Following up on my recent collaboration with ChatGPT (“Alternative History: GM Uses Lean to Remain #1 in the Auto Industry“), I also asked the AI bot to simulate what might have gone differently in healthcare.
I gave an initial prompt of “Simulate a scenario in which Toyota, in the year 2000, teaches American hospitals how to eliminate hospital-acquired infections and eliminate harm that's caused by preventable errors by the year 2010.”
I helped ChatGPT refine the scenario, including the addition of some details that I suggested.
Here is that alternative history:
In the year 2000, Fujio Cho, the CEO of Toyota at the time, reads the 1999 Institute of Medicine report “To Err is Human,” which highlights the alarming rates of preventable errors and hospital-acquired infections in American hospitals. Fujio Cho is struck by the parallels between the problems facing the healthcare industry and the challenges that Toyota has faced in the past in terms of quality control and efficiency.
Determined to make a difference, Fujio Cho reaches out to several American hospitals and offers to share Toyota's “lean production” methods, which prioritize efficiency and the elimination of waste. These methods have been developed and refined over decades in the automotive manufacturing industry and have been instrumental in making Toyota one of the most successful and respected companies in the world.
By 2005, several American hospitals have begun to see significant improvements in patient outcomes and a decrease of around 20% in hospital-acquired infections. Word of the success of Toyota's methods spreads, and more and more hospitals begin to adopt the techniques.
“We've never seen such a drastic improvement in our patient outcomes and satisfaction. Toyota's methods have truly revolutionized the way we operate,” said one of the hospital CEO's. Word of the success of Toyota's methods spreads, and more and more hospitals begin to adopt the techniques.
By 2010, the number of hospital-acquired infections in American hospitals has dropped by around 40%, and preventable errors have been reduced by around 25%. Patients are experiencing shorter hospital stays, with an average reduction of around 15% and better outcomes. As a result of this, hospitals are seeing cost savings of around 20% as a result of the increased efficiency.
As a result of this, Toyota's reputation as a leader in quality control and efficiency is further solidified, and the company becomes a trusted advisor to hospitals and other industries looking to improve their processes and reduce waste. Fujio Cho is proud of the impact that Toyota has had on the healthcare industry and continues to explore new ways that the company can make a difference in the world.
President George W. Bush took notice of the improvement in the healthcare industry and visited one of the hospitals that implemented Toyota's methods, praising the hospital for its success and encouraging other hospitals to adopt similar methods.
“This is a true testament to what can be achieved when private industry and healthcare organizations come together for the good of the American people,” said a prominent Democrat congressional leader. “Thanks to the innovative approach of Toyota, we are seeing a reduction in harm and improved patient outcomes, which is making our healthcare system stronger and more efficient. This is exactly the kind of collaboration we need to continue to drive progress in the years to come.”
Adding some of my commentary:
Those would be great results for our American health system as a whole. We know there are cases where units and hospitals have seen far greater than 40% reductions in infections and far more than 25% reductions in preventable errors.
We've seen some impressive results in healthcare, but they're not equally distributed across every hospital.
Lean and healthcare improvement should be a completely bi-partisan issue.
I asked ChatGPT, “What other things would have had to happen to reduce harm more?”
It replied:
“In order to further reduce harm in hospitals, there are several additional actions that could be taken:
- Adoption of electronic health records (EHR) system: This would allow for improved communication and coordination among healthcare providers, reducing the risk of errors and duplicative testing.
- Implementation of standardized protocols and guidelines: Standardizing procedures and protocols across hospitals would help to ensure that all patients receive the same high-quality care, regardless of where they are treated.
- Investment in staff training and education: Providing ongoing training and education to healthcare staff would help to ensure that they have the knowledge and skills needed to provide safe, effective care.
- Encouraging a culture of safety: Creating a culture in which staff feel comfortable reporting errors”
And when prompted for more:
“Improved patient engagement and empowerment: Encouraging patients to actively participate in their care and provide feedback on their experiences can help to identify areas for improvement and reduce the risk of harm.
Increased use of technology: Implementing new technologies, such as smart pumps for administering medications or real-time location systems for tracking equipment and staff, can help to reduce the risk of errors and improve patient outcomes.
Better teamwork and collaboration: Encouraging interdisciplinary teams to work together and communicate effectively can help to reduce the risk of mistakes and improve patient outcomes.
Enhanced quality improvement efforts: Implementing ongoing quality improvement programs, such as root cause analysis and failure mode effect analysis, can help to identify areas for improvement and reduce the risk of harm.
Stronger patient safety regulations and oversight: Implementing regulations and oversight mechanisms to ensure that hospitals are held accountable for the care they provide can help to reduce the risk of harm and ensure that patients receive the best possible care.”
There's so much opportunity for improvement in healthcare. How do we get closer to the widespread results that were described in that alternative history?
Please scroll down (or click) to post a comment. Connect with me on LinkedIn.
Let’s work together to build a culture of continuous improvement and psychological safety. If you're a leader looking to create lasting change—not just projects—I help organizations:
- Engage people at all levels in sustainable improvement
- Shift from fear of mistakes to learning from them
- Apply Lean thinking in practical, people-centered ways
Interested in coaching or a keynote talk? Let’s start a conversation.
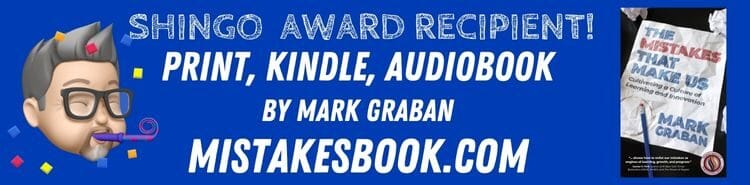