A culture of learning makes the difference, not “low inventory”
Last year, I wrote a post that criticized those, including the Wall St Journal, who claimed that Toyota was “abandoning” the Toyota Production System or that strategically adding some inventory meant they were moving away from “Just in Time” approaches:
Toyota leaders, including my friend Jamie Bonini, were quoted in this new article by HBS professor Willy Shih in HBR:
What Really Makes Toyota's Production System Resilient
Did TPS hurt Toyota during the pandemic?
“In reality, TPS [the Toyota Production System] is really what allowed us to do as well as we did,” Chris Nielsen, executive vice president of Toyota North America, told me. Nielsen oversaw quality and demand/supply management and managed through numerous disruptions over the last two years.
TPS is about resilience not “zero inventory.”

From the piece (with my added bullet points for easier reading):
“Toyota takes a strategic approach to inventory planning.
Operationally this stands on three legs:
- strategically sized inventories in the right locations to act as a buffer to meet changing demands,
- safety stock that factors in the risk of disruption,
- and a nuanced view of lead times.”
Again, these are strategic inventories and safety stocks. This doesn't mean MORE inventory is always better any more than the extreme approach of ZERO inventories would be workable.
Hear Mark read this post — subscribe to Lean Blog Audio
It's About Learning
It's not surprising to see Toyota described as a learning organization, learning from mistakes or otherwise:
It has been pointed out that the company learned a great deal from the Tōhoku earthquake and tsunami of 2011, after which it identified parts vulnerable to disruption and, as a result, were candidates to be stockpiled.
A Different Plan for Every Different Part
Toyota realizes that different inventory strategies are needed for:
- Parts that are relatively simple, being built right near the factory (like seats)
- Parts that are complex, with long and variable lead times (like semiconductors)
You just aren't going to make computer chips on site with one-piece flow that's perfectly synced to the level-loaded mixed-model vehicle assembly schedule.
You need different supply chain strategies, planning, and execution for different categories of parts.
Sometimes, you decide that having inventory (while realizing it's “waste”) is better than the waste of not meeting customer demand.
The company maintains 13 weeks of steel coil inventory in Georgetown because it uses a custom alloy that is made in batches. “Many people have the mistaken impression that TPS is against having inventory; that's not right,” Nielsen said.
They'll also make seasonal adjustments when weather risks (ice or snow) increase the risk of supply chain delays or disruptions. It's an eminently reasonable policy — it's not dogmatic about “zero inventory” or “lower inventory is always better.”
Helping Suppliers, Not Beating Them Up
Toyota also uses dual suppliers — not to play them off each other in a never-ending price war — but to increase supply chain resilience, as the article describes.
Toyota famously helps suppliers improve — which is win/win.
When a suppler encounters problems, Toyota offers to help them address them, and they are willing to accept it. “Our supplier partners open the door for us and say, ‘Look, we know you're not going to penalize us for some mistake we made, and you're here to help, you're part of the team,'” Bonini, the president of the Toyota Production System Support Center, told me.
Learning from mistakes instead of penalizing them. Sounds familiar!!
Learning from Mistakes
On that note, I've captured stories about that from former Toyota people, including Isao Yoshino and David Meier, as part of the “My Favorite Mistake” podcast series (which is becoming a book!).
Learning, Learning, Learning – Culture and Philosophy
It's about learning, like I said, and the article explains, again citing Bonini:
“TPS is a learning system.
“The biggest thing most people overlook about TPS is that it is a system designed for learning.”
The article concludes by reminding us that TPS (and by extension Lean) isn't just about tools and it's not just about inventory. It's a culture and a philosophy.
“The Toyota Production System is an organizational culture as much as it is a factory operating system. Its core philosophy — to motivate and develop people so that they can surface and solve problems quickly and build a culture of continuous improvement…”
Values, Including Psychological Safety
It's not just about “motivating” people to surface problems. It also requires “psychological safety,” as Toyota talks about very directly.
As I quoted from the book Toyota Culture, in this recent blog post:
“Safety [at Toyota] includes more than just physical safety; it also means feeling safe psychologically. This starts with a respectful environment where team members do not fear psychological abuse.”
If we're going to emulate anything from Toyota, let's emulate that?
As Shih concludes (and I agree):
“As with any culture, Toyota's culture is deeply rooted in values. That means if you really want to get the benefits of the company's operating system, it is not sufficient to copy just the tools like lean and just in time. You have to start with the values and beliefs. That makes it much harder to replicate, even though the benefits are clear.”
Please feel free to share a comment below or take part in the LinkedIn discussion:
Please scroll down (or click) to post a comment. Connect with me on LinkedIn.
Let’s work together to build a culture of continuous improvement and psychological safety. If you're a leader looking to create lasting change—not just projects—I help organizations:
- Engage people at all levels in sustainable improvement
- Shift from fear of mistakes to learning from them
- Apply Lean thinking in practical, people-centered ways
Interested in coaching or a keynote talk? Let’s start a conversation.
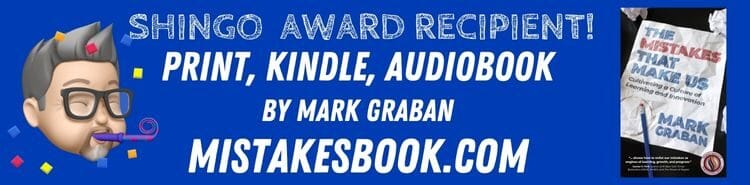