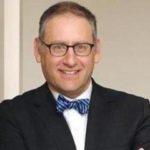
My guest for Episode #262 is Steven J. Spear (@stevenjspear on Twitter). He is author of the fantastic book The High-Velocity Edge: How Market Leaders Leverage Operational Excellence to Beat the Competition.
He's a Senior Lecturer at the MIT Sloan School of Management and recently taught a summer course on Lean and Six Sigma for the Leaders for Global Operations program (I graduated from that program in 1999 when MIT was teaching TQM in that summer course) and he also teaches executive education programs for MIT Sloan.
Steve was previously a guest in Episodes #58 and 87. I'm glad to have him back on the show after six years.
You can read a summary and quotes from the podcast via LinkedIn (Part 1 and Part 2).
Streaming Player (Run Time 44:09)
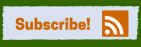
For a link to this episode, refer people to www.leanblog.org/262.
Topics & links for this episode:
- Steve's article “Beyond the Jargon,” which forms the basis for this conversation.
- As you write, “jargon like “gemba,” “kaizen,” “LEAN,” statistical process control” seems irrelevant to people in healthcare and contrary to the medical approach?
- How can we help people see the parallels and applicability?
- Why do outsiders think manufacturing is “deceptively “routine”?
- Are there examples of “better apples” that you've seen in healthcare recently who are dramatically outperforming others, even though they have the same underlying equipment, facilities, and staff credentials and education?
- “Some organizations are delivering more value, quicker, and easier.”
- “You can never delegate responsibility [as a leader].”
- To receive some articles from Steve, send an email to HVELLC@sendyourslides.com with the subject line HPE-HVE
Podcast Summary
You can also read and download a 4-page PDF summary of the podcast as:
- Low resolution (to read on screen)
- High resolution (to print)
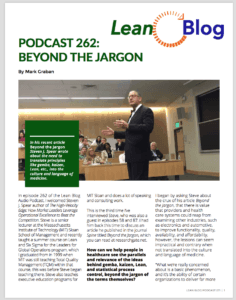
Audio Clips:
For earlier episodes of my podcast, visit the main Podcast page, which includes information on how to subscribe via RSS, through Android apps, or via Apple Podcasts. You can also subscribe and listen via Stitcher.
Thanks for listening!
Past Podcasts and Blog Posts:
Videos with Steve Spear:
Transcript
Announcer (42s):
Welcome to the Lean Blog podcast. Visit our website at www.leanblog.org. Now here's your host, mark Graban.
Mark Graban (53s):
Hi, this is Mark Graban. Welcome to episode 262 of the podcast. It's September 12th, 2016. My guest today is Steven J Spear. He is author of the fantastic book, the High Velocity Edge: How Market Leaders Leverage Operational Excellence to Beat the Competition. Steve is a senior lecturer at the MIT Sloan School of Management. He recently taught a summer course as he's done the past few years on Lean and Six Sigma for the Leaders for Global Operations Program. I actually graduated from that program in 1999 when MIT was still basically teaching TQM in that summer course. That was before Steve came over to MIT.
Mark Graban (1m 35s):
He also teaches executive education programs for MIT Sloan and, and does a lot of speaking and consulting work. Steve was previously a guest in episodes 58 and 87. If you want to go into the archives and find those, I'm really happy to have 'em back on the show after it's been six years. Steve is going to be one of the keynote speakers at the upcoming Northeast Lean Conference, which is being held October 4th and fifth in Massachusetts. It's produced by G B M P. I hope you will check it out. It's, I've participated in past years. It's always been great. And you'll also get to meet Bruce Hamilton of Toast Kaizen Fame.
Mark Graban (2m 17s):
So if you wanna learn more about that, go to northeast lean conference.org. If you want, links to Steve's website, his books. I'm also linking to an article that we talked about here in the episode called Beyond the Jargon. He's shared a PDF of that article. For all of that, go to lean blog.org/ 2 62. Steve, hi. Thank you so much for joining us again here on the podcast.
Steve Spear (2m 45s):
Oh, hey, good morning, Mark. Thanks for having
Mark Graban (2m 47s):
Me. So we're gonna talk about, you know, two different articles that, that you shared. You wanna talk first about one, you know, title beyond the jargon. And as, as you wrote in the article, you know, jargon like, you know, know, gemba, kaizen, lean Statistical Process Control often seems irrelevant to people in healthcare. And, and maybe even, you know, contrary to the medical approach, can, can you sort of elaborate on, on that thought and maybe talk about how we can help people in healthcare see the parallels and, and the relevance of, of these terms, whether we use that specific jargon or not?
Steve Spear (3m 21s):
Oh, sure. So indulge me a little bit. I'll just walk, walk this through. So what we're really concerned about is, is a basic phenomenon and it's the ability of certain organizations to deliver far more value into the marketplace quicker and easier than their counterparts. And, and when you, you run that through more value, quicker, easier, what it means is that the benefits accrue to everybody. It's not an either or, you know, to the benefit of the customer at the expense of the supplier, benefit of the customer, at the expense of the employee. If it's better, faster, easier, it's better for everybody. So that's the core phenomenon.
