tl;dr: In this post, Mark reflects on the 25th anniversary of the term “Lean Production,” delving into the original article that coined it. He discusses the impact the term and its underlying principles have had on various industries, from manufacturing to healthcare. Mark critically examines how the term has evolved and the significance it still holds for ongoing improvements in quality, efficiency, and organizational culture.
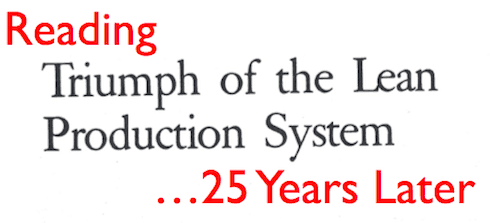
People often ask me where the term “Lean” comes from. It's not an acronym, so it shouldn't be spelled “LEAN” (but it often is). Lean is not a synonym for “lacking or deficient” in resources, as some dictionaries will tell you or as it gets used in news headlines about “surviving the lean economy.”
The term “lean production” arguably was first used in an MIT Sloan Management Review article by John Krafcik that was published 25 years ago this fall (Fall 1988), titled “Triumph of the Lean Production System” (pdf via LEI). In the 1980s, Krafcik, who worked with The Lean Enterprise Institute's Jim Womack in the MIT International Motor Vehicle Program is now president and CEO of Hyundai North America (update: he's now CEO of TrueCar — he's now CEO of Waymo).
I'm told by LEI that Womack and Krafcik are writing an article, with their reflections, that will be published soon at lean.org. For now, you get my humble thoughts as somebody who read it 15 years ago… and again just recently.
The article was assigned reading when I was a student at MIT in 1998, but until recently I hadn't returned to it since. I wanted to revisit it and write about it for the 25th anniversary – but it was difficult to find a copy online. The article could not found on the SMR web page for the Fall 1988 issue, or via search, to be purchased or read for free. Diligent Google searches turned up just one poorly scanned version of the article from a Chinese website that seems to specialize in pirated files. But, I had at least I had found it (I later found a hard copy in my grad school box… the article will kept more handy in my office from now on). Click the image at left to read the first page.
I followed up with SMR to plead with them to let me purchase a legal copy. They eventually sent me a free copy and agreed they would start offering the article for purchase (this still hasn't happened, after a few months of back and forth). LEI has requested that they start selling the article. I don't feel comfortable sharing the full article, due to copyright, etc.
UPDATE: The article is now available from the Lean Enterprise Institute (free PDF).
Why is this article important? I recommend it to lean practitioners and leaders today, not just as a historical artifact, but because its key points are still valid and relevant. What makes a “lean production system?” It's not the tools; it's the management style and the culture. That was true in 1988 and it's true today.
Lean or Fragile?
Krafcik wrote about the origin of the term “lean” in contrast to what might be called the traditional approach – a “buffered” production system.
When I started my career at a GM engine plant in 1995, the plant certainly followed the “buffered” approach. The plant's management philosophy attempted to keep, for example, the engine block machining line running at all costs by storing large (and virtually unlimited) buffers of parts in many locations.
If one machine was down, they would run all of the other machines, building a “buffer” of parts that would be used later. These “buffers” often contained defective parts, which caused problems down the line. It was a never-ending game of production whack-a-mole, constantly offloading and loading buffered parts to and from the line. Ironically, our highly buffered line had exactly one half the productivity of our benchmark Toyota plant. Krafick said this strategy was “a safe bet for a steady, if unexceptional return.”
Krafcik went on to describe a “lean” plant, which had inventory levels that were “kept at an absolute minimum” so that quality problems and downtime occurrences could be “quickly detected and solved.” He said this strategy presented higher risks but had greater potential gains. Many of the “risks,” such as downtime or poor quality, could be “neutralized given an experienced, well-trained workforce, responsive suppliers, and good product designs.”
Today's lean thinkers would recognize the role of methods like mistake proofing and Total Productive Maintenance, along with having more collaborative relationships between factories and suppliers, as well as manufacturing and product development.
In an endnote, Krafcik cites earlier work that used the terms “robust” and “fragile” instead of “buffered” and “lean.” For all of the handwringing that takes place about the negative connotations of the word “lean,” we can count our blessings that the term “fragile” wasn't used. There would be no “Fragile Enterprise Institute,” I'm sure. No bestselling book called The Fragile Startup, either.
Lean as a Coherent, Integrated Management Policy
Some people criticize the “early days” of the Lean movement as focusing too much on tools or for not fully understanding the implications of Toyota's management system. I think people who review this article (or even re-read The Machine That Changed The World), would appreciate how much attention Krafcik paid to Toyota's “production management policies,” as he called them. He didn't write about tools like 5S, kanban systems, or heijunka boxes. He wrote primarily about management, leadership, and culture.
Krafcik's article builds on two years he spent working as an engineer at NUMMI, the GM-Toyota joint venture plant that started operations in 1984. Krafcik experienced the noticeably different management environment of NUMMI, much as I did in 1996 when the GM plant that employed me brought in a new plant manager who was transformed by his experience as an early NUMMI employee.
What were some of these philosophies and management practices? They included:
1) Lean is respect for humanity and continuous improvement
In a Lean environment, Krafcik “Management did not think of workers as replaceable cogs in a great production machine… and gave them the responsibility to continuously improve… Scientific management techniques were not thrown away; they were just performed by different, more appropriate employees” who had a “true grass-roots involved with all aspects of the operation.”
