My previous post in this series: A Lean Guy Gets Vaccinated at Dodger Stadium
On Saturday, March 6th, I had the opportunity to visit two mass vaccination sites that were each being run in partnership with the UC San Diego Health System. Thanks to Lily Angelocci for being my main host and thanks also to Tracy O'Rourke for posting about her previous visit online, which spurred me to invite myself (and Tracy joined us on the 6th).
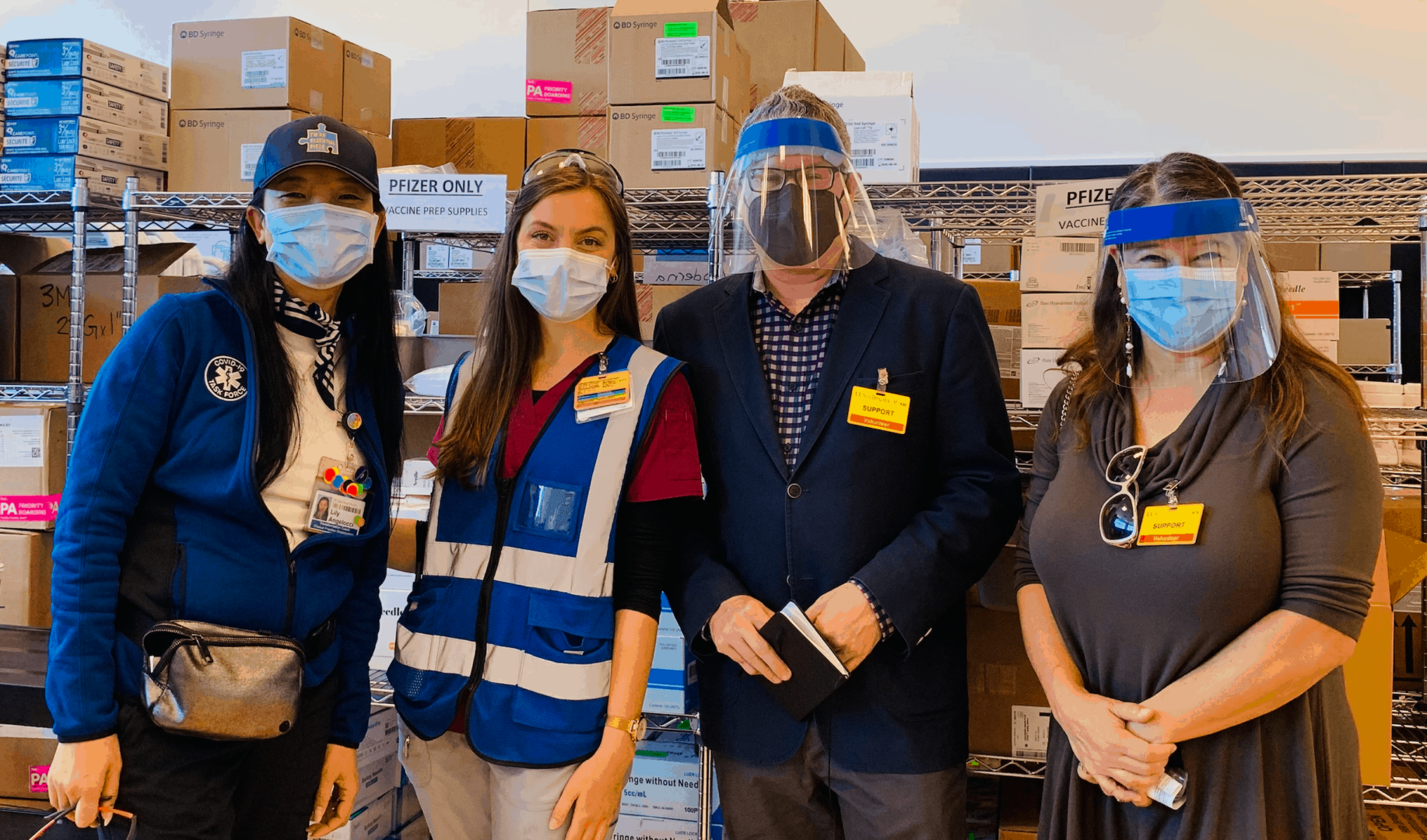
On Thursday, March 25th, I also had the chance to visit a mass vaccination site that was set up and run through a partnership between the City of Frisco (which is just north of Dallas) and TSSC, which is the non-profit arm of Toyota that has done so much amazing pro-bono work with many healthcare organizations and non-profits. Thanks to Elizabeth Chase from the city for hosting me. The site was a former Sears store, and the mall provided the space for free.