Steve Spear (4m 0s):
And the context for everybody is that in order to deliver value, whether you deliver a lot or a little fast or slow, easy or hard to deliver value means trying to harmonize the efforts of many people towards some common purpose. And those efforts might be something way upstream like development somewhere midstream like design or the fabrication delivery of a product or service. But it requires this choreography, harmonization of the efforts of many towards some common purpose. So, you know, so what we have is that's the common operating condition. We have real differences in the ability to manage well within that operating environment.
Steve Spear (4m 43s):
And so the question gets to why is that? And what you find is that the folks who do this exceptionally well understand that if you have very complex systems, which are dynamic, right, lots of people doing different things at different times, and those complex dynamic systems are subject to disturbance. Either internal disturbance like, you know, I show up today, I'm not quite as focused cuz I'm tired, or if my flight was later I was drinking too much or subject to external disturbance, bad weather, my customer, my supplier, my competitors have changed the operating environment. That if you have these complex dynamic systems subject to disturbance, then they have to have the capacity for self-correction, internal self-correction.
Steve Spear (5m 27s):
So that, that's the common theme, right? The, the common operating condition, the common challenge is this ability to self-correct and even self-improve. And the evidence is very, very strong that some manage that mixture much better than others. Yeah. All right. So underneath that, there has to be some sort of basic science of how you manage complex dynamic systems to achieve great results. So that's the starting point. Then what happens, different communities look at exactly the same challenge and they start assigning labels and labels are necessary, right? Because, you know, if we didn't put a label on, you know, an apple, you know, you and I couldn't have a conversation about whether we wanted an apple or an orange.
Steve Spear (6m 10s):
But anyway, start assigning labels. But the, the problem with labels is that they start acquiring meaning to a subset community, which is not transferrable to other communities. And I think when we start looking across the disciplines of Lean Six Sigma TQM and, and all these other movements and efforts towards helping people deliver more value to market quicker, easier than they would otherwise, what you find is that the lexicon originally was meant to be clarifying for those using the lexicon. And what ends up happening, it becomes confusing. So you see this particularly trying to make the transition from the industrial world into the healthcare world.
Steve Spear (6m 57s):
Cuz in the industrial world, when you and I let's say use the word gemba, it has meaning to us. And it's not just a word which is sort of a bastardized Japanese word. It means, you know, you and I both know, oh, gemba means I have to get onto the shop floor. I have to get close to the occurrence of events, I have to get close to the occurrence of problems that are affecting those events. And I understand the necessity of doing that because if I don't get close, I'm gonna miss subtlety and idiosyncrasy. That is really fundamental to understanding the event. And if I don't have that deep understanding of what's fundamental to the event, then I'm really handicapped in my ability to improve it. All right? So that, that, that works fine for you and me and, you know, are the friends who think of gemba and all the rich deep meaning behind those five English letters.
Steve Spear (7m 42s):
Yeah. Right Now you say gemba to a guy who's trained up as a doctor or a nurse, and they look at you and it's like, what the hell is gemba? And you know, and, and then it gets explained through this very shorthand, abbreviated explanation. It's like, go to the shop floor. Well, you know, you and I, when we hear that, you know, that go to the shop floor carries conveys so much meaning and importance. And to them it's like, well, I don't even have a shop floor, I have a bedside. Right? Right. So I think that's the problem. And I think the, so anyway, that, that's our problem. And you know, thinking this through kind of like disciplined a three problem solving, we always have to go, you know, what's the problem? The presentation, what's the cause and how do we countermeasure, counteract, treat that?
Steve Spear (8m 24s):
So I think the, the problem is our inability to communicate into the healthcare sector. So our inability as folks who've come to deep appreciation of how industry is successful of value to market at speed with ease and affect a sector that really would benefit from those lessons. Right? Yeah. So that, that's the problem. The lack of communication, I think the root cause gets to, we're using lexicon, which has great meaning to us, which has no meaning to them. So I, you know, know, what I have found as a useful countermeasure to that is actually re-express exactly the same ideas with their rich and subtle meaning, re-express it in terms familiar to the audience.
Steve Spear (9m 12s):
So for example, you know, just picking on this term countermeasure, you and I both know Oh, countermeasure, right? I get it. I means a, a change in how work is done based on a response to some root cause, which is an explanation for a problem. Yeah. Well, countermeasure to a doctor or a nurse or a pharmacist has actually little meaning. However, if you say to them treatment plan, their, their brain goes through exactly through the same cycle of, oh, the reason we have treatment plans is because a patient came in presenting symptoms. See they have symptoms, we have problems. And those symptoms, we did a diagnosis for those symptoms. You know, you and I do root cause analysis, they do diagnosis.
