Today, I'm sharing a 10-minute video that was shared by the Five Hills Health Region within the Saskatchewan health system. In the video, Heather, the director of women's health unit and pediatrics, describes their kanban system for managing supplies and materials. They started in November 2013 with this approach.
Note: This is not a post about the “kanban” method of work visualization and planning that's been written about by people including David Anderson and Jim Benson. This is about what I'd call the original meaning (and continued meaning) of kanban as a materials management and/or production scheduling method (see Toyota's website). The use of the word kanban in areas like software development causes some confusion…
Back to the video, Heather smartly engaged the knowledge of nurses and unit clerks in the design of this approach and the organization of the supplies. They spent one full dedicated week to do the initial setup of the system, which seems realistic to me based on my past experience in setting up a kanban system. An approach like this also requires some pre-work to try to collect data on the normal and “worst case” usage for each item.
The video shows a very typical two-bin kanban system that works great. It's far more effective and less time consuming, I'd say, than the more typical hospital “par level” system (an approach that requires a lot of counting).
They've utilized color coded bins to make it easier for staff:
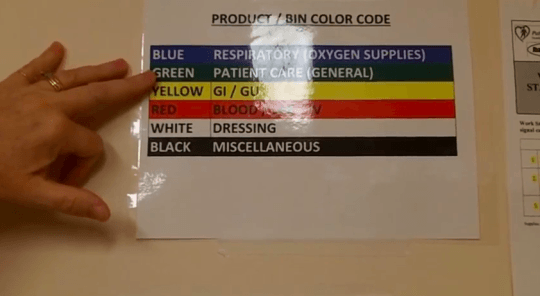
Each item is clearly labeled:
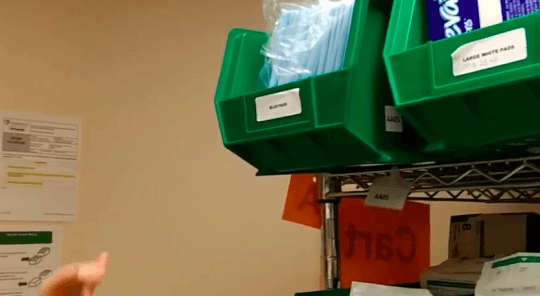
And there is a bar-code label on the side of each bin:
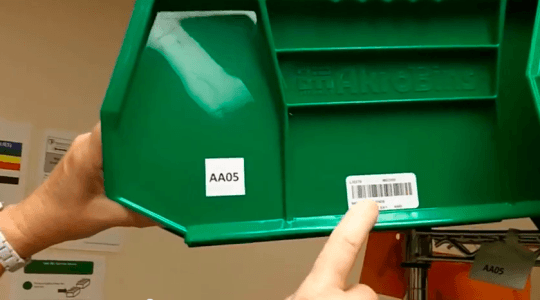
Materials management comes up every weekday to scan empty bins. The “AA05” refers to the shelf location of the bin, which is also clearly labeled on the shelf and “it's easy to locate what you need.”
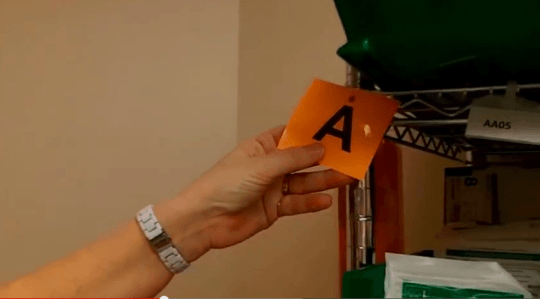
When a bin is empty, it gets placed into the large grey bin container (something that's easy for staff to do):
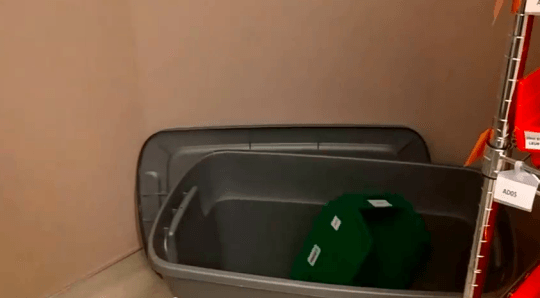
And then the second bin that still has supplies in it gets pulled forward.
Heather talks about how they tried to estimate demand for items, but they also had to account for peaks in usage. Early on, they “did run out of some supplies,” which isn't unusual in the start up of a kanban system. The key, then, is to adjust kanban levels accordingly because the goal is to NOT run out.
In my work, I like to err on the side of having a little too much inventory at first. Otherwise, if there are stock outs and missing supplies, people lose faith in the kanban system. Over time, you can adjust the inventory levels down if it seems like bins for certain items aren't having to be restocked very often.