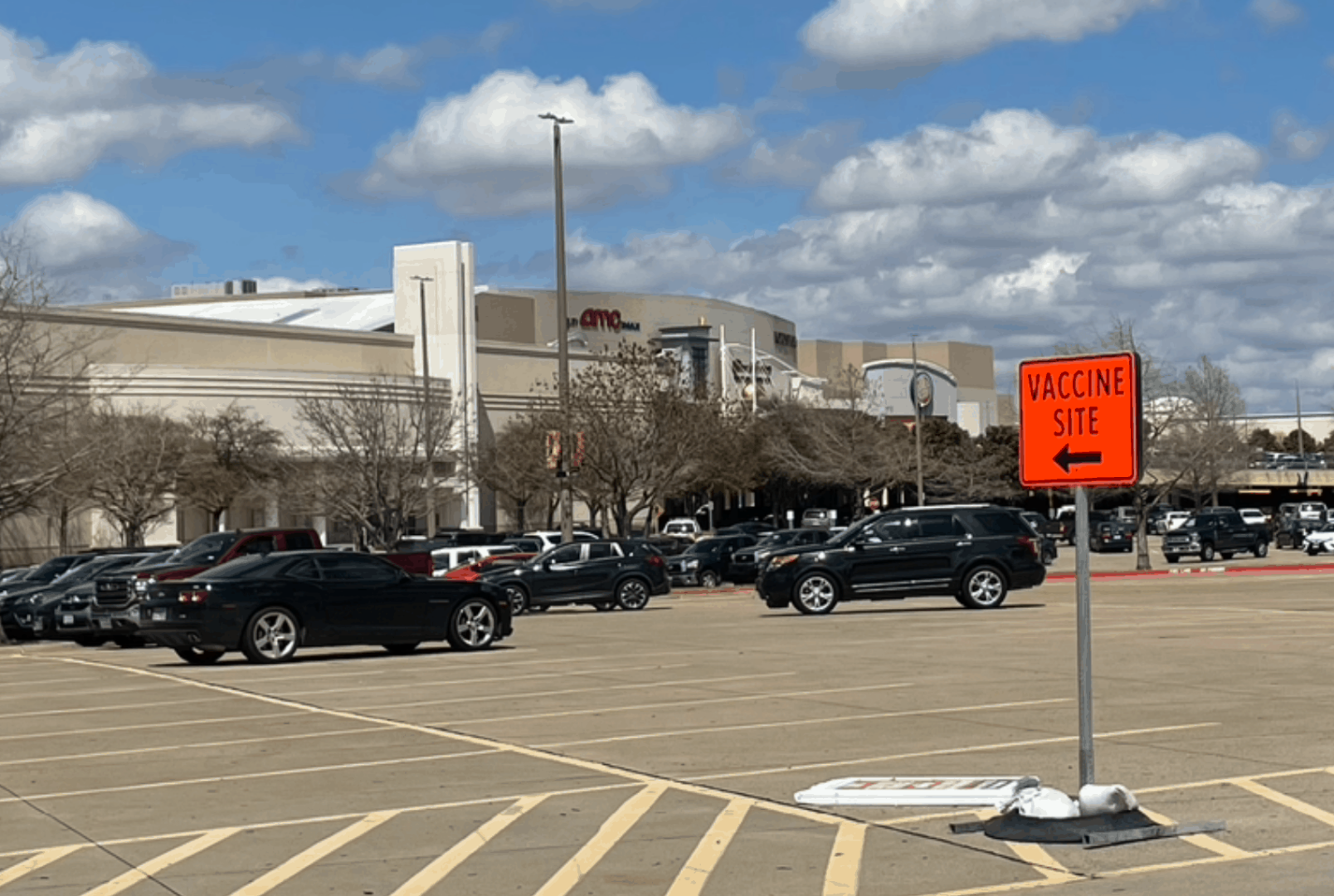
At a high level, the two sites were very similar in their setup and their flow. Both are, of course, heavily influenced by Lean / Toyota Production System. You can see that in the design of the process, the way the people are being managed, and how continuous improvement (kaizen) is taking place.
