When I started my career in the auto industry, I learned that a “not defect” is a product that doesn't meet specifications in some way. An “escape” is a defect that reaches the customer.
Through inspection and other quality tests, you hope to prevent any defects from escaping. Even Toyota has final inspection areas in their assembly plants (even in Japan).
The ideal state, of course, is to build quality in at the source… to do it right the first time… but even Toyota doesn't do that 100% of the time. They don't have zero defects and they don't have zero escapes, as good as they are.
Escapes in Published Books
When it comes to book publishing, it seems EVERY book ever published has some defect… and it's an “escape” because it reached the customer — or the reader.
As I blogged about, Jeff Liker‘s book The Toyota Way and the first edition of my book Lean Hospitals, both had defects on the very FIRST page of the book, as I blogged about here:
There was one other particularly annoying error in the first printings of Lean Hospitals. This is how the one figure was supposed to appear, with arrows going up and down. The caption below the figure refers to going up and down in the organization.
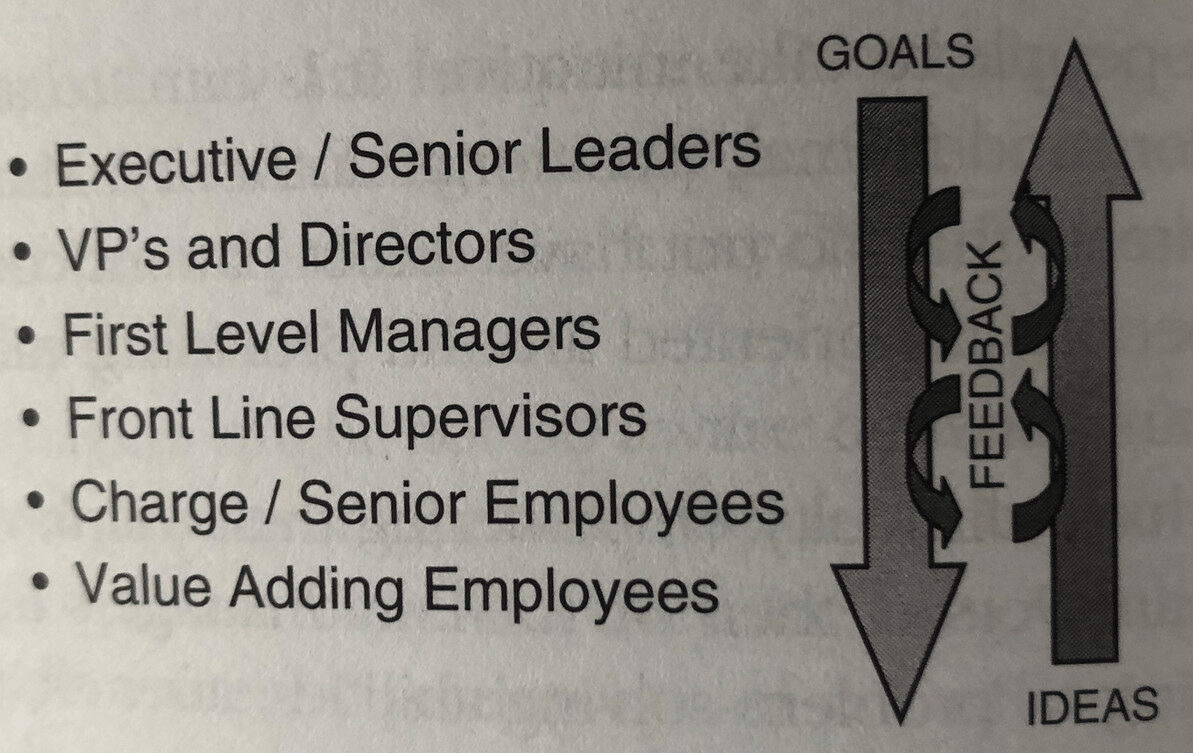
In the publishing process, a PDF of the book gets thrown back and forth between the author and the publisher's people many times.
When I reviewed what's called the “Final Pages” PDF of the book, the figure was correct.
Somehow, a new defect got INTRODUCED between Final Pages and printing. Needless to say, that is NOT supposed to happen.
