't other American companies do it? To me, the only difference between Toyota and American manufacturers is that Toyota develops its people, and the best way to develop people is from their own creative ideas.
Please do listen to the podcast…
And give me some feedback,
Thank you”
Here is an amazon.com link to Norman Bodek's Books.
My announcer is my old friend, Steve Sholtes, a musician from Michigan.
Automated Transcript:
Are you struggling to recruit senior leaders because of compensation and relocation challenges? Stiles Associates, the premier executive search firm for lean leadership, has the latest data and insights you need to clear those hurdles and attract your industry's top talent. Go to leannexecs.com to view the free blueprint and transform your recruiting strategy. Thanks as always to Stiles Associates for being a long-term sponsor and supporter of this podcast. Again, visit their website at leannexecs.com.
Welcome to the Lean Blog podcast. Visit our website at www.leanblog.org. Now here's your host, Mark Graban.
Welcome to the first-ever Lean Blog podcast. This is Mark Graban, creator of the Lean Blog, and my guest today is Norm Bodek, one of the leading voices in the lean manufacturing world, and I'm very happy to have him here with us. But first, a little bit about this podcast. It's my first attempt. You'll notice I'm not a professional broadcaster; I'm a lean consultant.
I've worked with lean as an engineer and a consultant for about twelve years, and I started what was then the lean manufacturing blog in early 2005 when I was working as an internal lean change agent for a large manufacturing company. I continued the blog as I moved last August into a new role as a lean healthcare consultant working in hospital settings. And so the website evolved into what we call simply the Lean Blog because it's about manufacturing, healthcare, and aspects of lean that really do apply in any sort of industry. The blog has been a great learning opportunity for me. I'm hoping that this podcast will expand my learning, and I'm hoping that others will join me in that learning journey.
So this is the first of what I hope will be a monthly series of podcasts, each of them an interview with a leader or an innovator in the lean world. And today I start with Norm Bodek. He is the president of PCS Press, a publishing, training, and consulting company based in Vancouver, Washington. He discovered and published the works of the truly great Japanese manufacturing geniuses, Dr. Shigeo Shingo and Taiichi Ohno, the inventors of the Toyota Production System. From his numerous trips to Japan, he introduced to the Western world the Kaizen Blitz, Single Minute Exchange of Die (SMED), Total Productive Maintenance, Hoshin Kanri, Poka-Yoke, and other new manufacturing methodologies that have helped companies improve their quality and productivity around the world.
Norman has written countless books, including “The Idea Generator: Quick and Easy Kaizen,” and his most recent book, “The Power and Magic of Lean.” You can find more about Norman and his books at his website, www.pcspress.com. Norman, I want to thank you very much for being here on the first Lean Blog podcast. It really is a pleasure to have you here.
Norm Bodek: Well, Mark, I want to thank you very much for doing this with me. I think it's going to be a lot of fun. We'll talk about a lot of management issues. Hopefully, this will stimulate a lot of people out there to focus more on continuous improvement. And our first topic, we're going to talk about quick and easy Kaizen, what this means, why it's so important, and why I think it's the heart of the Toyota Production System.
Mark Graban: Well, I was hoping we could start off first by talking a little bit about the background of quick and easy Kaizen. That's the title of one of your books, of course. Tell us how you discovered that approach and how that might be different from what other people think of with Kaizen or Kaizen events.
Norm Bodek: Yes, they are distinctly different. It's a shame that Bob Hall and the other person changed the name. Originally it was called “Five Days and One Night.” I met Ohno's two chief assistants, Iwata and Nakao. They told me they were leaving Toyota and they wanted to come to America to teach us consultants. I said, fine, I'll bring you over and I'll run events for you. And I did. I brought them over, and they ran these events called “Five Days and One Night.” Then Bob Hall changed the name to Kaizen, the Kaizen Blitz, which is not appropriate because Kaizen really is small, incremental improvements. That's what Kaizen is. Kaizen is change. Kaizen is small, continuous improvement. Kaizen Blitz is really kaikaku, which is the name of my other book. Kaikaku means radical change. And that's what Kaizen Blitz is, a radical change. What Kaizen is, as I said, is small, incremental improvements, getting everyone in the company involved. The suggestion system I credit to Kodak back in 1898, and the first suggestion was to clean the windows. It's a wonderful idea. And the purpose of a suggestion system was to get ideas, to get all the employees involved, to empower people, to help them participate in a direct way in the organization.