They have a clipboard that's used for communication about items that have run out, been discontinued, etc. or if they have questions about what items are really being used:
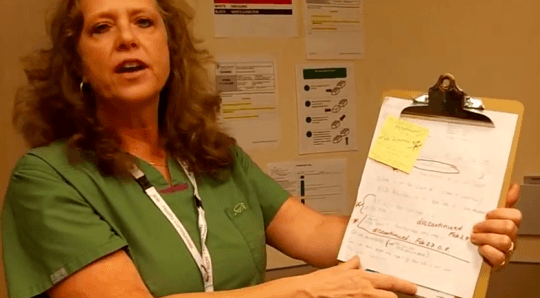
Some bins might be removed if an item has been discontinued (and there's communication to staff):
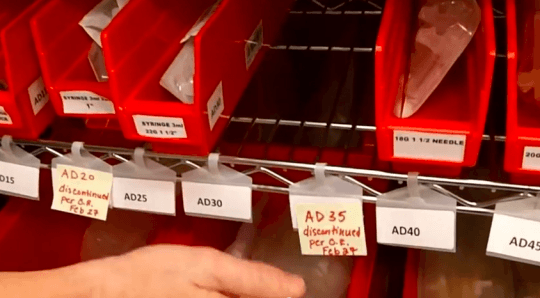
They also kept track of training each staff member on the kanban system, which “takes five minutes, it's easy.” It's important to make sure everybody gets that training.
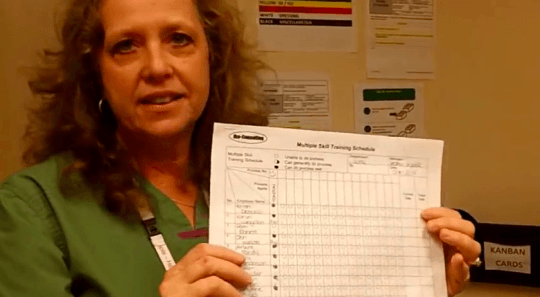
Some items have associated kanban cards, maybe because they don't fit neatly into two bins or maybe because the quantity needed doesn't justify two full bins:
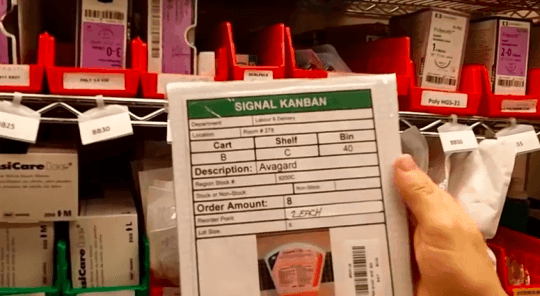
When inventory gets down to a certain non-zero level, the card gets placed in the holder on the wall:
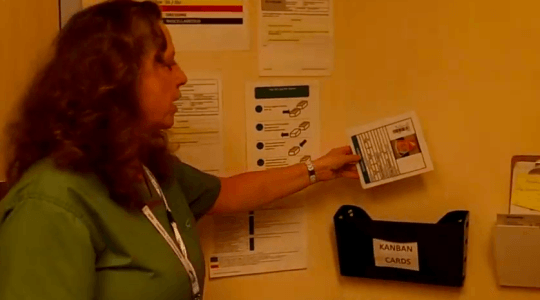
Easy! Effective!
Thanks to the Five Hills region for sharing this nice overview of a working kanban system.
As I wrote about in Lean Hospitals, a kanban system can be very effective at achieving both:
- Increasing the availability of supplies, while
- Reducing overall inventory costs
Jeff Hajek, coincidentally, just sent a link to this good kanban description yesterday in his email newsletter (sign up for it here).
Have you utilized kanban? What have been the results? Is your organization still clinging to the outdated par level approach?
Please scroll down (or click) to post a comment. Connect with me on LinkedIn.
Let’s work together to build a culture of continuous improvement and psychological safety. If you're a leader looking to create lasting change—not just projects—I help organizations:
- Engage people at all levels in sustainable improvement
- Shift from fear of mistakes to learning from them
- Apply Lean thinking in practical, people-centered ways
Interested in coaching or a keynote talk? Let’s start a conversation.
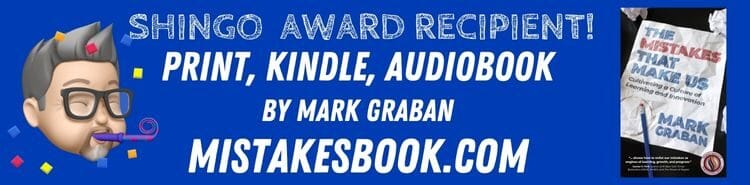
Loved it, was an easy explanation. Followed it to end.
Wow, that’s a great video. I really like how much she talks about the lived experience of it instead of the theory of it.
I know zip about hospitals, so I’m curious as to your reaction to the part where she talked about a big-bang adoption, where a couple senior people spent a full week organizing everything. In my world, software, I work hard to avoid that. It seems to me that the more people are involved in figuring out the process, the more likely they are to recognize that they’ll always need to keep tinkering. But I could think of several reasons why software would be different in this regard.
Hi William — in a software environment, are you using kanban as a materials management method or a planning method? There are two different things that each get called “kanban” — they are related, but different.