What got printed was this:
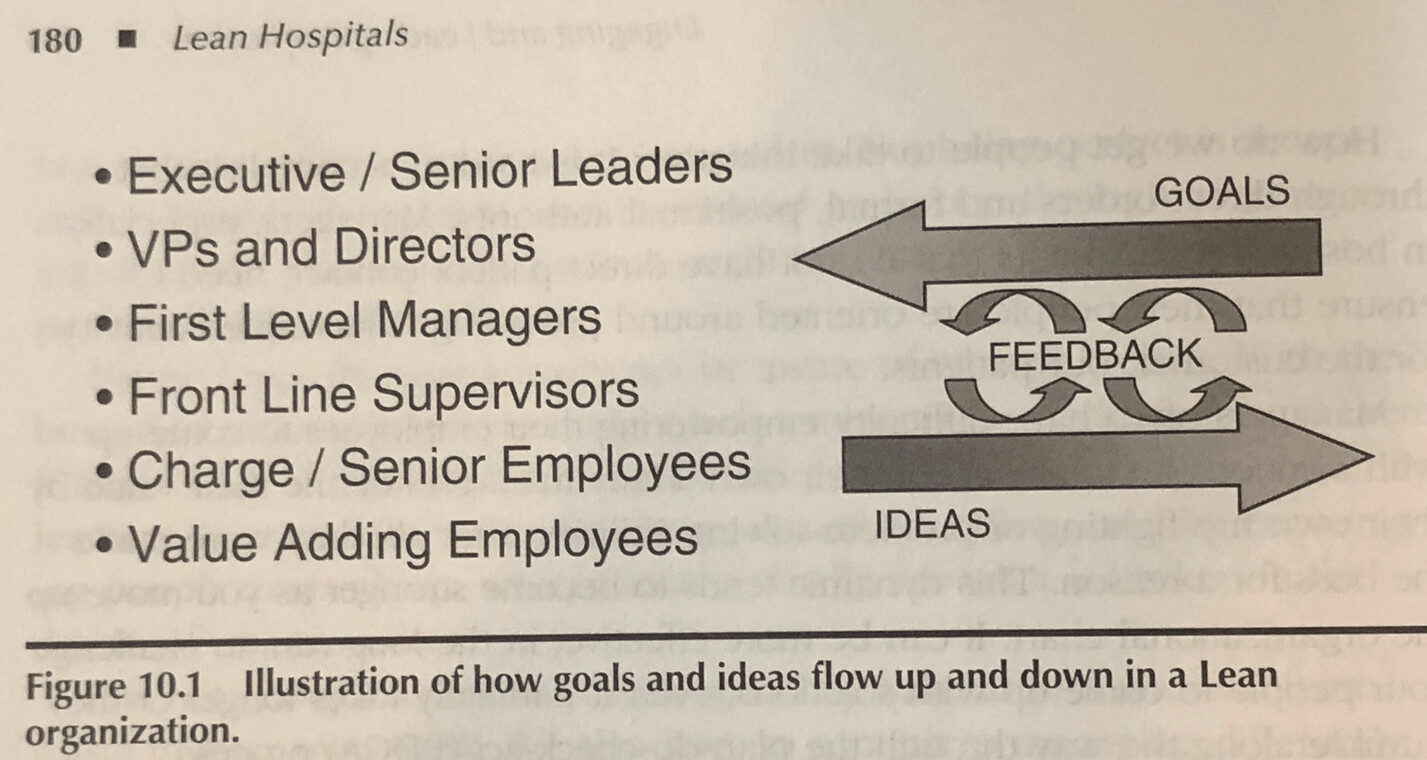
I don't know if rotating the graphic somehow made it fit better on the page. It didn't seem like it was really the case. Was a disgruntled employee sabotaging the book? Again, note how the caption says “flow up and down.” That was frustrating. It was probably a bad process, not a bad person.
But, we're all human. Organizations are made of humans. 100% inspection is never 100% effective — even at Toyota.
But, I still wonder why somebody at the publisher apparently didn't follow the process. If they felt the need to make a change, it should have led to a “Final Final Pages” document that should have been thrown back to me for review. That would have been the proper process, but alas.