Steve Spear (9m 54s):
And when we did those diagnoses, we found what we thought were some causes for the symptoms that were occurring and be, and in response to those causes, we're gonna develop a treatment plan. And I, I, I think what we need coming out of industry is to respect the fact that we've spent a lot of time developing our lexicon and assigning not only meaning cognitive meaning to it, but emotional norm value meaning to it, and that other communities have their own lexicon. Yeah. And then if we want to communicate well with those communities, it becomes wickedly important to respect the lexicon, the meaning and the values behind it, and communicate through their lexicon and not insist that they learn ours in a sense as a second language.
Steve Spear (10m 43s):
So anyway, how's that, how's that in terms of making sense?
Mark Graban (10m 47s):
Yeah, no, that makes, that makes great sense. Yeah, it's interesting in terms of the jargon, you know, when I first got into healthcare, there's challenges in the other direction. When you hear, or even as a patient, you know, take that medication PRN, you're like, what? And they Oh, as, as needed. I'm like, well, why don't you just say as needed? Right, right. I think it's the same number of syllables as PRN or you know, tho those doctors are locum tenons, and I'm like, what? And I'm like, oh, they're, they're here temp, you know, temporary assignment. And I'm like, well, why don't you say that, but Right, right. It's interesting. Yeah, you say that, you know, the context, even a word like kaizen, you know, people say like, oh, that means continuous improvement. And, and there's, there's a lot more context even behind a simple word like that.
Mark Graban (11m 27s):
So what I hear you saying is to try to try understand their, their language, translate it when you can, but but also make sure they're understanding the context behind the word.
Steve Spear (11m 38s):
Exactly. Right. Exactly right. And and the thing is, when you go into healthcare, you know, if you spend enough time there, you're gonna pick up, you're gonna pick up their lingo and be able to, well, here, here, first of all, the observation, right? So if you listen to a PRN, I guess is the acronym you used, you'll probably see that when clinicians talk to each other, they'll actually use those abbreviations out of context. So when they're talking about medication, they'll talk about, you know, take the medication prn as needed, but then they'll, they'll be talking about something else, like, how often do you have your car washed? Oh, you know, PRN depends on the weather, right?
Steve Spear (12m 19s):
And, and, and you'll start to internalize their lexicon and their meaning. And when you do so it'll be, you start gaining, I wouldn't say native fluency, but you'll gain some, some modicum of fluency in, in their language. So you can express your ideas in ways that they don't have to translate. You're doing the heavy lifting of doing the translating.
Mark Graban (12m 41s):
Yeah. Well, it's funny. Yeah, I think even within the, you know, quote unquote lean community, there, there are translation issues where the one thing I hear all the time, somebody will say, oh, I'm gonna do my first kaizen next week. And what they really mean is a, a kaizen event, or what people in healthcare would call a rapid improvement event. You know, there's, there's, there's a, a shorthand where, you know, not, you know, a kaizen event is not the only form of kaizen. I I might, I might push back and say, so I'm just Right. Curious if you see other, other cases of, you know, even within a field where you would hope we have common definitions that there's maybe troublesome variation in terms of, of the phrase or the approach.
Steve Spear (13m 22s):
Well, yeah. So I, I think what what you're saying there about just even within industry is that these terms have really deep rich meaning, and again, I think the meaning is both, you know, sort of cognitive rational, you know, action verb oriented, but also norms and values, right? So when you gemba, and you mean it in a way that is probably high fidelity to folks at Toyota, it's not just the physical action of going to the event, but it, it's arriving as an active, respectful, observer learner who's arriving without a preconception, precondition, a willingness and actually intense desire to observe it empathetically the situation that's going on, right?
Steve Spear (14m 12s):
So even that one word, when we start using it, you know, again, it carries both normative value of what you're supposed to do when you're using that word, but also almost an emotional moral norm. Yeah. Value overlay. But then, but then you have folks who they just heard the term gemba and didn't have the chance to experience it again in this high fidelity fashion. So for them, gemba means go to the shop floor, and it doesn't, doesn't carry all the extra meaning associated with it. Yeah. So anyway, you know, know ear earlier on, you said, now doctors, you know, well, why don't you speak in normal an, you know, plain English, you know, if, if you want it taken as necessary, say take as necessary.
Steve Spear (15m 2s):
And I think even within the industrial community, we probably should follow your device on that. Yeah. And then sometimes say, Hey, you know, let's go see the problem and see if we can really understand it from the perspective of the associate doing the work. Yes. That's a longer statement than gemba. Right. But sometimes necessary.