2) Lean is an integrated management and operational system
Krafcik explains, “This system encourages the full development and integration of all existing technology, policies, and human resources in a way that traditional… policies seem to miss.”
3) Lean is about culture change
Krafcik explains how one automotive company that made great improvements on both quality and cost “implemented more and more lean production management policies in its plants, in effect incrementally altering its own corporate culture to better fit the lean model.”
Lean Management Was (and Still Is) the Best Predictor of Success
Krafcik described a “management index” that predicted a plant's productivity far better than its level of automation or national location. The four components of the index that predicted success were:
- Levels of teamwork throughout the plant
- “Visual control,” as “a proxy for worker span of control” (a Lean plant has more cross-training than a traditional plan)
- Unscheduled absentee-ism rates, “an indicator of worker participation and management's expectations”
- The amount of space dedicated to repairs, illustrating management's expectations about quality being built in (traditional plants planning and expecting to do a large number of repairs as part of normal daily operations).
Krafcik seemed optimistic that the “lean production management policies” could be adopted in the U.S., as “perhaps the most important competitive weapon in the U.S. industry's arsenal [is] the ability to accept and digest new ideas rapidly,” whereas “Most European plants are saddled with… the not-invented-here syndrome.” Some say healthcare is saddled with that very problem today.
25 years later, what is your assessment? Has “lean production” triumphed in the auto industry? At the plant level, I would say yes, this seems clear, as GM, Ford, and Chrysler have made great strides in changing their factories' cultures. But what about other manufacturing industries or, more importantly, healthcare?
It's still fascinating to me that such an influential and well-cited article is so hard to find 25 years later. I think it's really important for the Lean community to understand the roots of the concepts and principles, not just the word “Lean.” As much as people are discovering the importance of culture and management systems, not just tools, the wisdom of a truly Lean approach has always been out there in articles like Krafcik's.
Please scroll down (or click) to post a comment. Connect with me on LinkedIn.
Let’s work together to build a culture of continuous improvement and psychological safety. If you're a leader looking to create lasting change—not just projects—I help organizations:
- Engage people at all levels in sustainable improvement
- Shift from fear of mistakes to learning from them
- Apply Lean thinking in practical, people-centered ways
Interested in coaching or a keynote talk? Let’s start a conversation.
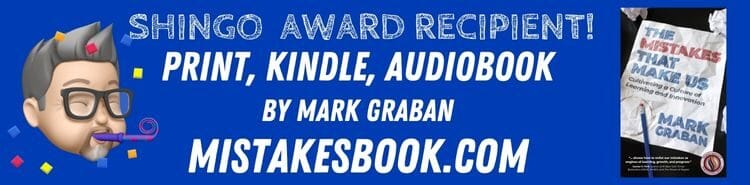
Nice article Mark! Very cool trying to get that article available again!!
[…] See on http://www.leanblog.org […]
[…] The Term “Lean Production” is 25 Years Old – Some Thoughts on the Original John Krafcik Articl… by Mark Graban – “Lean is respect for humanity and continuous improvement… Lean is an integrated management and operational system…” […]
[…] I wrote the post The Term “Lean Production” is 25 Years Old – Some Thoughts on the Original John Krafcik Articl… back in September, I was frustrated that this groundbreaking article was NOT available for viewing […]
Here’s a good follow up post by Jason Yip:
LINK
[…] there was the Lean Production System, The Machine That Changed the World, and Jim Womack and Dan Jones’ book, Lean Thinking. Today, […]
[…] John — Term “Lean production” is 25 years old — link to the original article can be found in my blog post […]
[…] the “Lean” in the “Lean Startup” methodology basically comes from Toyota, it was […]
Krafcik ended up as CEO of the company True Car after leaving / being replaced at Hyundai:
Article Link
[…] de la production “lean”, veuillez-vous référer à cet article; pour un article fêtant les 25 ans du “lean management”, veuillez-vous référer […]
[…] started with “Lean Production” over 25 years ago, as a different name or adaptation of the Toyota Production System. Lean became the “Lean […]
[…] The roots of “Lean Production” go back further than that, with the origins in Toyota post 1945 and as the term “Lean Production” was coined over 25 years ago. […]
[…] term “Lean” was coined by American researchers to describe the management and leadership practices they observed at Toyota (and subsequently applied […]
Mark, thanks much for posting. John Krafcik’s observations remain very relevant. The ongoing challenges that I encounter in work with clients are these: 1) leadership focusing on results rather than the work processes that drive results; 2) a lack of respect for the knowledge, creativity, and intelligence of line workers. The most important teaching of Lean is the absolute importance of a leadership team going to the line and interacting with line workers in ways that demonstrate their clear understanding that line workers, the employees who make the product or deliver the service, are the organization’s most important employees and that they are greatly respected.
[…] term lean was first used in manufacturing by John Krafcik in an article published in the late ’80s based on his master’s in management thesis at […]
[…] and eliminate waste while still creating value for customers. Lean encompasses a variety of things and Lean manufacturing terms, tools, and practices are mainly derived from the Toyota Production System and was first coined in the 1980s by John Krafcik. […]