Error Cards — Baseball
When I was a kid in the 1980s, I loved baseball cards. A special treat was finding an “error card.” Yes, even professional baseball card companies sometimes had glaring mistakes. These included:
- Misspelling a player's name (like “Craig” instead of Graig Nettles)
- Reversing the negative (leading to a left-hand hitting Hank Aaron, shown below)
- Editors not noticing Billy Martin's middle finger (I own this card)
- No name appearing on the front of a Frank Thomas rookie card
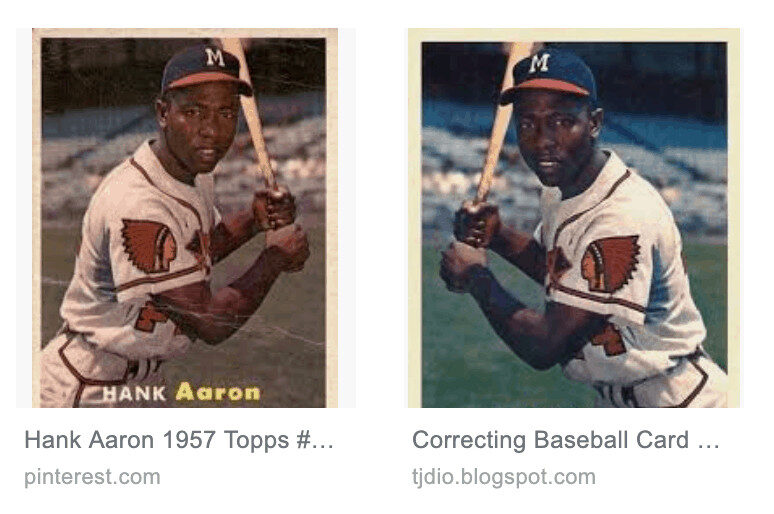
The card companies would then start printing corrected cards, at some point, but the error cards were already out into the wild. Sometimes, these error cards are pretty valuable because of the scarcity.
Will the same be true with some of the first printed paperbacks for my book Measures of Success?
Nobody's Prefect
When I self-published my latest book Measures of Success as an eBook, I used a professional editor to work with me… and there were still some typos and other small defects that got through — escapes.
One great thing about self publishing is that I can very quickly and easy make updates in the eBook publishing platforms. With a traditional publisher, I found that they didn't want to make many changes… partly because they were printing big batches of paperbacks. Now that my book is a paperback, it's printed (by Amazon and IngramSpark) using “print on demand” technologies. So, it's likewise easy to make updates to the PDF file that I upload to them for the interior of the book.
And, oh, did I need to make updates.
People sometimes confused the words “honored” and “humbled.” I was honored to be invited to speak at the “Systems Thinking TO” group in Toronto last night. It would have been humbling if I had given a talk that nobody liked or told jokes that nobody laughed at. Last night was more honoring than humbling.
What's humbling is making mistakes and letting book defects escape to customers.
When I was getting the back cover designed, I felt under time pressure because I was generally busy and, thankfully, many people were emailing me to ask when the paperback would be available.
I shouldn't have rushed.
When I got the first books, I was appalled to see a typo that I didn't catch before approving this with Amazon. I should have asked somebody with fresh eyes to review this, but I skipped that step. Lesson learned.
It says, “With methods grounded in the Lean, math, and science…”
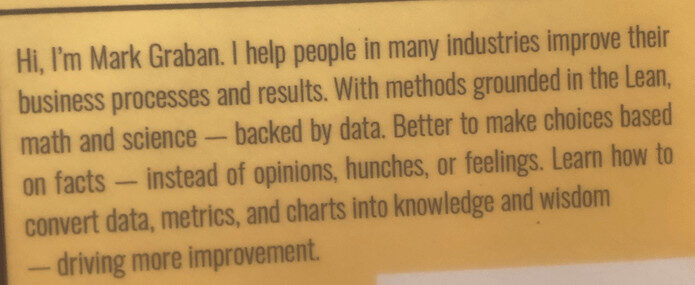
Oops! It said, “… in the Lean methodology” during one iteration. I don't know how and when that word disappeared. As the publisher and the final approver, I only have myself to blame.
The back of the book, as it's currently shipping, says simply, “…grounded in math and science…”
Again, it's not like a large batch of hundreds or thousands of books got printed with that defect. It's a defect that many people might not notice, since our eyes sometimes help our brain read what we think it says… or people might just wonder what “the Lean” is.
There is also something about the front cover that really bothered me when I noticed it. I've shown the physical book to many people and it doesn”t jump out at them at all, so it's a less severe defect. Can you see it?