Mark Graban (15m 20s):
Yeah. I mean, it seems like language can, can create clarity and common bond or I, I, I think sometimes this happens both with, you know, quote unquote lean experts or with physicians, it creates barriers. If somebody says, yeah, we, we, we did some Nemawashi and now we're gonna Yokoten uor kamishibai boards, what, like, I, I even have trouble following that string of Japanese words,
Steve Spear (15m 43s):
All right? And you're like, yeah, sounds great. Sign me up for that one. You know? Yeah. And, and again, actually, you know, I was being facetious, but it, it kicks in, right? So someone uses a term and then we hear the term and we don't actually understand what they mean by the term. But then we get into all this cognitive bias stuff, which is, we don't say, Hey Mark, what the heck did you mean by all that stuff? You know, actually, I can't even repeat the words back. First of all, tell me what you said and don't tell me what you meant. But it was like, you know, instead what we, we, we were locked into the, the head nodding of, oh yeah, yeah, of course I want to do that. Just what I don't wanna do is look stupid. Right. And, and give the appearance. I don't understand.
Steve Spear (16m 23s):
Well,
Mark Graban (16m 23s):
And, and I'm, I'm, you know, I, if I threw those words out, I might be happy you didn't question it and push back, cuz maybe I don't really understand.
Steve Spear (16m 30s):
Right, right.
Mark Graban (16m 33s):
But you know, you, you said one thing I I wanted to maybe come back to, you said, if I was transcribing this one sentence, I believe you said Lean six Sigma TQM as a sort of three separate things. But there's also this, this terminology out there where people talk about Lean Six Sigma as a single thing. I'm, I'm curious if you have any thoughts on, on that distinction or, or terminology that's out there, how that relates to, you know, I think, you know, we were talking before the podcast, you used the phrase Fidelity to Toyota, which I thought was an interesting phrase. Can you, what are your thoughts on that?
Steve Spear (17m 11s):
Yeah, so let, let, let's, let's hook this next piece off of the phrase fidelity. So there's the fidelity to Toyota and there's the fidelity to Edwards Deming, and there's fidelity to some of the other real luminaries who came up with these ideas, you know, whether it's shoe heart and so on and so on. Now, again, you take a look at each of them and, well, first of all, let's step back for a second and say, it's not obvious to me that Deming had much influence on Toyota's thinking. It's not obvious that Toyota Toyota had much influence on Deming's thinking.
Steve Spear (17m 52s):
And the other organization I've written quite a bit about is the, the Navy's experience with nuclear power, the Navy nuclear propulsion program. And it's pretty clear that Toyota and Deming did not influence the founder of that program, Hyman Rickover. All right, so you have these three sort of independent efforts. Now what you get is three independent efforts to come to some deep, deep understanding of how you manage the efforts of dozens, hundreds, thousands towards some common purpose, right? Because, you know, the folks at Toyota Edwards, Deming and the Navy reactor program were dealing with exactly the same common challenge of this harmonization of human effort towards common purpose.
Steve Spear (18m 40s):
And not surprisingly, they came up with some real common ideas, fundamentals, you know, cuz each of 'em were dealing with these systems like we mentioned before, which were, are incredibly complex in constant movement. So dynamic and subject to constant disruption. And all three independently recognize that for all the declaration you can make on how you think things are gonna work, you also have to have this very intense feedback and capability for self detection, self-correction, self-improvement, right? So that, that, that's common across all those, those three, what ends up happening.
Steve Spear (19m 24s):
And, and, and let me just add one other thing that's real common is that the folks at Toyota put a huge, huge emphasis on the actions of leaders to influence the, the values, the norms and behaviors of those they support. And Admiral Rickover has a, you know, incredible reputation for his, let's say somewhat caustic social skills. But fundamentally he was constantly emphasizing the, the point of leadership encouraging these dynamic capabilities for problem seeking and problem solving. And he, he has a line, I remember something like, you can delegate authority, but you can never delegate responsibility.
Steve Spear (20m 8s):
Something like, and, and, and if you look back at Edwards Deming, you know, he had a, a collection of different tools, techniques to gain dynamic control, you know, feedback as we would have learned at mit, you know, dynamic control of systems. But the amount of time he spent talking about the role of leadership and special causes and general causes and profound knowledge. I mean, Deming also was really talking to leaders and how they had to manage organizations. So the organizations had these capabilities of self-correction, self-improvement, right? So that, that that's the common, and that's, and it's sort of planning list. Then what happens, you start developing a lexicon and not only do you develop a lexicon, but you start talking about the tools each of these luminaries developed and used to achieve the, or express the underlying fundamental common principles.
Steve Spear (21m 5s):
So in the case of Toyota for example, you have things like standard work in Jidoka, in the case of Deming, you have things like statistical process control, run charts and, and upper and lower limits. And, and Rick over within the Navy community had his own terms. So what ends up happening, you and I, who are newbies to these movements, we don't get leveled up in terms of the basic phenomenon, the basic thinking, but we get taught is the, the tools, right? And you know, and again, you start thinking about how we train up as engineers.
