Updated May 2024: I worked with ChatGPT 4 to create a longer, hopefully better, version of the alternate history story here.
ChatGPT is still all the rage. It's one thing to treat the chatbot like Google. But I recently learned about some capabilities that are far more interesting — the ability to “simulate” events that never happened in real life (a.k.a. “the original timeline” or OTL as it's referred to in the “alternative history” genre).
In OTL, General Motors started its formal partnership with Toyota at the NUMMI plant in 1984. GM had the opportunity to learn from Toyota, but the company didn't exactly rush to emulate the Toyota Production System. Causes of this included arrogance, denial, and being pretty set in their ways.
Check out these two podcast episodes with Steve Bera (Part 1 and Part 2). He was one of the GM leaders who was sent to learn at NUMMI and speaks about why GM wasn't receptive to the Toyota way of leading and improving.
GM came around, but they lost a lot of time… and they fell behind Toyota and other automakers.
My original prompt to ChatGPT was this:
“Simulate a scenario where General Motors learns enough from NUMMI so that they effectively copy the Toyota Production System and remain #1 in market share.”
If this happened, I would never blogged about a book called How Toyota Became #1.
The first draft was interesting. I made a few suggestions to the bot, and this is the “final” result, below. Below that is another version generated by ChatGPT 4 in May, 2024.
An Alternative Timeline Where GM Remains #1
In 1989, General Motors (GM) CEO Roger Smith was deeply affected by the release of the documentary film “Roger & Me,” which portrayed the negative impact of GM's plant closures and layoffs on the city of Flint, Michigan. The film served as a wake-up call for Smith, and he realized that the company needed to change its approach to manufacturing in order to better serve its customers and its communities.
In response, Smith decided to study the Toyota Production System (TPS), which is a methodology used by Toyota to achieve efficiency, quality, and productivity. He sent executives and engineers to spend significant time studying TPS at the New United Motor Manufacturing Inc. (NUMMI) joint venture between Toyota and GM, which was opened in 1984. They learned the principles of just-in-time production, continuous improvement, and standardization, which were key to Toyota's success.
With this knowledge, GM began to implement a new system called the GM Management System (GMMS) in its own factories and plants across the country. The GMMS is based on the principles of the TPS and emphasizes teamwork, employee empowerment, and respect for people. This involved changes to the company's management structure and culture, such as giving front-line workers more decision-making authority and providing them with the training and tools they need to improve their work processes. GM also emphasized collaboration and better relations with the United Auto Workers, the union representing GM employees, involving them in the implementation of the GMMS.
As a result of these efforts, GM saw improvements in efficiency, quality, and productivity, which enabled the company to produce vehicles at a lower cost and with fewer defects. This helped GM to better compete with Toyota and other automakers in terms of price and quality, and GM retained its position as the top automaker in terms of market share.
Interestingly, other American automakers such as Chrysler, Ford, and others also came to visit GM plants to learn from their new management system, GMMS and how they were able to collaborate with their unionized workforce to achieve success.
By creating and implementing the GMMS, GM was able to improve its manufacturing processes, increase efficiency, reduce cost and improve the quality of its cars. The company was able to maintain its position as the top automaker in the global automotive market, and also became a benchmark for other American automotive companies to follow.
Through this experience, Smith became a humbled leader, understanding the importance of listening to the voices of the communities and workers impacted by the company's decisions, and making sure that the company's management system is aligned with the values of fairness, respect and empowerment.
2024 Version by ChatGPT 4
With light editing by Mark Graban
The NUMMI Catalyst: General Motors' Reinvention as a Lean and Agile Innovator
The NUMMI Genesis
In the mid-1980s, General Motors stood at a crossroads, grappling with declining market share and operational inefficiencies. This critical juncture marked the beginning of a transformative era, as GM initiated a pioneering joint venture with Toyota to create the New United Motor Manufacturing, Inc. (NUMMI). Through this collaboration, GM was introduced to the Toyota Production System (TPS), embracing lean manufacturing principles such as Just-In-Time production, continuous improvement (Kaizen), and a deep respect for the workforce. This shift was more than an operational upgrade; it was a cultural realignment towards excellence and quality.
The Lean Leap and Corporate Philosophy Evolution
The lessons learned from NUMMI in 1985 inspired GM to implement “The Lean Leap,” applying lean principles across its operations. The release of Michael Moore's film “Roger & Me” in 1989, which critiqued GM's impact on Flint, Michigan, ended unexpectedly with Moore meeting Roger Smith. This meeting revealed a company amid significant transformation. Smith highlighted GM's new “no layoffs” philosophy and a collaborative relationship with the United Auto Workers (UAW), fostering a stable and engaged workforce environment.