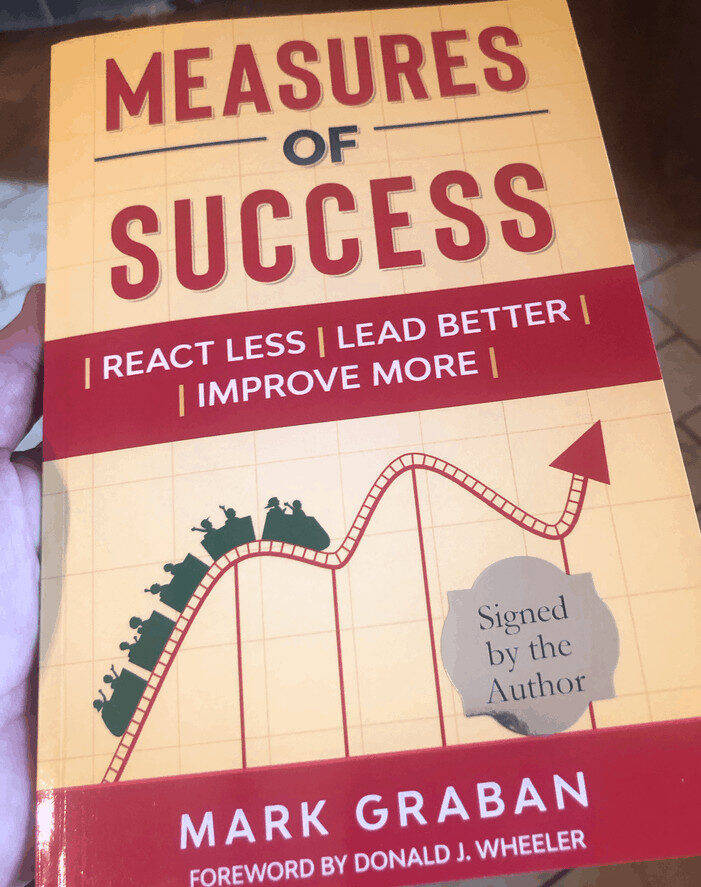
When I got the initial “proof ” printed by Amazon, the front cover was correct, but the “MEASURES OF SUCCESS” text was a bit too close to the top edge of the book. The back cover was fine at that iteration, by the way.
I asked my cover designer, I think quite literally, to “move down the MEASURES OF SUCCESS text so it's better centered in the top section.” He did that. Below, the left shows the eBook cover. The right shows the print cover front with the defect… can you see it?
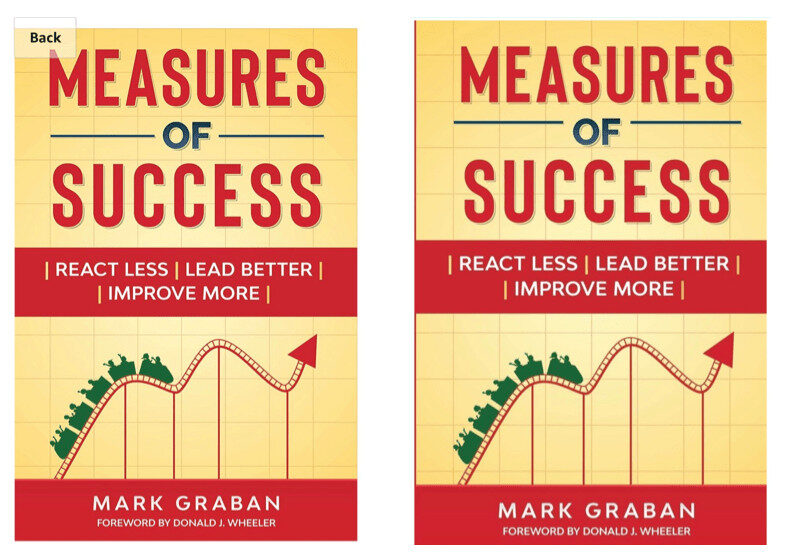
The blue lines around “OF” didn't get moved down. Again, I don't think I asked the designer to do that… I assumed he would and he didn't. That's MY fault for giving poor direction and it's my fault for not noticing the line placement for submitting it to Amazon for an update.
So, again, that's now fixed for any books that are ordered and printed after today.