Steve Spear (21m 47s):
So in engineering, you know, mechanical engineering is what I studied. You go in and, you know, they, they put something on a desk and they say, this is an object. It has a mass guy named Isaac Newton. He told us, if you put a force on a mass, it wants to go faster and faster. And we often don't observe that because, you know, there's friction and viscosity in the world, but you know, we're gonna show you actually about this acceleration thing, right? And then they, then they start teaching you tools, right? You get equations as a form of a tool. Maybe you get a piece of software as a form of a tool. You get all these different tools, but you always come back to the basic principle about forces causing objects to accelerate. Now this, I think the problem we've had in the industrial world and in the organizational world more generally is that there there is this very fundamental parsimonious basic science about managing these complex dynamic systems, which are subject to constant disruption.
Steve Spear (22m 45s):
People don't learn and internalize and socialize on the fundamentals first. They're handed the tools. It's like if you went to engineering school, they didn't tell you about Newton, but they gave you MATLAB. And, and, and so then when, when, when you, you get tools, not surprisingly Toyota was dealing with an operating environment different from Deming. So the tools they developed to express this deep, basic understanding are different than Deming's tools. So then you get situations where you have lean tools and you know, people who sort of almost ritualistically coalesce around lean tools. And then you get people who, because they're exposed to 'em, they coalesce almost ritualistically around six Sigma tools.
Steve Spear (23m 31s):
And then someone has a, an epiphany saying, ah, what we should do is combine the communities and we'll call it Lean Six Sigma, lean, you know, whatever the term is. And we'll have a basically saying, we'll have a more holistic approach to the use of tools. So anyway, that, that, that's my interpretation is that the reason we have this fragmentation and then these sort of funny attempts to synthesize, right? Is because as, as practitioners, we don't come back to the basic science. We just look at the tools and, you know, fo you know, identify by the tools and not the, the core principles.
Mark Graban (24m 8s):
Yeah. And I, I think, you know, synthesis is a good goal. There's a lot of overlap. You know, people will debate sometimes is a, is a Pareto chart a lean tool or a Six Sigma tool? I'm like, well, it predates both of those. It's just a good, helpful thing to use. But I, I think sometimes the synthesis, the attempted synthesis breaks down. I, I think this is somebody else who used this analogy once, you know, a, a cat and a poodle can coexist in a room or even in a cage, but that doesn't make them a single animal called a catoodle. You know, that they're both, they're both still there. And they, they can, they can, they can play with each other and, and be fine.
Mark Graban (24m 49s):
But I think, you know, I've, I've heard people complain and say, well, you know, I was interested in learning about lean and so I was told, or I found, well I could learn this thing called Lean six Sigma. I'll learn both. I'll learn two things. And then, you know, it turns out the, the Lean six Sigma education or program is really 90% six Sigma deep statistics, again, you know, perfectly valid fine methods. And then they learn a little bit of fives. I'm like, well that, that really sounds like six sigma as opposed to being a synthesis, right. Of the two.
Steve Spear (25m 21s):
Right? Well, so you start thinking about the, the commonality. The commonality is you're trying to gain some dynamic control over a complex system. Now, some complex systems be they, you know, high volume, low variety, repeatable processes do lend themselves to and actually may necessitate the collection of very large data, which can only be accessed statistically. Yeah. And there's other situations you find yourself in which it might be an event which occurs with far less frequency, greater variety. And in that case, statistical analysis is not the tool you need.
Steve Spear (26m 4s):
You actually need this very binary, something that's working as predicted or it's not working as predicted. Right. And if it's working as predicted, I can continue. And if it's not, I have to come back and investigate. Actually Mark, you know, we started this conversation off with talking about healthcare. So healthcare does the same thing, right? When, when you're trying to understand the experience of a population, you use a lot of statistical tools and they kind of fall under the umbrella of public health, right? And then when you're trying to understand the experience of an individual, you take a different approach, which is, you know, obviously not statistical cuz you're looking at, at, at one. But now you start getting into things which depend much more on your causal reasoning and things are or, or are not normal and that, that sort of thing.
Steve Spear (26m 52s):
Now, no one would ever argue that, oh no, we, we, you know, we don't do public health, we do medicine or we don't do medicine, we do public health. For folks who describe themselves as healthcare professionals, they do the one that's right depending on the conditions. I was just reading up on AIDS in the advance in AIDS treatment and you know, if you really want to visualize it, there was this very famous photo and you think about just a huge visual contrast, this famous photo of this young man on his deathbed being attended to by his parents and his priest. And it's heartbreaking. The guy's got all this discoloration of his skin and, and his parents are distraught and the priest is doing his best to console the family, but he's clearly moved by this, you know, like this curse that's been come onto this guy.
Steve Spear (27m 42s):
And then, you know, just suppose that picture with Magic Johnson, you know, playing basketball in the Olympics part of the dream team, and he, he, he's got the same darn disease and you know, he's playing basketball at the highest possible level. Now you start looking at the transition there. Well how did that happen? Initially, AIDS and HIV was treated statistically because it was such a poorly understood experience that it was just a matter of trying to identify who had what symptoms in what conditions to figure out at least a pattern of where this thing started to emerge.
