Recently, I re-shared a LinkedIn post by Maryam Najafi PhD, a clinical scientist from Germany.
I re-posted it and that drove even more visibility (over 100,000 views) and more discussion. You might need to click through to LinkedIn to see the entire image.
The comment I initially added was:
This sign could be hung in many types of workplaces. Being open and honest about mistakes then leads to “not repeated.” That could be added to the sign.
Somebody asked on the original post, “What about prevented?” and the response from Maryam was, “Yeah, that too.”
We can be proactive in preventing some problems or mistakes from occurring the first time. Lean methods including mistake proofing and an effective system of standardized work can help prevent some mistakes.
In a standardized work system, need more than an SOP document. We need:
- Accurate, achievable, and helpful standardized work documentation
- Effective training on said standarized work
- Effective supervision of that standardized work
- Continuous improvement of the standardized work
As much as we'd love to prevent all mistakes, the Lean principle of “respect for people” (or “respect for humanity”) recognizes that… we're all human. We're all fallible. We get distracted. We get fatigued. Now, we can design systems that mitigate those risks and human failings, but none of us are perfect.
Former Toyota executive Gary Convis said it well, when it comes to the need for good systems:
“You respect people, you listen to them, you work together. You don't blame them. Maybe the process was not set up well, so it was easy to make a mistake.”
When we blame people, they're less likely to participate in countermeasures that would prevent the next mistake. When we blame people, they learn to hide and cover up mistakes and that means we can't learn and improve.
Sir Liam Donaldson, former Chief Medical Officer for NHS England, says a similar thing:
“Human error is inevitable. We can never eliminate it.” We can eliminate problems in the system that make it more likely to happen.”
Back to the sign… knowing that we're all human (leaders and team members, alike), we have to EXPECT that mistakes are going to happen. Even with mitigation and prevention, people will likely find new mistakes to make.
We can't just lecture people about the importance of not making mistakes. We can't just hang signs that tell people to “be more careful.” Did you know I have an entire blog on that topic?
We have to RESPECT the people doing the work, which means looking at systemic causes and drivers — don't blame people for being human.
To me, INSPECTED means that we have to analyze mistakes — again, looking for systemic factors and then figuring out how to improve (which leads to CORRECTED).
“Corrected” doesn't mean we lambast, lecture, or punish employees for simple human error.
We also shouldn't shrug our shoulders, as I see some leaders do unfortunately, and say, “Well, it's human error… what could we do?” What we can do is improve systems and processes. This supports our employees and leads to better results and fewer mistakes over time.
We explore some of these themes in episodes of the My Favorite Mistake podcast series. We aim to normalize the discussion of mistakes in a blame-free way that focuses on learning, so we don't repeat the same mistakes over and over — in our own lives or in our organizations.
Please scroll down (or click) to post a comment. Connect with me on LinkedIn.
Let’s work together to build a culture of continuous improvement and psychological safety. If you're a leader looking to create lasting change—not just projects—I help organizations:
- Engage people at all levels in sustainable improvement
- Shift from fear of mistakes to learning from them
- Apply Lean thinking in practical, people-centered ways
Interested in coaching or a keynote talk? Let’s start a conversation.
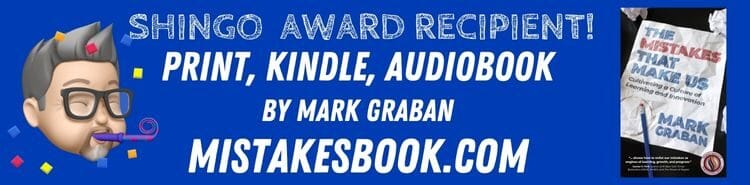