I've been talking to a lot of healthcare organizations about Kaizen and continuous improvement. There are many organizations embracing the methods that Joe Swartz and I wrote about in Healthcare Kaizen. I think there's some momentum building out there for making sure that Lean isn't only a bunch of projects — instead, having everybody engaged in improvement (as Imai says: everybody, everywhere, every day).
But, I've also heard a somewhat disturbing pattern of organizations saying they aren't ready for Kaizen because their senior leaders aren't “on board” yet. They think Kaizen makes sense, but they are going to wait. Until when?
I understand the importance of having senior leaders understand Kaizen so they can model the leadership behaviors that are necessary for Kaizen to thrive. This is true at Franciscan St. Francis (Joe's system), as well as places like ThedaCare and Virginia Mason Medical Center where the CEOs are working every day to create and build a culture of continuous improvement.
That said, how do you build a culture of continuous improvement if you don't start working at it? I thought of an analogy the other day…

At left is a young Michael Jordan, one of the greatest basketball players in the history of the NBA (he's turning 50 this week).
Let's say the 11-year old Michael said he liked the idea of playing in the NBA. Let's say he said, “I'm not going to start playing or practicing basketball until I grow to be at least 6′ 3″, because I wouldn't be good at basketball if I'm tall. I'll wait until I am ready for basketball.”
Let's say he was 16 years old and he suddenly shot up in height from 5′ 10″ to 6′ 6″ in a short period of time, as some kids do. So, then he starts playing basketball because he's tall enough. He's now a very tall and very inexperienced player. His basketball development is far behind kids who started playing when they were young. Maybe it's too late to catch up and achieve the dream of being an NBA player.
Sidebar – when I was an undergrad at Northwestern, the men's basketball team had a 7-foot center who was just terrible. He didn't start playing until his senior year in high school and he was just an uncoordinated mess. He once dunked the ball into the wrong basket when he was in junior college before transferring to Northwestern.
So, while your hospital is sitting there saying, “we're not ready for Kaizen,” other hospitals (maybe your competitors) are practicing Kaizen and they are getting better at it. Can you catch up if you start a few years later?
When you start playing basketball, you're going to be pretty bad. You don't know how to dribble, or how to shoot, or how to play the game. The same is true with Kaizen. You might, in a way, dribble the ball off your knee a lot… but you have to keep playing. That's how you get better.
If you don't start playing, you can't get better. Great players don't wait until they are tall enough for the NBA to start playing.
Unlike basketball, we don't need rare Michael Jordan-type talent to be successful with Kaizen. Everybody can practice Kaizen… you have to be willing to start. You have to give up the fear of being terrible at it first (and I rarely see people who really are terrible, even at the start). There are so many challenges facing healthcare – what better time is there than now to start engaging everybody in improvement.
Did Toyota become a Kaizen culture overnight? Of course not… look at their data (which I believe is from the book 40 Years, 20 Million Ideas: The Toyota Suggestion System):
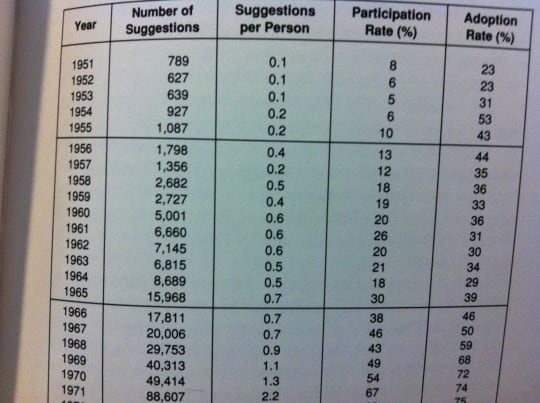
It took 20 years to get up to two suggestions per person per year. Toyota wasn't an overnight success with Kaizen.
Look at the data from Joe Swartz's organization (updated with 2012 data):
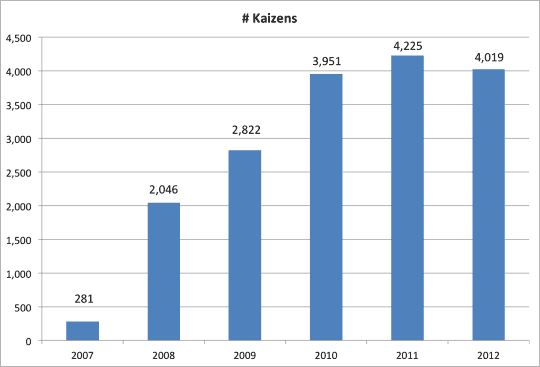
They got to about two suggestions per FTE by 2010 – four years into their program. And they've maintained that… because they keep working at it. They weren't afraid to start.
Starting somewhere and showing the impact of Kaizen might be the best way to get leaders on board. “It's easier to act your way into a new of thinking than it is to think your way into a new way of acting.”
Please scroll down (or click) to post a comment. Connect with me on LinkedIn.
Let’s work together to build a culture of continuous improvement and psychological safety. If you're a leader looking to create lasting change—not just projects—I help organizations:
- Engage people at all levels in sustainable improvement
- Shift from fear of mistakes to learning from them
- Apply Lean thinking in practical, people-centered ways
Interested in coaching or a keynote talk? Let’s start a conversation.
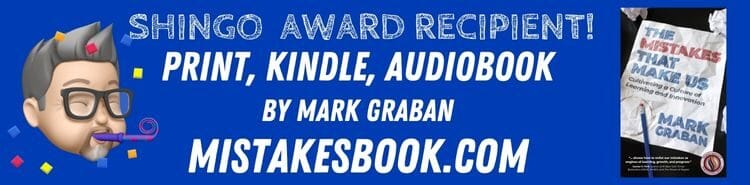
Here’s how you can tell if an organization is ready for kaizen: The organization says its not ready for kaizen.