But back then, in the late 1800s and early 1900s, people were just doing very simple, repetitive tasks, and the supervisor would not let the worker do these things. Very often when you do start a suggestion system, people come up with ideas for other people to do things, not for themselves. So it went from a suggestion system to a cost-saving system, where the average American company that had a system would get one idea every seven years. That's the statistics that were given by the American Suggestion System. That's per employee per year. So one idea every seven years. Toyota relooked at this in studying American management. They relooked at the American Suggestion System, and they said, we want to get all our employees involved. We're doing quality circles, which is putting people in teams. So teams are coming up with ideas, but how do we get everybody to come up with ideas, small little ideas to make their work easier and more interesting? They adapted at first the American system and slowly changed it. So the first year, I think Toyota started on this, they got one idea per employee for the whole year. After about ten years, they were up to 46 ideas per employee per year. One per month. One per month implemented ideas per employee. So that represented millions of ideas. In fact, I published a book once called “40 Million Ideas in 20 Years at Toyota.” 40 million ideas. Now, it's astronomical. When companies think of this, how can I manage those kinds of ideas?
In fact, I gave a lecture out here to a company in Oregon, and the manager had 900 people in the plant. And I said, you know, if I have my way, you could get two ideas per month per employee. And he said, no, when I have 900 people, I can't manage 1800 ideas. And he wouldn't go forward. It was so silly because you don't manage it. People manage it themselves. People come up with an idea, and they do it themselves. A lot of people do come up with ideas, and they implement them. But the beautiful part of this system is that it is a system, it's a process to stimulate and encourage everybody to participate in change, to use their creative ability. You know, most people have such boring, dead-end jobs in factories, and most people just hate to come to work. When I ask the question to audiences, what day of the week do you like? Almost everybody says Friday, Saturday, or Sunday. It never really happens if somebody says, I love Monday or Tuesday. They don't like work. And yet most of your life is spent at work. And the reason is because they don't have a creative opportunity at work. And this system, quick and easy Kaizen, is brilliant in that it gives everybody the opportunity to be creative, just for the smallest little thing. I gave a lecture on Tuesday with Sandia Labs in Albuquerque, New Mexico, and I kept misplacing my pointer. And then I said to the audience, what can I do? Help me. What can I do? And of course, right away, somebody says, you know, put a string on it or put a piece of Velcro on it or do something. There are so many clever ideas we can come up with to make our life so much easier. And so this very clever system became adapted by almost every major Japanese corporation. And the average in Japan is two ideas per month per employee–24 per year. I worked with Gulfstream Corporation in Mexicali, Mexico, and I went in there, I think it was about April of this year, a year ago when I first went there to give training, their goal was to get one idea per employee per year. They had about 1000 people. They wanted 1000 ideas. Prior to that, they were getting about one every seven years, just like the American average. Well, I ran a two-day course with them, and now they're up to 1000 a month. So they're getting one idea per employee per month. I'll give you one idea, just one idea. What they do at Gulfstream is they do the wire harnessing. That means they have people, predominantly women, wiring the inside of an airplane. It took these two women seven days to do their part of the wiring, to do this one harness, seven days to do it, and then they spend 4 hours to check it out. The way they check it out, they have to bend down under the panel. Visualize the panel as the size of an airplane wing. So they have to bend down under the panel, and they pull out these plugs, about 50 plugs. They take a plug and connect it to the panel to check that their wiring was correct. So it took them 4 hours every seven days to do that. Well, after my course and asking the people to make their work easier, this one woman came up with the idea, instead of bending down, why can't we take all the plugs and connect them to the top of the panel? So they did. They put all the plugs on top of the panel. Now they just pull them very easily from the top and make the correct connections. Instead of spending 4 hours, they do it in 1 hour. So two women save 3 hours a week times two, that's 6 hours. Forty airplanes in a year. You're saving 240 hours from that one little idea. Now there are 40 panels in that plant. That means there are 80 other people. So if you multiply 40 times 240, you get about 9600 hours that are saved from that one idea because we encourage people to copy each other.