Steve Spear (28m 24s):
Mm. And then with that, there was an advance in understanding of, oh, it, it, it seems to be related to infection and the infection seems to be conveyed in these different ways. But now that we know it's an infection, we click over from the statistical to the pharmaceutical trying to understand the internal biological chemical mechanisms, which go on. And then once we have that, now it kicks over to a medical problem where we can actually treat people to treat HIV as a chronic condition. Now, you would never say, oh one is better than the other. It's just that one was more appropriate in the circumstance than the other.
Steve Spear (29m 4s):
So anyway, to say that someone is trained up as you know, it's six sigma or lean all the time, it's not right. In both cases it's each has a set of tools associated with itself, which are meant to give you better understanding of these very, very complex dynamics situations. Right? And you use the, the tool, which is appropriate at the time, but not, not, not forgetting that the fellow associated with the advancement of lean tools, Deming really was focusing on tools as a means towards an end. And, and the end was profound knowledge. Yeah. And in the case of Toyota, they also have tools, but again, it's a, it's a means to an end.
Steve Spear (29m 48s):
It's, it's, you know, one of the Toyota's, so the Lexuses the relentless pursuit of perfection, right? You may never get it, but you pursue it and the way you pursue it is to the Toyota phrase of good thinking, good products that you have to advance your thinking, right? So both Toyota and Deming come at this as the basic problem is learning, right? And there are certain tools in certain situations which help you learn better or not. But anyway, to have sort of this sort of blind ritualistic adherence to some and not the other is one, I don't think it's shows fidelity to the geniuses who invented these things and is also not productive.
Mark Graban (30m 28s):
Yeah, I, I agree. And I think, you know, there's, you know, there's all sorts of different biases that people bring to the table when they're trying to learn new approaches. One is, you know, a bias toward tools. I'm gonna learn some new tools and, you know, I think, you know, we, we can talk about Tachii Ohno and others from, from the past, but you know, in current day, Jamie Bonini at Toyota does, I think an amazing job of articulating to outside organizations, including those in healthcare that, that they're supporting and helping that, you know, yes there are tools, but there's also, you know, a mindset or a philosophy that that starts to get into the realm of, of not just problem solving tools, but management system and culture.
Mark Graban (31m 13s):
And, you know, I think a lot of people are either just not exposed to that or, you know, may maybe they're comfortable with their existing philosophy and, and they're just looking for some quick hit tools. I mean, I think that's, I think that that seems to be a big challenge out there and, you know, copying something or, you know, learning it and, and being done learning as opposed to continuing to learn. And, you know, your, your different articles here we have linked to You talk about the competitive advantage of, of a learning organization. There's probably nobody out there who's becoming highly successful just by copying somebody else, right?
Steve Spear (31m 51s):
No, no, you can't. Cuz again, the basic, the basic condition, right? You know, we come back to you're trying to manage these very complex organizations, many people towards common purpose. Nothing is ever stable. There is no steady state, right? The, the world keeps changing and your, your own internal world keeps changing. So if the world keeps changing, what that means is that the world changes from situations which you think you have some understanding into situations which you have far less understanding. And, and, and, and the longer you go, the less and less you understand and the less and less relevant you are in, in, in a, in a changed world. Now again, you know, I'm saying what others have said more authoritatively and eloquently, but in a world which is getting increasingly connected and very nonlinear ways, right?
Steve Spear (32m 37s):
Yeah. Highly networked ways and in which things move more freely, more quickly. And those things could be ideas, finances, people, technology, the world is changing faster and faster, which means that it is ma making your current capability and your current knowledge less and less relevant faster and faster and faster, right? So the only way to keep pace is to learn better, faster, more consistently about what you should be doing and how you should be doing it. Because what you were doing and how you were doing it may have mattered a day, a week, a month, a year ago.
Steve Spear (33m 19s):
But for sure it, it matters less right now. And, and, and, and a day, a week, a month from now, it'll matter even less.
Mark Graban (33m 26s):
Well, and you know, when you, I I love your phrase, if, if I hedge jotted this down correctly, complex dynamic systems subject to constant disruption, that certainly sounds like healthcare today. That sounds a lot like, you know, the, the, the Eric Ries definition of a startup, you know, organizations facing high degrees of uncertainty is, is at least part of that definition. You know, one, one other thing I wanted to ask you about though is, you know, you know, hospitals with self-identify as complex dynamic systems subject to constant disruption. But you know, I think I've, I've heard this a lot. People in, in healthcare will really kind of, you know, pooh pooh manufacturing, you know, somebody from manufacturing, you know, we can maybe be self-deprecating and call ourselves, you know, you know, knuckle draggers and you know right.
Mark Graban (34m 14s):
Factory rats and whatever. But you know, as you say in the one article, people, outsiders often think manufacturing is deceptively routine. I was wondering if, if you could elaborate on that a little bit.