The San Diego site was set up (and is being managed) by a group of process improvement experts and leaders that included a former NUMMI employee, Brian Hand. NUMMI is the famed California joint venture between Toyota and General Motors that existed from the mid-80s until 2010. So, Brian has that training and he also has experience in many health systems.
In Frisco, the city library has utilized Lean methods for many years (which has been a very helpful strategy in a fast growing city that has grown its population 5x in each of the past two decades).
Elizabeth Chase has been one of the leaders of those library improvement and management efforts. A few years back, I had the opportunity to see their library work and I taught a Lean 101 class for a wide range of city departments.
Elizabeth has been teaching and coaching others, including the Fire/EMS department and she had a major role in the vaccination clinic setup, with major support from TSSC. This Lean training has served them well, given the Fire Department's major role in the operation of this vaccination site.
I wasn't allowed to take photos at the Frisco site, but here is a video overview of their process from a local TV news story:
Here is a write up that Toyota did about the Frisco center (and a Dallas County drive-thru center) with two embedded videos:
Toyota Supports COVID-19 Vaccine Administration
Here are two videos about the San Diego site (RIMAC is the name of the sports facility that is hosting the site)
The high-level flow of both sites is the same, schematically:

I put “Registration & Vaccination” into the same box, because those two steps were being done in parallel at a table with two people working together around the patient (like a two-person pit crew rather than an assembly). Both of these sites had that same design, although the division of work was slightly different).
The registration step — asking questions of the patient, getting their information, doing data entry, and giving information to the patient — was being done by a medical assistance at RIMAC and by a city employee (non clinical) at the Frisco site. At RIMAC, the injections were being done by nurses. In Frisco, it was either city EMS (who are all trained paramedics) or it was National Guard giving the injections.
In this photo, from the main vaccination room where they had 21 tables, with space for up to 24. Not all tables were staffed at all times, as RIMAC (and the Frisco) site was very constrained by limited vaccine supply. RIMAC was vaccinating only about 1,600 people on this day, even though they have capacity to do 5,000 a day if they are running full out.
You can see each table has two people working with a patient.