I started lamenting to myself that I have a bad combination of personality traits. I'm a perfectionist… but I also don't have the greatest attention to detail. So, I end up making mistakes and getting mad at myself.
I thought, “Well, the interior of the book is probably fine because there was my initial copy editor and then the firm that I hired to design the book interior had a professional proofreader.”
Well, some sharp-eyed early readers found a few bugs, or defects.
On page 124, it says “softwar-development” instead of “software-development.”
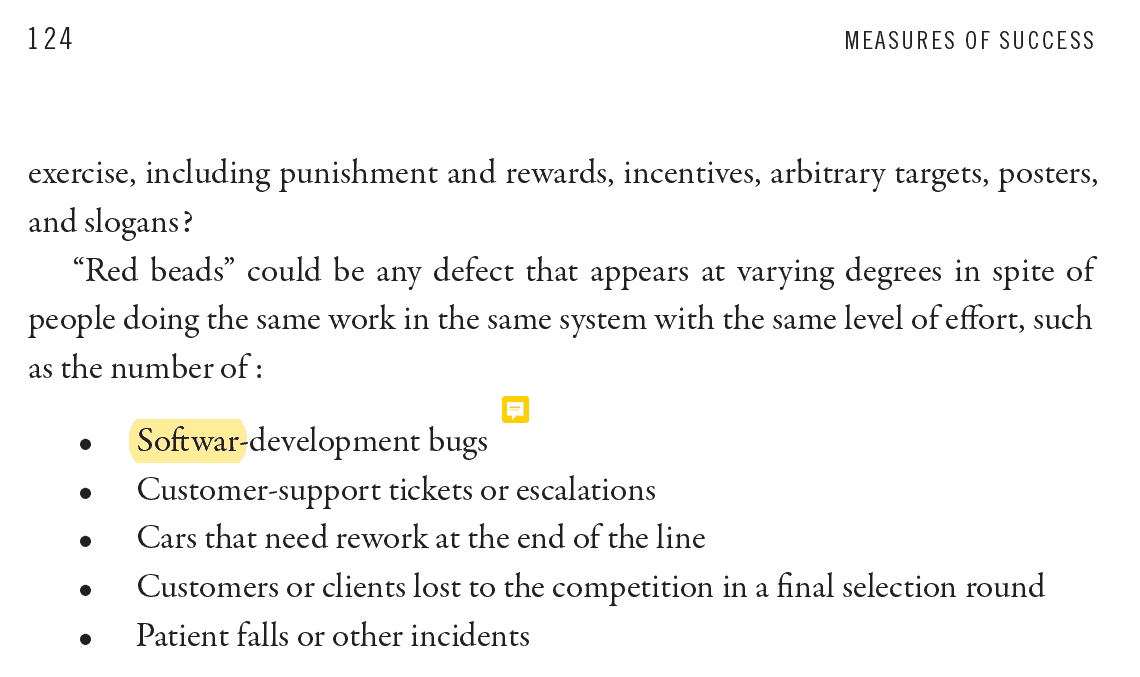
Oops! That defect was not in the manuscript that i sent to the design firm. So when was that defect introduced? I went back through the different PDF iterations. It was NOT in the initial PDF that the design firm created. That was the PDF that I read most closely. Somehow, that defect was introduced by the design firm in the second PDF iteration. Nobody caught that. Not a big deal. that's now fixed.
Here is another weird defect…. “ssafe-driving.”