Steve Spear (34m 25s):
Oh, sure. So we, we, we all have this problem, right? Which is, you know, look at something from a distance and it, the execution appears smooth and graceful and flawless and all of that. And so it's easy to conclude, it's easy, you know, go to a baseball game and see an outfield or chased down a fly ball and, and, and catch it with seeming a sort of nonchalant approach. Say, oh, that must be easy. You, right? When, when, you know, any of us who've ever played little league realizes how ridiculously difficult it is to track the ball off the bat and know where to be, to have it end up in our glove when it, you know, when we played little league, you know, ball or, you know, played high school, whatever, if the ball ended up in our glove, it was almost like miraculous.
Steve Spear (35m 19s):
And, and you come to appreciate just how hard it is to practice that skill that you can chase down a ball which is moving about a hundred miles an hour and, you know, get it in a deep corner in front of the green monster at, at Fenway Park. So, so you get the same thing also. You go to the ballet and you, you look, oh wow, you know, that that, that it looks so easy. Now if you happen to have a front row seat or a seat on the stage, you realize just how hard the ballerina is working. If you have a chance to see the ballerina in practice and see the number of falls and drops and twists and, and, and sprains and injuries that are required to get to the point of the flawless execution.
Steve Spear (35m 59s):
Well, you know, you know, for those of us who work inside industry, it's the same thing. It's, it, it requires so much constant adjustment to make sure that the external users experience is, is flawless. Now the thing is the external user, they don't see what's going on inside in terms of the, the need to constantly design, develop, practice, rehearse, correct, modify, you know, both short term and long term. All they see is flawless. And so they must come to the assumption that, oh, if it's flawless, it must be easy. Right? You know, I was having this conversation yesterday is that there's a huge amount of constant dynamic variability going on.
Steve Spear (36m 46s):
Now we can choose to run our systems in such a way that we absorb that in how we manage our systems. So the end, so the customer, the beneficiary doesn't experience that dynamic variability. Or we can run our own systems in a, in a much more ballistic, rote, non-responsive way. So we basically ignore the dynamic variability, but what we do is we impose it on the beneficiary of our work, right? Cuz no, no, they're getting this huge variety and experience. Yeah. I'll give you just, you know, link making the link between industry and healthcare. So you take a look at, you know, biological systems, the human body, right?
Steve Spear (37m 27s):
So, you know, you can be sitting someplace and you give every outward appearance of total stability. Of course what's going on inside is your body is making these constant adjustments to cognitive load, physical load, blood sugar levels, you know, you have the window open, a cool breeze hits you, your body's making these micro adjustments in terms vascular flow of blood for cooling and heating and that sort of thing. Now, externally, you're not aware of any of this and you, you're not affected by any of these internal changes, right? But your body's working very, very hard to absorb that variability so that your external experience is not marked by it at all anyway.
Steve Spear (38m 15s):
It's one or the other. So that the folks in healthcare may look at what happens in industry, and since they only see the car which rose off the assembly line, they have no idea of a huge amount of dynamic change that's required in the designing the car, designing the system that makes the car, making the car, et cetera.
Mark Graban (38m 33s):
As, as we start to wrap up, bring it back to healthcare again, you know, you talked earlier about this goal of better, faster, easier, some organizations really standing out by delivering more value quicker and easier. I is there anyone that you've seen in healthcare recently who is kind of reaching those heights, or at least on a good path toward that?
Steve Spear (38m 55s):
Right. So let me preface this with a very important caveat that my work typically goes very, very deep into an organization. I'm, I'm not, I'm not the guy who unders. So I can get into like a lot of real nuance. I'm not the guy who has a good sense of population. So in terms of a sense of the population in healthcare, there are others who understand much better who's actually advancing and, you know, moving the needle significantly versus not. My, my impression though is that by the little bit of the literature that I see and read in the conferences that I attend, in the conversations of which I'm part that healthcare as a sector still hasn't identified the management of complex dynamic systems, many people towards common purpose, they haven't identified that as a key condition which they have to be concerned about, and for which there's a fundamental basic science which will inform their efforts.
Steve Spear (40m 7s):
Now, if you take a look at other things like infectious disease in healthcare, they're constantly trying to advance their understanding of the basic science to inform the development of medications and, and their use of application. Similarly, you know, they're constantly trying to advance their understanding of the basic science of genetic code and how it affects our, our experiences. So there's a lot of places they do this, but it's not obvious to me that aside from very isolated pockets, they're looking at these complex human systems and trying to understand the basic science by which they can be managed far better.
Mark Graban (40m 50s):
Well, there's still a lot of work to be done and you know, I, I appreciate what, what you're doing to help move people's thinking along. One way you're gonna be doing that, you know, as I'd mentioned at the top, is the upcoming Northeast lean conference that's, that's being put on by the good folks at gbmp, October 4th and fifth northeast lean conference.org is the website. You're gonna be one of the keynote speakers. What's the, the topic or, or the theme that, that you're gonna be talking about there, Steve?