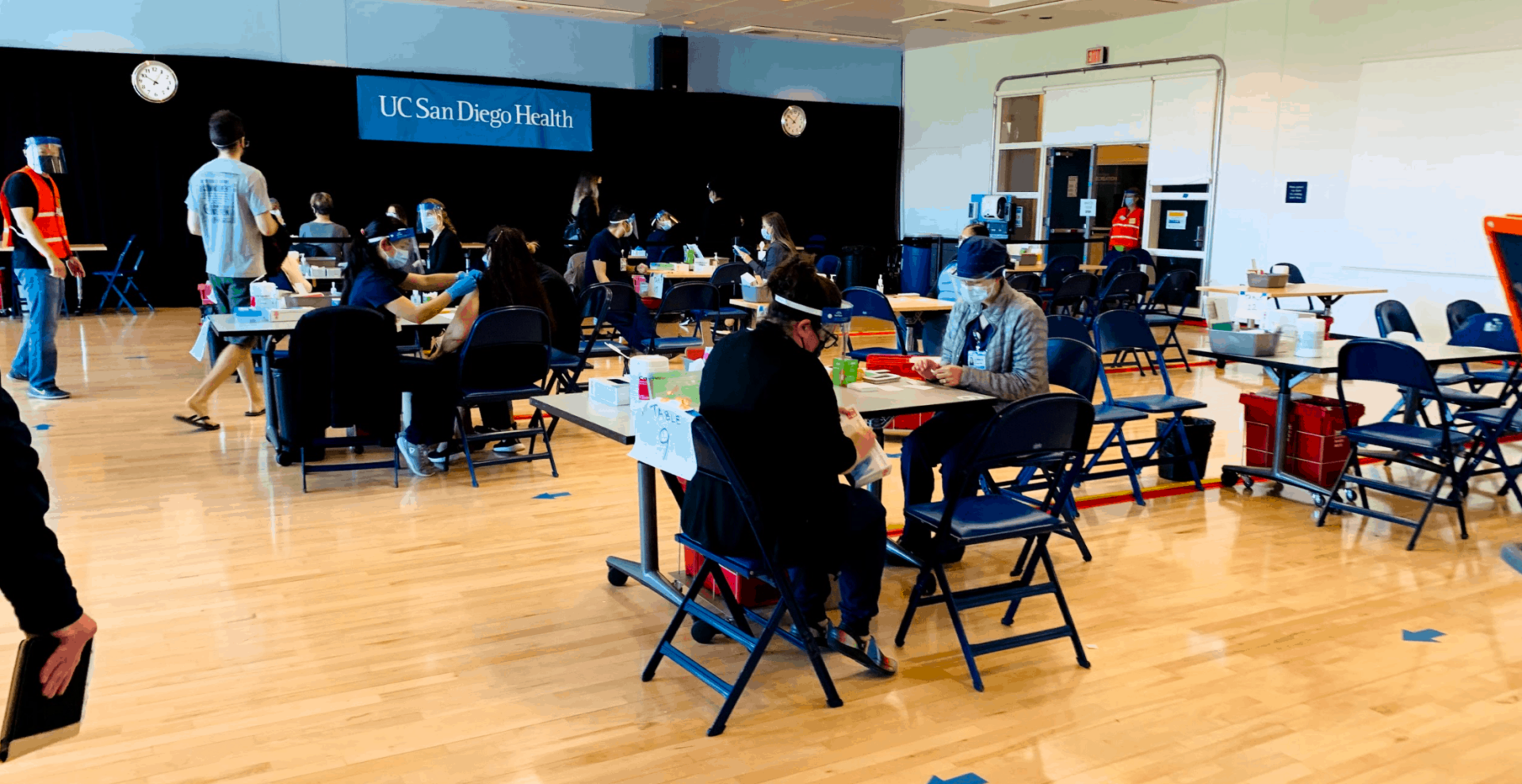
The Frisco site had 12 vaccination tables and a capacity of 4,000 people a day. The week I visited in Frisco, they were receiving only 8,000 doses, so they ran full out for two days and were closed the other days.
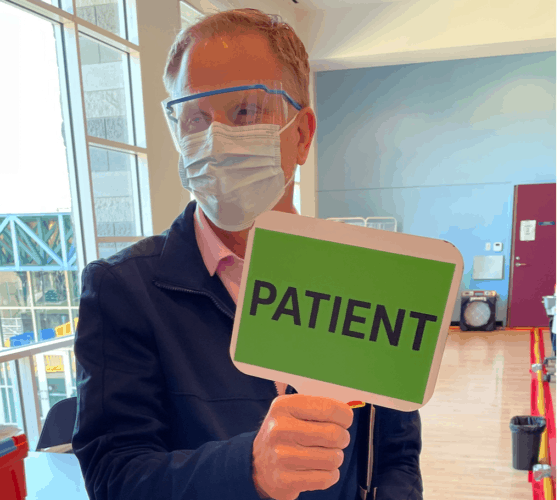
At RIMAC, at the front of the queue closest to the vaccination room, they had four dots on the floor that were staging patients who were ready to be sent next to a vaccination table. There were volunteers tasked with look for signals given by tables when they were ready for the next patient. The photo here shows Brian Hand holding one of those paddles.