Mark Graban: Now let me ask you then. You talk about there not being, I imagine, a big bureaucratic process involved in harnessing these ideas. I think of suggestion systems filling out a form, and it goes through a committee, and of course, there's a lot of waiting time and waste and delays before somebody blesses the idea as being a good one. How is the process different there with the wire harness?
Norm Bodek: Very good, Mark. The difference is this, and the reason the old suggestion system was bureaucratic is because they gave 10% of the savings back to the worker. And these are the accountants. You know, they can freak you out because before they're going to give you 10%. I mean, the funny thing is the company is saving 90%, and they're worried about the 10%. So what happens is they make a mistake. In this system, you don't give 10% for the ideas. Some companies do, though. Some companies do, like Toyota. We'll talk about that in a few minutes. Toyota does both. The average company in Japan maybe gives $5 for an idea. A lot of companies don't give anything. When I teach in America, I don't encourage any company to give any money. I do encourage them to share profits, maybe a bonus system, and maybe to give lots of prizes at the end of the month. You know, Toyota does things very cleverly. You know, if you have perfect attendance for the whole year, they put your name into a barrel and they give away, like, 15 cars at the end of the year, things like that. So you don't have to reward people. And it's not bureaucratic. A person comes up with an idea, and the system encourages that person to implement their own idea. So as a manager, you ask people to run experiments, and if they have an idea, to say, go try it, if it works, is that part of the process?
Mark Graban: Well, I'll keep it pretty simple. You come up with an idea, you can check with your supervisor. You have to check with the supervisor to get started, but if I'm going to put a piece of Velcro on a little clicker, I don't have to ask my boss's permission. You see the heart of the Toyota system as follows. There are two things that have made Toyota successful, just two pillars. One pillar is lean, the elimination of waste. The second pillar is called respect for people. Respect for people, which means you trust people. So if you set up a system like this, you trust people that they're going to do things right for the company, and if they don't, they're going to learn just the way everybody else learns.
Norm Bodek: Yeah. So we keep it very simple. Look at Technicolor. I started to teach there, and in 2001, they got 250 ideas, and 113 were implemented from 1800 people, which is a typical American suggestion system. One idea every seven years. In the last twelve months, they got 27,000 ideas, and 17,000 were implemented from the same population of about 17 to 1800 people. Sure. And they hired no additional person to administer those 27,000 ideas.
Mark Graban: So you had somebody counting the ideas, I guess, at some point.
Norm Bodek: Well, they count them, yeah, because the way the system works is you write up your idea in a simple form and you implement it. Then you submit it to your supervisor, and the supervisor should keep the statistics for his or her group and then turn it into one central person who's keeping the statistics for the company. And then the ideas are posted up on a wall all around the factory, all around the offices, so people can see ideas. And we also encourage people to copy from each other.
Mark Graban: Now, let me ask you, how do you manage the balance between the ideas of standard work and Kaizen and that experimentation? If you have people just trying things, they may be deviating from that standard. How do you keep the system from degrading?
Norm Bodek: Very good. The interesting thing about standardized work, as opposed to the old standard that you cast in stone, is that standardized work encourages people to make changes. So standardized work represents the best way of doing something. And if somebody does it better, you change the standard. So it's the same thing here. Most of these little ideas have nothing to do with the standards. Most of these ideas don't. Some will. But most of them are just very simple ideas that people get to make their work easier.
Mark Graban: So as a supervisor or a leader in this environment, you're keeping track of suggestions. And if you see something that's working, you're helping encourage, you're asking, or you're telling others to adopt, saying, hey, this was a good idea. You should be doing that also.
Norm Bodek: Very good, Mark. What you're saying is because the Toyota system, which I like very much, is the managers are taught not to tell but to ask. I owned a company called Productivity, and I had about 127 people. And I never asked. I never asked anybody. I was the boss. I must have been the smartest because I owned the company. That was my attitude. I never asked. I just told. Toyota is totally different. Their managers are taught to ask. So a worker comes up with an idea, you look at the idea, you compliment them, you never criticize the idea. That's a very difficult thing to do for American managers, but you never criticize. And then you hang it up on a wall, and you encourage everybody to read each other's ideas so they can copy. Now the worker has to be smart. If they're going to do something that affects the second shift, they should check with the second shift worker to see how it affects them. That's why I like the second pillar. It's called respect for people. People are mature. Given the opportunity, they'll do a superior job.