Steve Spear (41m 21s):
Yes, it's all about the people. It's all about the people. Mark and I, you know, on this, I feel very confident that I'm channeling the, the luminaries at Toyota, Edwards Deming, Admiral Rickover and some of these others that, you know, you can go out into the marketplace and you can buy gear. You wanna make, you wanna make microchips, you know, people will sell you for tens of millions of dollars equipment to make microchips and billions of dollars to build a clean room. I mean, the gear is out there. What is very clear, and this goes back to research all the way in the fifties, sixties and seventies, some people buy the same gear as everybody else and they get results far, far better. I mean, we're, we're talking orders of magnitude better. We're not talking like micro percentages better, and if they're buying the same gear and they're running the same stuff through that gear, it can only be the people and their understanding of what to do with the gear onto the stuff, which is the difference.
Steve Spear (42m 12s):
Yeah. So I'll be talking, it's all about the people and managing the people in such a way that, and I'll just lead the conference, but, you know, kind of end this conversation with, it's really fundamentally, if it's all about the people and people figuring out better things to do and better ways to do those things, then it's about everybody being an active learner and using the parlance of the day. It, it's really about converting everyone in your organization into a knowledge worker that, that, that's the fundamental thing. It's all about the people and everyone as knowledge workers.
Mark Graban (42m 47s):
Well, well, great. And I, I hope people will be able to attend and, and hear that message directly from you. There's still a little bit of time to, to register. I would encourage people check out the event in, in future years. It's a, it's a great annual event and glad you're gonna be a part of that. Steve, again, our guest has been Steve Spear, author of The High Velocity Edge and a lot of great articles. Steve, how can people find you on, on the web if they wanna read more?
Steve Spear (43m 19s):
Yeah, so I've got a, a website, you know, www.thehighvelocityedge.com. I think we simplified that also, not promising, but give a shot at www.hvellc.com and you know, for real quick
Mark Graban (43m 39s):
That works,
Mark Graban (43m 58s):
Okay. And I'll, I'll share that in show notes for the episode. If people are listening while driving, please don't try doing what Steve suggested while you're going down the road, even if you're in a, a quote unquote self-driving vehicle.
Steve Spear (44m 11s):
Right.
Mark Graban (44m 12s):
No,
Steve Spear (44m 12s):
No driving. Yeah.
Mark Graban (44m 13s):
But Steve, thank you again so much for taking time to, to be a guest on the podcast. I really appreciate it,
Steve Spear (44m 19s):
Mark. You're welcome. And and thanks for asking me. It's really, it's good to catch up.
Announcer (44m 25s):
Thanks for listening. This has been the Lean Blog podcast. For lean news and commentary updated daily, visit www.leanblog.org. If you have any questions or comments about this podcast, email Mark at leanpodcast@gmail.com.
Please scroll down (or click) to post a comment. Connect with me on LinkedIn.
Let’s work together to build a culture of continuous improvement and psychological safety. If you're a leader looking to create lasting change—not just projects—I help organizations:
- Engage people at all levels in sustainable improvement
- Shift from fear of mistakes to learning from them
- Apply Lean thinking in practical, people-centered ways
Interested in coaching or a keynote talk? Let’s start a conversation.
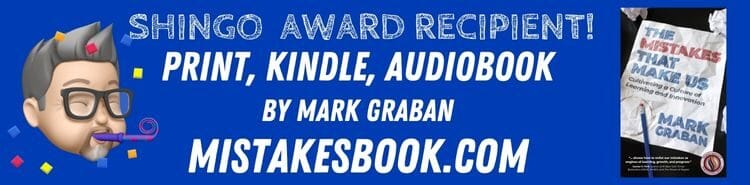
Thanks for bringing Steve Spear back on the podcast. As someone who can’t make it to NorthEast Lean event this year I’m glad to hear from him!
Good thoughts on jargon – not profound on the surface, but anything that affects the quality of communication is significant. One of my current favorite aphorisms is attributed to George Bernard Shaw: “The biggest problem with communication is the illusion that it has taken place.”
And the latter sections of the interview address really important, top-level considerations about why lean thinking has not yet fulfilled its potential in healthcare. Good stuff.
Thanks, Andrew, for listening and for sharing the quote!
I am wondering what he meant by his statement about the healthcare sector managing complex dynamic systems lacks the many people to a common purpose as a key condition. Is he speaking about healthcare at a macro level(healthcare policy) or at an operational level where for example an observer on a nursing unit would be hard pressed to identify much in the way of any type of coordinated purpose.
A recent visitor to a truly exceptional lean job shop (lot size of one, single piece flow, complex processing, two-day order to delivery) commented that he would take quickly trade all the lean artifacts back at the hospital for the teamwork he saw if he could have that on a nursing unit.
I’m glad to see the healthcare visitor could see and value the teamwork that was on display in the job shop!
I’d have to ask Steve… I’m guessing he meant at an operational level, as that’s where he does his work, he said.
A quote from the podcast you can share: