Back in 2018, I had the opportunity to deliver a virtual keynote for a medical conference in Turkey. The theme was close to my heart and deeply rooted in my work and books: how Lean thinking, grounded in respect for people and continuous improvement, can guide healthcare organizations toward sustainable excellence.
In this post, I want to share highlights and reflections from that talk. Whether you're new to Lean or leading a mature transformation, these foundational principles still apply. They're not steps to complete; they're pillars to stand on.
Lean Is a System–Not a Toolbox
It's tempting to think of Lean as a collection of tools:
- 5S,
- value stream maps,
- A3s,
- huddle boards.
But the heart of Lean isn't the tools–it's the thinking behind them. As I shared in the keynote:
“Toyota publications have referred to [Lean] as an integrated system. And we might see problems if we try to copy just one part of that system.”
One of the risks I see in healthcare is adopting isolated practices without understanding the culture they're meant to support. If we implement huddle boards without creating psychological safety, we're putting up wallpaper on a crumbling wall. Culture eats tools for breakfast, you might say
Two Pillars: Respect and Improvement
When you visit a Toyota facility, one of the first things you'll see in the visitor center is this phrase: The Toyota Way = Respect for People + Continuous Improvement. It's not just a slogan–it's how they manage every day.
“Before we think about Lean tools and methods, it's important to step back and ask: is our workplace a respectful environment?”
Respect for people extends far beyond mere politeness. It's about how we design our systems, how we respond to mistakes, and how we engage every individual in problem-solving.
“Respect means not asking people to be perfect–it means designing systems that help people succeed.”
Too often, I still hear leaders say, “We just need staff to be more careful,” or “We told them not to make that mistake again.” That's not Lean–that's blame. And it's not respectful.
A Lean leader looks at a mistake and asks: What in the system allowed that to happen? What can we do to prevent it in the future? As I said in the talk:
“We can be critical of broken systems without being critical of the people working in them.”
Developing People Through Kaizen
Improvement isn't just about metrics–it's about people. At Toyota, the primary purpose of Kaizen isn't just performance. It's development.
“The goal of improvement is not just to improve metrics. Toyota would say that the primary goal of Kaizen is to develop people first and meet goals second.”
I've seen this firsthand at Franciscan Health in Indianapolis, where my Healthcare Kaizen co-author Joe Swartz led their daily improvement efforts. Over the years, they've implemented over 30,000 improvements–not through top-down mandates, but by engaging everyone.
And the results? Yes, millions saved. But more importantly:
- higher staff engagement,
- fewer injuries,
- better care, and
- more joy in work.
As one nurse put it:
“Management allows us to implement things to see if it will work. That shows they trust us.”
That's respect in action.
Why Suggestion Boxes Fail
Many organizations try to “listen” through suggestion boxes. But they often turn into black holes for ideas. That's not a process–it's a trap.
“We can't just ask people to speak up and let their ideas sit in a box. We need to work with them to turn those ideas into action.”
Kaizen isn't a form, or a board, or a quarterly award. It's a conversation. It's leaders asking questions like:
- What's getting in your way today?
- What do you think we should try?
- How can I support you?
Improvement happens at the speed of trust. And trust is built through daily engagement, not annual slogans.
Easier, Better, Faster, Cheaper–in That Order
Too often, healthcare leaders jump straight to “cheaper.” But Lean teaches us to start with what matters most: making work easier and better.
“We focus on making work easier–not because we're lazy, but because we want to use our time adding value.”
The four goals of Kaizen, in order, are:
- Easier – Reduce frustration, barriers, and overburden
- Better – Improve quality and safety
- Faster – Eliminate delays and unnecessary steps
- Cheaper – Reduce cost without harming quality
When you prioritize easier and better, faster and cheaper tend to follow. But when you lead with cost-cutting, you often sacrifice quality and demoralize staff.
As I said in the keynote:
“A Lean environment doesn't drive cost cutting through layoffs. We don't overburden people. We make sure we have the proper staffing levels. We allow people to do meaningful work.”
That's not a cost center–it's an investment.
Leadership Means Coaching, Not Controlling
Ultimately, Lean leadership is about humility and curiosity. Not giving answers–but helping people find them.
“When we give people answers, we're stealing a development opportunity from them.”
As leaders, our job is to:
- Create the conditions for safety
- Set direction
- Provide support
- Develop capability
We don't improve for people–we improve with them. That's how we build systems that last.
Final Thought: Respect Is the Culture, Kaizen Is the Engine
If you're trying to create a culture of continuous improvement, remember: Kaizen is the engine, but respect is the fuel. Without it, improvement efforts stall out, or never get started.
Culture change isn't about a checklist–it's about how we show up. Every day. As I concluded in the keynote:
“My hope for you is that if you don't already have this culture of continuous improvement, you'll step back and think not only about Lean tools and projects, but about this philosophy. How do we demonstrate respect to our people every day? One way we do that is by engaging them in continuous improvement.”
Thanks again to the conference organizers for the invitation to speak–and to all of you continuing this important work in your own organizations.
Learn more about my speaking and bring me to your organization or event
Please scroll down (or click) to post a comment. Connect with me on LinkedIn.
Let’s build a culture of continuous improvement and psychological safety—together. If you're a leader aiming for lasting change (not just more projects), I help organizations:
- Engage people at all levels in sustainable improvement
- Shift from fear of mistakes to learning from them
- Apply Lean thinking in practical, people-centered ways
Interested in coaching or a keynote talk? Let’s talk.
Join me for a Lean Healthcare Accelerator Trip to Japan! Learn More
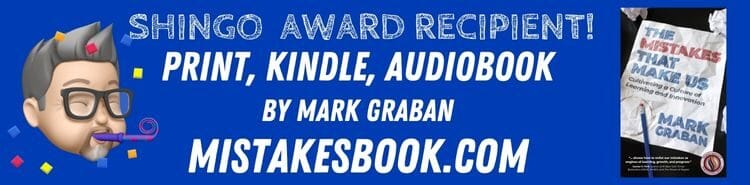