Mark Graban: So very good. That's a very good background into some of the differences in the Toyota or the Kaizen approach compared to what we normally see with suggestion systems. But let's focus on Toyota. You had mentioned that there were some changes that Toyota is making to their approach with Kaizen.
Norm Bodek: Yes. When Toyota came to America, they were very careful. They didn't want to impose the Japanese system that quickly. They were very careful. And this is looking at NUMMI or Georgetown, wherever Toyota came, they were very careful in setting up their system. Even their just-in-time system took a long time. Very careful in coming over here. So when they first came over, they pretty much adapted the American suggestion system and then put a variation of the Japanese system. Now the system became an American adaptation. It was different than in Japan. NUMMI and Georgetown and TMMK and up in Cambridge, their system became a combination system. A worker could get quite a few thousand dollars from Toyota if their idea saved a lot of money. This was very rare in Japan. But still, Toyota encouraged very small ideas. At first, I don't think they gave any money, then a little money, then they made a mistake. Somebody said, let's give $20 an idea. So they gave $20 an idea. And a couple of people got very clever. One man was so clever that he got himself a swimming pool for the $20 an idea. Because if I shuffled a piece of paper from one side of the desk to the other side and said, that's an idea, that got $20. And so one of the senior managers, I don't know who it was, might have been Mr. Cho or whoever was in charge up here, said, that's crazy. We're not going to do that anymore. And so what they did, which happens, you know, it's the old saying is you throw the baby, you don't throw the baby out with the bathwater. So you don't get rid of a good system because you made a mistake with the $20 an idea. I would have just done very simply and said, I'd only give $20 if it's worth $20. It was so simple. If it's worth $20, give $20. If it's not worth $20, then just pat them on the back, thank them for the idea, and put the idea into a hat because at the end of the month, maybe you have a drawing and give away two tickets for dinner somewhere.
Mark Graban: So there's a story for the people that might think that Toyota never makes mistakes.
Norm Bodek: Oh, they made a big mistake in the suggestion system because they stopped it. They went from 50,000 ideas. I think this was up in Cambridge and also in Georgetown. They went from 50,000 ideas to 500. This was after taking away the $20 per suggestion. So they didn't kill the system entirely. And I have to call them. I haven't spoken to them recently to see if
they readapted and got any smarter. I don't think they did. But maybe they did make some good changes. Even in Japan, they reevaluated this, and it went from 46 ideas a year to about nine or ten per year. So they switched the system a little bit in Japan, too. Give you an example. Subaru, though, a year ago, got 108 ideas per worker.
Mark Graban: What do you think is that difference coming from differences in management approaches? Is there more of an effort to track the ideas at Subaru? Because I've always wondered, with Toyota, you see the numbers on suggestions, and I wondered, well, how many of those little daily Kaizens, little changes are they actually stopping and taking time to formally document? I wonder if that reduced the numbers.
Norm Bodek: Toyota documented every single one of them, and that's what I do when I teach. I mean, the 27,000 ideas at Technicolor are all documented, and they're hung up on a wall. The ideas that are not implemented, you hang them up because then people can help you implement them. But what I really encourage, though, is I encourage the focus on the implemented idea, not on the suggestion. I like a system that is almost 100% implemented. You know, forcing the worker, you come up with an idea, and you get it done. You either implement it yourself, or you ask your supervisor to help you, or you ask a team leader to help you, a team member to help you. Now, some of the ideas might require engineering, they might require maintenance. You might have a Poka-Yoke idea, which is very good, but you don't know how to cut wood, so you get somebody to help you cut the wood. But I don't want you to leave your idea. I don't want you to come up with your idea for somebody else to do it for you. I want you to keep your ownership of that idea.
Mark Graban: Well, the other thing I like about that approach is that it shifts the emphasis. So many times people bring complaints to their supervisor. Here's what's bothering me, and it sounds like this approach really tries to encourage people instead of just complaining. Come to me with a solution to that.