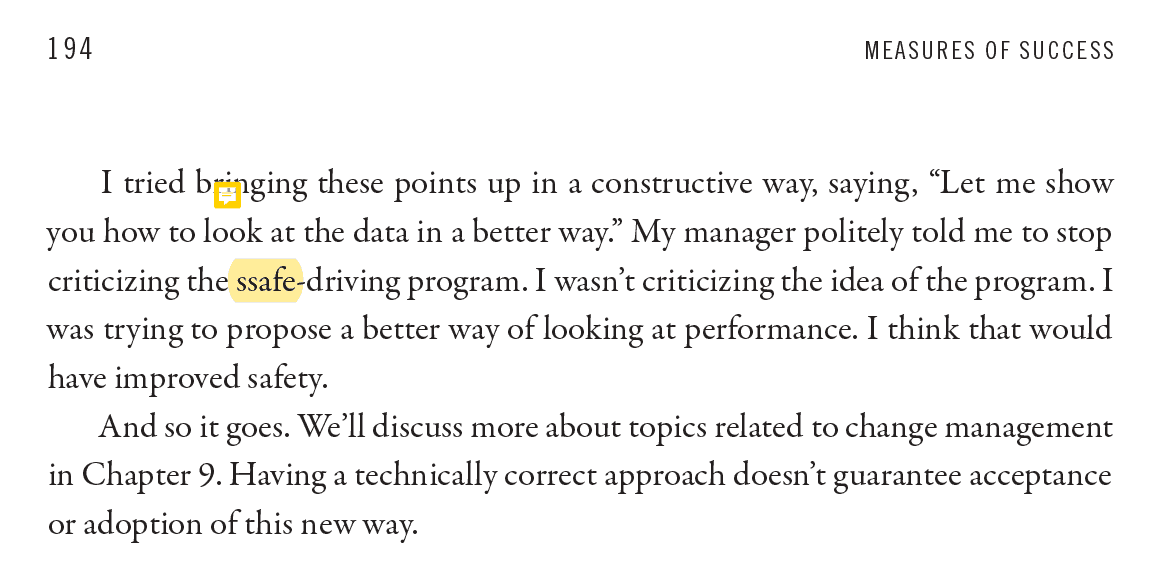
The “ssafe-driving” defect also got introduced for the 2nd PDF iteration. Nobody caught it, including myself. Oh well, not a big deal.
Part of the issue, I believe, is that the book design software does NOT include spell check as a feature. That's what my former publisher told me years ago and that seems to be the case here. How is that possible??? Adding spell check would be a great improvement to the system, eh?
Defects That Were Completely My Fault
There were a few other defects that were clearly my fault, in the manuscript and early eBook releases.
For this chart, the text below it refers to “April 17, 2018” when that was supposed to say “April 17, 2016.” That was the defect of muscle memory typing the current year instead of the correct year. This is now fixed.
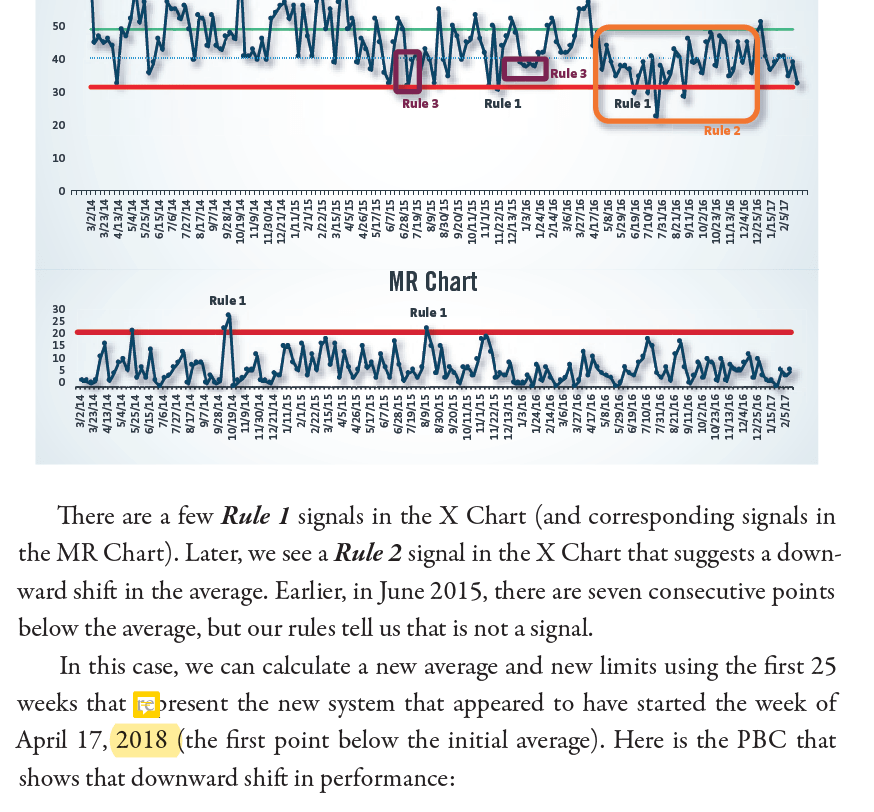
In the chart below, it's mistakenly labeled “Weekly Leads” when the chart shows monthly data. That's now been fixed. That's my fault and my inattention to detail…
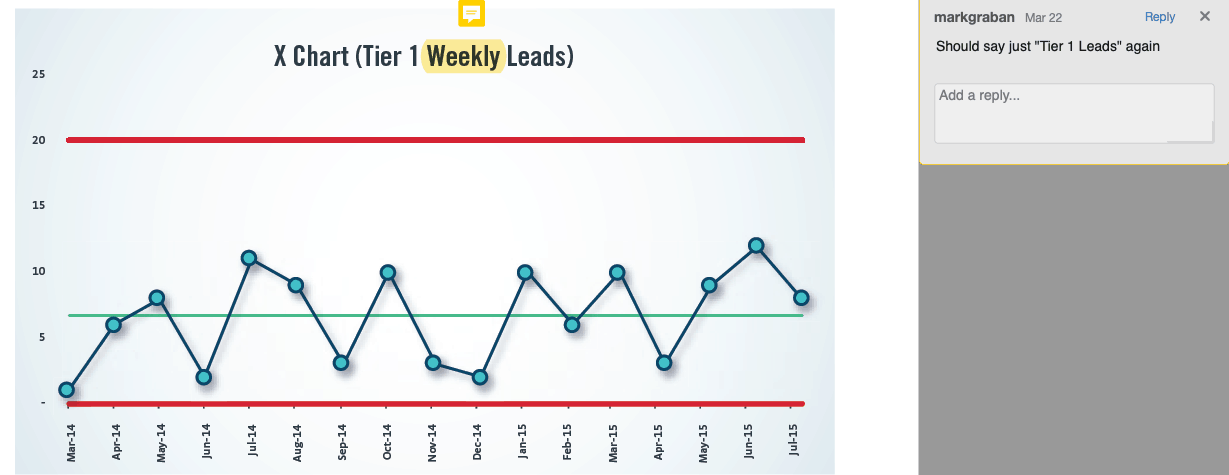
There was another chart where my submission to the design firm (and my initial eBook) was correct. The orange line's label was supposed to say “Dec 2010 – Nov 2011”. A defect was introduced when the designer was re-doing the graphics… and I didn't catch it. This has been fixed.
There was a more significant error in a chart on Page 157… totally my fault. The chart had an extra data point in it, somehow… the X-axis dates were wrong… oops. That has been fixed.
Humbling
Again, this is all really humbling. I try to be perfect and I have high expectations. I probably have unrealistic expectations. I'm human. We all make mistakes.
My wife and some author friends have reminded me that:
- The errors are not a big deal
- Every book ever printed has defects
I take solace in remembering that The Toyota Way and Lean Hospitals both had defects on PAGE 1. And that was with two different professional publishers involved.
I do feel bad that the earliest, most enthusiastic buyers of the book got books with defects. If you're one of those buyers / readers… maybe you can laugh at having a collector's edition.
