Long-time readers might remember this post of mine from February 2007:
Bad Lean/5S Hits the UK Media
Please check out that post. It's a classic example of what I shortly thereafter started (in March 2007) calling “L.A.M.E.” or Lean As Misguidedly Explained.
In that post, I shared a picture from the UK news article that typifies “Bad 5s” (and I've now added a label to the photo that hopefully makes that clear to anyone who might use the image).
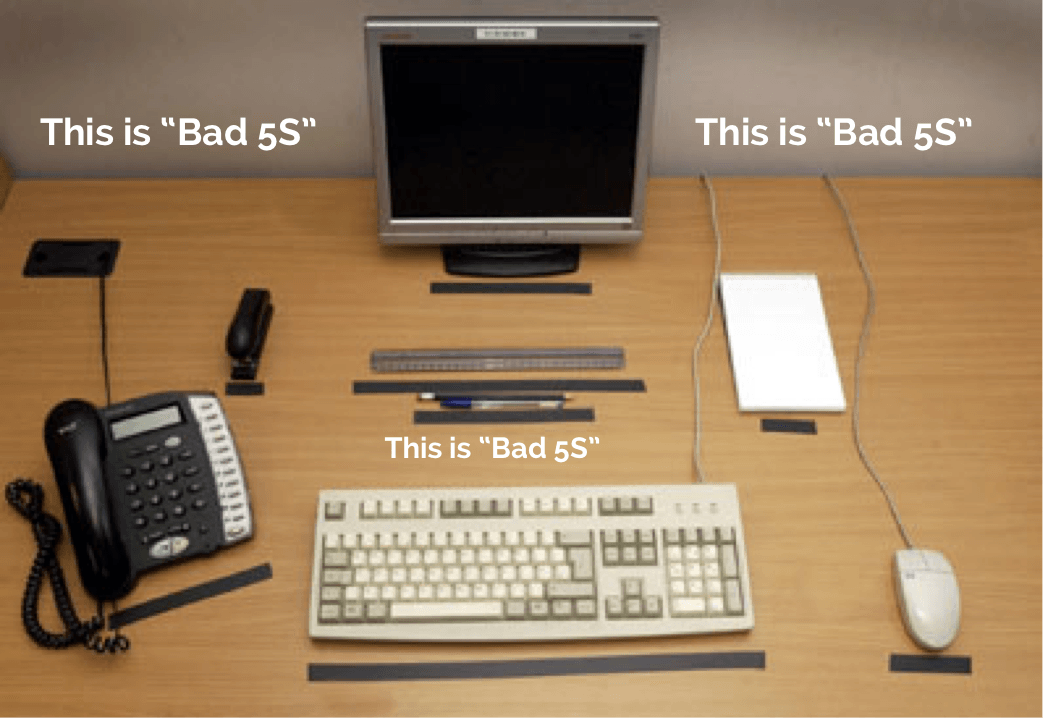
I've used that picture as a punchline in many presentations. That perhaps superficially LOOKS like 5S (tape has been used to mark locations of things)… but look at all of the tape that's been wasted in this case and similar circumstances.
How in the world does it help to mark where your keyboard goes? It doesn't. Has a corded keyboard ever gotten lost or gone missing? Would it affect a person's productivity to move it a bit?
What problem is solved by putting down tape marking the mouse location? None. The tape probably INTERFERES with the use of the mouse, ironically.
This is classic bad 5S… a tool chasing the wrong problem. It's not helping the organization perform better. In fact, I guarantee you that employees who are antagonized by top-down bullying 5S will perform worse because they're cheesed off. It's the type of thing I also blogged about here (the 5S cop) and made a video about.
Don't be L.A.M.E.
Don't do bad 5S to people.
Instead, solve problems that really matter to customers, employees, and the organization.
I was watching a recorded webinar the other day from a non-profit that will remain unnamed. It was a webinar about a “Lean Six Sigma” certification class they are going to be teaching (for healthcare).
One slide included the “bad 5S” picture without any commentary (nothing was said about the picture as the presenter talked about what you'll learn in their class) — I've hidden the organization's name and logo:

If your Lean instructors don't know the difference between helpful 5S and bad 5S, then….
Run away!!
How did the instructor find the image? I don't know, but if you do a Google Image search for “5S lean,” that picture currently shows up as one of the first results without too much scrolling. I wish I had added the “This is Bad 5S” text to the picture long ago.
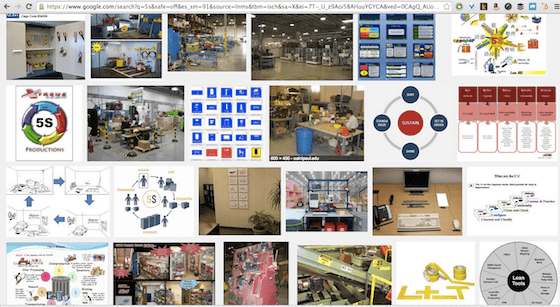
I hope the instructor knows the difference between good 5S and bad 5S. Maybe she was just lazy and did a quick Google search for an image without thinking about it or understanding what she saw.
