Hardwiring Excellence by Quint Studer
As I continue my journey in lean healthcare, I'm enjoying the chance to learn about the cultures of healthcare organizations. One book I've started reading could easily apply to lean efforts in any setting. The book isn't about “lean” per se, it's about leadership. But the author's lessons remind me of TPS and lean management concepts.
One of his key management principles reminds me of the idea of “Servant Leadership”, as Gary Convis from Toyota often discusses. “Stewardship” is a great book on this topic, as well.
Quint Studer says, as a leader (and even as CEO), you need to ask your employees:
“We want to make this a better place for you to work. What do I need to do?”
and
“Hi, my name is Quint Studer. I'm the administrator here. I work for you. What should I do today?”
Studer advocates for the idea that leaders need to help create an environment where people want to work. This often means fixings things for people that might seem inconsequential (such as “we need another copier”) but get in the way of people focusing on taking care of patients (or customers).
I like how Studer focuses on asking the employees what needs to happen. Management doesn't need to have all of the answers, you need to focus on people and building a workplace that naturally retains and attracts good people.
Studer also talks about an idea that reminds of the lean concept of the “gemba” (or “actual place”).
“Where leaders spend their time sends a clear signal to the organization about what is important.”
The final idea is that of “hardwiring excellence,” which reminds me of the lean concept of standard work.
“I've seen too many good organizations lose good results when a leader leaves. My goal was to hardwire results so that when I left, they would sustain the gains. Hardwiring works.”
Isn't this true in many factories? The factory makes great strides with lean, then it all falls apart once that initial driver and leader gets promoted or gets hired away. The beauty of Toyota is that they have truly instituted a SYSTEM (the “Toyota Production System“) that isn't dependent on just one person. TPS didn't go away after Shingo and Ohno had moved on. They truly hardwired excellence into Toyota.
Challenge yourself with that idea in your lean efforts… are you hardwiring excellence or not? Then again, unless you're the owner of the company maybe you don't have a true incentive to do that, the way most managers and executives are able to change jobs and change companies so often.
Anyway, I'm really enjoying the book so far and I highly recommend it.
Please scroll down (or click) to post a comment. Connect with me on LinkedIn.
Let’s work together to build a culture of continuous improvement and psychological safety. If you're a leader looking to create lasting change—not just projects—I help organizations:
- Engage people at all levels in sustainable improvement
- Shift from fear of mistakes to learning from them
- Apply Lean thinking in practical, people-centered ways
Interested in coaching or a keynote talk? Let’s start a conversation.
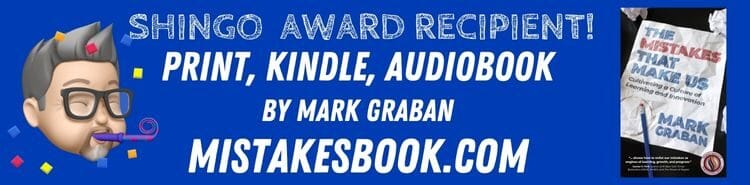
I can’t say I’ve ever had a boss ask me what he could do to make it a better place to work. I’ve had bosses who assumed what I wanted (and were half-right), but never any who bothered to ask. I like the hardwiring ideology.
[…] rid of the C’s comes from a book I admire very much, “Hardwiring Excellence“, by Quint Studer (which I’ve mentioned here before). He exemplifies many of the characteristics of a lean manager in a hospital setting — walking […]
[…] written before about former hospital CEO and healthcare consultant Quint Studer and his amazing book “Hardwiring Excellence.” I think it’s a great book even for […]
[…] Mark Graban on January 16, 2007 · 3 comments Quint Studer is a former hospital CEO who I’ve mentioned a lot here. He has an outstanding blog now. In his issues, he doesn’t talk about “lean” per […]
[…] Purpose, Worthwhile Work, Making a Difference was very inspirational and it’s something I wrote about before and recommended even to manufacturing leaders to learn from. We could all apply his methods for […]