Or, if you want to exchange your book for a freshly-printed copy with fewer defects (I won't say it's defect-free), please contact me. If your book is in reasonably good shape, I can do an exchange for you.
On the Positive Side
It is worth remember (and saying) that I love the work that was done by the design firm. People have told me that it's a very visually appealing book. I agree. I'm proud of the result.
More importantly, the book is proving useful to people… one review on Amazon.ca says:
“I finished this book about a week and a half ago. Mark has created an excellent companion and guide for those of us who seek continuous improvement while facing the demands for “meeting” targets from upper management. It is well explained and filled with clear and valuable examples.
I am certain that upper management can use the understanding of data and systems presented in Measures of Success as well.
Practically, Mark and his book helped me to focus on signals and have a clear understanding of noise. The data driven perspective allowed me to recognize that what I thought was noise was indeed a signal and make changes to the system rather that simply seeking “better” work from my team.As a result my KPIs have jumped exponentially to return us to a leading position. Of course, we need to see that this is a new trend and not a blip…but the main thing is that I can see better and therefore focus where needed based on data and signals NOT noise and normal variation. I will continue to rely on PBC's and the understanding shared in Measures of Success for the rest of my career!”
It feels good to get a 5-star view. What's even better is knowing that the book is helping people and their organizations. The writer of that review has emailed me and told me more about the story and what company it is. I can't disclose that, but it's a company that's personally important to me and I'm happy to have helped! I hope the book helps others, warts (defects / escapes / bugs) and all.