National Recognition and Praise
By 1987, GM's transformative efforts at NUMMI had captured national attention. President Ronald Reagan praised GM as a stellar example of American industrial might revitalized by embracing innovation that epitomized American ingenuity and resilience. Speaker of the House Tip O'Neill highlighted GM's initiative as a model for American manufacturers, demonstrating that traditional industries could adapt and excel amidst global economic shifts.
Maintaining NUMMI and Advancing in EV Innovation
GM fully embraced the lean and collaborative principles pioneered at NUMMI, making the Fremont plant a central part of its operations. The plant continuously adapted and improved, establishing itself as a hub of innovation and excellence, ideally suited for spearheading ventures like electric vehicles (EVs).
With lean manufacturing firmly in place, GM strategically positioned itself as a leader in the EV market. The company utilized NUMMI not just for manufacturing efficiencies but also as a center for rapid prototyping and advanced engineering. This strategic focus dovetailed with growing environmental concerns and a shift towards sustainable transportation, putting GM at the forefront of the EV industry.
Toyota's Ascent and the Impact on Ford and Chrysler
As GM thrived, Toyota also leveraged its TPS expertise, along with lessons gained from NUMMI about operating in America, solidifying its position as a strong number two in the market, surpassing both Ford and Chrysler. The latter companies were slower to adopt lean principles, which limited their ability to compete effectively in an increasingly efficient and innovative automotive landscape. Toyota's rise was marked by its continued implementation and evolution of TPS methodologies, which were not as comprehensively adopted by Ford and Chrysler, leading to a significant reshuffling of market positions.
Navigating the Financial Crisis and Beyond
Armed with a robust lean manufacturing system, a no-layoffs philosophy, and a strong partnership with the UAW, GM adeptly navigated the 2008 financial crisis without resorting to bankruptcy. These strategies provided the resilience needed to manage economic downturns efficiently.
Vision for the Future: Comments from CEO Mary Barra
Reflecting on the impact of lean principles on her career, GM CEO Mary Barra credits the company's early adoption of these practices for fostering a culture of flexibility and continuous improvement. “The lean approach inspired a mindset of relentless pursuit of excellence,” noted Barra. Looking beyond 2024, she emphasized GM's commitment to leading in innovation and sustainability, with plans to expand further into electric and autonomous vehicles. “Our journey with lean manufacturing was just the beginning. As we move forward, our focus is on leading in creating smart, sustainable mobility solutions for a global audience.”
Legacy of Innovation and Leadership
GM not only sustained NUMMI but used it as a springboard for leadership in the EV market, transforming its legacy from a traditional automaker to a leader in sustainable transportation. This transformation exemplifies how organizational changes can foster industry leadership and innovation, showcasing the power of strategic foresight and the enduring value of lean manufacturing principles.
General Motors' trajectory, with NUMMI as a cornerstone, illustrates how embracing transformative change and investing in sustainable practices can renew industry leadership and create a legacy marked by innovation and resilience.
GM's Market Share in This Timeline?
I asked ChatGPT if GM's market share would have evolved the same in this timeline. I was a little surprised that it said yes:
To provide an estimate of General Motors' market share from 1985 to 2024, it's important to look at the historical context and the major trends over these years, given that my last update was in December 2023.
Historical Market Share Overview
- 1985-2000: During the late 1980s and the 1990s, GM was the dominant player in the U.S. auto industry. In the early 1990s, GM's U.S. market share hovered around 35%. However, competition from Japanese automakers like Toyota and Honda began to erode this dominance, and by the end of the 1990s, GM's market share had declined to about 30%.
- 2001-2010: The early 2000s saw continued decline in GM's market share due to increased competition and an aging vehicle lineup. The financial crisis of 2008 and the subsequent recession severely impacted GM, leading to a government-backed bankruptcy in 2009. By 2010, after restructuring, GM's market share had fallen to around 20%.
- 2011-2020: Post-bankruptcy, GM stabilized and began to slowly regain some market share, benefiting from a refreshed vehicle lineup and improved quality. Market share during this period fluctuated, but generally, GM maintained a range of 17% to 18% in the U.S. market.
- 2021-2024: In the early 2020s, the global automotive industry faced new challenges, including supply chain disruptions caused by the COVID-19 pandemic and a semiconductor shortage. Despite these challenges, GM continued to focus on electric vehicles and new technologies, which helped maintain its market share in the competitive landscape, generally holding steady around 17%.
Impact of Lean Manufacturing and Strategic Decisions
If we incorporate a hypothetical scenario where GM fully implemented and capitalized on lean manufacturing principles learned from the NUMMI experience starting in 1985, and managed to sustain innovations and improvements consistently, it's plausible that GM could have mitigated some of the market share declines it experienced historically:
- Better Response to Competition: With a more efficient production system and higher quality vehicles, GM might have been better positioned to compete with the influx of Japanese vehicles, which were praised for their reliability and value.