When that green paddle goes up, a volunteer would point a patient to the table, or they might escort them over there.
At the Frisco site, there was better overhead visual management, including large numbers that made the location of each of the 12 numbered vaccination tables really clear and obvious.
When Tracy and I were observing the vaccination work cycles at one of those tables, the teamwork was amazing. Each patient was cycled in and out in about 80 seconds. The work was efficient, yet un-rushed and kind. If a person had questions, those questions were answered — they weren't rushed along because “their time was up” or anything like that.
The table we were observing was one of the furthest from the final queuing spots.
We'd observe something like this:
- Vaccinate a patient (80 seconds)
- Wait for next patient to walk over (60 seconds, but varies based on the patient)
- Vaccinate a patient (80 seconds)
- Wait for next patient (60 seconds)
- Repeat
You can see that the “waiting for next patient” was a 43% hit on their productivity. They didn't need that wait time to prep for the next patient. It was waste. They could do about 25 patients per hour given those cycles. 25 patients x 21 tables = 525 patients per hour and 10 hours a day is over 5,000 patients, or their stated capacity.
Note: that delay between patients time was shorter at the tables closest to the queue
Without that delay, the table could have vaccinated up to 45 patients per hour running full out.
When my hosts asked me for ideas or observations, one of the few suggestions I could think of was reducing that waiting time for the vaccination teams.
Could patients be staged “on deck” closer to the tables? Could there be an “on deck” spot to stand or sit that was right near each row of tables?
Now, when I visited the Frisco site, I saw a very similar idea in use. Here's a schematic of each of the 12 tables:
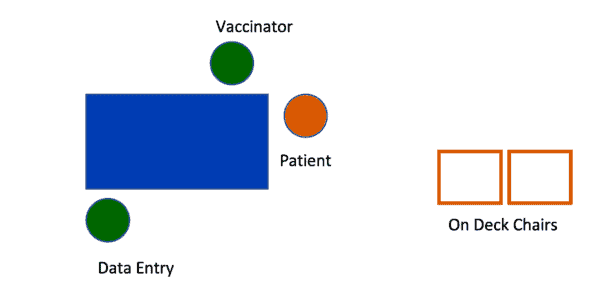
They had two “on deck” chairs next to each table. That represented one patient — the second chair was if they had somebody accompanying them. The chairs were six feet away from the vaccination table, hence minimizing that delay until the next patient.
I learned that these on deck chairs were NOT the original design. Adding those chairs was a Kaizen countermeasure that came up from observation and discussion with the team.
Here is a Toyota video about using on-deck chairs (“next patient chairs”) at a free medical clinic in Mississippi:
Both the San Diego and Frisco sites had an emphasis on engaging everybody in continuous improvement, as you would expect from Toyota-trained people.
So, at the Frisco site, their patient flow staff members would look to see where there was an empty patient chair at a vaccination table OR an empty on-deck chair if there were no open spots at tables yet.
I saw many instances where the patient arrived at the on-deck chair just as the previous patient was leaving the vaccination table (where the cycle times were only 60 seconds, by the way). “No, you don't have to sit there, come on over.” They could vaccinate up to 60 patients per hour with this workflow (but accounting for variation and other issues, they might not hit that ideal rate).
By the way, speed and flow was not the only thing that mattered to the Frisco team. Their five core city values include “outstanding customer service” and “operational excellence.” They were creating a happy, positive, and calm environment… that means not rushing people or stressing them out in the name of flow or speed.
I shared the “on deck” chairs idea back with Lily in San Diego. They were thinking of trying this, but hearing about it working well for the Frisco clinic gave them more confidence to try it.
As vaccine supply constraints are less of an issue, the need to increase hourly throughput like this becomes even more important.
