I just got back from Japan last night and I'm going to take it easy during this Thanksgiving week. Rest and family time are high priorities, of course, as I'm sure they are for many of you. I will be reflecting a lot on my trip and I'll be writing more posts about the trip soon.
On Friday, LinkedIn published a piece I wrote for their series of articles on the theme of “The Road Not Taken.” LinkedIn asked people to write about the “Plan B” that they maybe wish they had pursued. This was difficult for me, as I did pursue a Plan B – shifting from manufacturing to healthcare in 2005.
So, I wrote a piece that imagined what I might think if I had stayed in manufacturing.
Click here or on the image below for the piece… full text is also below.
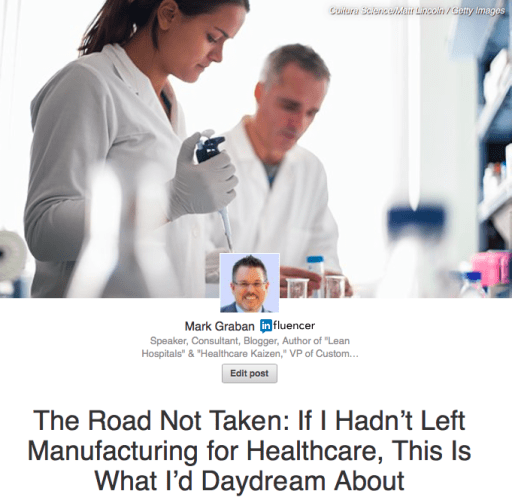
Do you have a career “Plan B?” What is it or what would it be?
Full Text:
Unlike some of the other authors in this LinkedIn series who haven't pursued a “Plan B” in their career, I was thankfully able to take a new road, switching my career path from manufacturing into healthcare.
As I learned, it's good to be flexible and open to new career opportunities. I was a little older than 30, about 8 years into my career, when I started wondering if working in big manufacturing companies was the best career path for me. Since, 2005, I've been been working as a healthcare consultant, as pictured below at one of my first clients, a medical laboratory.
I thought it would be interesting to write about how I'd feel if I had not made that switch and if I had stayed with my Plan A career path.
Again, what follows is a piece of fiction that might have been written if I were still, here in 2014, working in manufacturing (likely as a plant manager or a VP of operations or VP of continuous improvement role).
Had I not taken that road…
I've been working in manufacturing since I graduated from Northwestern University in 1995. I started my career at GM (my “best mistake“) and moved on after grad school to roles at Dell, Honeywell, and other companies. It's been very rewarding to help with and lead “Lean transformations. I've also directly led departments and factories as I've moved up through the ranks, becoming a VP of Operations for Worldwide WidgetCorp in 2013.
I did work for a startup software company, Factory Logic, for a few years in the early 2000s. You might have thought software and entrepreneurship would be my Plan B. But, I decided that wasn't the right path for me as it's often difficult being part of a startup, with all of the natural ups and downs that occur along the way.
I thoroughly enjoy the people and challenges that we face in manufacturing, as we work together to provide the most value and the best quality for our customers in the most timely way. We are under constant pressure to improve and that's energizing. We use Lean management principles to engage everybody in the organization, developing our employees as they work to meet evolving customer needs and strengthen the company's long-term financial performance.
However, I wonder what might have been had I pursued a different Plan B that presented itself back in 2005 — the idea of bringing my Lean and operations experience into healthcare.
In early 2005, I was part of an informal group called “The Valley Lean Council,” in Phoenix. People who worked with Lean methods in different companies would meet quarterly to compare notes. One of those meetings was held at a hospital in Scottsdale, where two former Motorola employees showed off improvements that had been made in the emergency department using Lean and Six Sigma. This seemed interesting at the time, but I didn't really feel motivated to spend time in a hospital — as a patient or an employee.
When my wife took a new job in Texas later that year, it forced me to leave Honeywell for a new opportunity. During my search, I had a brief chat with a recruiter from Johnson & Johnson, as they were looking to hire people with manufacturing improvement experience into a group that did improvement consulting work with labs and hospitals.