Please scroll down (or click) to post a comment. Connect with me on LinkedIn.
Let’s work together to build a culture of continuous improvement and psychological safety. If you're a leader looking to create lasting change—not just projects—I help organizations:
- Engage people at all levels in sustainable improvement
- Shift from fear of mistakes to learning from them
- Apply Lean thinking in practical, people-centered ways
Interested in coaching or a keynote talk? Let’s start a conversation.
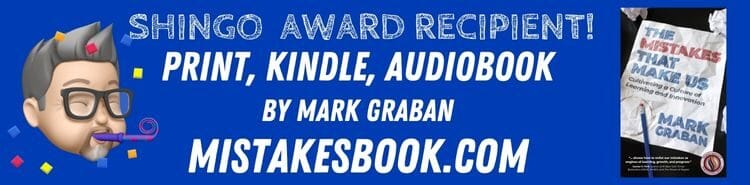
Was the typo in your blog intentional? :-).
” It didn’t seem like it was really the cas.”
No, but “Prefect” was intentional 🤓
Hi Mark,
There is another error in your post. I won’t tell you what because I know you are OCD and will look for it. Hint- not capitalized and should be.
But really this is so funny because I could say the same things about the books I wrote. We need to do a podcast on this issue of mistakes. The thing about a book is once it is printed that error is forever…on that copy anyway. And like you with The Toyota Way Fieldbook there were so many errors and I tried to find the root cause. It seemed unusual that in a copy/paste digital world that errors were introduced AFTER the manuscript was sent in. Jeff and I split the book in half and put pink post-its on each page with errors and I think there were well over 100! I took a photo and need to find it to send you. A lot of it has to do with how our brains “fill in the gaps” and “autocorrect” things we look at. That is an interesting study and helps with the question of “Why we make mistakes” which is a good book by the way.
At the distillery we had our first four labels printed and three had typos! And since then most labels have some “error” which most people will not notice but I do. But the analogy is kaizen. I learned kaizen does not apply to original creation. So the first effort has “flaws” and then you work to improve. It does suck though to preach “improvement” and then put out a product with errors.
But you only make mistakes if you do something so kudos to you for making the effort!
The big-name publishers and their subcontractors use different software to layout a book — typically QuarkXPress, which strips all formatting from and special characters from MSWord docs which is usually what authors use to write books. The conversion from MSWord to Quark introduces hundreds of new format errors, typos, etc. Finding all the errors is maddening for authors, and most copyeditors don’t know what they are reading (in terms of how text and other features should look). Having written and published books where MSWord was converted to Quark and then into .pdf format, and where only MSWord was used and then converted to .pdf, I can say that using Quark is unnecessary for many (but not all) types of books. Publishers could easily provide standard MSWord formats to authors in the most popular book trim sizes, with headers, pagination, etc., all conveniently set-up ahead of time. I long ago quit the Quark to MSWord conversion mess.
Yes, for relatively simple books, it’s quite possible to go directly from Word or Google Docs into a paperback book through Amazon.
One more thing Mark, at Toyota we talked about the fact that an error (defect) occurred and also why it was passed on. As you call them defects and escapes. There are different reasons why they happen. The root cause of a defect is some mistake, but the key thing is why was it not detected and stopped. Overlay that with the Toyota concept to “Never knowingly pass on a defect” and you can see the mind set was we make mistakes but to recognize and admit the mistake and do not hide it. And I don’t know about you but when I write it is the same as if I am having a conversation and in writing it is not always good to use that style. So I had to do a lot of “correction” based on that. And reading this post I could re-write it many times. But eventually you have to let it go!
Thanks for the comments and stories, David. We’ll have to compare notes sometime over from Glenn’s Creek Distillery products.
It does, again, make me feel a little bit better than professional publishers can’t create a defect-free book. Or, they can’t prevent escapes.
It’s interesting, like you said, that defects get INTRODUCED along the way. The two escapes of “softwar-” and “ssafe” were created when the designer fixed two things in the same area. The company I worked with said, “We’ll tell him to be more careful” probably won’t be an effective countermeasure. We’re all human.
In healthcare, where the stakes are life-and-death, we can’t just throw up our hands and say, “Well, it’s human error — what can we do?” What we can do is build better systems… manage and lead better… we can work at it. Working at it (and being transparent) is better than not working on it (or hiding the problem).