I'll hopefully be able to share results from what they try in San Diego at the RIMAC site.
This type of sharing is what we are facilitating in our free VacciNexus platform. We are also doing a weekly Zoom meeting where people from different health systems can compare notes and discuss things live.
During our last discussion, we talked about on-deck chairs and somebody raised an interesting issue: what if the patient is sent to an on-deck chair when the patient ahead of them has some delay… are they stuck in that on-deck chair? Is that like choosing the wrong line at the supermarket?
Maybe, but that delay might be very minimal. You could always redirect the patient to another table if there was a big delay at the table for some reason. I think that could be addressed.
At the Frisco / Toyota site, it was working for them.
There are MANY other aspects of the vaccination site visits that I could blog about, and I will.
My next blog post will be about the benefits of “drawing vaccines in a specialized subassembly area” rather than drawing up the vaccines at each table. When we combine the patient flow with the syringe flow, we might see a schematic like this:

I believe the “subassembly” area is really the best way to maximize throughput and minimize patient delays.
Please scroll down (or click) to post a comment. Connect with me on LinkedIn.
Let’s work together to build a culture of continuous improvement and psychological safety. If you're a leader looking to create lasting change—not just projects—I help organizations:
- Engage people at all levels in sustainable improvement
- Shift from fear of mistakes to learning from them
- Apply Lean thinking in practical, people-centered ways
Interested in coaching or a keynote talk? Let’s start a conversation.
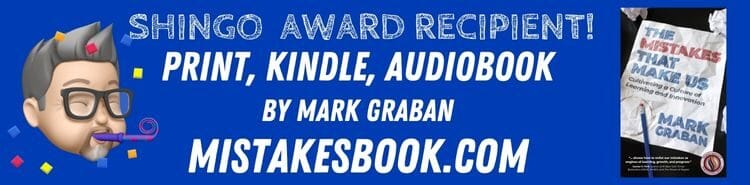
LinkedIn Discussion:
Mark
Just comment to make about the deck chairs, The picture shows the painting of a line on the ground around the chair. While people might not realise it, that line has played an important role in making sure people stay safe and also avoided vaccination staff having to waste time reordering chairs again and again.
Picture this, aged 70 +, you have been coocooning for 8 months, haven’t seen a soul to catch up in the local gossip with for months. You are down in the local gym hall for your vaccination and afterward you are sitting out your 15 or 30 minutes and you see Mary or Deloras who you haven’t seen for months. You can’t hear her properly so unconsciously you go to move the chair closer.. But then you see the boundry tape on the floor around and are reminded of the 2meter separation so stay put. Then as you leave being the tidy person you are you put the chair right back in the centre with the precision found in every grandmother….. Yes that tape keeps people safe and reduces the time those running the centre have to spend reordering the deck chairs in the vaccination centre.
I’ve seen and watched it in action — its the little things that count a lot sometimes.! :-)
Hey Mark! I think the idea of an “on deck” chair would make a great difference. Those extra 20-30 seconds between patients walking to the table could mean more people getting vaccinated in a shorter period of time. This would make the site more efficient and effective, while helping more people in a given day, and possibly shortening their work day. Like you said, it could vary from patient to patient, but I definitely think an “on deck” spot could be more effective in the short and long term.Thanks for sharing!
Hello Mark,
I like the point that Joe Fortin pointed out, the on-deck system. This “on deck” system can be extremely effective considering that it could cut down the waiting time by half. This could be extremely effective for older groups of people who might have trouble walking, also gives them a chance to sit down and rest for 80 seconds. That 43% hit on their productivity could be reduced by a lot just by implementing this system. I think that every vaccination center should have an on-deck process.
Hello Mark,
This was a very interesting blog post, to start I really like the idea of make a small change that could make a huge difference. This really shows the power of lean because everyone wants things to go back to normal, and the first thing to is get people vaccinated. if the process of having an on deck chair could increase the rate of nation wide vaccines that could go a long way to getting the economy back and getting America healthy again.