Hear Mark read this post — subscribe to Lean Blog Audio
On August 16th, I presented a webinar at the invitation of the BC Patient Safety & Quality Council, as part of their “Quality Café” series. Thanks for the invitation!
I was open to the public and was titled:
“Standardize What Makes Sense… Then Engage Everybody in Improving What You Standardized“
You can view the recording on their page or directly through Vimeo:
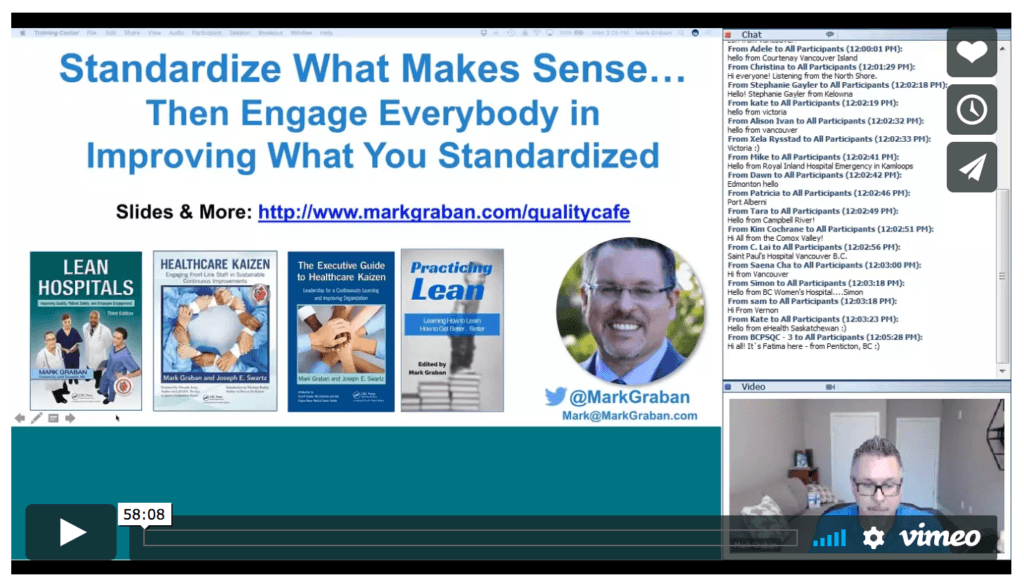
You can find past webinars on their Vimeo channel and mine will be posted there. One of interest was presented by my friend Dr. Mark Jaben on “The Science Behind Resistance.”
Webinar Description:
Standardization is sometimes seen from two extremes: a limitation of clinical autonomy that prevents people from using their best judgement to care for patients, or a technique that helps to ensure the application of best evidence, effective teamwork and communication, and consistency.
In this webinar, Mark Graban, an internationally-recognized expert of “Lean healthcare” and continuous improvement, will explore the meaning of work standards and standardized work as explained by Toyota and the Lean methodology. He will share examples from health care that help us:
- Strike the balance between too little standardization and too much standardization;
- Understand the balance between too much rigidity and too much flexibility in a process;
- Learn how standardization is meant to be temporary, until things are improved and re-standardized; and
- Understand the role that front-line staff should play in defining standardization and ideas for improvement.
Webinar Preview Thoughts
I've shared a number of links on this page. I'll also share my slides and a link to the video there afterward.
The webinar's “key points” are:
- Neither of these are meant to be forced on people:
- Standardized Work
- Kaizen (Continuous Improvement)
- It's up to leaders to engage & involve people
The “key questions” about Standardized Work include:
- What to standardize?
- For what purpose?
- To what degree?
- What what flexibility?
- By whom?
There are a lot of understandable fears in healthcare about so-called “cookbook medicine.” Long before Lean came into the conversation, physicians have felt like outsiders are telling them how to practice medicine – or what the “standardized work” should be. Or the protocols and requirements are too inflexible, say the doctors.
In the webinar, I try drawing on Toyota sources to compare “what Lean should be” versus “Lean As Misguidedly Explained.”
I cite The Toyota Way:
“…standardized work was never intended by Toyota to be a management tool to be
imposed coercively on the work force.On the contrary, rather than enforcing rigid standards that can make jobs routine and degrading, standardized work is the basis for empowering workers and innovation in the work place.”
Taiichi Ohno, in his book Toyota Production System: Beyond Large-Scale Production, wrote:
“Standards should not be forced down from above but rather set by production workers themselves.”
Modern-day Toyota books talk about team members and managers working together to not just DEFINE standardized work, but to improve it, through the practice of Kaizen. Workers developing standardized work doesn't mean everybody gets to do whatever they want. We need to standardize the things that matter, to the right level of detail, and with the right level of flexibility. And, we have to keep improving our standard over time.
I also mention how Toyota learned about this from Henry Ford:
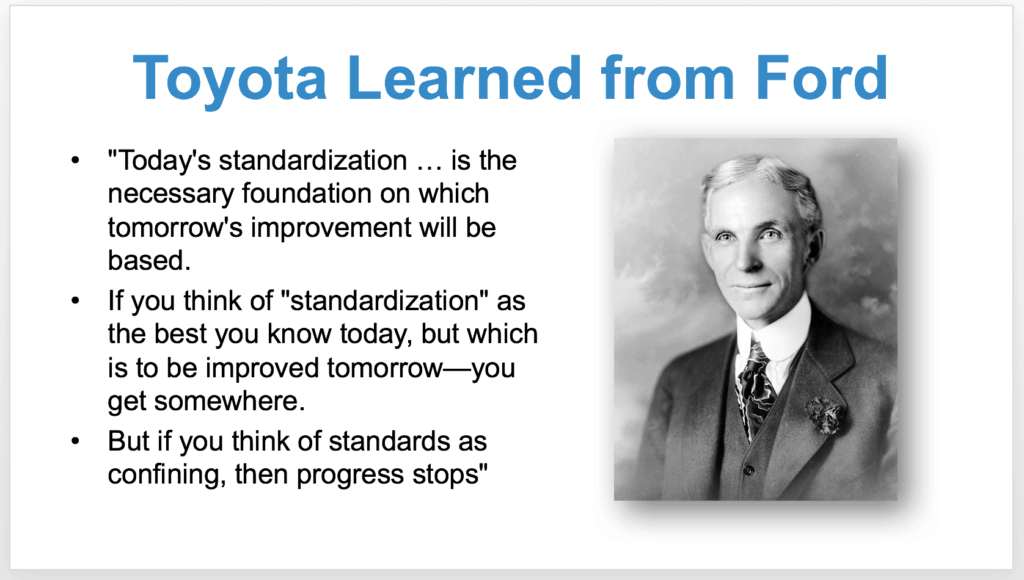
Cookbook Medicine and Cookbook Cooking
Again, I understand the concerns about “cookbook medicine.” What's often meant by that term is overly rigid and inflexible, if not inappropriate care. Lean, being a customer-focused methodology, wouldn't want doctors (or anybody) to be overly constrained by standardized work.
I love to cook. As you learn about cooking (I've been fortunate to take a few classes), they emphasize the need to taste as you cook. You don't just follow a recipe blindly. There might be variation in the potency of herbs or other ingredients. That might lead to you say “each stalk of rosemary is unique!”
I love the quote on this page about the topic of tasting as you cook:
“Cooking without tasting would be like painting a picture without looking at it.”
I've found this to be very true when making pizza at home. Yes, I follow a recipe for dough.
But, based on variation in the flour, humidity levels in the air, and other factors, I might CHOOSE to add more or less water to the dough as I'm making it. It's a bit of a Plan-Do-Study-Adjust process, not just blindly following the recipe. I want the results to be consistent, which sometimes means slight variation in the way I do my “work.”
It even says to do this in the “cookbook:”
“… any recipe can only give an approximation of the water content, depending on which brand of flour you use. You will have to adjust when you make it based on the feel of the dough. It shouldn't be sticky, but it should be very supple and also tacky to the touch.”
Yes, there's some amount of “knack” that you develop over time. Just reading a cookbook recipe didn't make me an expert the first time I tried making pizza. I think I've gotten pretty good over time.
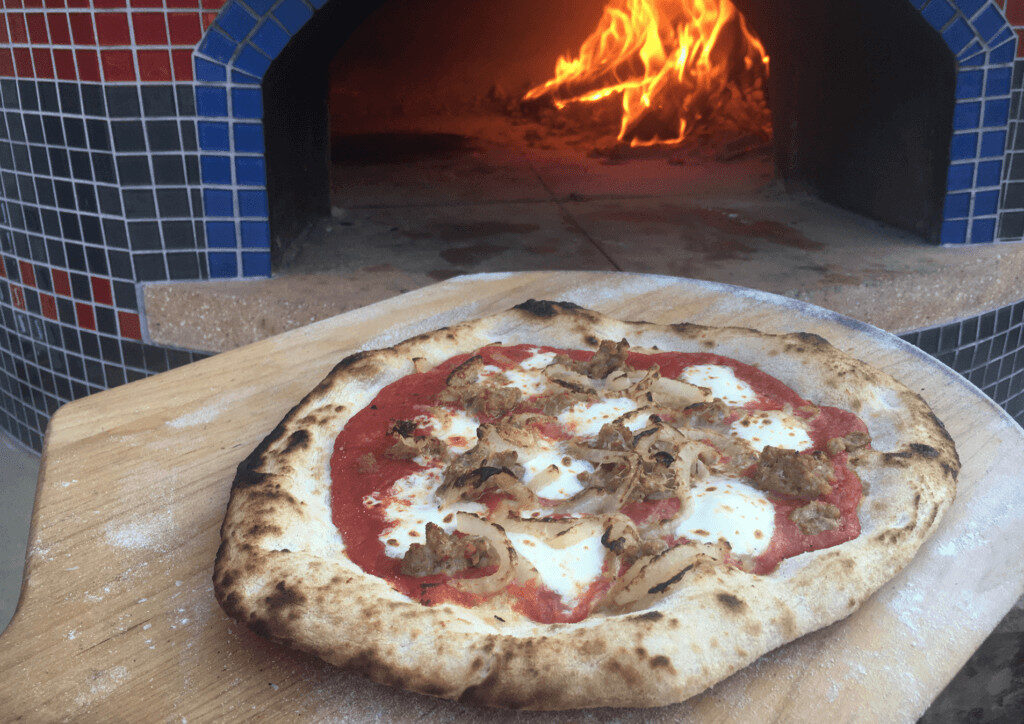
Summary & Discussion Points from Chapter 5 of Lean Hospitals
From my book (and you can download Chapter 5 of the book via this page):
Lean Lessons
- The foundations of Lean are standardized work, heijunka, and kaizen.
- Practices that are more consistent lead to quality that is more consistent.
- Standardized work should reflect an emphasis on quality and safety, not speed.
- Standardized work is written by those who do the work.
- Do not standardize for the sake of standardizing.
- Standardized work frees people to be creative problem solvers, rather than turning them into robots.
- Explaining why shows respect for people.
- Standardized work is not just a one-time documentation exercise.
- Managers must directly observe and audit to see if standardized work is being followed.
- Standardized work is not permanent; it must be improved over time.
Points for Group Discussion
Feel free to respond to any of these questions as a comment on this post.
- How is patient safety impacted by standardizing our work?
- How do irregular or unexpected circumstances fit into standardized work?
- Why is it important that the people who do the work author standardized work documentation?
- How does standardized work apply to physicians and surgeons?
- How can we gain acceptance of standardized work?
- In your workplace, what might be some examples of critical tasks, important tasks, and nonimportant tasks?
- What methods do you currently have in place to verify if work methods are being followed?
- What would be an example of overly specified work in your area? What problems does this cause?
Standardized Work and Continuous Improvement
In the webinar, I'll also talk about the connections between standardized work and Kaizen, as I adapted from a Toyota guidebook that I was given a long time ago:
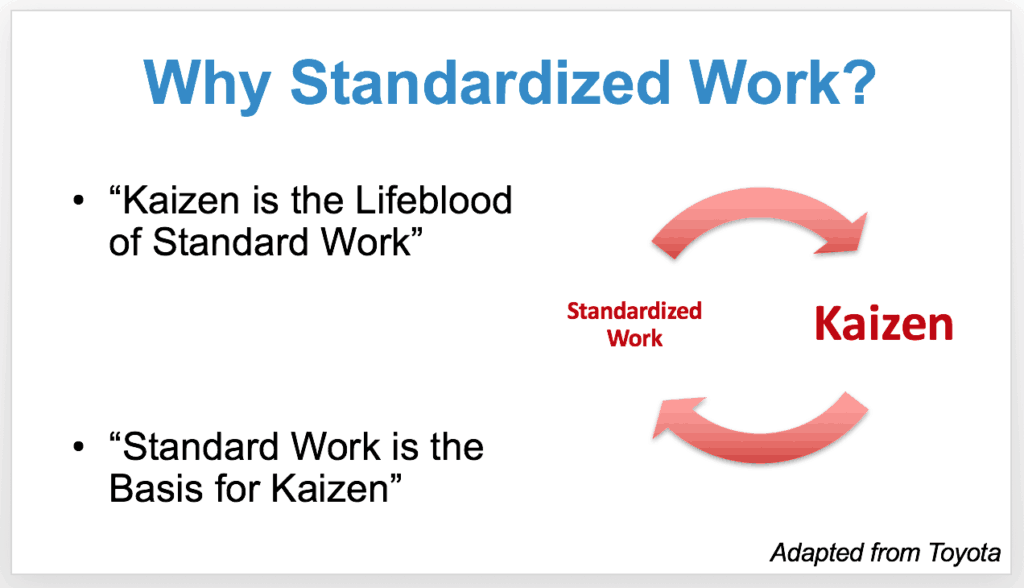
They go hand in hand.
Again, you can view the recording here.
Tweets About the Webinar
What do you think? Please scroll down (or click) to post a comment. Or please share the post with your thoughts on LinkedIn – and follow me or connect with me there.
Did you like this post? Make sure you don't miss a post or podcast — Subscribe to get notified about posts via email daily or weekly.
Check out my latest book, The Mistakes That Make Us: Cultivating a Culture of Learning and Innovation:
Why is it important that the people who do the work author standardized work documentation?
Just yesterday I was speaking with someone who used to work at Ford. I was asking how employees are engaged in improvements at his current company. He told me he didn’t know at the plant level, but he then went on to tell me how employees were engaged at Ford when he was an employee. He said the front line staff members wrote their own standard work. He said this is true respect for people because they do the work. He said why would it be done by anyone else? Pretty good insight coming from a HR guy.
I’m not covering this in the webinar, but here’s a myth about “standard work” as it’s explained here.
Myth: Standardized work “should allow virtually anyone to perform the work without any variance in the desired output.” https://www.isixsigma.com/dictionary/standard-work/
That’s insulting to the people who do the work. No standard work document would make me qualified to do brain surgery.
Irony… a video about “standard work” that’s shot in a very unsafe manner… while the speaker is driving and making turns on the streets.
A pizza lesson from the master, Chris Bianco, who talks about variation in the recipe so that you get consistent outcomes:
“You gotta stop when it’s done.”