I hope somebody teaching 5S and Lean for healthcare would have her own examples.
I hope people who want training and education can find experienced people to teach them. Otherwise, I'm afraid we'll end up with more L.A.M.E. in healthcare, when we need Lean.
Please scroll down (or click) to post a comment. Connect with me on LinkedIn.
Let’s work together to build a culture of continuous improvement and psychological safety. If you're a leader looking to create lasting change—not just projects—I help organizations:
- Engage people at all levels in sustainable improvement
- Shift from fear of mistakes to learning from them
- Apply Lean thinking in practical, people-centered ways
Interested in coaching or a keynote talk? Let’s start a conversation.
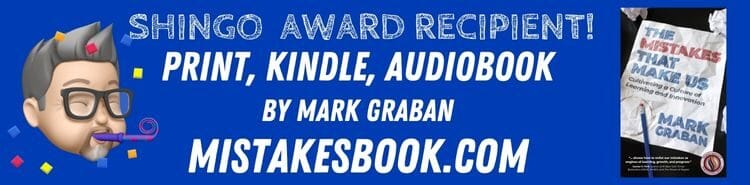
Hi Mark
Age old problem surfaces that we have all seen to often in LEAN, people teaching and trying to do LEAN without applying basic common sense. Labels and marking are only really needed when people share a facility, and even than only for things that do not have a distinct location. If everyone knows where something is supposed to be, marking may be just another waste.
Office 5S is one area where it gets overdone far too often. As a society, we have gotten to dependent on others establishing order that we fail to apply what should be common sense.
As part of my attempts to prevent future cases where that “bad 5S” photo mistakenly gets used as an example of 5S, I offered the photo to Dan Markovitz who is now using it in this post:
http://timebackmanagement.com/blog/the-5s-mind/
I had a few offline discussions about this with people who defended the use of tape.
It sort of went like:
Them: But that photo shows all 5 of the 5S’s
Me: Why? What problem is that tape solving?
Them: Why wouldn’t you want to do 5S?
Me: Because the point of 5S is to prevent problems or to make problems visible.
Them: But I was taught you have to do this (in my class / by my “belt” mentor).
Me: OK, let’s agree to disagree
It was a variation of the fake discussion in the video (which is based on reality):
And I posted these images on Twitter :-)
and
This seems to be what separates the management academics from the management practitioners. The academics want to understand the purpose (the why) behind some trend and apply it understanding the pros and cons. The practitioners want to make visible progress, and that progress usually entails the how.
So, for example, I experienced “Language Processing” in a corporate culture and realized that the changes the corporation made to the “how” completely destroyed the “why”.
We also had our 5s cycle. It worked great for the break room, but not so well for our desks.
I experienced “Extreme Programming” implemented in a corporate culture. They decided that “pair programming” was 50% wasteful, so they chose not to do that, but somehow, they were very upset when a programmer left and the schedule blew up.
Just like “Lean”, Agile development is also poorly understood in the same way. Companies want to be “agile” yet they want to promise customers what features will be in the product six months or a year out. They don’t want us to waste time on planning, yet every two weeks, they want to understand all the implications of changing this or that feature.
To be “perfectly clear”, that is the reason why western culture won´t learn 5´S or any other Lean concept easily.
Because western culture continues to teach Lean concepts the “western way” (Mark Graban´s way).
See Karate Kid movie and learn how to teach mechanicss first so people learn mechanics and later understand concepts and not question until the learning is achieved.
To be “prefectly clear”……..Your lesson of “Bad 5´S” stinks .
David – can I assume then that you’ve found it a successful strategy to:
1) Irritate employees by telling them 5S means no family photos on their desk
2) Once they’ve “learned the mechanics” this way, they then go do productive things with 5S?
That seems like an unlikely scenario, but if you have stories to share that prove me wrong, I’m open to hearing them.
I’m pretty certain that Toyota, through their TSSC, doesn’t teach the mechanics of 5S to suppliers and non-profits by making them put tape outlines around their desks, and also removing personal items.
They teach mechanics and mindsets by solving problems that matter.
When people associate Lean or 5S with something negative (telling me how to arrange my personal desk), that disengages people and they think Lean is bad instead of helpful.
Employees in Western companies will not just blindly accept a Mr. Myagi type person telling them to do things for no apparent reason.
They WILL accept good 5S that makes their work easier… tape on desks doesn’t accomplish that.
Following up on this, Toyota doesn’t force people to use 5S on their desks and they’re allowed to have family photos:
https://www.leanblog.org/2017/10/toyota-helps-young-inventor-look-dads-toyota-desk/