- Financial Stability and Innovation: Effective lean practices could have led to better financial health pre-2008 crisis, possibly alleviating the need for bankruptcy and allowing for more investment in innovation, particularly in emerging sectors like electric vehicles.
- Consumer Perception and Brand Loyalty: Improved product quality and customer satisfaction could have bolstered GM's brand image, potentially retaining and attracting customers more effectively.
Given these adjustments, GM's market share trajectory from 1985 to 2024 might have shown less dramatic declines during tough periods and potentially more robust recovery phases. While it's difficult to quantify the exact market share without a detailed alternative history simulation, these strategic improvements could have helped GM maintain a more stable and possibly higher market share, potentially staying above 20% consistently post-2010.
Is There a Scenario Where Market Share Could Have Stayed Near 30%?
Holding General Motors' market share near 30% consistently from 1985 to 2024 would require a confluence of highly effective strategic, operational, and market conditions. Here are some scenarios and strategic initiatives that could have supported maintaining such a high market share:
Effective Adoption of Lean Manufacturing
- Full Integration of Lean Principles: Had GM implemented lean manufacturing not just in pockets but thoroughly across all production lines immediately after learning from the NUMMI experience, it could have significantly improved efficiency, reduced costs, and increased product quality. These improvements might have helped GM better compete with Japanese automakers on reliability and value, which were key factors in consumer decisions.
Proactive Response to Market Shifts
- Early Emphasis on SUVs and Trucks: In the late 1990s and early 2000s, there was a significant shift in consumer preference towards SUVs and trucks. GM could have capitalized more aggressively on this trend by expanding their offerings in these segments earlier and more robustly, capturing and retaining a larger market share as these segments grew.
- Leadership in Electric Vehicles and Hybrids: Had GM aggressively pursued electric vehicle (EV) and hybrid technology development early on, particularly after the release of the Toyota Prius and the initial interest in Tesla's roadster, it could have established itself as a leader in this growing segment. Successfully leading in EVs could have positioned GM as a forward-thinking, environmentally conscious company, attracting new segments of the market.
Strategic Financial and Corporate Decisions
- Avoidance of the 2009 Bankruptcy: If GM had managed its finances more prudently and responded more effectively to the warning signs leading to the 2008 financial crisis, it might have avoided bankruptcy. Maintaining financial stability would have preserved consumer confidence and avoided the disruption in operations and brand image that came with the bankruptcy proceedings.
- Global Expansion: More aggressive and strategic global expansion, particularly in emerging markets like China and India, could have compensated for any softening in North American market share by adding substantial new sales and improving global market share. This approach would have required a more nuanced understanding of local markets and consumer preferences.
Enhanced Product Development and Marketing
- Focus on Consumer Needs and Technological Integration: Keeping a close finger on the pulse of consumer needs and rapidly integrating new technologies–like advanced infotainment systems, connectivity features, and autonomous driving technologies–could have kept GM's product lineup more appealing to a broader demographic.
- Robust Marketing and Brand Positioning: Enhancing brand perception through effective marketing strategies that highlight quality, innovation, and customer satisfaction could have helped retain loyal customers and attract new ones, reinforcing a positive cycle of sales and market share stability.
Industry and Economic Conditions
- Navigating External Challenges: Successfully navigating external economic and industry challenges such as the semiconductor shortage, supply chain disruptions, and shifts in global trade policies would also be critical. Proactive management of these factors could mitigate negative impacts on production and sales.
To maintain a market share near 30%, GM would have needed not only to execute internally on production and innovation but also to anticipate and respond adeptly to external market shifts and economic conditions. This scenario, while optimistic, highlights the importance of agility, foresight, and strategic execution in maintaining industry leadership in a highly competitive and rapidly evolving global market.
As somebody who grew up in the Detroit area, starting my career at General Motors, I sure wish it had turned out this way.
Here are some of my blog posts about that GM experience in the OTL:
Please scroll down (or click) to post a comment. Connect with me on LinkedIn.
Let’s work together to build a culture of continuous improvement and psychological safety. If you're a leader looking to create lasting change—not just projects—I help organizations:
- Engage people at all levels in sustainable improvement
- Shift from fear of mistakes to learning from them
- Apply Lean thinking in practical, people-centered ways
Interested in coaching or a keynote talk? Let’s start a conversation.
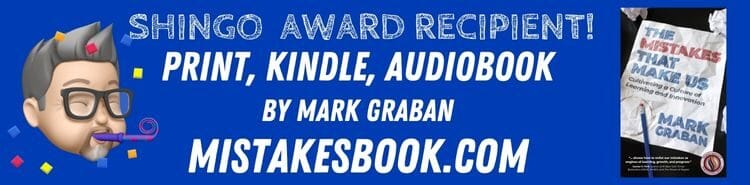