What I heard Heather say was that the bulk of the setup was done in a week:
1) Gathering parts info and usage data
2) Setting up the racks and bins
3) Creating the cards, etc. and other mechanics
4) Teaching staff how to use it
She said they keep tinkering with it and improving it over time. I’d consider that first week an “initial setup” not being “done.”
Thanks for the reply. I’d agree on both counts: software is up to something different, and for them it was surely initial setup.
I suppose what I’m wondering about is the extent to which increased investment in initial setup leads to decreased appreciation of the value of continued tinkering. The perennial failure of software planning methods is people following rituals that no longer work well for the situation (if they ever did). The way I’ve gotten people to take on that continual tinkering is by apparently underinvesting in initial setup, so that initial system is obviously inadequate, forcing people into an inspect-and-adapt loop early on. I also tend to find the smallest part of the process to switch, changing over gradually. this to help building those habits for the long haul.
So I was just curious as to your reaction to the amount of setup here. Would you, say, have gotten them to start with improving just one section of the supply room? My guess is that hospitial-specific factors (e.g., perhaps, higher cost of error, circumstances that favor formal training over knowledge diffusion) make working in larger lumps more appropriate. But since I know beans about hospitals, I thought I’d ask.
I’d worry about “underinvesting” as people in a hospital are very likely to turn their backs on something that “doesn’t work.” That’s why my experience leads me to err on the side of over-investing, including having slightly too much inventory rather than slightly too little… to gain people’s confidence that kanban works.
You could start with one section of the supply room… but that might run the risk of suboptimizing or confusing people. I, generally, like the idea of starting with one supply room rather than trying to roll this out hospital wide all at once. Small tests of change are helpful. The question is about the right size of small.
Great post. I really appreciate you pointing out the difference between true kanban and what many others are recently calling kanban (personal kanban, project kanban, etc). I recently had asked someone what elements of lean they utilize and they said they were using a kanban system in their office. I asked if I could see it and when I was shown a series of post-it notes on the wall I was a little surprised as that is not at all what I expected to see.
I also really like how they determined as a team what type of kanban works best for each (2 bin, actual cards, 2 “tube” item instead of trying to make one method fit everything.
From a reader via email… will post a response later.
My default would be to try a two-bin, given its simplicity. But, some times when I’d use a card system might include:
1) If the items are large and don’t fit into bins (like large boxes of lab reagents that are stacked on a pallet)
2) If the usage of an item is low… let’s say the re-order point is 1 and the re-order quantity is naturally 4. You could do a two-bin with two items each, but you’d have more inventory. You might care about the difference between 1 and 2 for the re-order point if the item is expensive and/or large
Great post and example of the elegant simplicity and usefulness of the 2-bin kanban. Perhaps I missed it, but the video kind of glossed over what happens with the empty bins after they get tossed into the “collector”. I presume that the daily pickup brings them to a centralized resupply area to be refilled and full bins delivered back shortly (same day?). Having the bar code on the bin makes it easy to know exactly what part/product goes in the bin and in what quantity.
It is great to hear that the “front line staff” (nurses in this case) love the system. I wonder what, if any, impact this has had on the centralized resupply folks? I would bet (hope) that it makes things easier for them as well. Wouldn’t it be neat if they realized that a similar system (scaled-up) could be implemented for all of the bulk reordering of the supplies?
Also – is “chanson” just an autocorrection of “kanban” or did I just learn a new Lean term? :)
Yes, “chanson” was a crazy Mac autocorrect that just started happening. I’ve never once intentionally typed that word until now (which probably now further confuses the autocorrect feature). I’ve typed the word kanban A LOT. It was autocorrecting and I clearly didn’t notice or correct all of them. Thanks. They are now fixed.
Back to the other, more important, question.
Heather mentioned that somebody comes around each weekday to scan bins and/or collect cards. They probably don’t physically carry the bins… there are pros and cons to taking the bins back and filling them in central supply, vs just bringing supplies to the unit supply rooms (and it depends if you’re restocking one supply room or many).
The delivery sometimes happens “same day” or some kanban systems have the delivery the next day (they size inventory accordingly). The route for materials management might be:
Monday: Come check for empty bins/cards AND deliver stuff triggered on Friday
Tuesday: Come check for empty bins/cards AND deliver stuff triggered on Monday
That means only one trip a day to each unit instead of two and I’d generally be able to make that work.
Things are decidedly NOT easier for materials management. Leadership needs to make sure materials has enough people on staff to do this work properly. Sometimes a hospital will spend MORE on materials management labor as a way to improve care and SAVE money overall.
There’s time saved for materials management with a kanban system because they’re no longer spending time counting each item for the par level system. The question of “restock or not?” becomes very binary, unambiguous, and visual.
Thanks for the reply! Your last point is what I was implying in terms of making things “easier” for the bulk resupply. But yeah, I can certainly imagine that an obstacle to implementing this in some hospitals (or, ahem, factories…) would be the localized increase in cost for materials management. Only by looking at the overall benefits as you say does make sense as a true improvement (and money-saver).