I said no to further discussions because I didn't see how time in healthcare, as interesting and admirable as it might seem, would help me in my manufacturing career path. I had goals that included becoming, someday, the chief operating officer at a large manufacturing company. That's what I studied for at Northwestern and MIT's Leaders for Manufacturing program. I couldn't turn my back on that. I mean, I had a plan and I had to see it through.
So, I took an internal Lean consultant role at AssemblyCo, near Fort Worth, and eventually moved into roles with direct management responsibility.
In what little free time I had, I continued reading about Lean healthcare over the years. As I read books about the successful application of Lean principles and Lean leadership at ThedaCare and Virginia Mason Medical Center, I saw the influence that manufacturing leaders had on their improvement efforts, translating lessons from factories to patient care.
It was great to read about the improvements they (and other hospitals) made, including:
- Reducing patient harm
- Improving quality and outcomes
- Reducing waiting times
- Creating a better workplace for nurses, doctors, etc.
- Improving the bottom line for the hospitals and saving money for those who paid for healthcare (such as my manufacturing companies)
In manufacturing, we improve safety and quality, while providing faster delivery to customers and better profitability for our shareholders. But, I have been starting to wonder if “shareholder value” is really what my life's mission is all about. I find myself daydreaming about my “Plan B” of healthcare during boring corporate retreats. I can get the job done in manufacturing and still feel it's an important driver of jobs and opportunities for people. But, maybe helping patients is a more meaningful challenge.
I have friends from the manufacturing sector, like Michael Lombard, who successfully made the transition into healthcare roles. When I'm at different Lean conferences, people I meet say Lean healthcare can be incredibly challenging — old habits, mindsets, and practices can be slow to change — but it's worthwhile. I can only imagine how it must feel to see nurses smiling during the day instead of being overworked and frustrated… and to realize that patients are getting better results in a shorter time at a lower cost.
Maybe it's time to try Plan B. Thanks to those who have paved the way. If it doesn't work out in healthcare, I guess I can always go back to manufacturing.
Please scroll down (or click) to post a comment. Connect with me on LinkedIn.
Let’s work together to build a culture of continuous improvement and psychological safety. If you're a leader looking to create lasting change—not just projects—I help organizations:
- Engage people at all levels in sustainable improvement
- Shift from fear of mistakes to learning from them
- Apply Lean thinking in practical, people-centered ways
Interested in coaching or a keynote talk? Let’s start a conversation.
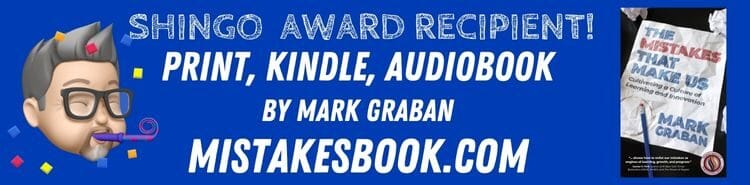
I often think about how things would have been different had I not gone into healthcare back in 2005. I think I helped many healthcare organizations start down the path of continuous improvement, and I think there has been a positive impact on patient satisfaction and patient safety in many of those cases. My 9 years in healthcare also helped me grow as a professional and as a person. I’ve now moved on to financial services, but I’d like to think I helped the cause of improving healthcare in the U.S.
I should have given you a shout out in the article too, Dean, as you made that transition pretty early and helped many organizations in different ways.
Thank you, but not necessary, Mark. Those of us who were early to the healthcare party made plenty of mistakes, but being humble and being willing to learn the business before trying to make big sweeping changes helped me get there. I think healthcare is appraching the stage that manufacturing was in a few years ago where the way to apply the tools and philosophy is becoming known, but the willingness of leadership to take the chance and change how they lead is becoming the biggest barrier to success.
It’s good that you move from manufacturing. No matter what changes we implement, it’s almost impossible to compete with labor costs, and management will likely always choose the latter. After I was laid off, the unemployment office suggested to study something different to move away from manufacturing. It’s sad because as one teacher told us, it’s our job to keep manufacturing here in the United States; however, the people who have the strings to do that, prefer the easy fixes.