Norm Bodek: Of course, we have a very clever form, which is, this is before improvement. This is after improvement. Now, to have complaints is not bad. You want some avenue for people to express their complaints. But I like what you said, Mark, which is you turn it around and you get everybody to focus on what we call continuous improvement because that's what Kaizen means, it's continuous improvement. And the role of the supervisor, they have to be very careful not to criticize. I was teaching one company, and one of the first ideas that was submitted, this woman goes to her boss, and she shows her the idea, because we're telling everybody, we want you to come up with at least two ideas per month. Most companies now, I tell them, I want to see one idea per week. I want you to come up with 50 ideas, and you can do it very easily. I mean, I have people that are coming up with an idea a day, like Gulfstream. Oscar Ortez, he comes up with at least one idea every single day, an implemented idea every single day. And so this one worker brings this idea to the worker, the supervisor. The supervisor looks at it and says, you know, that's not exactly what we mean to. So the worker walks out of the room, and what do you think the worker says to their fellow worker?
Mark Graban: I'm sure they're discouraged, and that might be the last thing they suggest.
Norm Bodek: Absolutely. You're right, Mark. They said, I'll never give them another idea. You know, the funny thing is, this is so simple to do. I'm, I don't know why I'm working on this now. I'm working on a new book, trying to understand why we don't adapt this. Why don't we do simple things like this? I mean, Technicolor claimed they saved $8 million last year, the third year running. So in three years, they saved $24 million from these ideas from their employees. The average in Japan is $4,000 per employee per year. Arvin Meritor, this is an automotive parts company in Michigan. They also claim that they're getting about $4,000 a year savings per employee. Why aren't other companies doing it? We're running to China to save money. And we can save a fortune by just asking our people to help.
Mark Graban: Well, that's all our time. Norman, thanks again for being here on the first-ever Lean Blog podcast.
Norm Bodek: Thank you, Mark, very much.
Mark Graban: So that's the first podcast. I would really like to thank Norman for being here. We talked about suggestions, and ironically enough, this podcast really was a suggestion from Norman. He approached me about the idea of doing an interview, and it turned into this podcast, which I plan on continuing as a monthly feature. More discussions with Norman, but also other leaders and innovators in the lean world. And talking about his comments about people being in boring, dead-end jobs. As I've been working in healthcare, I'm even seeing cases of that in hospitals. For example, in a hospital laboratory, a woman approached me one day and started talking about how she felt like a robot, as she put it, because of advances in the laboratory equipment over time. Here was a scientist, and she felt like she was reduced to the role of material handler, of loading tubes into the instrument. And she didn't even look at the test result most of the time unless there was something really out of the ordinary that required her review. So I talked to her about how lean, and particularly Kaizen, was going to help make the most of her brains and her training and her experience as a med tech. That it was going to be part of her job not just to load tubes into an instrument now, but to come up with ideas every day for making it a better workplace and for ultimately providing better care to patients.
So at least in the healthcare environment, we're lucky it's easy to rally everyone around the patient. That's why people enter the field, and it's certainly a very important reason to come up with Kaizen in daily work. So whether you're in a factory or healthcare or any sort of environment, if you're working with lean, as Norman talks about, I would definitely encourage everyone to look at more than just reducing waste, look at that second pillar, the respect for people pillar of the Toyota Production System, and think about how you can make sure that people are really contributing and not just being robots.
Thanks for listening. This has been the Lean Blog podcast. For lean news and commentary, updated daily, visit www.leanblog.org. If you have any questions or comments about this podcast, email mark@leanpodcastmail.com.
Hey, podcast listeners. I'm excited to announce the release of the audiobook version of my new book, “The Mistakes That Make Us: Cultivating a Culture of Learning and Innovation.” Listen and dive into powerful insights on fostering growth through mistakes. Whether you're a leader, entrepreneur, or just trying to get better at learning from mistakes, this audiobook is for you. Get it now on Audible, Amazon, and Apple Books. Visit mistakesbook.com for more info.
Please scroll down (or click) to post a comment. Connect with me on LinkedIn.
Let’s build a culture of continuous improvement and psychological safety—together. If you're a leader aiming for lasting change (not just more projects), I help organizations:
- Engage people at all levels in sustainable improvement
- Shift from fear of mistakes to learning from them
- Apply Lean thinking in practical, people-centered ways
Interested in coaching or a keynote talk? Let’s talk.