I like the sports analogy. For some time I have used the same analogy, but in the context of learning to play music.
Yes, I like that analogy with music – nobody becomes a Grammy award winner overnight. Too many people, especially in healthcare, are paralyzed by the idea that they shouldn’t try something unless it’s going to go perfectly… although that hasn’t stopped any Electronic Medical Record implementations!
“Here’s how you can tell if an organization is ready for kaizen: The organization says its not ready for kaizen.” — Brilliant
[…] https://www.leanblog.org/2013/02/the-best-time-to-start-kaizen-is-today/ […]
The only way to start anything in Life is to Just Start. If I would have waited to be ready to start in any new business I would never have done anything, the only way to cause actual change is to simply start changing.
If you want to wait to be ready it will usually be to late.
I love the Jordan analogy. I was recently involved in conversation that used the “wait until you can afford children to have a baby” as the same analogy. I think this is very similar.
Yes… there’s never a perfect time to have a baby. How many people are waiting for the “right time” to quit a job that they currently hate? How many are waiting until they are ready to start that company they dream of?
The sooner you start making and fixing mistakes, the sooner you will start improving. It was difficult for my staff to understand that learning only happens when you acknowledge the mistakes you made and begin fixing them. Not all improvements have to be huge, and fixing small mistakes as you encounter them WILL produce huge improvements given time. Start learning while you stop making excuses about being ready for Kaizen.
Great post and right on point. The Jordan analogy may be more appropriate than you know. I grew up in Wilmington during the Jordan years. Jordan didn’t make the sophomore team at Laney High School as a sophomore – he was too short. Instead of accepting that he wasn’t ready, he became the star of the JV team through a lot of hard work. Between the skills he developed and a growth spurt over the next year, making the varsity team as a junior was never in doubt – and the rest is history. Funny how both life and lean journeys often work – get the wheel turning and gaining momentum, and opportunities that didn’t exist before just seem to appear from nowhere.
I just wanted to let you know that I loved this post! My organization still struggles with this at times and we’ve been working on building a process improvement culture for years, long before they hired a dedicated resource to teach and facilitate (me). Do you have any suggestions for helping senior leaders that might still be struggling with making the change from a traditional, top-down management style turn the corner and get on board with the Process Excellence/Lean gal? :)
Hi Sara – Thanks!
Joe Swartz and I have recently sent our publisher the manuscript for our upcoming new edition of our book “Healthcare Kaizen” that’s targeted toward CEOs and senior leaders:
The Executive Guide to Healthcare Kaizen: Leadership for a Continuously Learning and Improving Organization
I’ll be able to share the new Chapter 1 for that book soon… we’re hoping the book helps senior leaders understand “why Kaizen?” but also more about the behaviors that are required to make improvement happen. For now, you can have them read sections of our original “Healthcare Kaizen” book perhaps :-) Or have them view our KaiNexus education videos, which are useful (we think) to organizations that aren’t our customer.
What quick suggestions do I have? One good practice from Joe’s organization is to have leaders first work on their own Kaizen improvement (related to their own work). This experience sets a good example for others and they learn a lot from doing Kaizen instead of just “sponsoring” or encouraging it…
As Mark Twain said, “The secret of getting ahead is getting started.”
People, will you please stop assuming that Lean is the only solution and is right for everyone. Do you know how many unused gym memberships I’ve purchased over the years because I got sucked in by salespeople selling their “one and only” solution to my fitness challenge?
Sure Lean is great for us because we get it and we’ve seen it work. But I’ve also seen it not work…lots of times. And usually its because senior management wasn’t ready for it, or didn’t believe in it, or didn’t want to change anything,or whatever the reason.
So my advice to leaders of organizations who have to change is this: either do something or get out of the way. If you believe in Lean and you truly want to embrace it then go for it. If you truly believe in some other methodoligy then go for it. But if you have no idea what to do then please DO NOT choose Lean. Please, I beg you. The last thing I need is to hear about another Lean (or Mean) initiative that failed because it “wasn’t right.” If you’re going to do anything pick something other than Lean and screw that up. Or better yet graciously step aside and let someone else lead your organization.
And as for the sports analogy for every Michael Jordan there are thousands of kids who hate basketball becausae they were forced to play so their parent could live out his/her unfulfilled fantasy. If you don’t have passion for what you do then do something else.
Kevin, will you please stop assuming that we “people” assume Lean is the only solution?
We’re in violent agreement that:
1) Lean isn’t right for everyone
2) People shouldn’t “do Lean” if they aren’t willing to change their own leadership styles
3) They shouldn’t “do Lean” if they aren’t committed to it.
You’re reacting to things I didn’t say. Michael Jordan wasn’t forced to play basketball, I’m pretty sure he was pretty danged driven (and still is).
If you’re buying gym memberships and not using them, that’s your fault, not the gym’s
Is important that our top management are ready , but is more important that our shop floor peoples have the total commitment in Lean, Lean is not one fashion is the only way for survivor and grow in the present and future market. like you told above lines everywhere, everybody, everday.
And I think the best (and maybe only way) to get the shop floor employees to have a total commitment to Lean is to start engaging them in daily Kaizen and they will see that improvements benefit them (make their work easier and more productive and improve quality) while being fun and rewarding to do.
[…] See my past blog post about how the best time to start is today. […]