Join me for a Lean Healthcare Accelerator Trip to Japan! Learn More
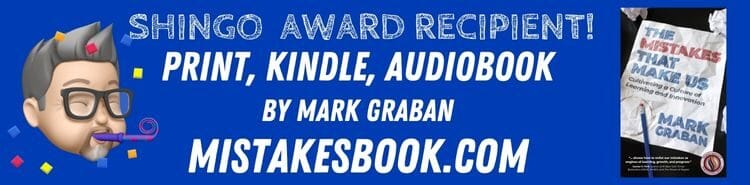
Great! I’ve been looking for a lean podcast and this is the first one that I’ve found.
Keep it up!!
Mark:
In this first podcast, in reply to your important (and practical) question of the interplay between implementation of worker suggestions and standards, Norm’s response was that implementation of suggestions had nothing to do with standards. That comment puzzled me when I first heard it and it is still puzzling.
Isn’t the whole idea of getting and implementing suggestions and having the production workers constantly problem solving a key element of the continuous improvement element of standards? Today’s standard should be changed tomorrow if it is improved—right? If you don’t incorporate implemented suggestions into new standards then you have the makings for chaos—and everyone doing it their own way. Surely, that is not what Norm meant.
Bryan
To be fair, Norman said that workers need to check with other shifts when they have an idea, that people can’t work in a vacuum.
He also said (at approximately 15:10) “If somebody comes up with a better way, you change the standard. Most of these little ideas have nothing to do with the standards.”
I’ll let Norman explain the difference between updating standards and “little ideas” in a comment and in a future podcast.
From Norman Bodek:
This is not a simple issue and something we could address in the next podcast:
Toyota does standardized work whereby the best way to do some things becomes the standard. Workers are required to follow those standards precisely unless they can come up with a better way. Standards are the way to do things, the procedures, or they are the exact measures, or tolerances, to follow. There are very few companies comparable to Toyota with standardized work. Quick and Easy Kaizen asks every worker to find a way to make their work easiier, more interesting, build their skills and capabiities and to improve the work environment. They might but they rarely affect standards. I published a book titled Forty Million Ideas in Twenty Years at Toyota. Very few of these idea affect the standards. I should not have said, “that implementation of suggestions had nothing to do with standards.” At Technicolor they implemented 17,500 suggestions last year. At Gulfstream they are implementing 2000 ideas per month, very few of trhese affect standards as we know them.
It really depends on what level you standardize. If you do 100% like stating exactly how the towel is to be folded on the rack, how you are to stand, etc. than yes you must be very careful with new standards but most companies are light years away. At one time Toyota was getting around 70 ideas per worker per year, today they are around 10 in Japan. Still I feel that very few of those affect the standardized work.
Let us talk more about this.
Best,
Norman
Hi Norman,
It seems many of us North American CI zealots are led to believe in many versions of the Toyota story that they do utilize standards that are continuously updated by the workers within an “enabling bureaucracy.” That is, rigid standards are adhered to as a countermeasure to variability, but workers are encouraged to make incremental improvements to the standard through the formal suggestion system.
Unless I’m misunderstanding your statement you are suggesting this not the case. So the next question is, does Toyota standardize 100% or as you stated: “exactly how the towel is to be folded on the rack”? If this is so, then it is any easy assumption that a change in “how to fold the towel” suggests that a change in the standard work is in order. Take this one step further: if the change is a simple 5S improvement, or safety improvement, or elimination of a step, or simple rearrangement of the work sequence, would that not demand a change of the standard work sheet? Another step further; wouldn’t a standard be required in order to positively transfer the knowledge of the improvement, via Toyota’s famed Job Instruction training methods? Or is this just grand assumptions or wishful thinking of an organizational ideal on my behalf?
Thanks for your insight,
Bryan L.
Thanks for your comment Bryan. I’ve passed that along to Norman and we can maybe address that in a future podcast. Please email me directly, as I’d like to bounce an idea off of you about participating in the podcast somehow.
Mark
[…] Mark Graban on July 30, 2006 · 0 comments I received a follow up question after my first Podcast with Norman Bodek, about where to find a template or example of a kaizen […]
[…] Episode #1 (7/16/06) – Norman Bodek discusses kaizen and employee suggestion systems. […]
[…] of PCS Press. This also celebrates the 1 year anniversary of the Podcast, which featured Norman as our first guest. As I’ve given him credit for previously, the Podcast really was Norman’s idea when he […]
[…] a big round number. 250 podcasts in just under 10 years. Thanks again to Norman Bodek (my first guest and frequent guest) for the idea back in […]
Comments are closed.